The Crucial Role of Swing Check Valves in Industrial Flow Control
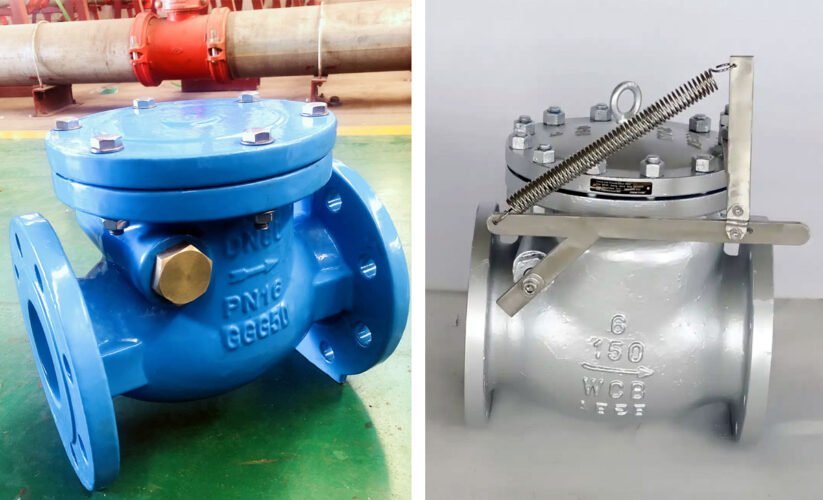
Table of Contents
ToggleIntroduction
Swing check valves play a significant role in maintaining flow control in various industrial settings. These simple devices are designed to allow the flow of liquids or gases in one direction while preventing backflow. Utilizing a swinging disc on a hinge, swing check valves come in different sizes and designs to accommodate specific application requirements. The functioning of swing check valves is based on the movement of the internal rocker swing structure, which ensures a complete absence of valve leaks. As fluid travels downstream, it causes the valve to open, and when the fluid reverses direction, the valve automatically closes, effectively sealing the valve.
- Swing check valves play a crucial role in maintaining flow control in industrial settings.
- These valves are designed to allow fluid to flow in one direction while preventing reverse flow.
- The swing mechanism allows the valve to open when fluid is flowing in the correct direction and close to prevent backflow.
- Proper installation of swing valves is essential to ensure efficient flow control and prevent damage to equipment.
- In industrial applications, these valves are commonly used in piping systems to maintain process efficiency and safety.
- The design of swing valves allows for minimal pressure drop when the valve is open, making them suitable for various industrial processes.
- Regular maintenance and inspection of swing valves are necessary to ensure their optimal performance and reliable flow control.
There are two main types of swing check valves: top-hinged and tilting disc. While both types operate similarly, they differ in the manner in which the valve disc is deployed. The top-hinged swing check valve, being the prevailing and widely used design, allows the disc to swing freely, aligning with the turbulent flow profile when it swings open. On the other hand, the tilting disc swing check valve opens fully at lower flow rates and closes quicker than a standard check valve, reducing reverse flow water hammer.
Swing check valves are constructed using a variety of materials commonly used in many types of valves, ensuring durability and reliability in industrial applications.
Understanding Swing Check Valves in Industrial Flow Control
The Basic Mechanics of Swing Check Valves
Swing check valves are crucial components in fluid control systems, designed to regulate the flow of fluids in one direction while preventing backflow. They operate using a swinging disc or flap that moves freely on a hinge or pivot. When fluid flows in the intended direction, the pressure pushes the disc open, allowing the fluid to pass through. However, in the case of backflow, the disc swings back into position, creating a seal and preventing fluid from flowing in the opposite direction.
Distinguishing Top-Hinged and Tilting Disc Valves
There are two main types of swing check valves: horizontal swing check valves and vertical swing check valves. Horizontal swing valves have a disc that swings on a horizontal axis perpendicular to the flow direction, making them suitable for horizontal flow applications. On the other hand, vertical swing valves have a disc that swings on a vertical axis parallel to the flow direction, making them ideal for vertical or inclined flow applications.
Selecting the Right Swing Check Valve for Industrial Use
When selecting a swing check valve for industrial use, it is essential to consider factors such as the flow direction, pressure requirements, temperature range, and the specific characteristics of the fluid being handled. Understanding the operational needs and environmental conditions will help in choosing the most suitable swing check for the intended industrial application.
