What Does CWP Mean on a Ball Valve?
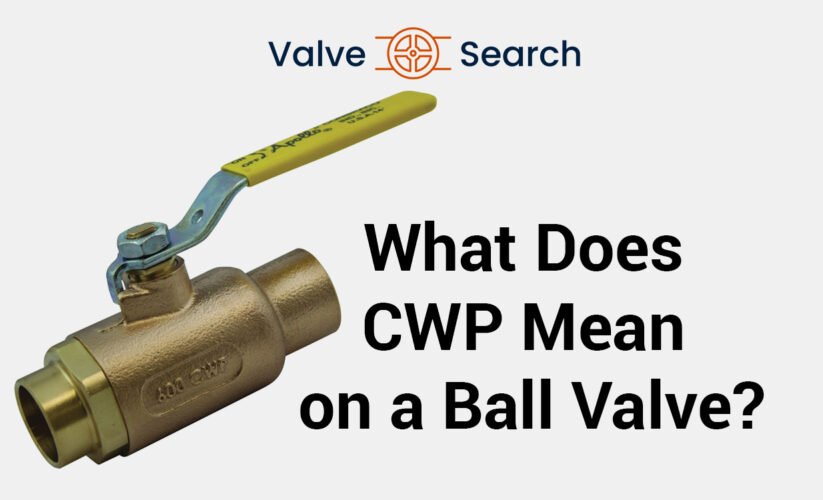
Understanding CWP in the Context of Ball Valves
In the world of fluid mechanics and valve selection, professionals often encounter various technical specifications and ratings that ensure the optimal performance of valve systems in their applications. Among these, CWP, an acronym for Cold Working Pressure, is a pivotal criterion, particularly when selecting and applying ball valves in systems where reliability and safety are paramount. This article aims to demystify CWP, delineating its importance in the selection and application of ball valves, enriched with real-life application scenarios and comparisons with other valve types.
What is valve CWP?
Cold Working Pressure (CWP) represents the maximum pressure at which a valve, in this case, a ball valve, can operate safely when dealing with fluids at standard room temperature (around 20°C or 68°F). It is crucial to note that this rating is determined based on the valve being in a cold condition; hence, it doesn’t account for any additional stresses or potential structural weaknesses that may arise at elevated temperatures. This distinction is vital for ensuring the integrity and reliability of the valve under specific operating conditions.
Why CWP Matters for Ball Valves
Ball valves, known for their robust design offering tight shutoff with minimal pressure drop, are ubiquitous across various sectors, including oil and gas, petrochemical, and water treatment, to name a few. These applications often entail handling media under high pressure and, at times, at fluctuating temperatures. Cold Working Pressure rating serves as a baseline indicating the valve’s capability to withstand pressures safely without risk of failure, leakage, or damage when operated within the temperature constraints the cold working pressure implies.
Choosing a ball valve with an adequate CWP rating is imperative for ensuring safety, efficiency, and longevity of the valve and the system it serves. Underestimating the importance of it can lead to catastrophic failures, posing safety hazards and incurring significant operational losses.
Real-Life Applications
Consider a scenario in the petrochemical industry where ball valves are used in a pipeline transporting natural gas at room temperature. In this instance, the CWP rating of the ball valve guides engineers to select a valve that can safely handle the pipeline’s operational pressure, ensuring a robust seal and reliable operation without the risk of gas leakage or valve failure.
Another application scenario could be in high-pressure water treatment systems. Here, engineers must consider this rating to ensure that the ball valves installed can withstand the system’s pressure demands, preventing any breach that could lead to system downtime or maintenance issues.
CWP vs. Other Valve Ratings
When comparing CWP with other ratings such as WOG (Water, Oil, Gas) or the more specific steam ratings, it becomes apparent that CWP provides a more conservative baseline, particularly useful in applications where the medium is at room temperature or where temperature fluctuations are not significant. For high-temperature applications, other ratings that factor in temperature effects, such as the WSP (Working Steam Pressure), become more relevant.
CWP and Ball Valve Design Considerations
The design and material composition of a ball valve directly influence its CWP rating. For instance, ball valves made of forged steel tend to have higher pressure ratings compared to those made from cast iron or plastic, due to the inherent strength and durability of forged steel under pressure. Furthermore, the thickness of the valve body and the design of the ball and stem also play critical roles in determining the valve’s CWP rating.
Conclusion
The significance of the Cold Working Pressure rating in the context of ball valves cannot be overstated. It is a critical factor that engineers and professionals must consider when selecting valves for their specific applications, especially in scenarios involving high-pressure mediums at ambient temperatures. Understanding CWP allows for the informed selection of ball valves, ensuring operational safety, efficiency, and longevity of both the valve and the system it integrates into.
As technology evolves and new materials and designs come to the forefront, the importance of CWP and its role in valve selection remains constant, providing a fundamental benchmark for evaluating valve performance under pressure.