Mastering Hydraulic Solenoid Valves Made Simple
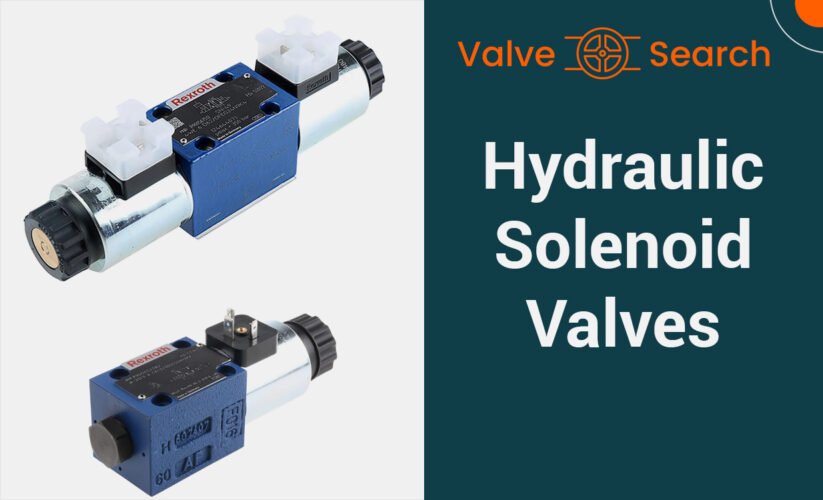
Introduction
In the intricate world of hydraulic systems, understanding each component’s role can sometimes feel like trying to unravel a complex puzzle. At the heart of these systems, governing the show like an invisible conductor, are hydraulic solenoid valves. However, wrapping your head around the functionalities, workings, and mastery of these essential units can be quite intimidating. We intend to demystify these critical components and provide an easy-to-grasp, comprehensive guide, designed to elevate your knowledge and confidence when dealing with these integral parts of hydraulic systems. Whether you’re a novice or a seasoned veteran, we invite you to join us on this enlightening journey through the core of hydraulics.
What is a Hydraulic Solenoid Valve?
The hydraulic solenoid valve can be described as a solenoid valve as part of a hydraulic process to control opening and closing or adjusting the flow direction of liquid. A hydraulic solenoid valve is a crucial device in many industrial applications. Its foundation lies in Faraday’s Law of electromagnetic induction, with its first practical application dating back to the early 19th century. Its basic function is to regulate the flow of a liquid or gas through a pipe or tube by employing an electromagnetic solenoid.
In the context of hydraulic systems, a solenoid hydraulic valve controls the fluid power. It consists of a solenoid coil, which creates a magnetic field when electricity passes through it, and a plunger, which reacts to the magnetic field and moves to open or close the valve.
These valves play a critical role in fluid control tasks in hydraulic systems, with applications ranging from industrial machinery to automotive braking systems. Understanding the function and operation of a hydraulic solenoid valve is key to its effective use and maintenance.

How does a Hydraulic Solenoid Valve Work?
The functioning of a hydraulic solenoid valve is a fascinating interplay of physics and engineering. In essence, a hydraulic solenoid valve acts as a kind of gateway in a hydraulic system, controlling the flow of fluid through the system.
Hydraulic Solenoid Valve Working Principle
The working principle of a hydraulic solenoid valve is centered on the fundamental concept of electromagnetism. As electricity passes through the solenoid coil, it creates a magnetic field. This magnetic field then moves a ferromagnetic plunger located within the coil, thus opening or closing the valve.
When the electrical current to the solenoid is turned on, the magnetic field causes the plunger to move and open the valve. Conversely, when the current is turned off, the magnetic field collapses, and a spring forces the plunger to return to its original position, closing the valve. This ability to rapidly switch the state of the valve from open to closed, simply by applying or removing an electrical current, is what makes the these valves such an effective control device in a hydraulic system.
One critical aspect of a hydraulic solenoid valve’s operation is the pressure balance. For the valve to function properly, there must be a balance between the hydraulic pressure acting on the valve and the force exerted by the solenoid and the spring. This is why the specifications of the solenoid, such as voltage and current, as well as the hydraulic system’s pressure, are essential parameters when selecting the right valve.
Understanding the working principle of a hydraulic solenoid valve is critical to leveraging its capabilities for fluid control in hydraulic systems. This understanding can provide insights into potential issues, aid in troubleshooting, and inform effective maintenance practices.
