Can globe valves be used for slurries or suspensions?
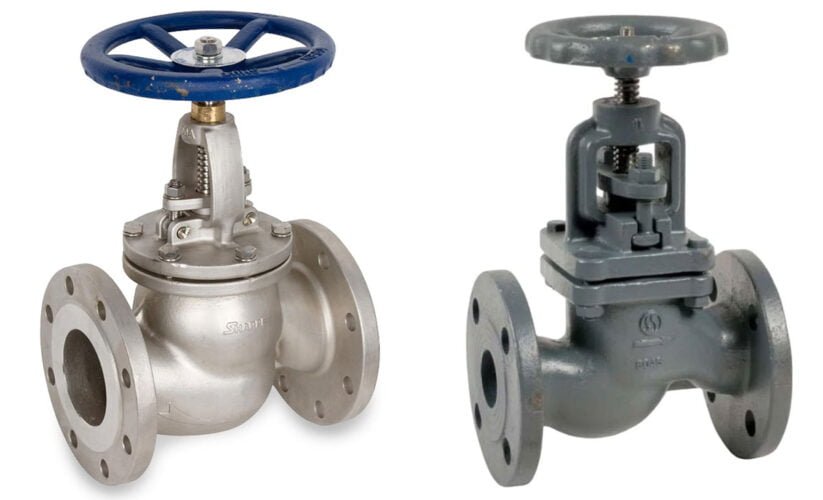
Globe valves are commonly used in various industrial applications, but are they suitable for handling slurries or suspensions? Let’s delve into this topic to understand the suitability of globe valves for such challenging fluid mediums.
Are globe valves appropriate for slurries or suspensions?
Understanding the Nature of Slurries and Suspensions
Slurries and suspensions are mixtures of solids and liquids, which can be highly abrasive and challenging to control. They are commonly found in industries such as mining, wastewater treatment, and chemical processing.
Globe Valves Overview
Globe valves are linear motion valves that are used to stop, start, and regulate the flow of a fluid. They consist of a movable disk or plug that can be adjusted to control the flow through the valve.
The Challenge of Slurries and Suspensions
Handling slurries and suspensions requires valves that can withstand abrasion and maintain tight shut-off capabilities to prevent leakage. The abrasive nature of these mediums can cause rapid wear and tear on valve components.
Suitability of Globe Valves
While globe valves can be used for controlling slurries and suspensions, their effectiveness in such applications depends on various factors such as the concentration of solids, velocity of flow, and the design of the valve.
Factors to Consider
When considering the use of globe valves for slurries and suspensions, it is important to assess the specific characteristics of the fluid, including particle size, hardness, and erosive potential. Additionally, the material of construction and the valve design play a crucial role in determining its suitability.
Specialized Globe Valve Designs
Some manufacturers offer specialized globe valve designs that are specifically engineered to handle abrasive mediums such as slurries and suspensions. These valves may feature hardened or abrasion-resistant materials to prolong their service life in challenging environments.
Maintenance Considerations
Proper maintenance and regular inspections are essential for ensuring the longevity and performance of globe valves used in slurries and suspensions. This includes monitoring for signs of wear, erosion, and leakage, and addressing any issues promptly.
Globe valves can be suitable for handling slurries or suspensions, depending on the specific application and the design of the valve. When considering the use of globe valves for slurries or suspensions, it is important to analyze the nature of the fluid being handled, as well as the characteristics of the valve itself.
In general, globe valves are known for their ability to provide good throttling and regulating control, making them potential candidates for applications involving slurries or suspensions. However, it is crucial to ensure that the valve is designed and manufactured to withstand the abrasive and erosive nature of slurries. The material of construction, the type of disk and seat, as well as the overall design must be carefully evaluated to determine the suitability of a globe valve for handling slurries or suspensions.
Several factors come into play when considering globe valves for slurries or suspensions. The flow properties of the slurry, such as its viscosity and particle size distribution, can impact the performance and longevity of the valve. Additionally, the pressure and temperature conditions under which the valve will operate need to be taken into account to prevent issues such as clogging, erosion, or leakage.
It is essential to address the concerns related to potential clogging or build-up within the valve, as slurries and suspensions can pose challenges in terms of maintaining smooth and unobstructed flow. Proper valve sizing and the inclusion of features such as self-cleaning capabilities or specialized trim designs can contribute to mitigating these issues.
In terms of specific design considerations, the choice of materials for the valve components is critical. For slurries with abrasive particles, valves made of materials with high erosion and wear resistance are preferred. Additionally, the sealing surfaces, such as the disk and seat, should be selected to withstand the erosive effects of the slurry while maintaining effective shut-off capability.
It’s worth noting that there are specialized globe valve designs, such as those with full port openings or adapted flow paths, that are specifically engineered to handle slurries and viscous fluids. These designs aim to minimize flow restrictions and reduce the likelihood of blockages within the valve.
Furthermore, the operational conditions, such as the frequency of valve cycling and the required degree of flow control, should be evaluated to determine if a globe valve is the most suitable choice for a given slurry or suspension application.
In conclusion, while globe valves can potentially be utilized for handling slurries or suspensions, careful consideration of the specific fluid properties, as well as the valve design and materials, is crucial. By selecting appropriate valve configurations and taking into account the challenges associated with abrasive and viscous fluids, it is possible to optimize the performance of globe valves in slurries and suspensions applications.