The Role of Ball Check Valves in Preventing Backflow in Piping Systems
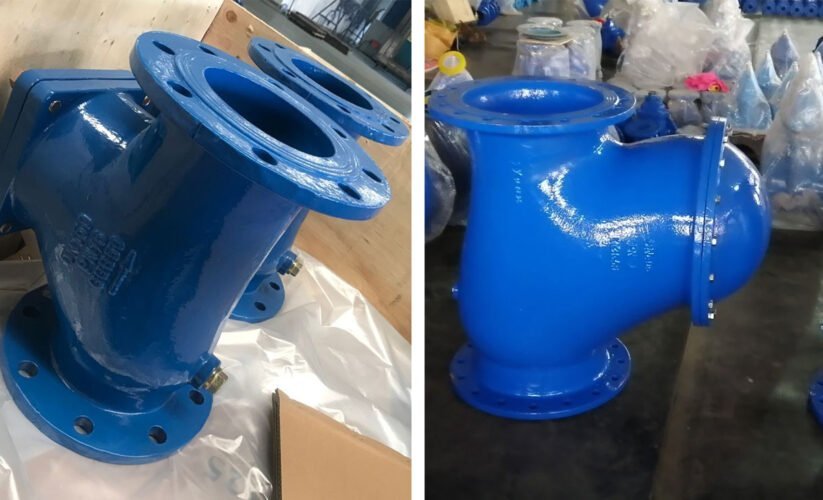
Table of Contents
ToggleFunction of Ball Check Valves in Piping Systems
Ball check valves play a crucial role in preventing backflow within piping systems. These valves utilize a spherical ball within the flow path to allow flow in only one direction, effectively preventing reverse flow. The spring-loaded ball inside the valve body is pushed against a seat when pressurized fluid flows in the desired direction, enabling fluid to pass through. In contrast, when non-pressurized fluid attempts to flow in the opposite direction, the ball closes the flow path by lowering against the seat due to the restoring spring force. This mechanism ensures unidirectional flow, making ball check valves ideal for use in various applications, including plumbing systems, pumping stations, and manufacturing processes.
Summary
- Ball check valves play a crucial role in preventing backflow in piping systems by allowing the flow of fluid in one direction while blocking the reverse flow.
- The design of ball check valves features a spherical ball that moves within the valve body to either allow or block the flow of fluid.
- When there is forward flow, the ball is pushed away from the seat, allowing the fluid to pass through the valve. However, when reverse flow occurs, the ball is pushed back against the seat, creating a seal that prevents backflow.
- Ball check valves are effective in preventing backflow in a wide range of applications, including water and wastewater systems, irrigation systems, and industrial piping.
- The use of ball check valves helps maintain the integrity of piping systems by preventing contamination from backflow and ensuring the proper direction of fluid flow.
- Proper installation and maintenance of ball check valves are essential to their effective performance in preventing backflow in piping systems. Regular inspections and replacement of worn components are necessary to ensure continued reliability.
The simplicity and effectiveness of the ball check valve design make it popular in the plumbing industry, where it is used in water supply systems to prevent backflow and ensure the quality of potable water. Additionally, ball check valves are widely employed in pumping stations to handle solid contaminants and maintain valve performance with minimal maintenance. In manufacturing processes such as injection molding, these valves are crucial for controlling the flow of production fluids in a unidirectional manner. Understanding the operation and application of ball check valves is essential for ensuring the efficiency and reliability of piping systems.
Understanding Ball Check Valves
A ball check valve is a type of valve used to ensure that the flow of fluid in a piping system moves in one direction only. The valve contains a ball that moves within the seat of the valve, allowing flow in one direction while preventing backflow. The Basics of Ball Check Valve Functionality
Ball check valves are designed to open and allow fluid to pass through when the pressure of the fluid exceeds the cracking pressure. Once the pressure drops or reverses, the ball is pushed back into the seat, preventing backflow. This functionality ensures that the fluid only moves in the desired direction, providing effective backflow prevention.