Technical Features of Hydraulic Solenoid Valves
Hydraulic solenoid valves, also known as solenoid hydraulic valves, are complex mechanical devices with a myriad of technical features that are crucial to their operation. In order to appreciate the functionality of these components, it’s essential to delve into their specific technical attributes.
The Anatomy of a Solenoid Hydraulic Valve
he physical structure of a hydraulic solenoid valve typically comprises of three main parts: the solenoid coil, the plunger or armature, and the valve body. The solenoid coil is essentially an insulated wire wound around a metallic core, designed to generate a magnetic field when an electric current is passed through it. The plunger, made of a ferromagnetic material, is designed to move within the coil, triggering the opening or closing of the valve based on the magnetic field. The valve body, usually made of brass or stainless steel, houses the other components and is designed to withstand the hydraulic pressure of the fluid being controlled.
Hydraulic Solenoid Valve Diagram
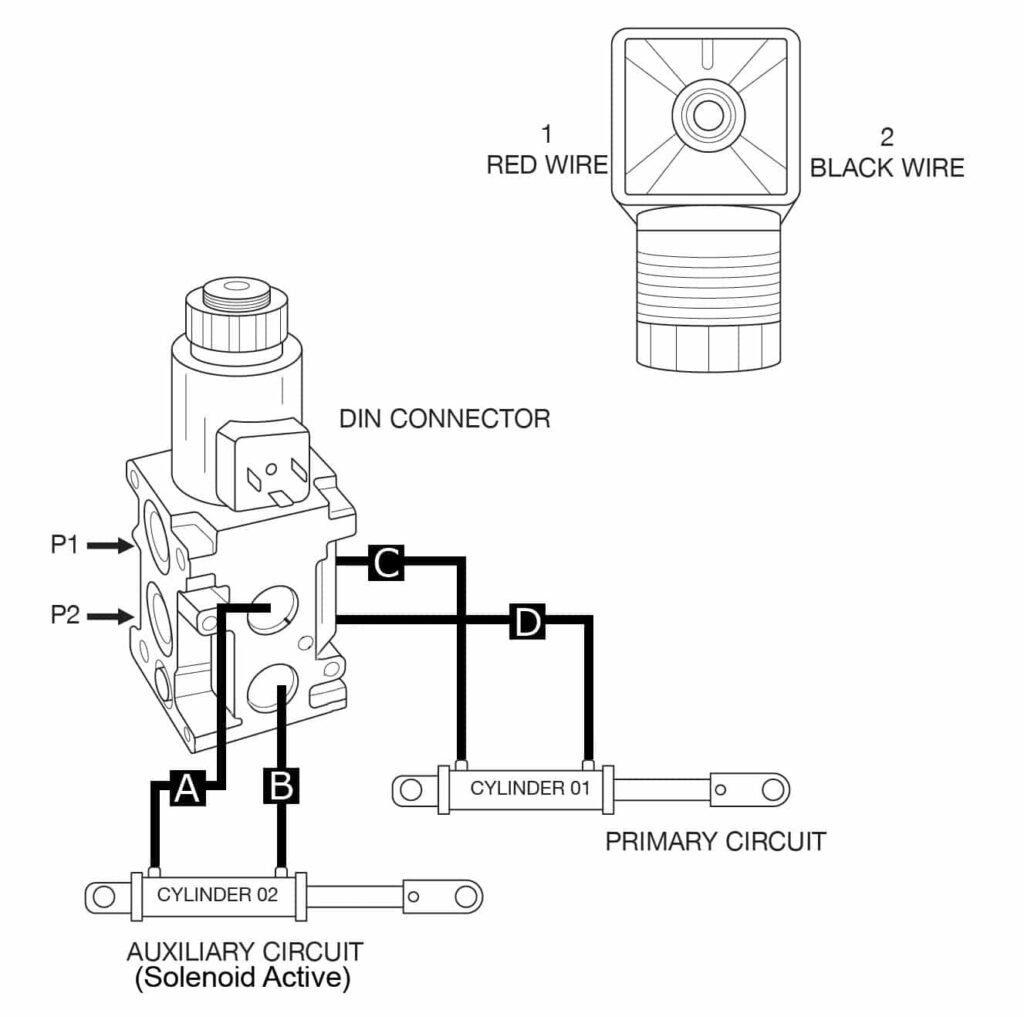
This diagram serves as a visual guide, detailing the assembly and functionality of the valve’s core components – the solenoid coil, the plunger or armature, and the valve body. It’s instrumental in understanding how the electrical energy in the solenoid is converted into mechanical energy to control the hydraulic flow. Here, it is key to comprehend how the coil’s magnetism dictates the plunger’s movement, ultimately influencing the hydraulic flow. Understanding this interplay is fundamental to appreciating the dynamic operation of these valves.