The Importance of Swing Check Valves in Industrial Systems
Preventing Backflow and Maintaining Safety
Swing check valves are essential components in industrial systems, particularly in preventing the occurrence of water hammer effects. Water hammer, identified by sudden pressure surges in pipelines, can result in significant damage to pipes, valves, and other crucial equipment. Swing check valves act as a critical barrier, effectively preventing the reversal of flow and minimizing the impact of water hammer. Their unique design facilitates rapid closure, swiftly swinging shut when a sudden pressure surge occurs, thereby averting the backward flow of fluid and reducing the intensity of water hammer. This attribute is pivotal in safeguarding the safety and integrity of industrial systems.
Enhancing System Efficiency with Swing Check Valves
Beyond their role in preventing water hammer, swing check valves contribute significantly to the overall efficiency of industrial pipeline systems. By maintaining a unidirectional flow, these valves ensure a smooth and uninterrupted transfer of fluid. This, in turn, enhances the operational efficiency of the system, minimizes energy loss, and improves overall performance. Their ability to facilitate efficient flow management underscores the critical role swing check valves play in enhancing the efficiency of industrial processes.
Application-Specific Advantages of Swing Check Valves
When considering the application of swing check valves, it is essential to recognize their specific advantages in industrial settings. These valves are particularly beneficial in industries where the prevention of backflow is crucial for operational safety and efficiency. Their rapid closure and dissipation of kinetic energy make them vital for mitigating the effects of water hammer, thus safeguarding industrial equipment and minimizing potential disruptions. Additionally, selecting check valves from reputable manufacturers ensures that these components meet industry standards and are tailored to withstand the unique demands of industrial applications, further underscoring their essential role in diverse industrial systems.
Design Features of Swing Check Valves
Swing check valves play a crucial role in maintaining flow control in industrial settings. Understanding the design features of swing check valves is essential for ensuring optimal performance and reliability in various applications.
Materials Used in Swing Check Valve Construction
Swing check valves are constructed using a variety of materials to ensure compatibility with different operating conditions and media. Common materials include stainless steel, carbon steel, brass, and bronze. The choice of material is determined by factors such as pressure, temperature, and the nature of the fluid being handled. For corrosive or abrasive applications, specialized alloys and coatings may be used to enhance durability and longevity.
The Role of Cracking Pressure in Valve Performance
Cracking pressure, also known as the opening pressure, is a critical factor in the performance of swing check valves. It refers to the minimum upstream pressure required to initiate the opening of the valve and allow fluid flow. Proper consideration of cracking pressure is essential in the selection and sizing of swing check valves to ensure efficient operation within specific flow conditions and prevent undesired backflow.
Leak Prevention and Internal Design Considerations
Swing check valves are designed to minimize the risk of leakage and ensure a reliable shutoff when the flow stops. The internal design features of swing check valves, such as the seating arrangement, disc geometry, and hinge mechanism, are engineered to provide effective sealing and prevent fluid leakage in both open and closed positions. Additionally, internal components are optimized to reduce turbulence and pressure drop, contributing to improved overall system performance.
Installation and Maintenance of Swing Check Valves
Best Practices for Swing Check Valve Installation
When installing swing check valves in industrial settings, it is crucial to follow best practices to ensure optimal performance. Begin by selecting the right valve size and material suitable for the specific application. Proper valve support and alignment must be ensured during installation to prevent stress on the piping system. It is essential to use appropriate gaskets and seals to prevent leaks. Additionally, follow manufacturer guidelines and industry standards for installation procedures.
Routine Maintenance for Long-Term Reliability
To guarantee long-term reliability of swing check valves, regular maintenance is imperative. This includes periodic inspections to check for wear, corrosion, or any signs of damage. Proper lubrication of moving parts is necessary to ensure smooth operation. Additionally, cleaning and flushing the valve and its components should be performed to remove any debris or build-up that may affect functionality. Adhering to a maintenance schedule will help prevent unexpected issues and prolong the lifespan of swing valves.
