3 Types of Air Valves and Their Applications
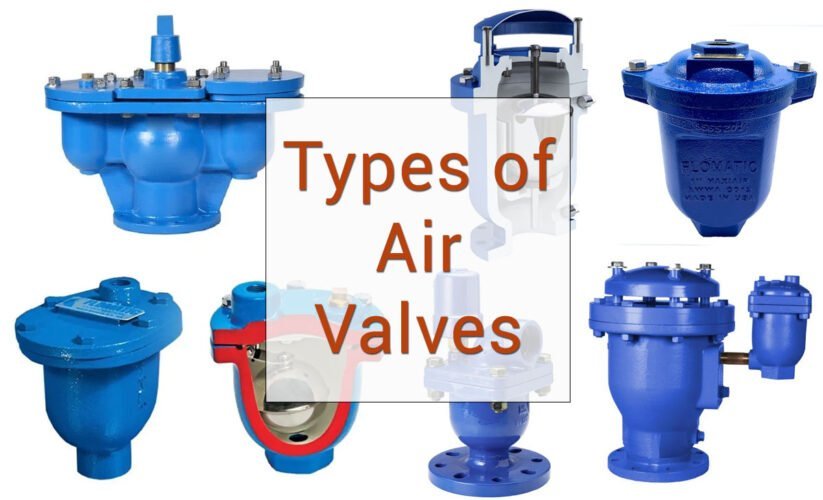
Table of Contents
ToggleExploring the Different Types of Air Valves: A Comprehensive Guide
Air valves play a crucial role in maintaining the efficiency of various systems by managing air and gas flow. This comprehensive guide will delve into the function and application of three main types of air valves: Air Relief Valves, Air/Vacuum Valves, and Combination Air Valves. Understanding the differences and benefits of each type is essential for optimizing system performance and preventing potential issues.
Understanding Air Valves and Their Importance
In today’s industrial landscape, efficient control of fluid flow is crucial for operational success. A key component in this process is the valve, a device used to regulate, direct, or control the flow of a fluid by opening, closing, or partially obstructing fluid flow. Among the various types of valves available, pneumatically operated valves have carved a niche for themselves due to their numerous advantages. These valves, which use air pressure for operation, are known for their safety and energy efficiency.
Valves are an indispensable part of any industrial process. They serve several crucial functions that ensure the smooth, safe, and efficient running of operations across a wide range of industries.
Flow Control
The primary function of a valve is to control fluid flow. This can be achieved by starting, stopping, or modulating the flow, allowing precise control over process quantities like flow rate and pressure.
Safety
Air valves play a critical role in maintaining safety in industrial processes. For instance, safety or relief valves prevent equipment damage by releasing pressure when it exceeds a set limit. This function is particularly vital in industries such as oil and gas, power generation, and chemical processing, where overpressure can lead to catastrophic failures.
Process Isolation
Valves are used to isolate parts of a process for safe maintenance or repair work. They allow specific sections of a pipeline or process to be shut off without affecting the rest of the operation.
Regulation of Process Conditions
Valves help maintain and regulate process conditions like temperature and pressure within desired limits. This is crucial for processes where specific conditions are required for optimal performance and product quality.
Direction of Flow
Certain types of valves, like check valves, are used to ensure fluid flows in one direction only, preventing backflow that could cause process disruptions or equipment damage.
