Guide to Large Diameter Butterfly Valves: All You Need
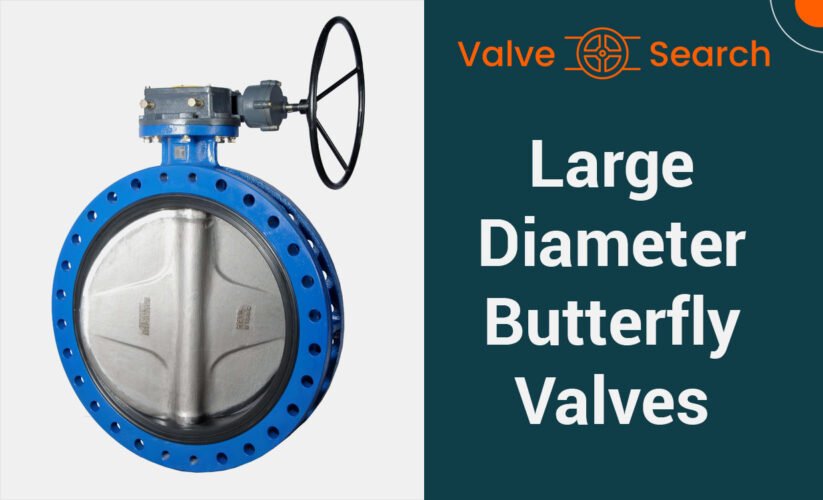
Introduction
The industrial landscape is continually evolving, with innovation leading the way. A significant development that has revolutionized fluid control systems is the large diameter butterfly valve. Offering robustness, versatility, and cost-effectiveness, these valves are increasingly becoming a preferred choice for various industries. This blog post aims to delve into the intricacies of large diameter butterfly valves, providing a comprehensive guide about their design, applications, pros, and cons.
Understanding the Large Diameter Butterfly Valves
Large diameter butterfly valves play a pivotal role in managing fluid flow within industrial settings. These devices regulate fluid movement by utilizing a rotating disk, positioned on a central rod, that aligns or obstructs the path of the fluid. When in the open state, the disk orients parallel to the fluid’s direction, promoting uninhibited flow. Conversely, when the valve is closed, the disk is set perpendicular to the fluid’s path, thereby blocking flow.
The attribute of “large diameter” is a reference to the valve’s size, which makes them suitable for applications involving high volumes or elevated pressures. These valves can handle immense fluid flow with relative ease, making them an optimal solution for robust industrial applications. By combining their unique design with operational efficiency, large diameter butterfly valves pave the way for effective fluid management in diverse industrial contexts.
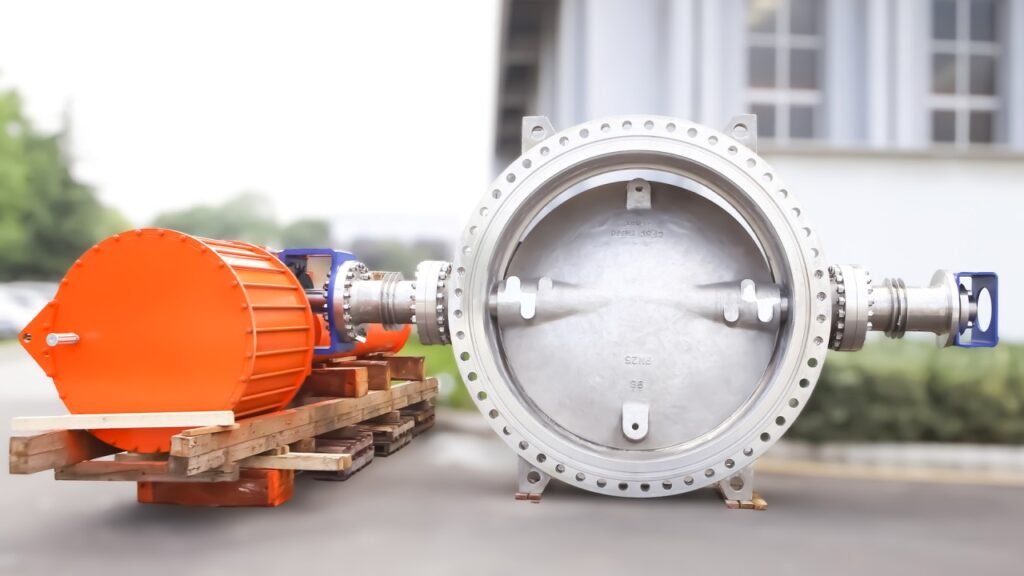
Wide-Ranging Applications of Large Diameter Butterfly Valves
These colossal valves are not limited to one industry but are instead leveraged in various sectors due to their superior ability to handle high volume flow and pressure. From water treatment plants where they aid in the purification processes, to the oil and gas industry where they help manage the flow of crude oil and natural gas, large diameter butterfly valves are everywhere.