Troubleshooting Common Swing Check Valve Issues
In industrial settings, certain issues may arise with swing check valves, affecting flow control. Common problems include leaking, noisy operation, or failure to close properly. When troubleshooting these issues, it is important to check the condition of the sealing surfaces and flapper to identify any damage or wear. Additionally, inspect the internal components for any obstructions or foreign objects that may be impeding the valve’s function. Regular testing of swing valves to verify proper sealing and functionality is essential to address and mitigate potential issues.
Comparing Swing Check Valves with Other Check Valve Types
Swing check valves and spring check valves are both effective in preventing reverse flow, yet they differ in their design and functionality. When deciding between these valve types, it is crucial to understand their unique characteristics and consider the specific requirements of the system or application in question.
Swing Check Valves vs. Ball Check Valves
Swing check valves utilize a swinging flap to regulate the flow of fluids or gases, whereas ball check valves use a ball to control the flow. The swinging motion in check valves allows for larger flow capacity, making them suitable for applications with horizontal forward flow. On the other hand, ball check valves are advantageous for their tight seal and minimal pressure drop, making them ideal for systems with limited space.
When to Choose Swing Check Valves Over Others
Swing check valves are particularly suitable for systems with horizontal forward flow or vertical upward flow due to their swinging motion. They are cost-effective and offer large flow capacity, making them a practical choice for applications such as firefighting equipment, sewage system flood prevention, and toilet flush mechanisms. However, when considering systems with downward vertical flow or limited space, ball check valves may be more suitable due to their tight seal and minimal pressure drop.
By carefully evaluating the specific flow requirements and space limitations of the system, the most appropriate check valve type can be selected to ensure optimal flow control.
Case Studies: Swing Check Valves in Action
Success Stories in Water and Wastewater Management
In the water and wastewater management sector, swing check valves have played a crucial role in maintaining flow control and preventing backflow. For instance, in University boiler feed lines, swing check valves effectively addressed low flow and chatter issues. Similarly, in mine dewatering applications, these valves effectively mitigated water hammer concerns. The success stories in this sector demonstrate the reliability and efficiency of swing valves in ensuring continuous flow and preventing disruptions in water and wastewater management systems.
Customized Swing Check Valves for Unique Industrial Needs
Industries often encounter unique challenges that require tailored solutions. Swing check valves have been customized to address specific industrial needs, such as in the natural gas sector where they were deployed to address low flow and excessive cycling in turbo-expander vertical installations. Likewise, in the petroleum production and refining industry, swing check valves were specifically designed to tackle issues like excessive wear, failure, and high flow and foam backup in vertical treater dump valves. These customized solutions showcase the adaptability and versatility of swing check valves in meeting the diverse demands of industrial applications.
FAQ: The Role of Swing Check Valves in Maintaining Flow Control in Industrial Settings
How does a swing check valve maintain flow control in industrial settings?
A swing check valve is designed to allow fluid or gas to flow in one direction while preventing backflow. This helps maintain the desired flow direction and prevents potential damage or disruption to industrial processes.
What are the main applications of swing check valves in industrial settings?
Swing check valves are commonly used in various industrial applications such as water treatment, oil and gas processing, chemical manufacturing, and power generation. They are crucial in maintaining flow control and preventing backflow in these operations.
How does a swing check valve contribute to safety in industrial environments?
By preventing the reversal of flow, swing check valves play a key role in ensuring the safety of industrial operations. They help mitigate the risk of equipment damage, contamination, and potential hazards associated with backflow.
In what ways do swing check valves support efficient fluid and gas flow control?
Swing check valves help optimize the efficiency of fluid and gas flow by allowing unidirectional movement while preventing the wastage of resources and energy that could occur due to backflow or improper flow direction.
What are the key factors to consider when selecting swing check valves for industrial applications?
When choosing swing check valves for industrial settings, factors such as pressure rating, material compatibility, size, and environmental conditions should be carefully evaluated to ensure optimal performance and longevity in the specific industrial environment.
Conclusion
In industrial settings, swing check valves play a crucial role in maintaining flow control and preventing backflow of liquids or gases. Their simple yet effective design allows for seamless flow in one direction while promptly closing to stop reverse flow, ensuring the smooth operation of various applications. Swing valves come in different types, such as top-hinged and tilting disc, each offering specific advantages based on the application’s requirements. Additionally, these valves are constructed using a variety of materials, making them versatile and adaptable to diverse industrial environments. Overall, swing check valves are indispensable assets in maintaining efficient flow control in industrial settings.