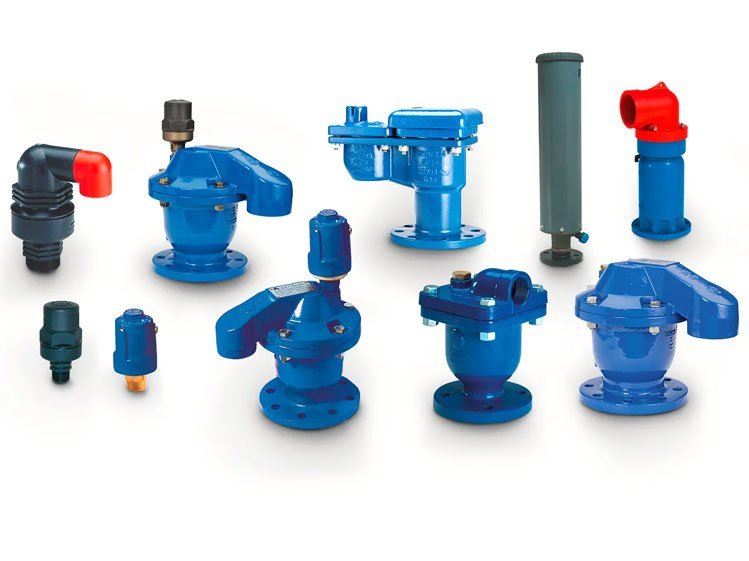
Pros and Cons for 3 Types of Air Valves
Air valves play a crucial role in the efficient operation of fluid systems, ensuring the proper functioning and longevity of pipelines. Understanding the advantages and disadvantages of different types of air valves is essential for engineers and professionals in the fluid handling industry. In this listicle, we will analyze the pros and cons of three common types of air valves: Air Relief Valves, Air/Vacuum Valves, and Combination Air Valves.
1. Air Relief Valves
Advantages
- Preventing pipeline collapse: Air relief valves are designed to release air pockets that can accumulate in pipelines, preventing the formation of vacuum and potential pipeline collapse.
- Protection against water hammer: These valves help in reducing the risk of water hammer by releasing air from the pipeline, thereby preventing pressure surges.
- Easy maintenance: Air relief valves are relatively easy to maintain, making them a cost-effective solution for pipeline systems.
Disadvantages
- Limited functionality: Air relief valves are primarily designed for releasing air and may not be suitable for applications requiring more complex functionality.
- Limited air release capacity: In high-flow systems, air relief valves may have limitations in their capacity to release air efficiently, leading to potential performance issues.
2. Air/Vacuum Valves
Advantages
- Air and vacuum release: These valves are capable of releasing air during system filling and of preventing vacuum formation during system drainage, ensuring optimal pipeline operation.
- Versatility: Air/vacuum valves can be used in a wide range of pipeline systems, making them a versatile option for various applications.
- Reduced risk of corrosion: By preventing the accumulation of air and vacuum, these valves contribute to reducing the risk of corrosion within the pipeline system.
Disadvantages
- Complexity: Some air/vacuum valves may have a more complex design, requiring additional expertise for installation and maintenance.
- Potential for clogging: In systems with particulate matter or debris, air/vacuum valves may be prone to clogging, affecting their efficiency.
3. Combination Air Valves
Advantages
- Comprehensive functionality: Combination air valves are designed to provide a comprehensive solution, including air release, vacuum relief, and surge protection, making them suitable for various pipeline systems.
- Efficient air and vacuum release: These valves are capable of efficiently releasing air during system filling and preventing vacuum formation during system drainage, ensuring optimal pipeline performance.
- Minimal maintenance: Combination air valves are often designed for minimal maintenance, reducing the overall operational costs of the pipeline system.
Disadvantages
- Higher cost: The comprehensive functionality of combination air valves may come with a higher initial cost compared to other types of air valves.
- Size and installation challenges: Due to their complex design, these valves may require more space for installation, and their positioning within the pipeline system may require careful consideration.
The proper selection of air valves is crucial for the efficient and reliable operation of pipeline systems. Each type of valve offers distinct advantages and disadvantages, and understanding these factors is essential for making informed decisions in pipeline design and maintenance. By weighing the specific requirements of the system against the characteristics of each type of air valve, engineers and professionals can ensure the optimal performance and longevity of pipeline systems.
The Function-Based Classification of Air Valves
Air valves play a crucial role in maintaining the efficiency and integrity of various fluid systems. Understanding the distinct functions of different types of valves is essential for ensuring optimal performance and longevity of these systems. Now we will provide a comprehensive overview of the function-based classification of air valves, focusing on Air Relief Valves, Air/Vacuum Valves, and Combination Air Valves.
Air Relief Valves
Air Relief Valves are designed to release air that accumulates in a system during operation. They prevent air pockets from causing inefficiencies or damage by automatically venting excess air. This type of valve is particularly important in systems with varying flow rates or where air can become trapped at high points.