The energy sector also utilizes these valves extensively in power generation facilities, ensuring efficient operation of turbines by controlling steam flow. HVAC systems, tasked with maintaining a comfortable indoor environment, depend on these valves for effective air flow management.
Fire protection systems are another area where these valves are extensively used, helping control water flow in sprinkler systems during emergencies. Besides, these versatile valves also come in handy in applications requiring both throttling service and full-on/off service. Their expansive size makes them especially effective in pipelines that transport dense liquids or gases. Understanding these varied applications can help industries identify where these valves can best be utilized for optimal fluid management.
Design and Technical Specifications of Large Diameter Butterfly Valves
Large diameter butterfly valves are designed to manage substantial fluid flow, requiring specific technical specifications to accommodate various industrial applications. One of the most widely utilized designs is the double eccentric butterfly valve. This design is renowned for its longevity and reduced friction because the disk is situated slightly off the center of the valve, minimizing wear on the disk and seat.
Technical aspects of Large Diameter Butterfly Valves
The technical aspects of these valves are largely dictated by their intended usage. These factors include pressure rating, the maximum and minimum temperature the valve can withstand, and the nature of the fluid being controlled. Pressure rating determines the maximum pressure a valve can handle before it fails or becomes inefficient. The temperature resistance refers to the range of temperatures in which the valve can operate optimally. This is particularly important for applications dealing with high-temperature fluids or environments.
Lastly, the type of fluid being managed is a crucial specification. Different fluids, such as gases, liquids, or slurries, have varied characteristics that may affect the operation of the valve. For instance, highly abrasive or corrosive substances may cause damage over time. Consequently, valves destined for such applications may require specific materials or coatings to enhance their resistance.
Manufacturers may provide customized solutions based on the precise requirements of an application, allowing for adaptations in design and technical specifications. Therefore, when considering a large diameter butterfly valve, a clear understanding of these specifications is vital to ensure a good match between the valve and its intended application.
The Advantages of Large Diameter Butterfly Valves
The design and functionality of large diameter butterfly valves bring a multitude of benefits to industrial applications:
- High Volume Handling: With their expansive size, these valves are equipped to handle high volume fluid flow with relative ease. Their large diameter provides a broad pathway for fluids to pass through, making them an ideal choice for heavy-duty applications.
- Cost-Effectiveness: When compared with other valve types, large diameter butterfly valves typically come at a more affordable cost. They offer an economically viable solution without compromising on operational efficiency.
- Versatility: Large diameter butterfly valves can manage a wide variety of fluids, ranging from gases to liquids and even slurries. Their adaptability makes them a valuable asset across diverse industrial sectors.
- Low Maintenance: The simple design of these valves results in less wear and tear, reducing maintenance requirements. This contributes to long-term cost savings for businesses.
- Space Efficiency: Despite their large size, these valves are designed in a way that minimizes the space they occupy. This makes them ideal for applications where space is at a premium.
- Ease of Operation: The operation of large diameter butterfly valves is straightforward. They can be easily opened or closed with minimal effort, enhancing the efficiency of fluid control processes.
- Durability: These valves are built to last. Their robust construction, often using high-quality materials, ensures they can withstand harsh industrial conditions for extended periods.
- Customizability: Many butterfly valve manufacturers offer customization options. This allows for adaptations in design and specifications, making the valves more suitable for specific application requirements.
In summary, the large diameter butterfly valve offers an impressive combination of efficiency, durability, and versatility, making them a worthwhile addition to any industrial fluid management system.
Potential Disadvantages to Consider
Despite the many advantages of large diameter butterfly valves, it’s important to also take note of certain limitations. First, these valves might not be the ideal choice for applications requiring a complete shut-off, as a minor degree of leakage may occur. This could potentially result in efficiency losses, particularly in systems where airtight closure is essential.
Another consideration is their suitability for handling highly abrasive or corrosive fluids. The design of butterfly valves exposes the disk and seat directly to the fluid flowing through them. Consequently, over time, this exposure can lead to wear and tear, affecting the valve’s performance and lifespan. This makes them less favorable for applications involving substances that are highly corrosive or abrasive.
It’s also worth mentioning that despite their large size, these valves may not be able to match the flow control precision of other valve types in certain high-pressure scenarios.
Understanding these potential downsides is crucial for selecting the most appropriate valve for a specific application. It enables industries to weigh the benefits against the limitations, ensuring a choice that best aligns with their operational requirements. As always, expert guidance from butterfly valve manufacturers can be invaluable in making an informed decision.
