The Standards Implemented by Top Butterfly Valve Manufacturers
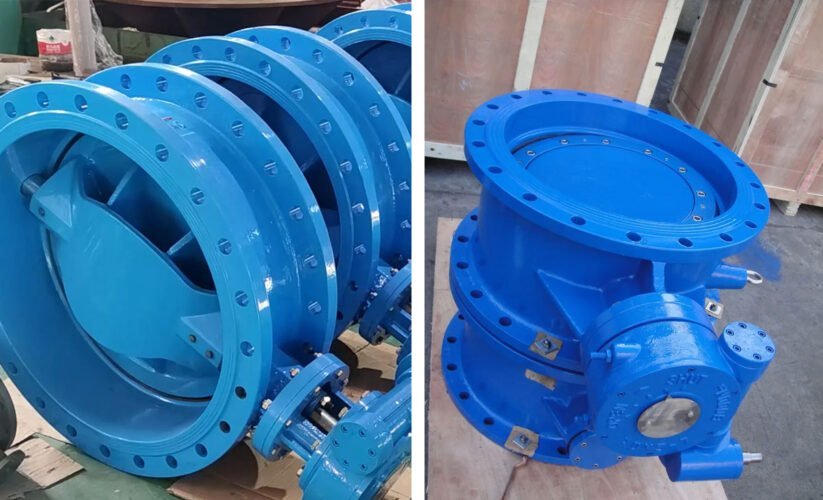
Table of Contents
ToggleQuality Control in Butterfly Valve Production
Definition and Objectives of Quality Control
Quality control in butterfly valve production refers to the systematic processes and procedures implemented to ensure that the manufactured valves meet the required standards and specifications. The primary objectives of quality control include maintaining consistency in product quality, adhering to industry regulations, and meeting customer expectations. By incorporating rigorous quality control measures, butterfly valve manufacturers can enhance the reliability and performance of their products.
Steps in Ensuring High-Quality Butterfly Valve Production
The process of ensuring high-quality butterfly valve production begins with the careful selection of raw materials. Through meticulous material testing and inspection, manufacturers can ascertain the suitability and durability of the components. Subsequently, precise machining, assembly, and finishing techniques are employed to create products that conform to exacting standards. Additionally, adherence to strict quality control protocols at every stage of production is essential to achieve optimum results.
Inspection and Testing Procedures for Butterfly Valves
Comprehensive inspection and testing procedures are integral to quality control in butterfly valve production. This involves dimensional checks, pressure testing, leak testing, and material analysis to validate the integrity and functionality of the valves. Utilizing advanced testing equipment and methodologies facilitates the identification of any defects or irregularities, ensuring that only flawless products are released to the market.
Role of Quality Control in Valve Longevity and Reliability
Quality control plays a pivotal role in determining the longevity and reliability of butterfly valves. By systematically monitoring and addressing potential issues during the production process, manufacturers can minimize the likelihood of premature wear, corrosion, or operational failures. Through stringent quality control practices, the resultant valves exhibit enhanced resilience, operational efficiency, and overall performance, thereby bolstering their longevity and reliability in diverse industrial applications.
Quality Assurance Practices for Butterfly Valve Manufacturers
Quality Assurance vs. Quality Control
Quality assurance is the proactive approach taken to prevent defects in products by focusing on processes. It involves establishing a quality management system, whereas quality control is the reactive process of identifying and correcting defects in finished products. By implementing rigorous quality assurance practices, top butterfly valve manufacturers can ensure consistent product quality and customer satisfaction.
Implementing a Quality Management System
Top butterfly valve manufacturers implement a robust quality management system to ensure that all processes and procedures adhere to specified standards. This system encompasses quality policies, objectives, and responsibilities, providing a framework for achieving and maintaining high-quality products. By integrating quality management into every aspect of production, manufacturers uphold their commitment to delivering reliable butterfly valves to their customers.
Continuous Improvement and Training in Valve Manufacturing
Continuous improvement is a fundamental aspect of quality assurance in valve manufacturing. Manufacturers invest in ongoing training and skill development programs to ensure that employees are equipped with the latest techniques and knowledge. This emphasis on continuous improvement enables manufacturers to adapt to changing industry trends and technological advancements, leading to the production of superior butterfly valves.
Traceability and Accountability in Production
Traceability and accountability are essential components of quality assurance in valve manufacturing. Manufacturers implement meticulous tracking systems to trace the origins and processing of materials used in valve production. This level of traceability ensures that any potential issues can be swiftly identified and addressed, maintaining the integrity of the final product. Additionally, by establishing clear accountability throughout the production process, manufacturers uphold the highest standards of quality and reliability in their butterfly valves.
