Comparing Proportional vs. On/Off Directional Control Valves in Fluid Power Systems
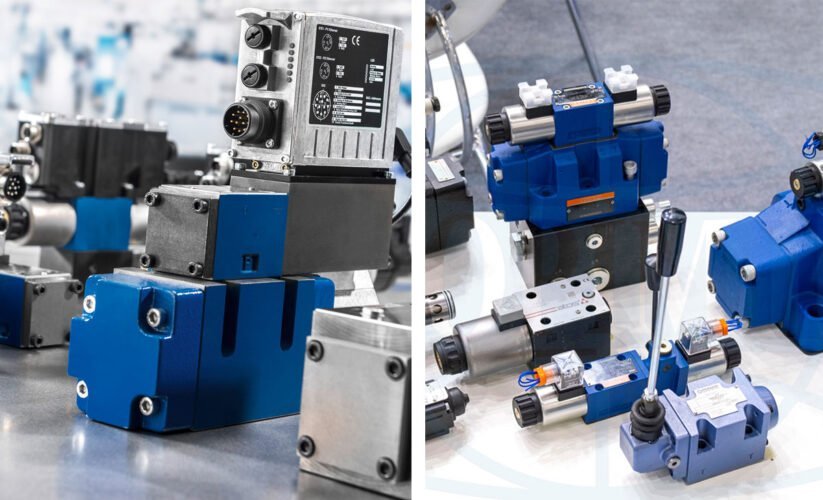
Table of Contents
ToggleExploring On/Off Directional Control Valves in Fluid Power Systems
When considering the control of hydraulic actuators, the choice between using proportional solenoid valves and directional solenoid valves is crucial. Proportional solenoid valves offer precise and accurate fluid flow control at any point between fully open and fully closed, while directional solenoid valves are binary, with only open or closed positions. The differences in functionality and applications between these two types of directional control valves warrant a closer examination to determine the most suitable option for a specific fluid power system.
Proportional Control Valves
- Provide variable flow rates and directions
- Offer precise control over fluid flow and pressure
- Suited for applications requiring fine-tuned adjustments
- Control current to a solenoid, adjusting the valve opening
- Tend to be more expensive than on/off valves
On/Off Directional Control Valves
- Allow fluid to flow or stop flowing completely
- Ideal for applications that do not require variable flow rates
- Operate in a binary manner, either fully open or fully closed
- Control the opening and closing of the valve mechanically or through solenoids
- Generally more cost-effective compared to proportional valves
Understanding Fluid Power Systems
Hydraulic and pneumatic systems are fundamental components of fluid power systems, facilitating the transmission of power through pressurized fluids to perform mechanical work. In hydraulic systems, this power is transmitted through the use of a liquid, while pneumatic systems utilize a gas, typically compressed air. These systems play a pivotal role in various industrial, construction, and off-highway applications, providing the force and control necessary for heavy-duty tasks.
Basics of Hydraulic and Pneumatic Systems
In a hydraulic system, the force is generated by the mechanical action of a pump, which pressurizes the liquid (usually oil) to transmit power to actuators, such as hydraulic cylinders. This pressurized fluid allows for the multiplication of force, enabling the performance of heavy-duty tasks with relative ease. Pneumatic systems operate on a similar principle but use compressed air to transmit power, providing an effective alternative in certain applications.
Importance of Control Valves in Fluid Power Systems
Control valves are crucial components within fluid power systems as they regulate the flow and pressure of the hydraulic fluid or compressed air. These valves enable precise control over the operation of hydraulic and pneumatic actuators, allowing for smooth and efficient functionality. By adjusting the flow rate and direction of the fluid, control valves play a key role in ensuring the proper execution of tasks and the overall performance of fluid power systems.
The integration of control valves in fluid power systems not only enhances operational precision but also contributes to safety and energy efficiency. Properly designed and maintained control valve systems are essential for achieving optimal performance and extending the operational lifespan of hydraulic and pneumatic equipment.
In summary, the understanding of fluid power systems, encompassing both hydraulic and pneumatic applications, is fundamental for grasping the significance of control valves and their role in regulating the transmission of power through pressurized fluids. These systems form the backbone of various industrial operations, offering reliable force multiplication and precise control for a wide range of applications.
What Are Directional Control Valves?
Directional control valves are an essential component in fluid power systems, responsible for regulating the flow of hydraulic or pneumatic fluid to different sections of the system. These valves determine the direction of flow and the start or stop of the fluid flow in response to electrical, mechanical, or pneumatic signals.
Function of Directional Control Valves
The primary function of directional control valves is to direct the flow of fluid within a hydraulic or pneumatic system. These valves can control the direction of movement of a hydraulic actuator, such as a cylinder or hydraulic motor. They also manage the start and stop of fluid flow, making them critical for the efficient operation of fluid power systems.