The Design and Components of Ball Check Valves
Ball check valves typically consist of a body, seat, ball, and a cover. The body serves as the main housing for the valve, while the ball moves within the seat to control the flow. The design is often simple and compact, allowing for easy installation and maintenance.
What are the applications of ball check valves?
Ball check valves are commonly used in various industries such as water treatment, chemical processing, oil and gas, and manufacturing. They are ideal for applications where backflow prevention is crucial, such as preventing contamination in water supply systems or protecting sensitive equipment from damage caused by reverse flow.
What are the disadvantages of ball check valves?
While ball check valves are effective in preventing backflow, they may have limitations in certain applications. These include potential for ball wear and leakage, limited flow capacity, and potential for water hammer in high-pressure systems. It’s important to assess the specific requirements of the system to determine the most suitable valve type.
The Importance of Preventing Backflow
Backflow in piping systems poses significant hazards, such as contamination of the clean water supply. This occurrence can lead to serious health risks for the consumers relying on the water from these systems. It is crucial to have measures in place to prevent backflow and maintain the integrity of the water supply.
Hazards of Backflow in Piping Systems
Backflow, defined as the unwanted reversal of water flow, can carry harmful substances back into the potable water supply. This can include contaminants from irrigation systems, wells, or other non-potable water sources, compromising the safety of the water. The potential for waterborne diseases and health concerns makes backflow prevention essential in safeguarding public health.
The Role of Ball Check Valves in Water Supply Systems
Ball check valves play a crucial role in preventing backflow in water supply systems. These valves are designed to allow flow in only one direction, effectively blocking reverse flow and safeguarding against contamination. By utilizing the principle of a ball moving in response to fluid flow, these valves provide a reliable barrier against backflow, ensuring the purity of the water supply.
Incorporating ball check valves into water supply systems is paramount for maintaining the health and safety of communities and individuals reliant on clean water. The installation of these valves is a proactive measure to prevent the risks associated with backflow and maintain the quality of the water supply.
Operating Principles of Ball Check Valves
A ball check valve employs a simple yet effective design to prevent backflow in piping systems. This section will delve into the flow direction and ball dynamics, as well as the interaction between the ball, spring, and seat within the valve.
Flow Direction and Ball Dynamics
The operation of a ball check valve is predicated on the flow of pressurized fluid in one direction, which manipulates the position of the ball inside the valve. As fluid enters the valve, it exerts pressure on the spherical ball, causing it to move against the force of the spring. This movement permits the flow of fluid through the valve. Conversely, when fluid attempts to flow in the opposite direction, the ball, propelled by the restoring spring force, descends and effectively blocks the flow path, preventing backflow.
The dynamic behavior of the ball, coupled with the spring action, enables the valve to regulate the flow direction efficiently, thereby ensuring unidirectional flow within the piping system.
Interaction Between the Ball, Spring, and Seat
Integral to the functionality of a ball check valve is the interaction between its key components: the ball, spring, and seat. The spherical ball, slightly larger in diameter than the seat/through-hole, is designed to fit snugly within the valve body. The tapered design of the valve seat serves to guide the movement of the ball, facilitating a positive seal when the valve is in the closed position. This interaction between the ball and seat ensures effective prevention of backflow, contributing to the reliability and performance of the valve.
The spring, pivotal to the valve’s operation, provides the necessary force to enable the ball to move in response to fluid pressure. The spring stiffness is calibrated to ensure that the ball functions optimally, opening and closing as required to maintain unidirectional flow.
In essence, the seamless interplay between the ball, spring, and seat allows the ball check valve to fulfill its crucial role in preventing backflow within piping systems, making it an indispensable component in various applications.
Applications of Ball Check Valves in Various Industries
Ball check valves play a crucial role in preventing backflow in piping systems across a wide range of industries. Their versatile design and functionality make them indispensable in numerous applications.
Use in Plumbing and Water Infrastructure
In plumbing systems and water infrastructure, ball check valves are essential in ensuring the unidirectional flow of water and preventing any backflow that could contaminate the clean water supply. These valves are commonly used in household plumbing, municipal water supply systems, and wastewater treatment facilities to maintain the integrity and safety of the water supply.
