Types of Hydraulic Pressure Reducing Valves: Evaluating Pros and Cons
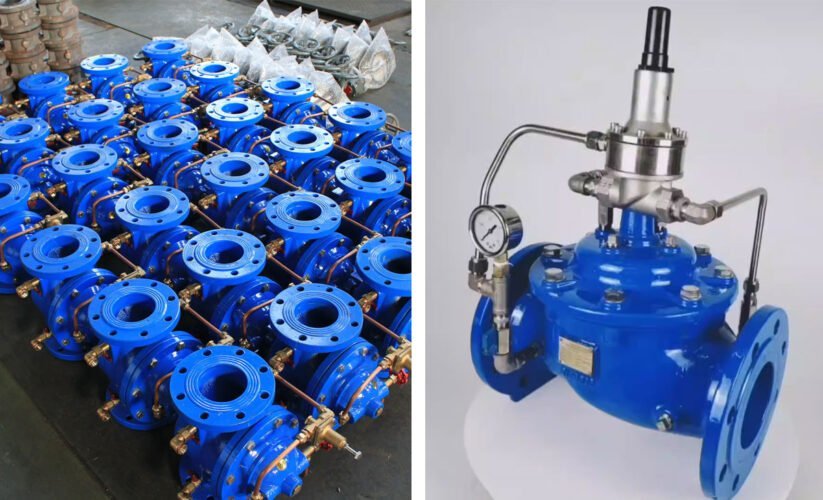
Table of Contents
ToggleComparing Different Types of Hydraulic Pressure Reducing Valves: Evaluating Pros and Cons
Hydraulic pressure reducing valves play a crucial role in controlling the flow of hydraulic fluid within a hydraulic system. In this article, we will delve into the comparison of different types of hydraulic pressure reducing valves, analyzing their respective pros and cons. Understanding the distinctions between these valves will provide valuable insights for engineers, maintenance professionals, and anyone involved in hydraulic system design and maintenance. Ultimately, this knowledge will aid in making informed decisions when selecting the most suitable hydraulic pressure reducing valve for specific applications.
Hydraulic Pressure Reducing Valves Explained
- A hydraulic pressure reducing valve is a crucial component in hydraulic systems, designed to regulate and maintain a specific pressure level within the system.
- The valve operates by diverting or restricting the flow of hydraulic fluid to ensure that the downstream pressure remains constant, irrespective of variations in the upstream pressure.
- It is commonly used in various applications such as industrial machinery, construction equipment, and hydraulic power units.
- The hydraulic pressure reducing valve consists of a main valve element, a spring mechanism, an adjusting mechanism, and a control or sensing element.
- The main valve element controls the flow of hydraulic fluid, while the spring mechanism and adjusting mechanism work together to set and maintain the desired pressure level.
- The control or sensing element continuously monitors the downstream pressure and adjusts the valve accordingly to ensure it stays within the specified range.
- Proper installation and regular maintenance of the hydraulic pressure reducing valve are essential to ensure its optimal performance and longevity.
- Choosing the right type and size of the valve is crucial to match the specific requirements and operating conditions of the hydraulic system.
The Role of Pressure Reducing Valves in Hydraulic Systems
Hydraulic pressure reducing valves play a crucial role in managing the pressure within a hydraulic system. They are essential for ensuring that the system operates efficiently and safely. These valves are designed to regulate the pressure of the hydraulic fluid, allowing for precise control and preventing potential damage to the system and its components. By reducing the high pressure from the input side to a lower, stable pressure on the output side, these valves enable the hydraulic system to function optimally without the risk of overload or malfunctions.
Key Features of Hydraulic Pressure Reducing Valves
Hydraulic pressure reducing valves boast a range of features that make them indispensable in hydraulic systems. These include precise pressure control, which allows for the adjustment of pressure levels as needed for different functions within the system. Additionally, these valves often feature a compact and robust design, making them suitable for a variety of hydraulic applications. Furthermore, many modern pressure reducing valves are equipped with advanced technology that enables them to maintain consistent pressure levels even in dynamic operating conditions, ensuring smooth and efficient system performance.
Direct-Acting Hydraulic Pressure Reducing Valves
Direct-Acting Pressure Reducing Valves function by utilizing a spring-loaded mechanism to control the downstream pressure. When the downstream pressure surpasses the set limit, the valve’s diaphragm pushes against the spring, thus reducing the flow of the fluid or gas to maintain the predetermined pressure. This method allows for a straightforward and efficient means of pressure reduction without the need for external power sources or additional control components.
