The Working Mechanism of Lift Check Valves in Piping Applications
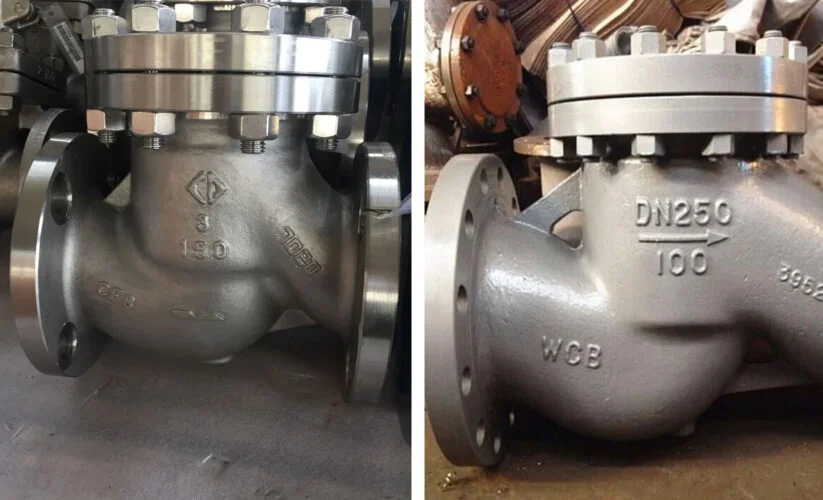
Table of Contents
ToggleHow Lift Check Valves Work in Piping Systems
Understanding the working mechanism of lift check valves in piping applications is crucial for ensuring the efficient and safe operation of fluid systems. Lift check valves play a vital role in preventing backflow and maintaining fluid consistency within the piping network. These valves are designed to allow fluid flow in one direction while preventing reverse flow, thereby safeguarding the system from potential damage and ensuring uninterrupted operation. Lift valves are typically constructed from robust materials such as stainless steel, cast iron, and carbon steel, enabling them to withstand high-pressure service, extreme temperatures, and high velocity. By comprehending the functionality and types of lift check valves, engineers and professionals can make informed decisions regarding their suitability for specific applications.
What is a Lift Check Valve?
Lift check valves play an essential role in piping systems, ensuring the smooth and uninterrupted flow of fluids while preventing backflow. These valves are crucial components for maintaining pressure and preventing damage to pumps and other equipment. Lift check valves are designed to automatically open and allow fluid to flow in one direction, while closing to prevent reverse flow.
Essential Role in Piping Systems
In piping applications, lift check valves are vital for preventing the reversal of flow, protecting equipment, and maintaining system efficiency. These valves are commonly used in situations where backflow could cause damage or disruption to the process, such as in industrial, commercial, and residential plumbing systems.
Material Selection for Durability
The durability and performance of lift check valves are heavily reliant on the materials used in their construction. Stainless steel, brass, and bronze are commonly chosen for their corrosion resistance and durability. The selection of the appropriate material ensures longevity and reliability in demanding operating conditions where the valves are subjected to high pressures and harsh fluids.
Comparison Between Forged and Casted Lift Check Valves
When it comes to lift check valves, there is a choice between forged and casted construction. Forged lift check valves are known for their superior strength and resistance to impact, making them suitable for high-pressure applications. On the other hand, casted lift valves are more cost-effective and can offer adequate performance in lower pressure settings. The choice between the two depends on the specific requirements of the application, taking into account factors such as pressure, temperature, and budget constraints.
How Lift Check Valves Function
Lift check valves play a crucial role in ensuring the smooth and uninterrupted flow of fluids within piping systems. Understanding how these valves function is essential in appreciating their significance in various applications.
The Principle of Pressure Difference
The operation of lift check valves is based on the principle of pressure difference. When the pressure of the fluid flowing in the forward direction exceeds that of the reverse flow, it causes the valve to open, allowing the fluid to pass through. However, when the pressure of the reverse flow becomes greater, the valve closes, preventing backflow.
The Lifting Mechanism Explained
Lift check valves are designed with a mechanism that lifts an internal disc or ball to allow fluid passage only in one direction. This lifting action occurs in response to the pressure exerted by the forward flow, ensuring smooth flow while preventing reverse flow when the pressure conditions change.
