Flow Control Valves: Types, Functions, and Applications
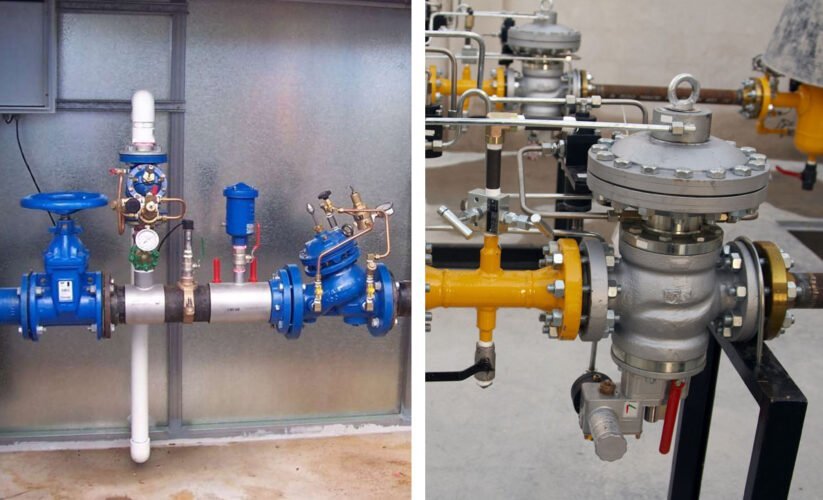
Table of Contents
ToggleCommon Types of Flow Control Valves and Their Operating Principles
The flow control valve is a crucial component in a wide range of industrial and mechanical systems. It allows for precise regulation of the flow rate of liquids or gases, enabling optimal performance and efficiency. Understanding the functionality and benefits of flow control valves is essential for engineers, technicians, and anyone involved in fluid power systems. In this blog post, we will delve into the fundamentals of flow control valves, their applications, and the factors to consider when selecting the right valve for specific requirements.
What is a Flow Control Valve?
Flow control valves are essential components in fluid power systems, playing a crucial role in regulating the flow of fluids within a system. These valves are designed to control the speed or rate of fluid flow, ensuring optimal performance and efficient operation of various types of machinery and equipment.
Definition and Function of Flow Control Valves
A flow control valve is a mechanical device that is used to adjust the flow rate of a fluid within a system. It achieves this by manipulating the size of the flow passage, thereby controlling the amount of fluid that can pass through at any given time. By regulating the flow, these valves help maintain proper pressure levels and ensure that the system operates within desired parameters.
6 Types of Flow Control Valves
- Ball Valves: Ball valves use a spherical disc to control flow. When the valve is open, the sphere allows for straight-through flow; when closed, the sphere is rotated to block flow.
- Butterfly Valves: Butterfly valves use a rotating disc to regulate flow. When the disc is turned parallel to the flow, it allows for unrestricted flow; when turned perpendicular, it restricts flow.
- Gate Valves: Gate valves use a raised or lowered gate to control flow. When fully open, the gate allows for unobstructed flow; when closed, it forms a seal to stop flow.
- Globe Valves: Globe valves use a movable plug to adjust flow. When the plug is lifted, it allows flow; when lowered, it restricts flow by closing off the passage.
- Diaphragm Valves: Diaphragm valves use a flexible diaphragm to regulate flow. When the diaphragm is raised, it allows flow; when lowered, it closes off the passage to stop flow.
- Piston Valves: Piston valves use a piston within a cylinder to control flow. When the piston is in an open position, flow is allowed; when the piston is moved to close the passage, flow is stopped.
In summary, flow control valves are integral to the functionality of fluid power systems, and understanding their various types and functions is essential for optimizing system performance and efficiency.
Importance of Flow Control Valves
Efficiency in Fluid Flow Management
Flow control valves play a critical role in efficiently managing fluid flow within a system. By precisely regulating the rate of flow, these valves ensure optimal performance and prevent issues such as pressure fluctuations and flow inconsistencies. This level of control is essential in various applications, including hydraulic systems, HVAC systems, and industrial processes, where maintaining a consistent flow is crucial for overall operational efficiency.
Impact on System Performance
The proper functioning of flow control valves has a significant impact on the overall performance of a system. These valves help in maintaining the desired flow rate, which in turn contributes to the system’s efficiency and reliability. By controlling the flow of fluids, they help in preventing overload, cavitation, and excessive wear and tear on system components. Additionally, they enable precise adjustments, ensuring that the system operates at its optimal capacity, thereby enhancing its longevity and performance.
How Flow Control Valves Work
Operating Principles
Flow control valves regulate the flow of fluid in a system to maintain a desired speed, direction, pressure, or flow rate. These valves operate on the principle of controlling the energy in a fluid system. By using a variety of methods, they ensure that the fluid flow remains within the required parameters. The valves achieve this by manipulating the flow rate, thus enabling the system to function optimally and efficiently.
Control Mechanisms
Flow control valves employ different control mechanisms to modulate fluid flow. One common mechanism is the use of an orifice plate to restrict the flow, creating a pressure differential and regulating the volume of fluid passing through. Another control mechanism involves the use of a needle valve, which adjusts the flow rate by changing the size of the orifice. Additionally, some valves utilize a diaphragm or piston to respond to changes in pressure differentials and modulate the flow accordingly, ensuring precise control over the fluid within the system. These control mechanisms collectively enable flow control valves to finely regulate flow rates and pressures, thereby optimizing the performance of fluid systems.
