Guide to Butterfly Valve Parts: Components and Maintenance
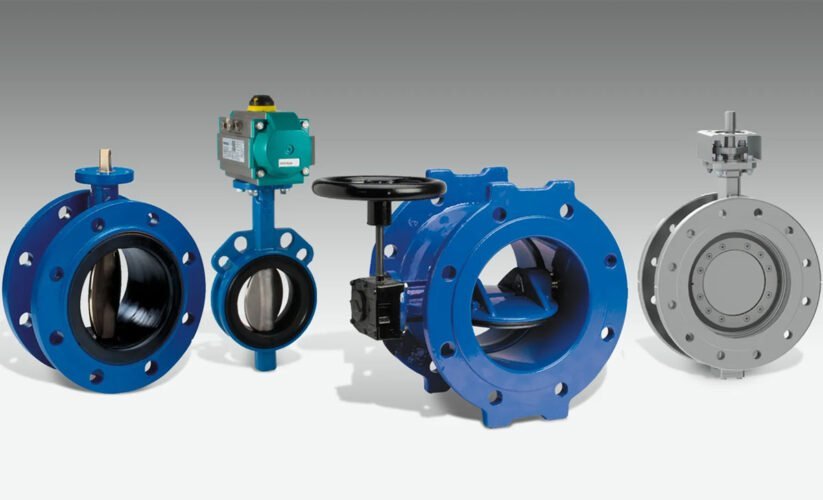
Table of Contents
ToggleExploring the Components of Butterfly Valve Parts
A butterfly valve is a crucial component in various industries due to its simple design, low number of moving parts, and low maintenance costs. It is particularly well-suited for high flow, low-pressure systems due to its ability to seat well and seal tight, even in systems with a large amount of suspended solids. The main components of a butterfly valve include the stem, body, sealing arrangement, upper bearing, lower bearing, bonnet, actuator, seat, and disc. The design of each component varies based on the materials used, flow media, and purpose. The body of a butterfly valve fits between two pipe flanges, with the most common designs being lug and wafer. The flow closure member of a butterfly valve is the disk, and the stem may be a one-piece shaft or a two-piece split-stem design. The seat of a resilient-seat butterfly valve utilizes an interference fit between the disk edge and the seat.
Understanding Butterfly Valves and Their Functions
A butterfly valve is a crucial component in various industrial applications, playing a significant role in controlling the flow of fluids within a piping system. These valves are specifically designed for on-and-off applications and are recognized for their simplistic construction and compact size. They function as quarter-turn rotational motion devices, utilizing a rotary disc to regulate the flow of fluids within pipelines. When the disc is coplanar to the flow cross-sectional area, it fully obstructs the flow. Conversely, in an open position, the fluid is allowed to pass through.
The Role of Butterfly Valves in Industry
Butterfly valves are extensively used in industries where efficient fluid flow control is essential. Their primary function is to regulate the flow of various fluids, including liquids and gases, within pipelines. These valves are particularly ideal for applications that require quick shutoff, tight sealing, and low maintenance. Their ability to provide efficient flow control makes them invaluable in a wide range of industrial processes and systems.
Advantages of Using Butterfly Valves
There are several advantages to using butterfly valves in industrial settings. These include:
- Compact Design: Their compact size and lightweight construction make them easy to install and handle.
- Quick Operation: Butterfly valves can be operated with a simple 90° turn, providing swift on-and-off control of fluid flow.
- Cost-Effectiveness: Their relatively simple design and ease of operation make butterfly valves a cost-effective solution for flow control applications.
- Low Maintenance: With fewer moving parts and a simpler structure compared to other valve types, butterfly valves require minimal maintenance.
In conclusion, butterfly valves play a pivotal role in industrial fluid control systems due to their efficiency, reliability, and cost-effectiveness. Their straightforward operation and low maintenance needs make them an attractive choice for various applications across different industries.
Main Components of a Butterfly Valve
Butterfly Valve Body
The body of a butterfly valve serves as the main structure that houses all the internal components. It is designed to withstand the flow of fluids and to provide a secure connection between the piping system.
The Disc
The disc, also known as the “butterfly,” is the component that controls the flow of fluid. When the valve is open, the disc is positioned parallel to the flow, allowing for unobstructed passage. Conversely, when the valve is closed, the disc rotates perpendicular to the flow, blocking the passage of fluid.
The Stem
The stem is responsible for transmitting the actuation force from the actuator to the disc. It must be strong and durable to handle the torque required to open and close the valve efficiently.
The Seat
The seat forms the tight seal around the disc to prevent leakage when the valve is closed. It is crucial for the efficiency and performance of the valve, as it maintains the integrity of the seal under varying pressures and temperatures.