Operating Specifications
Hydraulic solenoid valves operate based on specific parameters such as voltage, current, power, pressure range, and temperature range. The voltage and current specifications dictate the electrical requirements for operating the solenoid. The pressure range indicates the hydraulic pressure that the valve can handle, while the temperature range specifies the operational environment’s thermal conditions that the valve can withstand.
12 Volt Hydraulic Solenoid Valve
A particular variant of hydraulic solenoid valves is the 12-volt hydraulic solenoid valve, which operates at a voltage level of 12 volts. 12V hydraulic solenoid valvevalve is commonly used in mobile applications, such as marine, automotive, and off-road equipment, due to its compatibility with the 12-volt electrical systems typical in these applications. Despite the lower voltage, these valves offer robust performance and reliability, provided their operating conditions align with their technical specifications.
Understanding these technical features of hydraulic solenoid valves can provide valuable insights into their functionality and suitability for specific applications. By appreciating the intricacies of these components, you can make more informed decisions when selecting and utilizing these valves in your hydraulic systems.
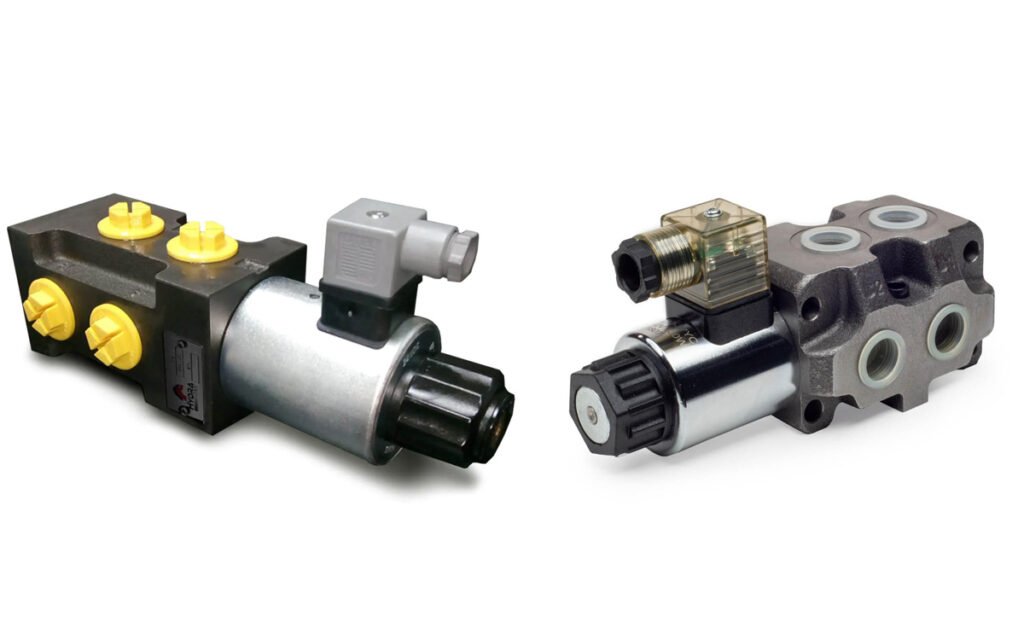
Types of Hydraulic Solenoid Valves
Understanding the types of hydraulic solenoid valves is essential for selecting the right valve for your application. Generally, these valves are classified into two major types, based on their operation and construction: the direct-acting solenoid valve and the pilot-operated solenoid valve.
Direct-Acting Solenoid Valves
In a direct-acting hydraulic solenoid valve, the solenoid directly opens or closes the valve. When electricity flows through the solenoid coil, it generates a magnetic field that moves the plunger, thus opening or closing the valve. Direct-acting solenoid valves are reliable and quick-acting, but they are usually limited to smaller flow rates due to the power required to move the plunger directly against the hydraulic pressure.