Ball Check Valves in Industrial Settings
In industrial environments, ball check valves are utilized to control the flow of various fluids and gases. They are commonly employed in pipelines for oil, gas, and chemical transportation, where maintaining the directional flow and preventing reverse flow is critical to operational safety and efficiency.
Importance in Pumping Stations
Pumping stations rely on ball check valves to facilitate the movement of liquids through pipes and ensure that the flow remains unidirectional. These valves help to prevent damage to pumps and pipelines by stopping the backflow of fluids, thereby optimizing the performance of pumping systems in various industrial and commercial settings.
Application in Injection Molding
Ball check valves are integral components in injection molding processes, where they enable precise control over the flow of molten materials. By preventing the backward flow of molten plastics or other materials, these valves contribute to the consistency and quality of the injection molding process, supporting the production of high-quality finished products.
Ball check valves, with their diverse applications, continue to be indispensable in maintaining the integrity and efficiency of piping systems across a wide spectrum of industries.
Ball Check Valves vs. Other Valve Types
Ball check valves are an essential component in preventing backflow in piping systems. They offer distinct advantages over other types of valves, such as swing check valves and regular ball valves.
Comparison with Swing Check Valves
Compared to swing check valves, ball check valves are more efficient in preventing backflow due to their simpler design and reliable sealing mechanism. While swing check valves utilize a hinged disc to regulate flow, ball check valves use a spherical ball that provides a tighter seal and reduces the likelihood of leakage. Additionally, ball check valves have a quicker response time, making them suitable for applications where rapid flow reversal needs to be addressed.
Differences from Regular Ball Valves
It’s important to distinguish ball check valves from regular ball valves, as their functionalities vary significantly. Regular ball valves are primarily used for on/off control of fluid flow, whereas ball check valves are specifically engineered to ensure unidirectional flow and prevent backflow. While both valve types feature a spherical component, the operational principles and applications differ, with ball check valves being the preferred choice for backflow prevention in piping systems.
By understanding the distinctions between ball check valves and other valve types, it becomes evident that ball check valves are uniquely tailored to address the challenges associated with backflow in piping systems, offering enhanced reliability and efficiency.
Installation and Maintenance of Ball Check Valves
Installation Guidelines for Optimal Performance
When installing ball check valves in piping systems, it is crucial to ensure proper positioning and orientation. The valve should be mounted horizontally to maximize its efficiency in preventing backflow. Additionally, it is essential to verify that the flow direction aligns with the arrow on the valve body, indicating the correct orientation for installation. Proper sealing of the connections is vital to prevent leaks and to maintain the integrity of the valve’s function. Utilizing a high-quality thread sealant or tape is recommended to achieve an effective seal and prevent potential leaks.
Routine Maintenance
Routine maintenance is essential to ensure the optimal performance and longevity of ball check valves in piping systems. Regular inspections should be conducted to check for any signs of wear, corrosion, or damage. Proper lubrication of the valve components is also crucial to ensure smooth operation and to prevent any potential seizing. Additionally, it is important to clean the valve and surrounding area to prevent the accumulation of debris that could impair its function. Periodic testing of the valve’s functionality is recommended to identify any issues early and prevent potential backflow problems.
Troubleshooting
In the event of any issues with ball check valves in piping systems, troubleshooting may be necessary to identify and rectify the problem. Common issues such as leakage, reduced flow, or unusual noises should be promptly addressed. Inspecting the valve for any signs of damage, wear, or blockages is crucial in troubleshooting these issues. Additionally, ensuring that the valve is properly aligned and sealed is essential to prevent any potential backflow. If troubleshooting efforts do not resolve the issue, consulting a professional for further assessment and maintenance is recommended to prevent any disruptions in the piping system’s functionality.
Material Selection for Ball Check Valves
Before installing a ball check valve, it’s crucial to consider the material it’s made of to ensure optimal performance and longevity. The right material for the valve depends on various factors that influence its operation and lifespan.