Upper and Lower Bearings
The upper and lower bearings support the disc and ensure smooth operation during opening and closing. They reduce friction and wear on the moving parts, contributing to the valve’s longevity and reliability.
The Bonnet
The bonnet provides protection for the internal components of the valve, such as the stem and bearings. It also allows for easy access for maintenance and repairs when necessary.
Actuators
Actuators are the driving force behind the movement of the disc. They can be manual, electric, pneumatic, or hydraulic, providing the necessary energy to open, close, and regulate the valve as needed. The choice of actuator depends on the specific application and control requirements.
By understanding the main components of a butterfly valve, it becomes clear how each part contributes to the overall functionality and effectiveness of the valve in controlling fluid flow within a system.
Types of Butterfly Valve Bodies
Lug Style Bodies
Lug style butterfly valves feature lugs on the body of the valve, facilitating direct mounting to the pipe without the use of flanges. This design allows for the counter flange bolts to thread directly into the lug-style butterfly valve. Lug style bodies provide a cost-effective solution for isolation and are suitable for applications with limited space. These valves are available in several options, with the most common being API609 and high performance. The zero offset valve is the most commonly used and least expensive among the lug-style valves. Additionally, these valves are typically resilient seated, but double and triple offset valves can feature metal seats. When using a metal seat valve, it is crucial to ensure the seat is replaceable for longevity.
Wafer Style Bodies
Wafer butterfly valves are sandwiched between two flanges, and none of the bolts on the flange will thread into the valve body itself. This style offers a low-cost solution for isolation. There are various options for wafer-style valves, including AWWA C504, API609, and high-performance designs. The compact design of wafer-style valves makes them ideal for applications with limited space. These valves can be zero, single, double, or triple offset butterfly valves. The zero offset valve is the most commonly used and the least expensive among the options. Most resilient seated wafer-style valves can have replaceable seats, but it is essential to identify the type being used and its benefits for the specific application.
Diverse Butterfly Valve Disc Designs
Orientation and Flow Improvement
Butterfly valves are designed with a variety of disc orientations to suit specific operational requirements. Offset disc or eccentric butterfly valves are engineered to enhance flow and reduce seat wear. The disc is positioned away from the valve shaft, creating a cam-like action during operation, which minimizes friction and wear on the seat. This design ensures a bubble-tight shut-off and provides effective control of the flow through the valve. Additionally, a double offset or high-performance butterfly valve features a disc that is not only placed off-center but also designed to have a slightly conical shape. This innovative design significantly improves flow control by reducing turbulence and pressure drop across the valve.
Materials and Applications
Butterfly valve discs are manufactured from a wide range of materials such as stainless steel, ductile iron, aluminum, and various alloys, allowing for compatibility with diverse operating conditions and media. The choice of disc material is crucial in determining the valve’s suitability for specific applications. For instance, in corrosive environments, a disc constructed from a corrosion-resistant material such as Duplex stainless steel ensures long-term reliability and performance. In high-temperature applications, discs made from heat-resistant alloys guarantee the integrity of the valve under extreme heat conditions. Furthermore, the diversity in disc materials enables butterfly valves to find applications across industries including water treatment, chemical processing, HVAC systems, and oil and gas production.
By incorporating innovative disc designs and selecting appropriate materials, butterfly valves can be tailored to meet the intricate flow control requirements of various industrial processes. Whether it’s enhancing flow efficiency or ensuring compatibility with aggressive media, the diverse disc designs available empower engineers to optimize system performance and reliability.
The Stem’s Role and Design Variations
One-Piece vs. Two-Piece Stems
In butterfly valves, the stem plays a crucial role in controlling the flow of fluids. The design of the stem varies, with one-piece and two-piece stems being the most common options. A one-piece stem is a solid, single unit, offering simplicity and reliability in operation. On the other hand, two-piece stems consist of separate components that are connected to provide enhanced flexibility and easier maintenance. When choosing between the two, consider the specific requirements of your application and the ease of maintenance needed for the valve.
Material Selection for Durability and Compatibility
Selecting the right material for the stem is essential for ensuring durability and compatibility with the intended application. Stainless steel is a popular choice for its corrosion resistance and strength, making it suitable for a wide range of operating conditions. For applications where superior corrosion resistance is required, using materials such as alloy 20 or hastelloy can be beneficial. Additionally, for compatibility with different fluids and temperatures, consider materials like PTFE or other fluoropolymer coatings to minimize the risk of corrosion or material degradation.
By understanding the role of the stem and the design variations available, you can make informed decisions when selecting butterfly valves for your specific requirements.
Sealing Arrangements in Butterfly Valves
Leakage prevention is a critical aspect of butterfly valve design. The sealing arrangement, which includes the seat, interference fit, and seat materials, plays a pivotal role in achieving effective leakage prevention.