How Direct-Acting Valves Work
Direct-Acting Valves operate by directly reducing the pressure of incoming fluid or gas to a predetermined and consistent level, ensuring that downstream systems are safeguarded against excessively high pressures. This is achieved through a simple and reliable mechanism, where the internal components work in unison to maintain the desired pressure, enhancing operational safety and efficacy.
Pros of Direct-Acting Valves
- Simplicity in design facilitates easy installation and maintenance
- Self-regulating mechanism reduces the reliance on external power sources or control systems
- Ideal for applications requiring a compact and cost-effective pressure control solution
- Well-suited for environments with limited access to power sources or where reliability is crucial
Cons of Direct-Acting Valves
- Limited capacity compared to pilot-operated valves, making them unsuitable for high-flow applications
- Sensitivity to pressure variations in the upstream system, potentially impacting precise pressure control
- May exhibit reduced accuracy in maintaining constant pressure levels compared to pilot-operated alternatives
Pilot-Operated Hydraulic Pressure Reducing Valves
Pilot-operated pressure reducing valves function by using a main valve controlled by an adjustable pilot valve operating in conjunction with an orifice or needle valve. The pilot valve senses the downstream (outlet) pressure and reacts immediately to changes in demand.
Functionality of Pilot-Operated Valves
The pilot diaphragm automatically senses changes in the flow of the system and continuously controls the main valve to throttle, open, or close to maintain the desired, preset reduced outlet pressure. This functionality allows the valves to regulate the flow and maintain a constant reduced downstream pressure despite fluctuations in demand and upstream pressure.
Advantages of Pilot-Operated Valves
One advantage of pilot-operated valves is their ability to provide precise control and maintain a constant outlet pressure, even when there are significant variations in demand and upstream pressure. They are also known for their high flow capacity, making them suitable for applications that require a large volume of fluid to be regulated.
Disadvantages of Pilot-Operated Valves
On the downside, pilot-operated valves can be more complex and expensive compared to direct-acting pressure reducing valves. Additionally, they may require more frequent maintenance due to the intricate pilot and control systems.
Pilot-operated pressure reducing valves are an excellent choice for applications that require precise control and high flow capacity, but the complexity and maintenance requirements should be considered when evaluating their suitability for a specific use case.
Mechanism of Proportional Valves
Proportional pressure reducing valves are designed to modulate pressure in hydraulic systems by adjusting the flow in proportion to a control signal. This is achieved through a combination of electronic and hydraulic components. The valve receives electrical input, which controls the opening and closing of the internal hydraulic passages. By regulating the flow in response to the input signal, these valves can maintain a steady pressure despite fluctuating demand.
Benefits of Proportional Pressure Reducing Valves
Proportional pressure reducing valves offer precise control over pressure and flow rates, making them well-suited for applications requiring accurate and stable pressure regulation. These valves also provide flexibility, as the control signal can be adjusted to meet changing system requirements. Additionally, proportional valves can improve energy efficiency by reducing pressure losses and minimizing heat generation in the system.
Limitations of Proportional Pressure Reducing Valves
Despite their advantages, proportional pressure reducing valves may be more complex to install and maintain compared to simpler relief valves. They also tend to be more sensitive to contamination and require regular cleaning and maintenance to ensure proper functioning. Another limitation is the potential for increased costs due to the need for additional electronic control systems and sensors.
Comparing Valve Performance
Hydraulic pressure reducing valves play a critical role in ensuring the efficient and reliable operation of hydraulic systems. When comparing the performance of different types of hydraulic pressure reducing valves, several key factors come into play. These include response time and stability, pressure adjustment range and accuracy, as well as flow rate capabilities.
Response Time and Stability
The response time of a hydraulic pressure reducing valve is crucial for maintaining stability within a hydraulic system. A rapid response time ensures that the valve can react quickly to changes in pressure, helping to maintain stability and prevent pressure fluctuations that could impact system performance. When comparing different types of valves, it’s essential to consider the response time and stability characteristics to ensure optimal system performance.
Pressure Adjustment Range and Accuracy
The pressure adjustment range and accuracy of a hydraulic pressure reducing valve determine its ability to maintain precise pressure control within a hydraulic system. A broader adjustment range allows for greater flexibility in accommodating varying pressure requirements, while high accuracy ensures that the set pressure is consistently maintained. When evaluating different valves, a thorough assessment of their pressure adjustment range and accuracy is imperative to select the most suitable option for specific application requirements.
Flow Rate Capabilities of Hydraulic Pressure Reducing Valves
Flow rate capabilities of hydraulic pressure reducing valves dictate the maximum flow capacity they can handle while maintaining efficient pressure regulation. A valve with higher flow rate capabilities can accommodate larger volumes of fluid without compromising pressure control, making it ideal for applications with high flow demands. When comparing different valves, it’s essential to consider their flow rate capabilities to ensure compatibility with the required flow conditions.