The Role of Guide Ribs in Valve Stability
Guide ribs within lift check valves play a critical role in maintaining valve stability during operation. These ribs help to guide the movement of the internal components, ensuring proper alignment and preventing potential issues such as fluttering or excessive vibration. By providing structural support, guide ribs contribute to the reliable and efficient performance of lift valves.
Understanding the intricate workings of lift check valves sheds light on their functionality within piping applications, highlighting their effectiveness in controlling the flow of fluids while minimizing the risk of backflow and associated disruptions.
Types of Lift Check Valves and Their Uses
Lift check valves come in various types, each designed for specific applications to ensure efficient functioning within piping systems. Understanding the different types and their uses is crucial for selecting the most suitable option for your needs. Let’s delve into the various types of lift check valves and their specific applications.
Forged Lift Check Valves for High-Pressure Applications
Forged lift check valves are engineered to withstand high-pressure environments, making them ideal for applications where the flow of fluids or gases needs to be regulated effectively under extreme pressure conditions. These valves are constructed from forged steel, offering exceptional strength and durability, thus ensuring reliable performance in demanding industrial settings such as power plants, chemical processing facilities, and oil and gas refineries.
Casted Lift Check Valves for Cost-Effective Solutions
Casted lift check valves provide a cost-effective solution for applications that require dependable backflow prevention without compromising on quality. These valves are manufactured through the casting process, making them suitable for various general-purpose industrial and commercial applications where the operating pressure is within moderate ranges. Their robust construction and affordability make them a popular choice in water treatment plants, irrigation systems, and HVAC installations.
Vertical Lift Check Valves for Upward Flow Systems
Vertical lift check valves are specifically designed to facilitate upward flow systems, where the control of backflow is essential for optimal operational efficiency. Their unique vertical orientation allows for seamless flow regulation, preventing reverse flow and ensuring smooth performance in vertical piping configurations such as deep well pumping systems, sump pump installations, and sewage treatment plants.
Horizontal Lift Check Valves for Standard Installations
Horizontal lift check valves are widely used in standard piping installations where horizontal flow regulation is required. These valves are suitable for a broad range of applications, including industrial process pipelines, municipal water distribution systems, and fluid conveying pipelines in various manufacturing facilities. Their horizontal orientation enables efficient backflow prevention and smooth fluid or gas flow in horizontal pipeline configurations.
Understanding the distinctive features and applications of these lift check valve types is essential for making informed decisions regarding their selection and deployment within piping systems. Whether it’s high-pressure environments, cost-effective solutions, upward flow systems, or standard installations, choosing the right type of lift check valve is paramount for ensuring optimal performance and long-term reliability in diverse industrial and commercial settings.
Installing Lift Check Valves
Best Practices for Vertical Lift Check Valve Installation
When installing vertical lift check valves, it’s crucial to ensure proper orientation and positioning. Take into account the flow direction, with the valve positioned to allow for unobstructed flow and prevent backflow. Additionally, ensure that the valve is mounted in a vertical position to allow the disc to move freely. Proper support and anchoring of the valve are essential to prevent stress on the piping system and maintain optimal performance.
To achieve the best results, consider incorporating a soft-start mechanism to prevent the excessive slamming of the valve disc against the seat. This will minimize wear and tear, extending the valve’s service life. Maintaining alignment throughout the installation process is vital to ensure the valve operates effectively under varying flow conditions.
Key Considerations for Horizontal Lift Check Valve Setup
When configuring horizontal lift check valves, attention to detail is crucial for optimal performance. Positioning the valve to allow for unobstructed flow and prevent backflow is essential. Proper anchoring and support of the valve should be prioritized to mitigate stress on the piping system, ensuring long-term functionality.
Considering the flow characteristics and potential system pressure fluctuations, incorporating a suitable buffer may be necessary to minimize the impact of sudden flow changes on the valve’s operation. Additionally, verifying the compatibility of the valve material with the fluid properties and operating conditions is paramount for long-lasting performance.
Maintaining alignment during the installation process is essential to ensure the valve functions efficiently and offers reliable backflow prevention. Adhering to these considerations will contribute to the successful setup of horizontal lift valves, promoting smooth and consistent operation within the piping system.
Advantages of Lift Check Valves in Piping
Prevent Backflow: Lift check valves are designed to prevent backflow in piping applications, ensuring that the flow of fluids only goes in one direction, maintaining system integrity and preventing potential damage.
