Double Flanged Butterfly Valves: Pressure and Temperature Considerations
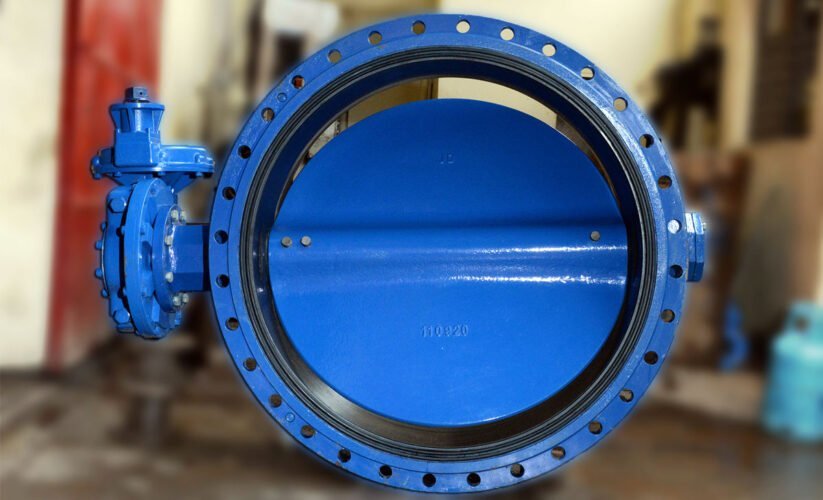
Table of Contents
ToggleUnderstanding the Impact of Pressure and Temperature on Butterfly Valves
When it comes to the performance and reliability of double flanged butterfly valves, understanding the impact of pressure and temperature is crucial. With the ability to control flow in various industrial applications, these valves must be able to withstand the rigors of high pressure and extreme temperatures. In this blog post, we will delve into the considerations for pressure and temperature that are essential for the proper functioning of double flanged butterfly valves in industrial settings.
Understanding Double Flanged Butterfly Valves
Double flanged butterfly valves are a type of butterfly valve that feature flanges bolted to the valve body on both sides, providing a double sealing effect for better sealing performance in high-pressure applications. The design allows for easy installation and maintenance, making them ideal for applications with severe conditions that require high-pressure ratings. When used with appropriate materials, these valves offer excellent performance and durability in extreme temperature environments.
Definition and Design Features
The double flanged design of these valves ensures a double sealing effect, enhancing their sealing performance in high-pressure applications. Typically larger in size, double flanged butterfly valves are used in applications with severe conditions that demand high-pressure ratings. This design feature also contributes to the reduction of fluid losses, making these valves valuable in environments where leakage is not permissible. Their robust design and construction make them suitable for withstanding extreme temperatures, making them a popular choice for applications that operate in such conditions.
Common Applications and Industries
Double flanged butterfly valves are widely used in industries such as chemical processing, water treatment, pharmaceuticals, and other processing plants. These valves play a vital role in isolating, regulating, and controlling the flow of liquids, gases, and slurries in pipelines. Their double flanged design and durability make them suitable for use in applications where high-pressure resistance and reliable sealing performance are essential. Additionally, the ease of installation and maintenance of double flanged butterfly valves contributes to their popularity in industries where efficient flow control and maintenance are crucial.
Basics of Pressure in Valve Systems
Pressure is a critical factor in the performance of valve systems. Understanding pressure ratings and how pressure affects valve performance is essential for the proper functioning of double flanged butterfly valves.
Pressure Ratings Explained
Pressure ratings, often indicated in pounds per square inch (psi), define the maximum pressure a valve can withstand without compromising its structural integrity. It is imperative to select a valve with a pressure rating that exceeds the maximum pressure expected in the system to prevent failure or leakage. When operating within the designated pressure range, the valve functions optimally and ensures safety and reliability.
How Pressure Affects Valve Performance
The impact of pressure on valve performance is multifaceted. Elevated pressures can influence the flow characteristics of the fluid passing through the valve. High-pressure conditions may lead to increased turbulence, erosion, or cavitation, which can degrade the valve and impair its functionality over time. Moreover, excessive pressure can exert undue stress on the valve components, potentially causing deformation or mechanical failure.
