The Complete Guide to Butterfly Valve Installation and Maintenance
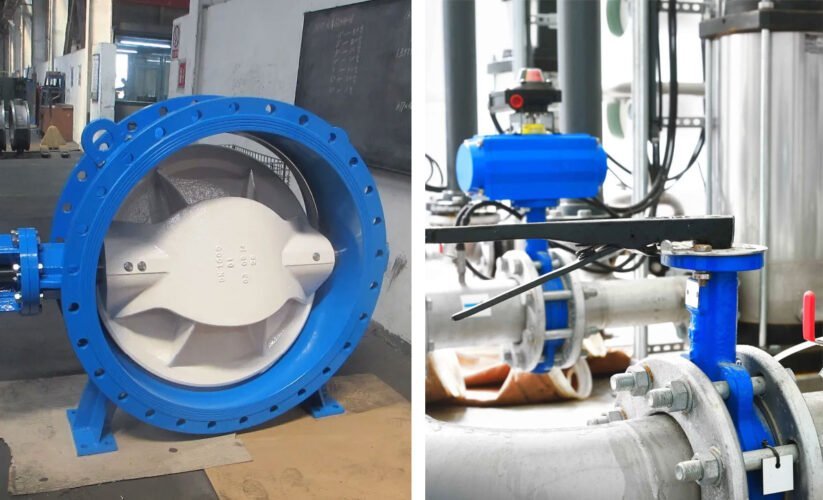
Table of Contents
ToggleImportance of Proper Alignment in Butterfly Valve Installation
In the realm of fluid transportation and control, pipe fitting valves are essential components that govern the movement and management of liquids and gases within industrial systems. This guide will focus on the crucial role of pipe fitting valves, shedding light on their types, functions, materials, and the significance of proper installation and maintenance. Understanding these aspects is fundamental to mastering the art of butterfly valve installation and maintenance, which is vital for ensuring efficient and dependable fluid management systems.
Understanding Butterfly Valves
Butterfly valves are essential components in various industrial and manufacturing processes, enabling the regulation of material flow within pipelines. Understanding butterfly valves involves recognizing their definition, types, components, and common applications in various industries.
Definition and Types of Butterfly Valves
A butterfly valve is a mechanism that controls the flow of materials within large pipe diameters through the quarter-turn rotation of a disc. This valve type comes in various forms, including:
- High-performance butterfly valves
- Resilient-seated butterfly valves
- Triple offset butterfly valves
- Double offset butterfly valves
Each type is designed to serve specific purposes based on the requirements of the application, ensuring efficient flow control in diverse industrial settings.
Butterfly Valve Components and Their Functions
Butterfly valves consist of essential components that enable their functionality. These components include the disc, stem, seat, actuator, and body. The disc is centrally positioned and connected to the actuator, which controls its movement to modulate flow. The seat provides a sealing surface for the disc, ensuring tight shut-off when required. Understanding the functions of these components is crucial for proper installation and maintenance of butterfly valves.
Common Uses of Butterfly Valves in Industry
Butterfly valves find widespread applications across various industries due to their versatility and reliability. Common uses include:
- HVAC systems: Regulating airflow and controlling heating or cooling processes.
- Water treatment and distribution: Modulating water flow in treatment plants and distribution networks.
- Chemical processing: Regulating the flow of chemicals and corrosive substances within industrial facilities.
- Power generation: Controlling the flow of steam and other fluids in power plants.
The diverse applications of butterfly valves highlight their significance in optimizing industrial processes and ensuring efficient resource utilization. Understanding the wide-ranging uses of butterfly valves is vital for implementing appropriate valve solutions in different industrial environments.
Pre-Installation Steps for Butterfly Valves
Before commencing the installation and maintenance of butterfly valves, it is crucial to adhere to a series of pre-installation steps.
Selecting the Right Butterfly Valve
- Size and Type: Consider the specific requirements of the application to determine the appropriate size and type of butterfly valve. Factors such as flow rate, pressure, and pipe diameter should be taken into account to ensure proper valve selection.