International Standards for Butterfly Valve Manufacturers
ISO Certification and Its Significance
The ISO 9001 certification is a critical quality management standard for butterfly valve manufacturers. This certification ensures that the manufacturer has a robust quality management system in place, guaranteeing consistent product quality and customer satisfaction. Adhering to ISO standards also signifies a commitment to continuous improvement and adherence to international best practices in valve manufacturing.
ANSI Standards and Their Impact on Butterfly Valves
The American National Standards Institute (ANSI) plays a vital role in setting standards for butterfly valves, ensuring their safety, reliability, and interchangeability. Manufacturers must comply with ANSI standards to ensure that their valves meet specific performance and quality criteria, providing end-users with confidence in the product’s performance and compatibility.
API Specifications for Butterfly Valves
The American Petroleum Institute (API) specifications are crucial for butterfly valve manufacturers serving the oil and gas industry. Compliance with API standards ensures that valves meet the stringent requirements for performance, durability, and safety, meeting the demanding operational conditions within the sector. Manufacturers adhering to API standards demonstrate their capability to produce valves suitable for critical applications in the energy industry.
CE Marking and Its Importance in Valve Manufacturing
For butterfly valve manufacturers exporting to the European Union, obtaining the CE marking is essential. This indicator affirms that the valves meet EU regulatory requirements for safety, health, and environmental protection. It assures that the manufacturer has conducted conformity assessments, making their valves suitable for use within the European Economic Area, enhancing market access and competitiveness.
Top Butterfly Valve Manufacturers’ Commitment to Excellence
Investment in Research and Development
Top butterfly valve manufacturers prioritize investment in research and development to ensure the continuous improvement of their products. Through extensive research, they aim to enhance the design, materials, and functionality of their valves, meeting the evolving needs of various industries. This commitment to innovation allows them to stay ahead of the curve, delivering cutting-edge solutions that set the standard for quality and performance in the market.
Adopting Latest Technologies for Enhanced Quality
Embracing the latest technologies is a key focus for top butterfly valve manufacturers. By incorporating advanced manufacturing techniques and precision engineering, they elevate the quality and reliability of their products. Utilizing state-of-the-art technologies enables them to produce valves with superior durability, efficiency, and performance, meeting the stringent demands of diverse applications across industries.
Collaboration with Industries to Meet Specific Needs
Top butterfly valve manufacturers actively engage in collaborative partnerships with industries to gain insights into specific operational challenges and requirements. By understanding the unique needs of different sectors, they tailor their valve solutions to address industry-specific demands effectively. This collaborative approach ensures that their products are finely tuned to deliver optimal performance in varying environments, enhancing overall operational efficiency for their partners.
Case Studies
Real-world case studies serve as compelling evidence of the commitment to excellence demonstrated by top butterfly valve manufacturers. These case studies showcase the successful implementation of their valves in complex industrial settings, highlighting the positive impact on operational efficiency, reliability, and cost-effectiveness. Through detailed and verifiable case studies, manufacturers underscore their dedication to delivering high-quality solutions that yield tangible benefits for their clients.
Future Trends in Butterfly Valve Manufacturing
Innovations in Design and Materials
The future of butterfly valve manufacturing is expected to be shaped by innovative design and materials. Manufacturers are investing in research and development to create valves with improved performance, durability, and efficiency. Advanced materials such as corrosion-resistant alloys, polymers, and composites are being explored to enhance the reliability and longevity of butterfly valves. These innovations aim to meet the evolving needs of industries, ensuring that valves can withstand harsh operating conditions while maintaining optimal performance.
The Role of Digitalization in Quality Assurance
Digitalization is revolutionizing quality assurance in butterfly valve manufacturing. Advanced technologies such as IoT (Internet of Things) sensors, data analytics, and AI (Artificial Intelligence) are being integrated into manufacturing processes to monitor quality in real time, identify potential issues, and optimize production efficiency. This digital transformation allows manufacturers to proactively detect deviations, improve accuracy, and ensure consistent quality across the manufacturing line, ultimately enhancing the reliability and performance of butterfly valves.
Sustainability and Eco-Friendly Manufacturing Practices
The future of butterfly valve manufacturing also emphasizes sustainability and eco-friendly practices. Manufacturers are increasingly adopting environmentally conscious approaches, such as using recyclable materials, reducing energy consumption, and optimizing production processes to minimize waste and emissions. By implementing sustainable practices, butterfly valve manufacturers aim to reduce the environmental impact of valve production while meeting the growing demand for eco-friendly solutions in various industries. This commitment to sustainability aligns with global efforts to promote environmental responsibility and create a greener, more sustainable future.