Common Types and Configurations
Directional control valves come in various types and configurations to suit different system requirements. Some common types include:
Hydraulic Directional Control Valves: These are designed specifically for hydraulic systems and are used to control the flow of hydraulic fluid to various hydraulic actuators.
Pneumatic Directional Control Valves: These valves are used in pneumatic systems to regulate the flow of compressed air to different pneumatic actuators.
Advantages of Using Directional Valves
The use of directional control valves offers several advantages in fluid power systems. These include precise control of fluid flow, enabling smooth and efficient movement of hydraulic or pneumatic actuators. Additionally, directional control valves contribute to the overall safety and reliability of fluid power systems, ensuring proper flow direction and fluid regulation.
By implementing directional control valves, operators can effectively manage the movement and operation of machinery, leading to enhanced productivity and operational efficiency in various industrial and mobile equipment applications.
Exploring Proportional Control Valves
Proportional control valves are a crucial component in fluid power systems, offering precise control over flow and pressure. These valves operate on the principle of changing their output in proportion to a change in input, allowing for continuous adjustment of pressure and flow.
Working Principle of Proportional Valves
Proportional control valves are engineered to provide infinite spool positioning, enabling precise regulation of flow or pressure in hydraulic systems. When the input to a proportional valve changes, the output pressure or flow responds proportionally, accommodating variations in input. This responsiveness ensures efficient and adaptable control of machines and systems.
Variable Flow Control and Precision
These valves are designed for applications where output pressure or flow may vary continuously or in discrete steps. This variability allows systems to adapt in real-time to changing demands or conditions, ultimately enhancing process efficiency.
Benefits of Proportional Valves in System Regulation
Proportional control valves offer diverse applications across a wide range of industrial processes and machinery. Their capability to cater to different industrial requirements with precision makes them indispensable in ensuring optimal performance at all times. Additionally, these valves provide dynamic set point adherence, enabling them to adjust to changing requirements on-the-fly. This middle-range capability makes them suitable for diverse industrial settings, offering versatility and adaptability.
Key Differences Between Proportional and On/Off Directional Valves
Comparison of Operational States
Proportional solenoid valves offer variable control over fluid flow, allowing for precise adjustments at any point between fully open and fully closed. In contrast, directional solenoid valves are binary in nature, with only two states – open or closed, offering limited control over fluid flow rates.
Flow Control Capabilities
Proportional solenoid valves are designed to provide accurate and precise flow control, making them suitable for applications that demand tight regulation of fluid flow rates. On the other hand, directional solenoid valves have more basic flow control capabilities due to their binary nature, allowing fluid to flow in one direction when open and stopping the flow when closed.
Response Times and Performance
Proportional solenoid valves typically exhibit faster response times and enhanced performance compared to on/off directional valves. The ability to make real-time adjustments and modulate fluid flow enables proportional valves to offer superior responsiveness and efficiency in fluid power systems. In contrast, directional solenoid valves may have slower response times and are limited in their ability to fine-tune flow rates.
When evaluating the choice between proportional and on/off directional valves, it is essential to consider the specific requirements of the application, the level of precision needed, and the trade-offs between cost and performance.
Applications of Proportional and Directional Valves
Directional control valves and proportional valves play crucial roles in fluid power systems across diverse applications. Understanding when to use directional control valves, identifying ideal situations for proportional valves, and examining sector-specific examples sheds light on the practical implications of these components.
When to Use Directional Control Valves
Directional control valves are essential for controlling the direction of fluid flow in systems involving cylinders and motors. In applications where binary control of fluid direction is sufficient, such as simple on/off operations, directional control valves are the preferred choice. Industries that commonly utilize these valves include agricultural machinery, construction equipment, and material handling systems.
Ideal Situations for Proportional Valves
Proportional valves excel in scenarios requiring precise control over fluid flow rates and direction, offering variable and fine-tuned adjustments. Situations where smooth and continuous variations in flow and pressure are necessary, such as in sophisticated automation, injection molding, and heavy machinery with variable speed requirements, are ideal for proportional valves. Their ability to modulate flow within a wide spectrum makes them indispensable in applications demanding precision and efficiency.
Sector-Specific Examples
In the automotive industry, proportional valves play a pivotal role in automatic transmissions, where seamless shifting between gears is crucial for optimal performance. Additionally, in aerospace and defense applications, proportional valves are utilized for precise control of hydraulic and pneumatic systems, ensuring smooth and accurate operation of critical functions. Furthermore, in the field of industrial automation, proportional valves contribute to the precise control of robotic movements and process automation, enabling enhanced productivity and quality.