Criteria for Choosing the Right Valve Material
When selecting the material for a ball check valve, factors such as the type of fluid flowing through the system, temperature, pressure, and environmental conditions should be taken into account. For instance, if the valve will be used in a corrosive environment, a material with high chemical resistance, such as stainless steel, would be suitable. Additionally, considering the flow characteristics and potential abrasive nature of the media is essential in material selection to prevent premature wear and failure.
Advantages of PVC, Brass, and Stainless Steel Valves
PVC Valves:
- PVC ball check valves are lightweight, cost-effective, and resistant to corrosion and chemical attack, making them ideal for applications involving water, as well as certain acids and alkalis.
- These valves are also easy to install and require minimal maintenance, offering a reliable solution for various low-pressure and non-critical systems.
Brass Valves:
- Brass ball check valves are favored for their durability, making them suitable for applications involving high pressures and temperatures.
- They exhibit excellent resistance to dezincification and provide good flow control, making them a versatile choice for a wide range of industrial and commercial applications.
Stainless Steel Valves:
- Stainless steel ball check valves offer exceptional corrosion resistance and are well-suited for harsh environments, including those with high temperatures and aggressive chemicals.
- These valves provide long-term performance, low maintenance requirements, and a high degree of reliability, making them a preferred choice for critical systems and applications where contamination must be minimized.
Choosing the right material for ball check valves is paramount to ensure the efficiency and longevity of piping systems, as well as to mitigate the risk of backflow incidents. Each material option offers distinct advantages, catering to specific operational requirements and environmental conditions.
Enhancing Valve Performance and Longevity
Overcoming Pump Capacity and Spring Stiffness Issues
Ball check valves play a crucial role in preventing backflow in piping systems, but issues related to pump capacity and spring stiffness can impact their performance and longevity. When a pump’s capacity exceeds the valve’s flow rate, it can lead to premature wear and reduced efficiency. To overcome this, it’s essential to select a ball check valve with a flow capacity that matches or exceeds the pump’s output. Additionally, spring stiffness must be carefully calibrated to ensure it provides sufficient force to close the valve promptly without causing excessive wear. Properly addressing these issues is essential for enhancing the overall performance and durability of ball check valves in preventing backflow.
The Self-Cleaning Feature of Ball Check Valves
One of the key advantages of ball check valves in preventing backflow is their self-cleaning feature. The spherical design of the valve allows for the efficient removal of debris, ensuring the smooth operation of the valve over an extended period. When flow is reversed, any accumulated debris is swiftly dislodged, preventing clogging and maintaining optimal performance. This self-cleaning mechanism not only enhances the longevity of the valve but also reduces the need for frequent maintenance and cleaning, making it a reliable solution for backflow prevention in various piping systems.
FAQs: The Role of Ball Check Valves in Preventing Backflow in Piping Systems
How does a ball check valve prevent backflow?
A ball check valve prevents backflow by using a spherical ball within the flow path to permit flow in only one direction. If the flow direction is reversed, the ball automatically closes to prevent unwanted backflow.
What is the purpose of a ball check valve in a piping system?
The purpose of using a ball check valve is to prevent reverse flow in a pipe. It achieves this by allowing flow in only one direction, automatically closing to prevent backflow if the direction is reversed.
What function does the ball valve serve in piping systems?
A ball valve is a type of quarter-turn valve that controls flow using a pivoting ball drilled through to allow or stop fluid or gas flow. When the hole aligns with the flow direction, it permits flow; when the ball is turned 90 degrees, it stops the flow completely.
Which valve is used to prevent backflow in a pipe?
Check valves are designed to prevent backflow. Backflow occurs when the flow reverses within a pipe, and check valves automatically close to prevent this from happening. The two most common types are the swing check and the lift check.
Conclusion
In the realm of fluid control, the ball check valve plays a crucial role in preventing backflow within piping systems. Its simple yet effective design, incorporating a spring-loaded ball and seat, ensures unidirectional flow, making it an ideal choice for various applications such as plumbing systems, water supply systems, and pumping stations. The self-cleaning action of the ball during operation minimizes maintenance requirements, and the selection of the right valve material is essential for ensuring compatibility in different applications. With its ability to maintain positive seal and prevent contamination, the ball check valve stands as a reliable component in the realm of fluid control technologies.