Different Types of Control Valves in Industrial Processes
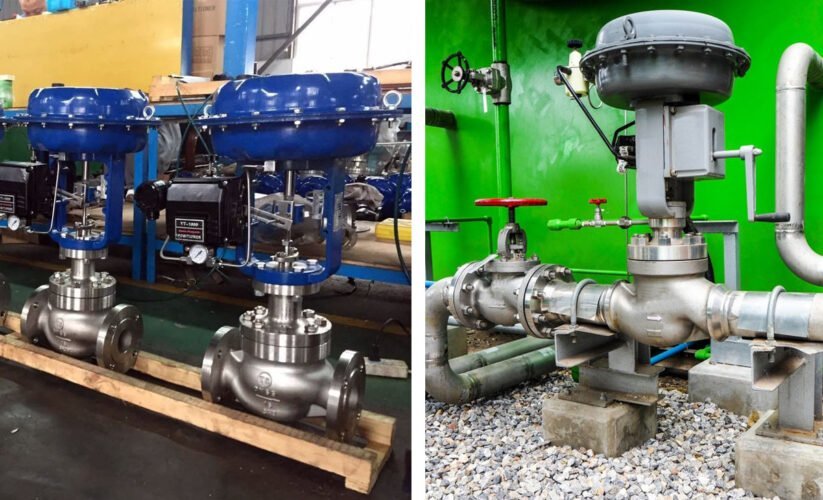
Table of Contents
ToggleUnderstanding the Basic Types of Control Valves in Industrial Processes
Control valves are essential components in various industrial processes, providing the means to regulate the flow, pressure, temperature, and level of fluids. There are several types of control valves, including globe valves, butterfly valves, ball valves, and diaphragm valves.
Globe valves are commonly used for precise control of flow, while butterfly valves are suitable for quick shutoff and flow regulation. Ball valves offer fast operation and tight sealing, making them suitable for on/off applications. Diaphragm valves are ideal for controlling highly corrosive or abrasive fluids. Each type of control valve has distinct characteristics that make it suitable for specific industrial applications, ensuring efficient and reliable process control.
Summary: Types of Control Valves
- Globe Valves: These valves control flow by moving a round plug up and down against the flow stream. They are suitable for applications requiring fine flow control.
- Butterfly Valves: These valves use a circular disc to control flow. They are often used in large pipelines and are well-suited for quick shutoff.
- Ball Valves: These valves use a pivoting ball to control flow. They provide tight shutoff and are commonly used in applications where tight sealing is critical.
- Diaphragm Valves: These valves use a flexible diaphragm to control flow. They are suitable for controlling highly corrosive or abrasive fluids.
- Pinch Valves: These valves control flow by pinching a flexible tube. They are ideal for applications with slurries or liquids containing large amounts of suspended solids.
- Plug Valves: These valves use a cylindrical or conical plug to control flow. They are commonly used in applications requiring minimal pressure drop and tight sealing.
- Needle Valves: These valves have a long, tapered, needle-like point at the end of the valve stem. They are suitable for precise flow control in low flow rate applications.
- Pressure Relief Valves: These valves automatically release excess pressure from a system. They are essential for protecting equipment from overpressure situations.
Understanding Control Valves in Industrial Processes
Control valves play a crucial role in regulating the flow, pressure, temperature, and liquid levels in industrial processes. These valves are an essential part of the control loop and are designed to modulate the flow of fluid or gas, ensuring that the process variables remain within the desired range.
What is a Control Valve?
A control valve is a mechanical device that regulates the flow of fluids or gases by varying the size of the flow passage as directed by a signal from a controller. This allows the process to operate at a specific set point, maintaining the desired conditions within a system.
The Role of Control Valves
Control valves are integral to the optimization and efficiency of industrial processes. They enable precise control over the rate of flow and the amount of pressure exerted on the fluid or gas, thereby ensuring that the system operates effectively and safely. By manipulating the flow, they contribute to maintaining the stability and reliability of the entire operation.
How Control Valves Affect Flow and Pressure
Control valves influence the flow and pressure within a system by modulating the size of the flow passage. By adjusting the valve opening, they can increase or decrease the flow of the fluid or gas, and subsequently, the pressure within the system. This dynamic regulation allows for the precise adjustment of process variables, contributing to the smooth operation of industrial processes.