Applications of Flow Control Valves
Flow control valves find extensive usage in diverse industrial, hydraulic, and pneumatic systems due to their ability to regulate the flow of fluid in response to changing conditions. Let’s explore the various applications of flow control valves in these contexts.
Industrial Usage
In industrial settings, flow control valves play a crucial role in regulating the flow of fluids to ensure the smooth operation of equipment. They are commonly employed in manufacturing processes, chemical plants, and power generation facilities to control the flow of liquids and gases. By adjusting the flow rate, these valves help maintain optimal conditions for different industrial operations, thereby enhancing efficiency and productivity.
Hydraulic Systems
In hydraulic systems, flow control valves are utilized to manage the flow of hydraulic fluid within machinery and equipment. These valves enable precise control over the speed and force of hydraulic actuators, allowing for smooth and accurate movement. Whether in construction machinery, agricultural equipment, or aerospace systems, flow control valves contribute to the safe and efficient operation of hydraulic systems, ensuring precise control of movements and loads.
Pneumatic Systems
Flow control valves also find widespread application in pneumatic systems, where they are employed to regulate the flow of compressed air or gas. By adjusting the airflow, these valves facilitate the precise control of pneumatic actuators, such as cylinders and rotary actuators, in various industrial and automation applications. This enables the precise movement and manipulation of components, contributing to the overall efficiency and accuracy of pneumatic systems.
By understanding the diverse applications of flow control valves in industrial, hydraulic, and pneumatic systems, it becomes evident that these components are indispensable for maintaining precise control over fluid flow in a wide range of operational scenarios.
Factors to Consider When Choosing a Flow Control Valve
Flow Rate and Pressure Requirements
When selecting a flow control valve, it’s crucial to carefully assess the flow rate and pressure requirements of the specific application. The valve must be able to handle the anticipated flow rates while maintaining the necessary pressure levels. Understanding the system’s operating conditions, including both normal and potential peak flow rates and pressures, is essential for choosing the most suitable valve to ensure optimal performance.
Material Compatibility
Another critical consideration is the material compatibility of the flow control valve with the substances it will come into contact with. Different applications may involve varying chemical compositions, temperatures, and pressures, necessitating the use of materials that can withstand these conditions without degradation. Factors such as corrosion resistance, thermal expansion properties, and material strength need to be carefully evaluated to ensure the longevity and reliability of the valve in the intended environment.
Environmental Conditions
The environmental conditions in which the flow control valve will operate play a significant role in the decision-making process. Factors such as temperature variations, exposure to harsh chemicals or abrasive materials, and the presence of any contaminants all need to be taken into account. It is imperative to select a valve that can withstand the specific environmental challenges it will face, ensuring consistent performance and longevity.
By meticulously considering the flow rate and pressure requirements, material compatibility, and environmental conditions, engineers and decision-makers can make informed choices when choosing a flow control valve, ultimately leading to improved system efficiency and reliability.
Maintenance and Troubleshooting of Flow Control Valves
Flow control valves are essential components in various industrial systems, and proper maintenance is crucial to ensure their optimal performance. Regular maintenance practices and prompt troubleshooting of common issues can significantly enhance the efficiency and longevity of these valves.
Regular Maintenance Practices
- Visual Inspection: Regularly inspect the valves for any signs of leakage, corrosion, or damage to the housing and associated components.
- Lubrication: Ensure proper lubrication of moving parts to prevent friction and wear, thereby extending the valve’s lifespan.
- Calibration: Periodically calibrate the valves to maintain precise control over the flow rates and pressure levels.
- Cleaning: Clean the valves and associated pipelines to prevent the accumulation of debris, sediment, or contaminants that could impede the flow or cause damage.
Common Issues and Solutions for Flow Control Valves
- Leakage: If leakage is detected, check for worn-out seals or gaskets, and replace them as necessary. Tighten any loose connections to prevent further leakage.
- Clogging: In case of clogging, flush the valve and associated piping system to remove any obstruction. Consider installing a filtration system to prevent recurrent clogging issues.
- Corrosion: Address corrosion issues by applying protective coatings or using corrosion-resistant materials for valve components. Regularly inspect for corrosion and take preventive measures to mitigate its impact.
- Erratic Flow: If the valve exhibits erratic flow behavior, check for potential obstructions, foreign particles, or malfunctioning control mechanisms. Clean or repair the affected components to restore proper functionality.
By adhering to these maintenance practices and promptly addressing common issues, you can ensure the reliable operation of flow control valves, minimizing downtime and optimizing the performance of industrial processes.
Conclusion
In conclusion, the flow control valve plays a crucial role in regulating the flow of fluids in various systems. By accurately controlling the rate of flow, it ensures optimal performance and efficiency. Whether in industrial applications, hydraulic systems, or HVAC systems, the proper functioning of these valves is essential for maintaining the desired flow rates and pressures. Understanding the importance of flow control valves and their proper maintenance can significantly impact the overall performance and longevity of the systems they are integrated into.