- Material: Evaluate the properties of the fluid flowing through the system to select the most suitable valve material that offers corrosion resistance and longevity.
Tools and Materials Needed for Installation
- Wrenches and Spanners: Utilize adjustable wrenches and spanners to facilitate the tightening and adjustment of bolts and nuts during the installation process.
- Gaskets and Seals: Ensure the availability of high-quality gaskets and seals that are compatible with the valve material and the characteristics of the fluid.
- Lubricants: Use appropriate lubricants to reduce friction and enable smooth operation of the valve components.
Preparing the Pipe System
- Clean the Pipeline: Thoroughly clean the pipe system to remove any debris, dirt, or contaminants that may interfere with the proper functioning of the butterfly valve.
- Alignment: Verify the alignment and positioning of the pipeline to ensure a seamless integration of the butterfly valve without any obstructions or misalignments.
By meticulously following these pre-installation steps, the foundation for a successful butterfly valve installation can be established, laying the groundwork for efficient and effective system operation.
Butterfly Valve Step-by-Step Installation Guide
When it comes to installing a butterfly valve, precision is key to ensure proper functionality. The following step-by-step guide will help you navigate through the installation process with confidence.
Aligning the Butterfly Valve in the Pipe System
Before installing the valve, it is crucial to align the connecting pipe flanges accurately. This involves creating adequate separation between the flanges to allow the valve body to be positioned between them without contacting the flange surfaces. For lug-style valves, the valve should be positioned between the flanges and all necessary bolts should be mounted between the valve and the mating flanges. It’s essential to hand-tighten the bolts without fully tightening them to avoid potential damage to the disc or seat faces.
Securing the Valve with Bolts and Flanges
Once the valve is properly positioned between the flanges, it’s important to ensure the valve is centered and the disc moves freely and unobstructed. After confirming the disc alignment, the flange bolts should be uniformly tightened in a specific sequence to achieve consistent compression. This step is critical in securing the valve in place within the pipe system.
Ensuring Proper Seal and Leakage Prevention
After securing the valve with bolts and flanges, it’s essential to open and close the valve to examine the actuator travel stop settings for correct disc alignment. This ensures that the valve operates without any interference. Additionally, the valve should be installed with the disc in the “ALMOST CLOSED” state, and the use of flange gaskets is not recommended to ensure a proper seal and prevent leakage.
By following these installation steps diligently, the valve will be ready for operation, ensuring efficient and reliable performance within the piping system.
Butterfly Valve Post-Installation Checks
After completing the installation of butterfly valves, it is crucial to perform comprehensive post-installation checks to ensure operational functionality, detect potential leakages, and troubleshoot common installation issues. The following procedures and tests should be conducted:
Testing for Operational Functionality
Upon completing the installation process, a thorough operational functionality test is essential. This includes verifying the valve’s opening and closing mechanism, ensuring it moves freely without any hindrance. Additionally, the valve’s responsiveness to control signals and its ability to regulate flow should be assessed. Any irregularities in the operational functionality must be addressed promptly.
Leakage Testing Procedures
Leakage testing is a critical step to assess the integrity of the installed valve. This involves pressurizing the system to the designated operating pressure and carefully inspecting the valve and its connections for any signs of leakage. Utilizing appropriate testing equipment and methods, such as visual inspection, soap bubble testing, or pressure drop measurement, is imperative to identify and address any potential leaks effectively.
Troubleshooting Common Installation Issues
In the event of common installation issues such as misalignment, improper sealing, or difficulty in actuation, troubleshooting steps must be implemented. This may include verifying alignment, adjusting the sealing components, or examining the actuation mechanism for any obstructions. Thorough troubleshooting is essential to ensure the optimal functionality and performance of the valve post-installation.