Importance of the Seat in Leakage Prevention
The seat in a butterfly valve is crucial for preventing leakage. It provides a seal between the valve body and the disc, ensuring that the flow of the medium is effectively controlled. A properly designed seat minimizes the possibility of leakage, offering reliability and operational safety.
Interference Fit
The interference fit in a butterfly valve ensures that the seat is securely held in place within the valve body. This fit creates a tight seal, preventing any potential leakage through the interface between the seat and the valve body. Proper interference fit design is essential for enhancing the overall sealing performance of the valve.
Seat Materials
The choice of seat materials significantly impacts the effectiveness of the sealing arrangement. Different materials, such as elastomers, metal, or PTFE, offer varying levels of resistance to corrosion, abrasion, and temperature extremes. Selecting the appropriate seat material is critical in ensuring long-term sealing integrity and operational durability for the butterfly valve.
By understanding the importance of the seat in leakage prevention, the significance of interference fit, and the role of seat materials, the design and performance of butterfly valves can be optimized for efficient and reliable operation.
Actuator Types and Their Functions
Actuators are essential components that enable controlled movements or positioning within a machine or system. They can be operated electrically, manually, or by fluids, and are crucial for tasks such as opening valves. Actuators require a control signal and a source of energy to bring about mechanical motion.
Manual Actuators
Manual actuators are operated by hand, typically through a hand wheel or lever. These actuators are often used in applications where precise control over a valve’s positioning is required. Manual actuators offer simplicity and reliability, making them suitable for various settings. Their design allows for easy maintenance and greater precision in valve positioning.
Automatic Actuators
Automatic actuators, on the other hand, are powered by various energy sources such as electricity, hydraulic power, or compressed air. They are capable of automated movement and are widely used in scenarios where continuous or remote valve operation is necessary. Automatic actuators contribute to improved efficiency and reduced manual intervention in valve control systems.
Automatic actuators encompass diverse types, including hydraulic and pneumatic actuators.
- Hydraulic actuators utilize hydraulic power to generate mechanical motion, resulting in linear, rotatory, or oscillatory movements. These actuators are known for their ability to exert substantial force, making them suitable for applications that require high force output. However, they typically involve more complex components and are prone to potential fluid leakage.
- Pneumatic actuators convert compressed air or pressurized gas into mechanical motion. They are favored for their rapid and precise response, making them suitable for swift valve control requirements. Pneumatic actuators offer simplicity and cost-effectiveness in various industrial applications.
Maintenance and Troubleshooting
Maintenance troubleshooting is a crucial aspect of ensuring the proper functioning of butterfly valves. It involves identifying and resolving issues that may arise during the operation of the valve. Common issues such as leakage, wear and tear, and control problems can be addressed effectively through proper troubleshooting techniques.
Common Issues and Solutions
- Leakage: One of the most common issues with butterfly valves is leakage. This can occur due to worn out seals or gaskets. Regular inspection of seals and gaskets is essential to identify any signs of deterioration. Once identified, replacing the seals or gaskets can effectively resolve the leakage issue.
- Wear and Tear: Over time, the components of a butterfly valve can experience wear and tear, leading to operational inefficiencies. Periodic maintenance and lubrication of moving parts can prevent excessive wear and extend the lifespan of the valve.
- Control Problems: In some cases, butterfly valves may face control issues, such as difficulty in opening or closing fully. This can be attributed to issues with the actuator or the valve disc. Calibrating the actuator and ensuring proper alignment of the valve disc can help address control problems effectively.
Tips for Prolonging Valve Life
- Regular Inspection: Conducting routine visual inspections of the valve components can help in early detection of potential issues. This proactive approach can prevent minor problems from escalating into major failures.
- Proper Lubrication: Applying suitable lubricants to the moving parts of the valve can reduce friction and wear, thereby prolonging the valve’s life span.
- Operational Checks: Performing regular operational tests to ensure smooth opening and closing of the valve can help in identifying any emerging issues.
- Training and Documentation: Providing adequate training to personnel involved in the operation and maintenance of butterfly valves can lead to proper handling, thereby minimizing the risk of premature failures.
Maintenance troubleshooting plays a pivotal role in ensuring the longevity and efficient performance of butterfly valves. Implementing proactive maintenance practices and promptly addressing any issues that arise can contribute to the optimal operation of these critical components in various industrial applications.
Conclusion
In conclusion, understanding the key components of butterfly valves is essential for their proper functioning and maintenance. The stem, body, sealing arrangement, bearings, bonnet, actuator, seat, and disc all play crucial roles in the valve’s operation. Knowing the differences between lug and wafer body designs, the variations in disk design, and the significance of stem and seat materials is vital for selecting the right butterfly valve for specific applications. By grasping the functionality of these parts, industries can ensure efficient flow control and longevity of their systems.