Lower Pressure Drop: These valves offer lower pressure drop compared to other types of check valves, allowing for more efficient flow and reduced energy consumption in the system.
Minimal Maintenance: Lift valves require minimal maintenance due to their simple design, resulting in cost savings and reduced downtime for the piping system.
Suitable for Vertical Installations: Their design makes lift check valves suitable for vertical piping installations, where other types of check valves may not be as effective.
Versatile Application: Lift valves can be used in a wide range of piping applications, including water distribution, industrial processes, and HVAC systems, providing flexibility and reliability in various settings.
The lift check valves offer several advantages that make them indispensable in piping applications. These advantages include:
Automatic Protection Against Backflow
Lift check valves provide automatic protection against backflow, ensuring that fluids flow in one direction only. When the flow changes direction, an internal disc or ball component raises to allow fluid passage in the intended direction, effectively preventing reverse flow from entering the process stream.
Preventing Fluid Contamination and System Damage
By allowing fluid flow in only one direction, lift check valves effectively prevent fluid contamination and potential damage to the piping system. This is crucial in maintaining the purity of fluids being transported and safeguarding the integrity of the entire system.
Maintaining Flow Consistency in Piping Systems
Lift check valves play a critical role in maintaining flow consistency in piping systems. They ensure that flow is regulated and controlled in the intended direction, thereby promoting efficient and reliable operations. This is particularly important in high-pressure applications where consistent flow is essential for optimal performance.
Maintenance and Troubleshooting
Regular maintenance is crucial for ensuring the longevity and optimal performance of lift check valves in piping applications. By performing routine maintenance, such as inspecting for wear and tear, ensuring proper lubrication, and checking for any leaks or abnormalities, you can significantly extend the lifespan of the valves.
Routine Maintenance for Longevity
Inspection: Regularly inspect the lift check valves for any signs of wear, corrosion, or damage. This proactive approach helps in identifying potential issues before they escalate into major problems.
Lubrication: Ensure proper lubrication of moving parts to prevent friction and wear. Use suitable lubricants recommended by the manufacturer to maintain smooth operation.
Pressure Testing: Periodically conduct pressure testing to verify the valve’s sealing efficiency and overall performance. This helps in identifying any potential leaks or sealing issues.
Troubleshooting Common Issues with lift check valves is essential for maintaining an efficient and reliable piping system. Some common issues include valve sticking, improper sealing, and internal leakage. Understanding how to address these issues can prevent system failures and maintain operational continuity.
Troubleshooting Common Issues with Lift Check Valves
Valve Sticking: If the lift check valve is sticking or not operating smoothly, it may indicate a buildup of debris or foreign matter. Cleaning the valve and ensuring proper lubrication can often resolve this issue.
Improper Sealing: In cases where the valve fails to seal properly, inspect the sealing surfaces for damage or wear. Replacing the seals or addressing any surface irregularities can rectify this problem.
Internal Leakage: Internal leakage can occur due to wear or damage to internal components. Carefully inspect the valve internals for any signs of damage and consider replacement or repair as necessary.
When considering Replacement and Repair of lift check valves, it is essential to assess the extent of the damage and evaluate the cost-effectiveness of repair versus replacement. Factors such as the valve’s age, condition, and the availability of replacement parts should be taken into consideration.
Replacement and Repair Considerations
Assessment of Damage: Evaluate the extent of the damage and determine whether it is feasible to repair the valve without compromising its performance and reliability.
Cost Analysis: Consider the cost of repair versus the cost of replacement, factoring in downtime, labor, and material expenses to make an informed decision.
Availability of Parts: Check the availability of genuine replacement parts and assess whether repair is a viable option based on the availability of required components.
By prioritizing routine maintenance, promptly addressing common issues, and making informed decisions regarding replacement and repair, you can ensure the uninterrupted functionality of lift valves in piping applications, contributing to the overall efficiency and reliability of the system.
Conclusion
Understanding the working mechanism of lift check valves in piping applications is essential for maintaining the integrity and efficiency of fluid systems. These valves play a crucial role in preventing backflow and potential damage to equipment. The design and operation of lift check valves, whether forged or casted, ensure unidirectional fluid flow, providing automatic and swift action to block reverse flow. Different types of lift valves, including vertical and horizontal variations, cater to specific flow orientations and system requirements. By comprehending the functionality and types of lift check valves, professionals can make informed decisions regarding their selection and installation in various piping applications.