Consider, for instance, the implications of pressure differentials on the operation of relief valves. The cracking pressure, the point at which a relief valve opens to release fluid, is a critical parameter influenced by system pressure. Understanding and controlling pressure differentials are essential for ensuring the proper functioning of relief valves and, by extension, the overall hydraulic system.
In summary, comprehending pressure ratings and the effects of pressure on valve performance is paramount for the selection, installation, and maintenance of double flanged butterfly valves. By considering pressure-related factors, engineers and operators can optimize valve functionality and uphold system integrity.
Temperature Factors in Butterfly Valve Operation
Understanding the impact of temperature on butterfly valve performance is crucial for ensuring efficient and reliable operation. Temperature plays a significant role in determining the limits and material considerations for butterfly valves, particularly in high and low-temperature environments.
Temperature Ranges and Limits
Temperature ranges and limits are critical factors to consider when selecting butterfly valves for specific applications. High temperatures can cause materials to weaken, leading to reduced valve lifespan and potential for leakage. Conversely, low temperatures can result in brittle fracture, especially if the valve material is not suitable for extreme cold conditions. It is essential to select butterfly valves capable of withstanding the intended temperature range to ensure long-term performance and safety.
Material Considerations for High and Low Temperatures
Choosing the right materials for butterfly valves operating in high and low-temperature environments is essential for maintaining optimal performance. High-temperature applications require materials with excellent heat resistance to prevent degradation and ensure long-term reliability. In contrast, low-temperature environments necessitate materials that can maintain structural integrity and flexibility without becoming brittle. Selecting appropriate materials based on temperature considerations is crucial for preventing premature wear, leakage, and system failures.
Temperature considerations significantly influence the selection and application design of butterfly valves across various industrial settings, ensuring reliable operation and minimizing safety risks. By understanding the impact of temperature on butterfly valve performance and selecting suitable materials, operators can optimize system efficiency and longevity.
The Importance of Pressure-Temperature Ratings
Pressure-Temperature Rating Charts
In the realm of industrial valves, understanding pressure-temperature ratings is crucial for optimal valve selection and safe operation. Pressure-temperature rating charts provide comprehensive guidelines for the maximum allowable pressure and temperature combinations, ensuring the valve’s suitability for specific application requirements. These charts are essential references that empower engineers and system designers to make informed decisions when choosing the right valve for their specific operational conditions.
Selecting the Right Valve Based on Pressure-Temperature Ratings
When selecting a double flanged butterfly valve, it’s imperative to align the pressure-temperature ratings with the demands of the intended system. Opting for a valve with lower pressure or temperature ratings than required can lead to catastrophic failures, while choosing a valve with unnecessarily high ratings can result in increased costs and inefficiency. By closely adhering to the pressure-temperature limitations outlined in the rating charts, engineers can confidently pinpoint the most suitable valve that promises optimal performance and longevity under operational stressors.
Installation Considerations for Double Flanged Butterfly Valves
Flange Compatibility and Gasket Selection
When installing double flanged butterfly valves, it is crucial to ensure that the flanges are compatible with the valve. Consider the pressure and temperature ratings of the flanges to ensure they are suitable for the intended application. Proper gasket selection is equally important to maintain a leak-free seal. The gasket material should be compatible with the process fluid and capable of withstanding the operating conditions to prevent any leakage or failures. It is essential to consult with the valve manufacturer or a qualified engineer to determine the appropriate gasket material based on the specific requirements of the installation.
Bolting and Torque Requirements
Correct bolting procedures are essential for the proper installation of double flanged butterfly valves. It is crucial to use the correct bolt type, size, and grade to achieve the required level of tightness. Additionally, proper torque requirements must be followed to ensure a secure and leak-free connection. Under-torquing can lead to flange leakage, while over-torquing can result in gasket damage or deformation. Using a calibrated torque wrench and following the manufacturer’s specifications for bolt tightening sequences and torque values is essential to ensure a reliable and safe installation.