In summary, the performance of hydraulic pressure reducing valves can be effectively compared by evaluating their response time and stability, pressure adjustment range and accuracy, as well as flow rate capabilities. Understanding these key factors is essential for selecting the most suitable valve to optimize the performance of hydraulic systems.
Application Suitability of Hydraulic Pressure Reducing Valves
Industrial Applications
Hydraulic pressure reducing valves find extensive use in industrial applications, particularly in heavy machinery and manufacturing processes that require precise control of hydraulic pressure. In manufacturing, these valves are crucial for regulating pressure in hydraulic systems powering heavy equipment such as presses, shears, and molding machines. Their ability to maintain consistent pressure levels enhances operational efficiency and safety, making them indispensable in industrial settings.
Mobile Hydraulic Systems
In mobile hydraulic systems, such as construction equipment and agricultural machinery, hydraulic pressure reducing valves play a vital role in ensuring smooth and precise operation. These valves effectively manage pressure levels in hydraulic systems of vehicles and equipment, contributing to their overall performance and safety. Whether it’s controlling the speed of a crane or assisting in the precise movement of agricultural machinery, the suitability of these valves in mobile applications underscores their importance in diverse industries.
Specialty Applications
In addition to conventional industrial and mobile applications, hydraulic pressure reducing valves are also utilized in specialty applications, including aerospace, marine, and medical equipment. In aerospace and marine industries, these valves are crucial for maintaining precise hydraulic pressure in critical systems, ensuring optimal performance and safety. Moreover, their use in medical equipment highlights the precision and reliability these valves offer, making them suitable for a wide range of specialized applications.
By catering to diverse industrial, mobile, and specialty applications, hydraulic pressure reducing valves demonstrate their versatility and reliability in regulating hydraulic pressure across various sectors, reaffirming their significance in hydraulic systems worldwide.
Maintenance and Reliability of Hydraulic Pressure Reducing Valves
When it comes to hydraulic pressure reducing valves, maintenance and reliability play a crucial role in ensuring optimal performance and longevity. By understanding the maintenance requirements for different valve types and comparing their durability and longevity, you can make informed decisions for your hydraulic systems.
Maintenance Requirements for Different Valve Types
Different types of hydraulic pressure reducing valves may have varying maintenance requirements. For example, pilot-operated valves may require regular checks and adjustments to ensure consistent pressure regulation, while direct-acting valves may necessitate periodic inspections for wear and tear on internal components.
Durability and Longevity Comparisons
When evaluating the reliability of hydraulic pressure reducing valves, it’s essential to consider their durability and longevity. Pilot-operated valves, known for their precision control, often exhibit extended durability due to their design complexity, while direct-acting valves, with their simplicity, may offer reliable performance over time with proper maintenance.
In the realm of hydraulic systems, the interplay between maintenance and reliability is fundamental to minimizing downtime and maximizing asset performance. By strategically addressing maintenance requirements and assessing longevity comparisons, you can enhance the reliability of hydraulic pressure reducing valves, contributing to the overall efficiency of your hydraulic systems.
Cost Considerations for Hydraulic Pressure Reducing Valves
Initial Investment and Installation Costs
When considering hydraulic pressure reducing valves, it’s important to take into account the initial investment and installation costs. The price of the valve itself can vary greatly depending on factors such as the type, size, and brand. Additionally, installation costs can fluctuate based on the complexity of the system and the need for professional assistance. It’s crucial to weigh the initial investment against the overall benefits and durability of the chosen valve.
Long-Term Operational Costs
In addition to the initial expenses, long-term operational costs should also be factored in. Different types of hydraulic pressure reducing valves come with varying levels of maintenance requirements, energy consumption, and durability. Analyzing the long-term operational costs will provide insight into the overall cost of ownership. This consideration is essential for making an informed decision that aligns with budget constraints and operational efficiency goals.
Conclusion for Hydraulic Pressure Reducing Valves
In conclusion, each type of hydraulic pressure reducing valve comes with its own set of advantages and disadvantages. The pilot-operated relief valve provides precise control but has complex installation and maintenance requirements. On the other hand, direct-acting relief valves are simple and cost-effective, but they may not offer the same level of accuracy. The balanced piston relief valve strikes a balance between the two, offering moderate precision and ease of use. When choosing a hydraulic pressure reducing valve, it’s essential to weigh these factors against the specific requirements of the hydraulic system to determine the most suitable option for optimal performance and efficiency.