Choosing an Air Valve: 5 Key Factors to Consider
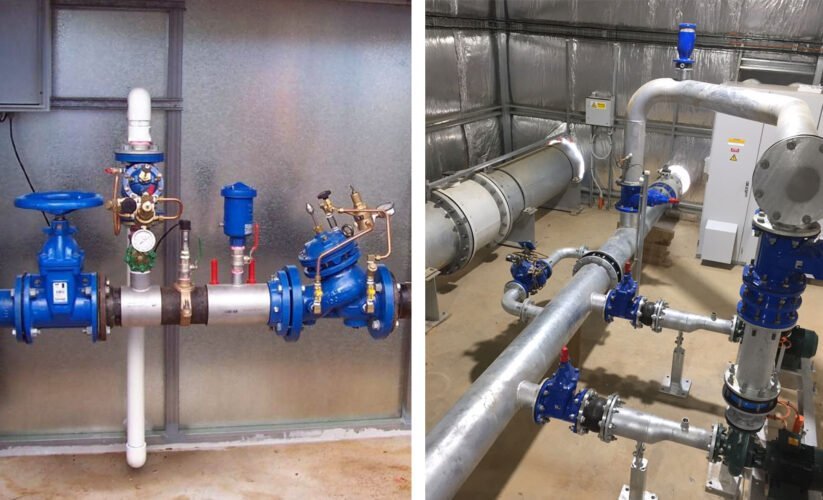
Table of Contents
ToggleChoosing an Air Valve: 5 Must-Know Factors
When choosing an air valve, several key factors need to be considered to ensure the correct valve is selected for the specific application. The type of media being controlled, application conditions, valve function, actuation method, and maintenance requirements are all crucial considerations in the decision-making process. Each factor plays a significant role in determining the effectiveness and longevity of the chosen air valve, ultimately impacting the overall performance of the system.
FAQ about Air Valves in Water Distribution and Industrial Processes
What is the function of air valves in water pipeline systems?
Air valves in water pipeline systems serve to release accumulated gases or admit air during pipeline filling, draining, or operation, ensuring the efficient flow of water.
Where are air valves provided in distribution pipes?
Air valves are placed at the summit of distribution pipes to eliminate the air that accumulates and creates backward pressure, which can impede the flow of water.
What is the role of air valves in irrigation systems?
Air release valves in irrigation systems help remove trapped air, promoting the smooth flow of water in pipelines and ensuring the efficient operation of the irrigation system.
How can air get into a water distribution system?
Air can enter a water distribution system during maintenance activities such as shutting off the water supply or conducting work on the water main, which may introduce air into the system. Running faucets briefly can often resolve this issue.
What are air relief valves and how do they differ from air release valves?
Air relief valves and air release valves are two terms used interchangeably to refer to the same type of valve, which is designed to release air or admit air into a system to maintain optimal operation.
How do air valves contribute to the efficiency of industrial processes?
In industrial processes involving liquid pipeline systems, air valves are crucial for releasing trapped air, preventing air locking, and ensuring the smooth and efficient flow of liquids through the pipelines.
What are the different types of air valves used in water distribution and industrial processes?
Common types of air valves include air release valves, air relief valves, and combination air valves, each serving specific functions such as releasing air, admitting air, and preventing air locking in pipeline systems.
How do air valves contribute to the overall safety of water distribution systems?
By preventing air locking and ensuring the continuous and efficient flow of water, air valves contribute to the safety and reliability of water distribution systems, helping to minimize the risk of blockages and pressure issues.
What maintenance is required for air valves in water distribution and industrial systems?
Regular inspection and testing of air valves, along with prompt repairs or replacements as needed, are essential to ensure the proper functioning and reliability of air valves in water distribution and industrial systems.
Are there specific considerations for selecting and installing air valves in water distribution systems?
When selecting and installing air valves, factors such as pipeline size, flow rates, pressure conditions, and the specific requirements of the water distribution system must be carefully considered to optimize the performance of the air valves.