Pilot-Operated Solenoid Valves
Pilot-operated solenoid valves, on the other hand, use the hydraulic pressure difference to open or close the valve. They are equipped with a small pilot valve, controlled by the solenoid, which then controls the main valve. Pilot-operated valves are efficient for larger flow rates but are slower to actuate and more complex in design than direct-acting valves.
Hybrid Solenoid Valves
There also exist hybrid solenoid valves that combine the principles of direct-acting and pilot-operated solenoid valves, leveraging the benefits of both types. They can handle higher flow rates and respond quickly.
Each type has its advantages and applications, and the choice will depend on factors such as flow rate requirements, system pressure, response time, and complexity of the system. Armed with this knowledge of the types of hydraulic solenoid valves, you are better equipped to make the right selection for your hydraulic system.
Applications of Hydraulic Solenoid Valves
Hydraulic solenoid valves are integral components in an array of industries due to their versatility and functionality. They play a pivotal role in industrial automation, providing precise control over fluid power in numerous applications.
Manufacturing and Industrial Applications
Hydraulic solenoid valves are often utilized in automated assembly lines and process control systems. They facilitate the control of machinery and equipment, enabling automatic start-stop functions and regulating fluid flow rates. Such usage is critical in industries like food processing, textiles, and pharmaceutical manufacturing.
Within the realm of energy and utilities, these valves control hydraulic fluid in power plants, facilitating the safe and efficient generation of electricity. They also play a crucial role in wastewater treatment plants, where they help regulate the flow of water and chemicals throughout the treatment process.
Automotive Industry
Hydraulic solenoid valves are integral to automatic transmission and power steering systems. They regulate fluid flow, thereby controlling gear shifts and steering mechanisms. Similarly, in braking systems, they help modulate the hydraulic pressure, improving safety and reliability.
Hydraulic solenoid valve applications in the automotive industry
In the realm of vehicle manufacturing, hydraulic solenoid valves play a crucial part in controlling the complex network of hydraulic systems that make up an automobile. They function as reliable switchgear, seamlessly shifting between different states to facilitate the operation of various vehicle systems like transmission, steering, and braking. For instance, they assist in the smooth operation of the convertible roof mechanism in luxury cars by precisely controlling the flow and pressure of the hydraulic fluid. Similarly, they regulate the hydraulic suspension systems in heavy-duty vehicles ensuring a smooth and stable ride.
HVAC
Another notable application of hydraulic solenoid valves is in heating, ventilation, and air conditioning (HVAC) systems. Here, they control the flow of refrigerant, thereby influencing the cooling or heating process. This ensures optimal indoor climate control and energy efficiency.
Medical
The realm of medical equipment is not left untouched by these valves. They find their way into devices like dialysis machines and ventilators, where precise fluid control is paramount.
In summary, hydraulic solenoid valves are foundational to the operation of diverse systems across a broad spectrum of industries. Their applications underscore the importance of understanding their function and operation, and the need for sound selection and maintenance practices.
The role of hydraulic solenoid valves in achieving energy efficiency in industrial applications
Hydraulic solenoid valves are crucial components that facilitate various functionalities in a wide array of sectors, ranging from manufacturing to medical equipment, by controlling the fluid flow efficiently. Furthermore, they contribute significantly to the conservation of resources and reduction of wastage by ensuring precise fluid control, ultimately bolstering operational efficiency and sustainability in industries.
These valves not only provide precise control over fluid flow in various applications but also play a crucial role in promoting resource conservation and operational efficiency across industries. They can adjust their position to alter fluid flow rates, enabling businesses to match fluid supply with demand accurately, reducing resource usage and waste. They are meticulously designed to offer long service life and require minimal maintenance, further contributing to sustainability and cost efficiency.
By leveraging the capabilities of these valves, industries can streamline their operations, reduce waste, and maintain consistent product quality, thereby maximizing productivity and sustainability. Their ubiquitous presence across diverse fields underscores the profound impact they have on our daily lives.
Known Brands
In the vast landscape of hydraulic solenoid valves, several brands stand out due to their superior quality, innovation, and reliability.