Maintenance and Repair of Large Diameter Butterfly Valves
Maintaining the optimal performance of large diameter butterfly valves is heavily dependent on regular maintenance and prompt repair actions. It is essential to conduct frequent inspections to detect any issues such as leaks, signs of corrosion, or wear on the valve components.
The design of butterfly valves exposes the disk and seat to the fluid flow. Over time, this can lead to degradation of these components, particularly in scenarios involving abrasive or corrosive substances. Being proactive in recognizing these signs and initiating timely repairs can enhance the durability and efficiency of these valves.
Guidelines for maintenance and repair procedures are typically provided by butterfly valve manufacturers. These guidelines are custom-made according to the valve’s design and specifications and provide invaluable information on maintaining the valve in peak condition. Following these instructions can not only prolong the valve’s lifespan but also ensure its operational efficiency.
In addition to adhering to these guidelines, the utilization of professional maintenance services can be beneficial. Professionals are well-versed with the intricacies of these valves and can help prevent potential issues, thereby saving costs on unexpected repairs or replacements.
In essence, the performance and longevity of large diameter butterfly valves are largely dependent on the quality of their maintenance and repair practices. With proactive measures and expert guidance, industries can significantly enhance the operational lifespan of these valves.
How long can a properly maintained large diameter butterfly valve last before needing replacement?
The longevity of a large diameter butterfly valve primarily hinges on diligent maintenance practices and the specific conditions of its usage. With routine inspections, timely repairs, and adherence to manufacturer guidelines, a properly maintained valve can often provide efficient service for up to 20-30 years. It’s worth noting that this lifespan can vary significantly based on factors such as the nature of the fluid being managed and the operating environment. For instance, valves exposed to highly abrasive or corrosive substances might necessitate earlier replacement. Therefore, while these estimates provide a general guideline, individual usage conditions and maintenance practices will ultimately dictate the precise operational lifespan of a large diameter butterfly valve.
Can a large diameter butterfly valve be used for regulating flow, or is it only for on/off control?
The versatility of large diameter butterfly valves extends beyond simple on/off control. While they excel in full open or close operations, they also have the capability to regulate fluid flow. This makes them a viable option for throttling applications where precise control over fluid flow rate is required. This versatility in operation is primarily attributed to their unique design, particularly in the case of double eccentric butterfly valves.
The double flanged design allows the disk to move off-center, providing more granular control over fluid passage, thus enabling flow regulation. However, it’s crucial to consider that while they offer throttling capabilities, they might not deliver the same precision as some other valve types in high-pressure scenarios. Therefore, the choice to use a large diameter butterfly valve for flow regulation should be based on a careful evaluation of the application’s specific requirements and the valve’s ability to meet them.
As always, consulting with butterfly valve manufacturers can provide expert advice, ensuring the valve’s operational capabilities align with the application’s demands.
How does the design of a large diameter butterfly valve differ from smaller ones?
The fundamental design principles remain consistent across all butterfly valves, regardless of size. However, due to their scale, large diameter butterfly valves often incorporate additional structural elements and might be constructed from different materials to handle high-volume, high-pressure applications. For instance, they might include reinforced shafts or heavier duty seals. Their size also calls for more robust actuation mechanisms to handle the physical demands of operation.
Essentially, this means that due to their larger scale, these valves require more durable components and mechanisms to withstand the operational demands that come with managing high volume and high-pressure fluid flow.
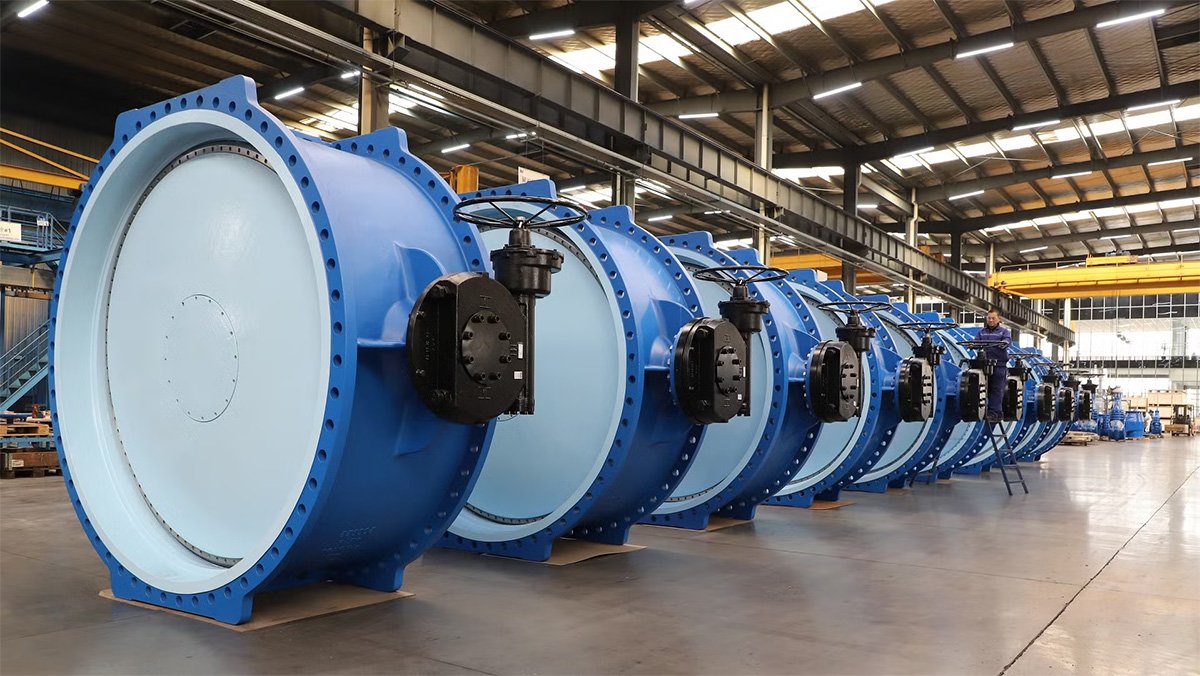
How does the cost of a large diameter butterfly valve compare to other types of valves?