What are the potential issues that can arise with air valves in water distribution systems?
Common issues with air valves may include air leakage, malfunctioning due to debris accumulation, or inadequate air release, which can impact the efficiency and reliability of water distribution systems and industrial processes.
Understanding Media Compatibility with Air Valves
Material Selection for Different Media Types
When selecting an air valve, it is crucial to consider the material compatibility for the specific media it will handle. Different media types may require specific materials to prevent contamination or reaction. For instance, stainless steel, brass, and food-grade plastics are commonly used for valves intended for drinking water applications. On the other hand, gases may demand tightness requirements to avoid leakage, with specific standards such as ISO 15848-1 and VDI 2440 (TA-Luft) being applicable.
Considerations for Harsh or Corrosive Environments
In environments with harsh or corrosive conditions, the choice of materials for air valves becomes increasingly critical. Factors such as exposure to aggressive chemicals, extreme temperatures, or high humidity levels can impact the longevity and performance of the valve. In these scenarios, selecting corrosion-resistant materials and coatings is essential to ensure the durability and reliability of the air valve.
Safety Considerations for Pressurized Gases
When dealing with pressurized gases, safety considerations take precedence. Valves must exhibit internal tightness when closed to avoid leakage, meeting stringent requirements for release into the atmosphere to prevent fugitive emissions. Furthermore, the valve’s ability to handle the specific pressure class and minimize pressure drop is pivotal in ensuring efficient operation and reducing energy consumption. Prioritizing safety features and adherence to industry standards is imperative when selecting air valves for pressurized gas applications.
Sizing and Application Conditions for Optimal Performance
Valve sizing plays a critical role in determining the efficacy of a pneumatic system. Proper valve sizing ensures optimal performance and efficient operation. When selecting an air valve, it’s essential to consider various factors, including the effects of temperature and pressure, as well as flow rate requirements and valve efficiency.
Importance of Proper Air Release Valve Sizing
Correct sizing of air valves is fundamental to achieving reliable and efficient system operation. Undersized valves can lead to insufficient airflow, resulting in decreased performance and potential system malfunctions. Conversely, oversized valves may lead to energy wastage and inefficiencies. By accurately sizing the air valve to match the application, you ensure that the system operates at its peak performance.
Effects of Temperature and Pressure on Air Relief Valve Choice
Temperature and pressure significantly impact the choice of air valves. Different materials and designs are suitable for varying temperature and pressure conditions. High temperatures can affect the valve’s internal components, potentially causing premature wear and failure. Similarly, extreme pressure differentials can impact the valve’s sealing capabilities. Selecting valves rated for the specific temperature and pressure conditions of the application is crucial for longevity and reliability.
Flow Rate Requirements and Valve Efficiency
Understanding the flow rate requirements of the system is essential for selecting the appropriate air valve. Factors such as maximum flow rate, required response time, and pressure drop influence the choice of valve. Additionally, considering valve efficiency is crucial to minimize energy consumption and optimize system performance. Efficiency considerations include the valve’s flow coefficient (Cv), which indicates the valve’s ability to pass fluid, and the valve’s overall design for efficient energy usage.
By carefully assessing these sizing and application conditions, you can select the most suitable air valve for your pneumatic system, ensuring optimal performance and reliability.
Selecting the Right Valve Function for Your System
Differences Between 2-Way and 3-Way Valves
When selecting an air valve for your system, it’s crucial to consider whether a 2-way or 3-way valve is the most suitable option. A 2-way valve controls the flow of fluid to either start or stop the flow, whereas a 3-way valve manages the direction of flow, allowing the media to divert in different directions. Understanding the function of each valve type is essential in ensuring optimal performance and efficiency within the system.