Maintenance and Testing for Optimal Performance
Routine Inspection and Maintenance Schedule
Regular maintenance and inspections are crucial for ensuring the optimal performance and longevity of double flanged butterfly valves. Establishing a routine maintenance schedule is imperative to prevent potential issues that may arise from wear and tear, corrosion, or other environmental factors. It is recommended to conduct visual inspections periodically to check for any signs of leakage, corrosion, or damage to the valve and its components. Additionally, lubrication of the valve components should be part of the routine maintenance schedule to ensure smooth operation and longevity.
Pressure and Temperature Testing Protocols
In addition to routine maintenance, pressure and temperature testing protocols are essential to ascertain the integrity and functionality of double flanged butterfly valves. Pressure testing involves subjecting the valve to varying pressure levels to ensure that it can withstand the specified pressure rating without any leakage. Similarly, temperature testing assesses the valve’s performance under different temperature conditions, ensuring that it can operate effectively within the designated temperature range. These testing protocols are vital for validating the performance and safety of the valves in demanding industrial environments.
Troubleshooting Common Issues for Double Flange Butterfly Valves
Leakage Due to Pressure or Temperature Misalignment
Leakage in double flanged butterfly valves can occur when there is a misalignment of pressure and temperature. When the pressure and temperature conditions exceed the valve’s design limitations, it can lead to the distortion of the sealing components, causing leakage. To troubleshoot this issue, it is imperative to ensure that the operating pressure and temperature are within the specified limits for the valve. Regular monitoring and adjustment of pressure and temperature parameters can prevent this type of leakage.
Wear and Tear from Extreme Conditions
Extreme conditions such as high pressure, temperature variations, and aggressive media can cause wear and tear on double flanged butterfly valves. Continuous exposure to extreme conditions can lead to erosion, corrosion, and degradation of valve components, resulting in reduced performance and potential leakage. To troubleshoot this issue, regular inspection and maintenance of the valves are crucial. Utilizing protective coatings, materials resistant to extreme conditions, and implementing proper maintenance schedules can mitigate wear and tear, prolonging the valve’s lifespan.
Advances in Double Flanged Butterfly Valve Technology
The evolution of double flanged butterfly valve technology has brought about notable innovations in materials and design, as well as the integrations of new technologies, resulting in enhanced pressure and temperature capabilities. These advancements have significantly impacted the efficiency and reliability of these valves in various industrial applications.
Innovations in Materials and Design
In recent years, the materials used in the construction of double flanged butterfly valves have undergone significant improvements, leading to enhanced durability and performance. Advanced materials such as high-grade stainless steel, carbon steel, and corrosion-resistant alloys have replaced traditional materials, offering superior resistance to wear, corrosion, and high temperatures. Furthermore, innovative design enhancements, including optimized disc and seal configurations, have contributed to improved sealing capabilities and reduced leakage rates, ensuring maximum operational efficiency and longevity.
Impact of New Technologies on Pressure and Temperature Capabilities
The integration of cutting-edge technologies, such as advanced computational fluid dynamics (CFD) and finite element analysis (FEA), has revolutionized the pressure and temperature capabilities of double flanged butterfly valves. These technologies have enabled manufacturers to optimize the valve geometry, enhance the flow characteristics, and minimize pressure drops, resulting in improved performance across a wider range of operating conditions. Additionally, the utilization of state-of-the-art surface treatments and coatings has further elevated the temperature resistance and pressure ratings of these valves, allowing for their reliable operation in demanding industrial environments.
The continuous pursuit of materials and design innovations, coupled with the adoption of new technologies, has elevated the capabilities of double flanged butterfly valves, making them indispensable components in modern flow control systems. These advancements not only enhance the overall efficiency and reliability of industrial processes but also contribute to the sustainability and cost-effectiveness of fluid handling operations.
Conclusion
Understanding the critical role of pressure and temperature considerations for double flanged butterfly valves is essential for ensuring optimal valve performance and longevity. By carefully evaluating the specific operating conditions and selecting valves that are designed to withstand the anticipated pressure and temperature ranges, industries can effectively mitigate the risk of valve failure and costly downtime. Additionally, regular maintenance and monitoring of pressure and temperature parameters are imperative for preserving the integrity of double flanged butterfly valves in demanding operational environments. With a comprehensive understanding of these factors, industries can enhance system efficiency and reliability while minimizing potential safety hazards.