Bosch Rexroth Solenoid Valve
Bosch Rexroth, a German multinational engineering company, is renowned for its high-performance hydraulic solenoid valves. They are well-regarded for their robust design, precision control, and versatility. Bosch Rexroth’s solenoid valves are widely used in a variety of industries, including automotive, aerospace, and industrial manufacturing. The company’s hydraulic solenoid valves are especially praised for their ability to function smoothly even in high pressure and high temperature conditions, owing to their durable materials and advanced engineering. They also feature quick response times and easy installation, making them a convenient and practical choice for many operators.
Mannesmann Rexroth Solenoid Valve
Mannesmann Rexroth is another distinguished name in the industry, recognized for their superior hydraulic solenoid valves that boast of longevity and impeccable performance. Ideal for demanding applications, Mannesmann Rexroth’s valves feature state-of-the-art design, and deliver precise fluid control with high efficiency, contributing to optimal system performance. Their products include the DR and 4WE series of solenoid valves, which can operate under pressure up to 315 bar and a maximum flow of 120 l/min, offering optimal response times and energy efficiency. This robust design and technical excellence make them a preferred choice in hydraulic applications.
Parker Solenoid Valve
Parker, a globally renowned manufacturer, offers durable and high-performing hydraulic solenoid valves known for their broad range of specifications and customizability. Their products, including the D1VW and D3W series, are characterized by exceptional flow control, easy installation, and capability to withstand demanding operational conditions. Additionally, Parker’s solenoid valves exhibit top-notch versatility, proving their effectiveness in diverse fields ranging from robotics to oil refineries. Their high resistance to corrosive environments and notable stability under vibratory conditions further increase their utility in multiple applications.
Vickers Solenoid Valve
Vickers, a part of the Eaton Corporation, is another key player in the hydraulic solenoid valve market. Their valves are synonymous with quality and efficiency. Known for their innovative design, Vickers hydraulic solenoid valves are extensively used in marine, industrial, and mobile equipment. Their valves offer excellent flow control, high pressure capabilities, and long service life. Particularly noteworthy is Vickers’ DG series of valves that can withstand pressure up to 350 bar, have flow rates of 4 to 250 litres per minute, and come with IP65 rated solenoids. Moreover, their KCG series are high-pressure solenoid valves with capacities up to 300 l/min and can resist pressure up to 350 bar, thus ensuring efficient fluid control under demanding conditions.
In summary, each of these brands has carved a niche in the market by delivering exceptional hydraulic solenoid valves. By understanding the unique strengths and offerings of these brands, you can make an informed decision when choosing a hydraulic solenoid valve for your application.
Selection Criteria for Hydraulic Solenoid Valves
Selecting the right hydraulic solenoid valve for your specific application can be a critical decision, directly impacting the efficiency and functionality of your hydraulic system. Here are some key factors to consider in the selection process.
1. Consider the Valve Type
As discussed earlier, hydraulic solenoid valves are primarily classified as direct-acting or pilot-operated, each with its own advantages and applications. For instance, if you need a valve for a high-flow system, a pilot-operated valve might be a better fit. Conversely, for quick-response systems, a direct-acting valve could be more appropriate.
2. Operating Specifications
Ensure that the voltage, current, and power specifications of the valve match your system requirements. Additionally, the valve’s pressure and temperature range should align with your system’s conditions to ensure optimal performance and longevity.
3. Analyze the Flow Rate
The flow rate of your hydraulic system, measured in gallons per minute (GPM), is a key determinant in selecting a hydraulic solenoid valve. A valve with a higher GPM rating than your system’s flow rate is generally recommended to prevent potential damage due to fluid velocity.
4. Consider the Valve Material
The type of fluid used in your hydraulic system and its operating environment will influence the material selection for your hydraulic solenoid valve. For corrosive or high-temperature environments, a stainless steel valve may be more appropriate, while a brass valve could suffice for less demanding applications.
7 Key factors to consider when designing a hydraulic system using solenoid valves
Designing a hydraulic system using solenoid valves is a complex process, calling for a deep understanding of the technicalities. Let’s explore the essential factors that come into play:
1. Valve Selection: The choice of hydraulic solenoid valve is critical. This selection must consider the valve type (direct-acting or pilot-operated), its operating specifications (voltage, current, power, pressure range, temperature range), flow rate, and the valve material. This is previously detailed in our selection criteria.