When discussing cost efficiency in fluid control systems, the large diameter butterfly valve emerges as a front-runner. Generally, these valves are more affordable when compared to other types of valves with similar functionality. Factors that contribute to this cost-effectiveness include their simpler design and lower material requirement. These aspects result in lower manufacturing costs, a benefit passed on to consumers.
Cost of a Large Diameter Butterfly Valve
The affordability of large diameter butterfly valves does not equate to compromised performance. Despite being economical, these valves offer an impressive combination of operational efficiency and durability. This balance of cost and quality offers substantial value to industrial applications. Of course, the specific cost can vary depending on the valve’s technical specifications, such as pressure rating, temperature resistance, and the materials used in construction.
Customization options offered by butterfly valve manufacturers could also influence the price. When comparing costs, it’s crucial to consider not only the initial purchase price but also the long-term operating expenses. Factors such as maintenance requirements, lifespan, and potential downtime for repairs can significantly impact the total cost of ownership. In many of these aspects, the large diameter butterfly valve again proves to be a cost-effective solution.
In summary, while the large diameter butterfly valve is often a more economical choice, it’s important to conduct a comprehensive cost analysis that factors in both initial and ongoing expenses. Doing so will ensure that the chosen valve provides the best value for your specific application needs.
What materials are typically used in manufacturing large diameter butterfly valves?
The construction of large diameter butterfly valves necessitates the use of robust and durable materials. These materials must be able to withstand high volumes of fluid flow, varying pressure levels, and diverse fluid characteristics, all while ensuring optimal performance and longevity. To meet these demands, butterfly valve manufacturers use a combination of metals and non-metals for the construction of these valves.
Parts of a Large Diameter Butterfly Valve
Commonly, the body and disc of these valves are made from metals such as stainless steel, ductile iron, or carbon steel, known for their strength and durability. These materials are highly resistant to wear and tear, making them suitable for the valve’s crucial components. Stainless steel, in particular, is often used due to its corrosion-resistant properties.
The seats of these valves, which form the seal when the valve is closed, are typically made from resilient materials like EPDM, PTFE, or Nitrile. These materials provide an effective seal and are resistant to various chemical interactions, contributing to the valve’s overall longevity. In the case of double eccentric butterfly valves, manufacturers may use additional materials for the shaft and bearings, such as bronze or hardened steel, which enhance the valve’s resistance to wear.
It’s important to note that the choice of materials may be customized based on the specific requirements of the application. For instance, if the valve is intended for an application dealing with high-temperature fluids or corrosive substances, manufacturers may use specific materials or apply special coatings to increase the valve’s resistance.
In essence, the construction of a large diameter butterfly valve involves careful selection of materials that balance strength, durability, and resistance, ensuring the valve is well-equipped to handle the demands of diverse industrial applications.
Conclusion
Undoubtedly, large diameter butterfly valves play an instrumental role in various industries, providing a multitude of advantages such as affordability, compactness, and precision in flow control. Although they present some challenges, like potential leakage and susceptibility to wear in certain environments, the key to harnessing their benefits lies in a deep understanding of their design, applications, and maintenance needs.
Whether you’re new to the world of industrial valves or a seasoned expert, continuous learning about these devices is essential in fully leveraging their capabilities. Remember, while this guide provides a solid foundation, collaboration with butterfly valve manufacturers can offer personalized advice tailored to your specific needs. In essence, the large diameter butterfly valves’ journey in fluid control systems is one of continuous evolution and growth – much like the industries they serve.