Air Relief Valves are commonly found in irrigation systems, water supply networks, and wastewater treatment plants. Their ability to release air ensures that pipelines remain full and operational, reducing the risk of cavitation and potential damage to pumps and other components.
Air/Vacuum Valves
Air/Vacuum Valves serve a dual purpose, providing both air release and vacuum protection. These valves are designed to expel air during system filling and to admit air to prevent vacuum conditions during system drainage or pump shutdown. By maintaining system pressure and preventing vacuum collapse, Air/Vacuum Valves safeguard pipelines and equipment from damage.
In water distribution systems, Air/Vacuum Valves play a critical role in preventing pipeline collapse and protecting against negative pressure events. They are strategically positioned to address air accumulation and vacuum formation at high points, ensuring the integrity and efficiency of the entire system.
Combination Air Valves
Combination Air Valves integrate the functions of Air Relief Valves and Air/Vacuum Valves into a single compact unit. These valves provide comprehensive air and vacuum management, offering a cost-effective and space-saving solution for fluid systems. By combining air release, vacuum protection, and surge alleviation capabilities, Combination Air Valves streamline the operation and maintenance of pipelines.
In municipal water and wastewater applications, Combination Air Valves are installed at critical points to address air and vacuum challenges while mitigating pressure surges. Their multifaceted functionality makes them a valuable asset in ensuring the reliability and performance of complex fluid systems.
The function-based classification of air valves encompasses distinct types that serve specific purposes in fluid systems. Air Relief Valves, Air/Vacuum Valves, and Combination Air Valves each play a vital role in maintaining system efficiency and integrity. Understanding the unique functions of these valves is essential for selecting the most suitable solution to meet the requirements of diverse fluid systems.
Air Valves by Body Construction
Air valves can be classified based on their body construction. Two primary types include single orifice and double orifice air valves.
Single Orifice Air Valves
Single orifice air valves are designed with a single orifice for the entry and release of air. They are commonly used in applications where air release at high flow rates is essential, such as during pipeline filling and draining or vacuum conditions. These air valves effectively prevent air accumulation during pressurized operations, offer surge protection, and ensure improved sealing even at low-pressure conditions.
Double Orifice Air Valves
On the other hand, double orifice air valves feature two orifices, allowing for separate entry and release of air. This design provides enhanced control over air release and intake, making them suitable for applications with varying air volume requirements. Double orifice air valves are often preferred in systems where precise air release and intake are critical for operational efficiency and performance.
Key Factors to Consider When Choosing Air Valves
Size and Its Impact on Air Flow
When selecting air valves, size plays a crucial role in determining the air flow capacity of the system. The size of the valve directly impacts how much air can pass through it at a given time. It is essential to choose a size that matches the specific requirements of the system to ensure optimal air flow without causing any restrictions or bottlenecks. Consider the volume of air that needs to be regulated and select a valve size that can accommodate the flow without creating excessive back pressure.
Fluid Medium
Another important consideration when choosing air valves is the type of fluid medium that will be flowing through the system. Different valves are designed to handle specific fluid mediums, such as air, water, or corrosive chemicals. It is crucial to select a valve that is compatible with the properties of the fluid to prevent any potential damage or malfunctions. Understanding the characteristics of the fluid medium, including its temperature, viscosity, and chemical composition, is essential in choosing the right valve for the system.
Specialty Applications of Air Valves
Air Valves in Sewage Networks
In sewage networks, air valves play a crucial role in maintaining the efficiency and durability of the system. These valves help to release air pockets that accumulate in the pipes, preventing potential damage and ensuring the smooth flow of wastewater. By releasing trapped air, air valves minimize the risk of pipe corrosion and water hammer effects, ultimately contributing to the overall functionality and longevity of sewage networks.
The Role of Air Valves in Water Distribution Systems
Air valves are integral to the optimal performance of water distribution systems. They effectively release air pockets that may accumulate in pipelines, preventing air locks and reducing the potential for damage to the infrastructure. By consistently eliminating air from the system, these valves help to maintain water quality, minimize energy consumption, and ensure the efficient transportation of water to end users.
Can Air Valves Be Installed Underground?