Routine Maintenance of a Butterfly Valve
Maintenance plays a crucial role in ensuring the longevity and optimal performance of butterfly valves. By following routine maintenance practices, such as cleaning, lubrication, and periodic inspections, the lifespan of these valves can be extended, and potential issues can be identified and addressed promptly.
Cleaning and Lubrication Best Practices
Proper cleaning and lubrication are essential for the smooth operation of butterfly valves. Before applying lubricant, it’s crucial to clean the valve components thoroughly to remove any accumulated dirt, debris, or old lubricant. Use a mild detergent and water to clean the surfaces, ensuring the removal of any rust or foreign particles that may hinder the valve’s functionality.
Once the valve is clean and dry, apply a recommended lubricant to the shaft, bearings, and seals. The lubricant helps reduce friction, prevents corrosion, and ensures ease of operation. It’s important to use lubricants specifically designed for butterfly valves to maintain their integrity and functionality.
Checking for Wear and Tear
Regular inspection for wear and tear is essential in maintaining the performance of butterfly valves. During routine maintenance, visually inspect the valve components for any signs of wear, such as corrosion, erosion, or damage to seals and O-rings. Pay close attention to the disc, stem, and sealing surfaces to ensure they are free from wear or damage.
Operate the valve to assess its functionality and listen for any unusual noises that may indicate internal damage or wear. By identifying and addressing signs of wear early on, potential malfunctions and costly repairs can be avoided.
Replacing Seals and O-Rings
Seals and O-rings are critical components of butterfly valves, contributing to their sealing integrity and preventing leaks. Over time, these seals may deteriorate due to exposure to operating conditions and environmental factors. As part of routine maintenance, inspect the condition of seals and O-rings, looking for signs of cracking, brittleness, or deformation.
If any damage or degradation is detected, it’s essential to promptly replace the affected seals and O-rings with high-quality, compatible replacements. Proper installation and seating of the new seals are crucial to maintaining the valve’s sealing performance and preventing potential fluid leakage.
By adhering to these routine maintenance practices, including cleaning and lubrication best practices, checking for wear and tear, and replacing seals and O-rings as needed, operators can ensure the optimal performance and longevity of butterfly valves while mitigating the risk of operational issues. Regular maintenance contributes to the reliability and efficiency of these essential components in various industrial applications.
Advanced Maintenance Strategies
Predictive Maintenance Techniques
Predictive maintenance techniques involve using data analysis, monitoring, and inspection to predict equipment failure before it occurs. By leveraging technologies such as vibration analysis, thermography, and ultrasonic testing, maintenance professionals can identify potential issues with butterfly valves. Implementing a predictive maintenance program can help organizations minimize downtime, reduce maintenance costs, and extend the lifespan of their equipment.
When to Schedule Professional Inspections
Professional inspections should be scheduled on a regular basis to ensure the optimal performance of butterfly valves. These inspections can uncover issues that may not be immediately apparent and provide an opportunity to address potential problems before they escalate. It is advisable to align professional inspections with manufacturer recommendations and industry standards to maintain the reliability of valve systems.
Upgrading to High-Performance Butterfly Valves
Consider upgrading to high-performance butterfly valves to enhance the efficiency and longevity of the valve system. High-performance valves offer improved sealing capabilities, reduced maintenance requirements, and enhanced corrosion resistance, making them an attractive option for industries that demand high-performance and reliability from their equipment. Upgrading to high-performance butterfly valves can yield long-term cost savings and operational benefits.
By proactively implementing predictive maintenance techniques, adhering to professional inspection schedules, and considering upgrades to high-performance butterfly valves, organizations can ensure the continued functionality and efficiency of their valve systems.
Conclusion
Mastering the art of butterfly valve installation and maintenance is crucial for ensuring efficient and reliable fluid management systems. Proper installation, regular maintenance, and careful consideration of materials are essential for maximizing the performance and longevity of butterfly valves. By understanding the types, functions, and importance of these valves, industries can optimize their operations and contribute to the seamless flow of fluids in various applications.