Types of Control Valves Based on Functionality
Choosing the right control valve can be a challenging task, especially for those new to the field. It requires a basic understanding of different regulation technologies and the types of control valves available. Let’s delve into the functionality of two main types of control valves: Linear Motion Valves and Rotary Motion Valves.
Linear Motion Valves
Linear motion valves, such as globe and diaphragm valves, are designed for applications where precise control of flow, pressure, and temperature is required. These control valves operate by linearly positioning the closure element to regulate the flow of fluids. Globe valves are commonly used in applications where throttling or frequent operation is needed, while diaphragm valves are suitable for controlling corrosive or viscous fluids due to their ability to create a tight seal.
Rotary Motion Valves
Rotary motion valves, including ball and butterfly valves, control the flow of fluids by using a rotating closure element. Ball valves, for example, offer straight-through flow and are well-suited for isolation applications. Their quick-acting and low-pressure drop characteristics make them suitable for a wide range of industrial applications. Similarly, butterfly valves are known for their compact design and compatibility with adaptive technologies, making them ideal for applications with demanding requirements, such as those involving particle-heavy fluids in refineries. These features make rotary motion valves a versatile option for various industrial control needs.
Detailed Look at Linear Motion Valves
Linear motion valves are a crucial component in fluid control systems, providing precise regulation of fluid flow. Understanding the various types of linear motion valves can help in selecting the most suitable option for specific applications. Here, we delve into the details of globe valves, gate valves, diaphragm valves, and pinch valves.
Globe Valves
Globe valves are characterized by a spherical body shape and a movable plug that regulates flow. The linear motion of the plug aligns with the flow path, enabling precise adjustment of fluid flow. These valves are commonly used in applications requiring frequent throttling and regulation of flow.
Gate Valves
Gate valves control flow through the raising or lowering of an internal gate. This linear motion mechanism provides a full flow or complete shut-off, making gate valves suitable for applications where a tight seal is essential.
Diaphragm Valves
Diaphragm valves utilize a flexible diaphragm to regulate flow. The linear motion of the diaphragm allows for accurate control of fluid passage, making diaphragm valves suitable for handling corrosive or abrasive fluids.
Pinch Valves
Pinch valves control flow by pinching a flexible tube to obstruct or permit fluid passage. This linear motion mechanism offers excellent sealing capabilities, making pinch valves ideal for applications involving slurries and solids.
Understanding the distinctive features of these linear motion valves is crucial in selecting the most appropriate option for specific fluid control requirements. Each type offers unique advantages, catering to diverse industry needs.
Exploring Rotary Motion Valves
Ball Valves
Ball valves are quarter-turn valves that use a pivoting ball to control the flow of liquids or gases. One main advantage of ball valves is their fast-acting nature, which allows for quick shut-off. Additionally, these valves provide a tight seal and are less prone to leakage. Their simple design and minimal maintenance requirements make them suitable for a wide range of applications, including high-pressure and high-temperature environments.
Butterfly Valves
Butterfly valves are lightweight and offer a quick quarter-turn operation, making them ideal for applications that require frequent adjustments. Their streamlined design reduces pressure drop and provides efficient flow control. These valves are commonly used in large-diameter applications where space and weight are critical factors. Additionally, butterfly valves are cost-effective and easy to install, making them a popular choice across various industries.
Plug Valves
Plug valves, also known as cock valves, use a cylindrical or conically tapered plug to control the flow of fluids. These valves are suitable for on/off and throttling applications, offering low torque operation and tight sealing capabilities. Their simple construction and ease of maintenance make them a preferred choice for industries such as oil and gas, petrochemical, and wastewater treatment. Plug valves provide reliable performance in demanding conditions and contribute to efficient flow management.
Specialty Control Valves for Specific Applications
In the realm of industrial processes, specialized applications often demand precise fluid and gas control. Control valves tailored for specific functions and conditions play a critical role in ensuring optimal performance and safety. Let’s explore three types of specialty control valves designed for specific applications.