Yes, air valves can be installed underground to effectively manage air accumulation in pipelines. The underground installation of air valves is particularly beneficial in preventing air locking, reducing the risk of pipe corrosion, and ensuring the smooth flow of fluids within the system. Proper installation and maintenance of underground air valves are essential to guarantee their optimal functionality and long-term performance.
Maintenance and Safety Aspects of Air Valves
Routine maintenance is crucial to ensure the valve system’s proper functioning and longevity. By following a few simple tips, you can keep your valves in top condition and avoid costly repairs or replacements.
Routine Maintenance Tips for Air Valves
Regular Inspection: Conduct regular visual inspections of your air valves to check for any signs of wear, corrosion, or leaks. Addressing any issues early can prevent more significant problems down the line.
Cleaning: Keep the air valves clean from debris, dust, and other contaminants that can affect their performance. Use a mild cleaning solution and a soft cloth to gently wipe the valves.
Lubrication: Apply lubricant to the moving parts of the air valves to keep them operating smoothly. Be sure to use the appropriate lubricant for your specific valve type.
Testing: Periodically test the valves to ensure they open and close properly. This can help identify any malfunctioning valves before they cause any issues in your system.
Safety Precautions and Proper Handling
When it comes to handling air valves, safety should be a top priority to prevent accidents and injuries. Here are some essential safety precautions to keep in mind:
Proper Ventilation: When working with these valves in enclosed spaces, ensure adequate ventilation to prevent the buildup of harmful gases or fumes.
Personal Protective Equipment: Use the necessary protective gear, such as gloves and safety goggles, when handling the valves to protect yourself from potential hazards.
Follow Manufacturer Guidelines: Always adhere to the manufacturer’s guidelines for handling and operating air valves to prevent accidents and ensure proper functionality.
By incorporating these routine maintenance tips and safety precautions into your valve maintenance routine, you can ensure the safe and efficient operation of your systems while prolonging the lifespan of your valves.
Conclusion
In conclusion, air valves are crucial for maintaining the efficiency and functionality of water distribution and sewage systems. By understanding the different types of air valves available, such as air relief valves, air/vacuum valves, and combination air valves, as well as considering factors like size and fluid medium, you can ensure the proper selection and installation of air valves for your specific application. Whether it’s preventing air accumulation or countering negative pressure, the right air valve can make a significant difference in the performance of your system.
FAQ: Usage Areas of Air Valves
An air relief valve is designed to release air that becomes trapped in a pipeline, preventing air locks and ensuring optimal system performance. It is commonly used in water pipelines, irrigation systems, and wastewater treatment plants.
An air/vacuum valve is utilized to automatically release or admit air during the filling or draining of a pipeline, preventing vacuum formation and potential pipeline collapse. It is commonly employed in water supply systems, sewage networks, and industrial process piping.
A combination air valve serves the dual function of releasing air during pipeline filling and admitting air during pipeline draining or surges, while also providing surge protection and vacuum relief. It is often installed in high points of water pipelines, pumping stations, and firefighting systems.
Air relief valves ensure continuous and efficient flow by preventing air accumulation, which reduces the risk of pipeline blockages, water hammer, and cavitation. This ultimately extends the lifespan of the pipeline and associated equipment.
Air/vacuum valves help maintain system integrity by preventing vacuum formation, which can cause pipes to collapse or implode. They also aid in reducing energy consumption and minimizing the need for maintenance and repairs.
Combination air valves protect pipelines from damage caused by surges and vacuum conditions, thereby safeguarding against potential leaks, bursts, and operational disruptions. They also contribute to the efficient and reliable operation of pumping stations.
Air relief valves play a crucial role in irrigation systems by preventing air entrapment, which can impede water flow and lead to uneven distribution. By maintaining optimal system pressure, these valves help maximize water efficiency and crop yield.
In sewage networks and wastewater treatment plants, air/vacuum valves help prevent the formation of vacuum pockets, which can cause sewer lines to collapse and inhibit proper drainage. This enhances system performance and mitigates the risk of environmental contamination.
In firefighting systems, combination air valves protect against potential vacuum collapse and provide surge protection, ensuring that water can be delivered rapidly and consistently in emergency situations. In industrial process piping, these valves help maintain system efficiency and reliability.