The Significance of Valve Orientation and Life Expectancy
Valve orientation and life expectancy play a pivotal role in the overall functionality of the system. The orientation of the valve determines the direction of media flow and must align with the specific requirements of the application. Additionally, considering the life expectancy of the valve is crucial in maintaining system reliability and reducing the frequency of replacements, ultimately optimizing operational costs.
Evaluating the Need for Diverging or Mixing Media
Assessing the necessity for diverging or mixing media within the system is an essential factor in selecting the appropriate air valve. Understanding the media requirements and the desired outcome of the system’s operation will determine whether a diverging or mixing functionality is necessary. This evaluation is critical in ensuring that the chosen valve aligns with the specific demands of the application, thereby maximizing operational efficiency.
Choosing the Appropriate Actuation Method for Air Valves
Manual vs. Automatic Operation
When choosing an air valve, one of the key considerations is whether to opt for manual or automatic operation. Manual operation is simple and cost-effective, making it suitable for basic applications where adjustments are infrequent. Alternatively, automatic operation provides greater precision and efficiency, making it ideal for applications that require frequent adjustments or where precise control is essential.
Comparing Electric, Pneumatic, and Hydraulic Actuators
Electric, pneumatic, and hydraulic actuators are the primary options for automatic operation of air valves. Electric actuators offer precise control and are suitable for a wide range of applications. Pneumatic actuators are known for their quick response and reliable performance, making them a popular choice for many industrial applications. Hydraulic actuators are ideal for heavy-duty applications that demand high force, although they require careful maintenance and pose potential environmental risks.
Determining the Need for Valve Position Indicators or Positioners
Valve position indicators or positioners are crucial for monitoring and controlling the position of air valves in automatic systems. These accessories provide real-time feedback on valve position, enabling operators to ensure optimal performance and troubleshoot any issues promptly. When choosing an air valve, it’s essential to assess the specific operational requirements and consider whether the inclusion of position indicators or positioners is necessary to achieve the desired level of control and reliability.
Maintenance and Serviceability of Air Valves
Frequency of Maintenance and Valve Accessibility
Maintaining air valves is crucial in ensuring their optimal performance and longevity. The frequency of maintenance largely depends on the type of valve and the specific application it serves. In general, it is recommended to conduct routine maintenance at regular intervals to prevent potential issues that can disrupt operations. When considering air valves, it is essential to prioritize accessibility for maintenance. Easy access to the valve for inspection, cleaning, and repairs can significantly reduce downtime and labor costs associated with maintenance activities.
Advantages of Ball Valves for Easy Servicing
Ball valves offer distinct advantages when it comes to servicing and maintenance. Their design features a simple structure with few moving parts, facilitating ease of maintenance. The ability to completely disassemble the valve for thorough cleaning and servicing ensures efficient operation and prolonged lifespan. Additionally, the straightforward maintenance process of ball valves minimizes the need for specialized tools and lengthy downtime, making them a practical choice for various industries.
Benefits of 3-Piece Valve Configurations for Maintenance
Opting for 3-piece valve configurations can enhance maintenance and serviceability. These valves are designed to be easily disassembled into three main components, allowing for straightforward maintenance procedures. The segmented construction simplifies cleaning, inspection, and potential part replacement without requiring the removal of the entire valve from the pipeline. This modular approach to maintenance not only saves time but also streamlines the overall servicing process, contributing to operational efficiency.
By considering the maintenance and serviceability aspects of air valves, businesses can strategically select valves that align with their maintenance schedules and operational requirements. This proactive approach can lead to improved reliability, cost savings, and sustained productivity in the long run.
Conclusion
In conclusion, when choosing an air valve, it is crucial to consider the media type, application conditions, valve function, actuation method, and maintenance requirements. Selecting the correct valve material based on the characteristics of the liquid or gas type being controlled, ensuring proper sizing and understanding the operating conditions are essential factors to consider. Additionally, determining the valve’s function and actuation method, along with evaluating the maintenance requirements, will contribute to the optimal selection of an air valve for your specific application.