Needle Valves for Precise Control
Needle valves are designed for applications that require precise regulation of flow rates. These valves feature a slender, tapered needle-like plunger that fits into a matching seat. By adjusting the position of the plunger, operators can fine-tune the flow of fluids or gases with exceptional accuracy. This level of control makes needle valves well-suited for tasks such as metering, calibration, and instrumentation in various industries, including oil and gas, chemical processing, and laboratory settings.
Check Valves and Non-Return Functions
Check valves, also known as non-return valves, serve a crucial function in preventing reverse flow of fluids or gases. These valves allow for unidirectional flow while automatically closing to prevent backflow. This feature is instrumental in maintaining system integrity and preventing damage or contamination. Check valves find application in diverse sectors, including water and wastewater systems, HVAC, and hydraulic systems, where ensuring uninterrupted flow in one direction is vital.
Pressure Relief Valves for Safety
In high-pressure systems, pressure relief valves provide essential protection against overpressurization. These valves are designed to automatically relieve excess pressure by opening and diverting the fluid or gas to a designated discharge location. By doing so, pressure relief valves help safeguard equipment, pipelines, and personnel from potential hazards associated with overpressure events. Their critical role in maintaining system safety makes them indispensable in industries such as petrochemical, pharmaceutical manufacturing, and power generation.
In summary, specialty control valves play a pivotal role in addressing the unique requirements of specific applications. Whether facilitating precise flow control, preventing backflow, or ensuring system safety, these valves contribute to the efficiency and reliability of industrial operations across diverse sectors.
Comparing Valve Materials and Construction
Valve materials and construction play a critical role in determining a valve’s suitability for specific applications. Different materials offer unique properties that cater to diverse operational needs. Here, we explore the significance of metal valves for high-strength applications, plastic valves for corrosion resistance, and hybrid valves for specialized environments.
Metal Valves for High-Strength Applications
Metal valves, crafted from materials like stainless steel, brass, or bronze, offer exceptional durability and strength, making them ideal for high-pressure and high-temperature environments. Their robust construction enables them to withstand harsh conditions without compromising performance or structural integrity. Industries such as oil and gas, chemical processing, and power generation benefit from the reliability and resilience of metal valves, ensuring safe and efficient operations under extreme operational demands.
Plastic Valves for Corrosion Resistance
Plastic valves, commonly constructed from PVC, CPVC, or PTFE, provide outstanding resistance to corrosive substances, acids, and alkalis. These valves are integral in applications where the presence of corrosive media necessitates reliable and long-term performance. Industries such as water treatment, chemical handling, and acid transfer systems leverage the non-reactive nature of plastic valves to maintain operational efficiency while mitigating the risk of material degradation and environmental contamination.
Hybrid Valves for Specialized Environments
Hybrid valves amalgamate the advantages of metal and plastic components to offer tailored solutions for specialized operational environments. By combining metal’s strength with plastic’s corrosion resistance, these valves cater to diverse applications with unique operational requirements. Industries such as pharmaceuticals, food processing, and semiconductor manufacturing rely on hybrid valves to ensure the optimal balance of mechanical robustness and chemical inertness, meeting stringent regulatory standards and operational demands.
The selection of valve materials and construction is pivotal in achieving optimal performance, longevity, and safety across varied industrial applications. Whether it’s the uncompromising durability of metal valves, the corrosion resistance of plastic valves, or the versatility of hybrid valves, each construction type serves as a fundamental component in maintaining operational integrity and efficiency.
Actuators and the Automation of Control Valves
Actuators play a critical role in the automation of control valves, enabling precise control over fluid flow and pressure. These devices convert energy into mechanical motion to open or close the valve. Here’s a breakdown of the different types of actuators commonly used in control valve automation:
Electric Actuators for Precise Operation
Electric actuators are known for their high level of precision and accuracy in controlling valve position. They are ideal for applications that require fine-tuned adjustments and constant monitoring. By utilizing electrical energy, these actuators deliver consistent and repeatable valve positioning, making them suitable for processes that demand strict control over flow rates and pressures. With the ability to integrate with digital control systems, electric actuators offer advanced control capabilities, allowing operators to optimize process efficiency and maintain operational safety.