Understanding the distinctive roles of directional control valves and proportional valves in various sectors underscores their significance in enabling efficient and precise fluid power operations. Their applications span across industries, addressing specific operational requirements with tailored functionality and performance.
Cost and Maintenance Considerations
Initial Investment and Operating Costs
When comparing proportional and on/off directional control valves in fluid power systems, one of the key considerations is the initial investment and operating costs. Proportional control valves typically have a higher initial cost compared to on/off control valves due to their advanced technology and precision control capabilities. However, in terms of operating costs, proportional valves can offer efficiency gains and energy savings, potentially offsetting the initial investment over time. On the other hand, on/off control valves may have lower initial costs but could result in higher operating costs due to energy inefficiencies.
Maintenance Needs and Lifespan
Maintenance needs and lifespan are crucial factors in the decision between proportional and on/off directional control valves. Proportional control valves often require more frequent maintenance and servicing due to their complex internal components and higher precision requirements. However, when properly maintained, proportional valves can have a longer lifespan compared to on/off valves. On/off valves, while generally requiring less frequent maintenance, may have a shorter overall lifespan, leading to potential replacement costs over time.
Ease of Integration with Control Systems
The ease of integration with control systems is another aspect to consider when evaluating the cost and maintenance of proportional versus on/off directional control valves. Proportional control valves can offer seamless integration with modern control systems, allowing for precise and dynamic control over fluid power systems. This integration capability can contribute to overall cost savings by optimizing system performance and reducing energy consumption. On the other hand, on/off control valves may have limitations in terms of integration with advanced control systems, potentially leading to higher operational costs and inefficiencies.
In summary, while the initial investment and operating costs, maintenance needs and lifespan, and ease of integration with control systems may favor different types of directional control valves in fluid power systems, a comprehensive cost-benefit analysis is essential to determine the most suitable option for specific application requirements.
Making the Right Choice for Your System
Analyzing System Requirements
When considering proportional vs. on/off directional control valves for your fluid power system, the first step is to thoroughly analyze your system’s requirements. This involves understanding the specific demands of your machinery, including flow rates, pressure levels, and the desired speed and precision of control. By conducting a comprehensive assessment of your system’s needs, you can determine the type of valve that will best meet these requirements.
Factors Influencing Valve Selection
Several factors play a critical role in influencing the selection of the most suitable control valve for your fluid power system. These include the nature of the application, response time, accuracy, sensitivity to load variations, energy efficiency, and the overall cost implications. Each of these factors must be carefully evaluated to ensure that the chosen valve aligns with the operational demands and budgetary considerations of the system.
Consultation with Experts and Manufacturers
Engaging in discussions with industry experts and valve manufacturers can provide invaluable insights into the decision-making process. These specialists can offer expert recommendations based on their in-depth knowledge of control valve technologies and their practical applications. Additionally, seeking guidance from manufacturers allows for a detailed exploration of available options, technical specifications, and customized solutions that could optimize the performance of your fluid power system.
Frequently Asked Questions About Comparing Proportional vs. On/Off Directional Control Valves in Fluid Power Systems
What is the difference between a proportional valve and a directional control valve?
A proportional valve opens by an amount that is proportional to the control signal, while a directional control valve sends the fluid into a desired outlet according to the control input.
What is the difference in operation between a proportional solenoid and an on/off DC solenoid?
A direct-operated 2-way standard proportional solenoid valve operates very similarly to a direct-operated solenoid valve, but the former operates through a range of valve positioning, while the latter only provides two switching states (i.e., on/off).
What are the advantages of using proportional valves in fluid power systems?
Proportional valves can help reduce cycle times by quickly achieving stable pressure, have a fast and precise response leading to improved efficiency, and provide repeatable control and pressure output for expected responses every time.
What are the two types of proportional valves?
Proportional valves can be divided into two structural forms: direct control and pilot control. Direct control is used in small-flow and low-power systems, while pilot control is used in large-flow and high-power hydraulic systems to form an electro-hydraulic proportional valve.
Conclusion
In conclusion, the choice between proportional and directional solenoid valves for fluid power systems depends on the specific needs of the application. Proportional solenoid valves offer precise and accurate control over fluid flow rates, making them suitable for applications requiring tight control. They are adaptable to various control systems and provide flexibility in controlling the flow of fluid at any point between fully open and fully closed.
On the other hand, directional solenoid valves are binary valves with two states – open or closed, making them suitable for simpler applications. They are available in different configurations and are relatively easier to install and operate. Understanding the requirements of the fluid power system and the level of control needed will help in making an informed decision between proportional and directional solenoid valves.