2. System Pressure: The hydraulic pressure within the system significantly influences the valve operation. Ensure the valve’s pressure range aligns with your system’s operational pressure to facilitate smooth performance.
3. Flow Paths and Ports: The design should account for the number of flow paths and ports required. Whether you need a 2-way or a 3-way hydraulic solenoid valve will depend on the complexity of the fluid flow control required in your system.
4. Operating Environment: The environmental conditions where your hydraulic system will operate impacts the solenoid valve’s functionality. Consider factors such as temperature, humidity, and potential exposure to corrosive substances.
5. Power Supply: As the solenoid valves operate electromagnetically, ensure a reliable and consistent power source is in place. Consider the solenoid’s power requirements and ensure these align with the available power supply.
6. Maintenance Accessibility: The design should allow for easy access for regular maintenance and potential troubleshooting. Regular maintenance can prolong the lifespan of the hydraulic solenoid valves and ensure optimal system performance.
7. Redundancy: In mission-critical applications, including a redundant hydraulic solenoid valve in your design can safeguard against system failure should a primary valve malfunction.
By focusing on these factors during the design phase, you can develop a robust and efficient hydraulic system using solenoid valves. The appropriate incorporation of these valves into your system’s design can enhance performance, reliability, and longevity.
FAQ
What are some common troubleshooting tips for faulty hydraulic solenoid valves?
If your valve isn’t functioning correctly, check the power supply to the solenoid coil. Ensure the coil receives the correct voltage and current. Examine the plunger for any obstructions or signs of wear and tear. Sometimes, the valve may not operate efficiently if the fluid is too viscous or the system pressure is too high.
How do I know which type of hydraulic solenoid valve to use for my specific application?
This depends on several factors including flow rate requirements, system pressure, response time, and system complexity. Direct-acting valves are quicker but better suited for smaller flow rates, while pilot-operated valves handle higher flow rates but are slower to actuate.
What is the difference between a 2-way and a 3-way hydraulic solenoid valve?
A 2-way valve has two ports and can either be normally closed or normally open. A 3-way valve has three ports and can switch the flow between two paths. For instance, it can route the fluid from one component to another, or it can bypass one component for another.
What role does the solenoid coil play in a hydraulic solenoid valve?
The solenoid coil, when energized, creates a magnetic field that causes the plunger to move. This in turn controls the opening or closing of the valve, regulating fluid flow in the hydraulic system.
Can hydraulic solenoid valves be used in extreme temperature environments?
Yes, provided they are designed for such conditions. Check the temperature range specification to ensure it aligns with your application environment.
What are the advantages and disadvantages of using a hydraulic solenoid valve?
Advantages include precise control, automation capability, and robust performance. Disadvantages may include the requirement of a power source and potential sensitivity to temperature and pressure variations.
What is the function of a hydraulic solenoid valve in a hydraulic system?
The function of a hydraulic solenoid valve in a hydraulic system is pivotal as it directs, blocks, or adjusts the flow of hydraulic fluid within the system. This is achieved by electrical activation, enabling the manipulation of larger volumes of hydraulic fluid and the capability to rapidly start or stop flow.
Conclusion
To conclude, a hydraulic solenoid valve is a fundamental component in various industrial systems, employing the principles of electromagnetism to control fluid power effectively. It’s crucial to appreciate its technical aspects, working principle, key features, and types to make an informed decision while selecting one for your specific application. Major brands like Bosch Rexroth, Mannesmann Rexroth, and Vickers offer top-quality solenoid hydraulic valves, each known for their distinct strengths and specialties.
A solid understanding of the functionalities and operations of hydraulic solenoid valves can improve the efficiency of your hydraulic systems and enable effective troubleshooting. The valve’s application extends to numerous sectors, from manufacturing and energy utilities to automotive and HVAC, underlining its versatile utility.
In designing a hydraulic system, the choice of the valve, system pressure, flow paths, operating environment, power supply, and maintenance accessibility are key considerations. Recognizing these factors can aid in building a robust and efficient hydraulic system.
In essence, hydraulic solenoid valves are integral to the seamless operation of numerous hydraulic systems, contributing to operational efficiency and resource conservation. Harnessing the capabilities of these valves, you can significantly enhance your system’s performance, leading to higher productivity and sustainability. A hydraulic solenoid valve is not just a component; it’s a solution, enabling precise control and automation in complex hydraulic systems.