Pneumatic Actuators for Reliable Performance
Pneumatic actuators are widely favored for their reliability and cost-effectiveness in automating control valves. These actuators utilize compressed air to generate the force needed to actuate the valve. They are well-suited for applications that require swift and responsive valve operation, making them a popular choice in industries where quick valve response is crucial. Pneumatic actuators are known for their simplicity, ruggedness, and suitability for hazardous environments, providing a dependable solution for a wide range of control valve automation needs.
Hydraulic Actuators for High Force Applications
Hydraulic actuators are designed to deliver high thrust and force, making them well-suited for applications involving large valves or systems that demand significant operating forces. By utilizing pressurized hydraulic fluid, these actuators offer precise and robust control over valve positioning, allowing for efficient management of heavy-duty processes. Their ability to generate substantial force makes hydraulic actuators an ideal choice for applications in industries such as oil and gas, power generation, and heavy manufacturing, where large-scale valve automation is essential.
Selection Criteria for Control Valves
Before selecting a control valve, engineers must consider several key factors to ensure optimal performance and efficiency in process control systems.
Flow Rate Requirements
The flow rate requirements of a control valve are crucial in determining its suitability for a specific application. Understanding the expected flow rates under varying process conditions is essential for selecting a valve with the appropriate flow capacity. Engineers must assess the minimum and maximum flow rates to choose a valve that can effectively regulate the flow within the desired operating range.
Pressure Ratings and Temperature Tolerance
Control valves operate within systems that experience fluctuating pressures and temperatures. It is imperative to select valves that can withstand the anticipated pressure differentials and temperature variations without compromising performance or integrity. Evaluating the pressure ratings and temperature tolerance of control valves ensures the reliability and longevity of the selected valves in challenging operational environments.
Compatibility with Fluids
The compatibility of control valves with the fluids present in the process system is a critical consideration. Different fluids exhibit unique properties that can impact the materials and design requirements of control valves. Engineers must carefully analyze the chemical composition, viscosity, and erosive characteristics of the fluids to select valves that are corrosion-resistant, erosion-resistant, and capable of effectively controlling the specific fluid media.
By thoroughly evaluating flow rate requirements, pressure ratings, temperature tolerance, and compatibility with fluids, engineers can make informed decisions when selecting control valves to optimize process performance and achieve precise control in industrial operations.
Common Challenges and Maintenance Tips for Control Valves
Dealing with Wear and Tear
Control valves are subject to wear and tear over time due to their constant operation and exposure to various elements. The moving parts such as the valve stem, plug, and seat can experience wearing, leading to reduced effectiveness and potential valve failure. To address this, regular inspection and lubrication of the moving components are essential to prevent excessive wear. Additionally, replacing worn-out parts in a timely manner is crucial to maintain the optimal performance of control valves and extend their lifespan.
Preventing Leakage and Blockages
One of the common challenges associated with control valves is the occurrence of leakage and blockages. This can result from factors such as corrosion, improper installation, or the accumulation of debris within the valve. To prevent leakage, it is important to conduct periodic checks for any signs of corrosion and address them promptly. Installing proper sealing mechanisms and ensuring correct valve positioning can also help mitigate the risk of leakage. Furthermore, implementing a filtration system to remove debris from the process fluid can aid in preventing blockages within the valve.
Regular Maintenance of Control Valves for Optimal Performance
Maintaining control valves through regular upkeep is essential for ensuring their optimal performance. This includes inspecting the valves for any signs of damage, leaks, or abnormal operation. Scheduled cleaning and calibration of the valves can help maintain their accuracy and efficiency. Additionally, monitoring the control valve’s performance parameters, such as response time and flow control, can aid in identifying any deviations from the desired operation, allowing for timely adjustments and preventive measures.
By addressing wear and tear, preventing leakage and blockages, and conducting regular maintenance, the longevity and effectiveness of control valves can be greatly enhanced, ensuring smooth and reliable operation within various industrial processes.
Conclusion for Types of Control Valves
Understanding the different types of control valves is crucial for optimizing the performance and efficiency of various industrial processes. Whether it’s globe valves, butterfly valves, ball valves, or diaphragm valves, each type has its unique features and applications. By selecting the right control valve for a specific process, businesses can achieve precise control over flow, pressure, and temperature, leading to enhanced productivity and cost savings. With this knowledge, engineers and operators can make informed decisions when it comes to selecting and maintaining control valves for their systems.