Selecting the Right Pressure Relief Valve for High-Temperature Applications
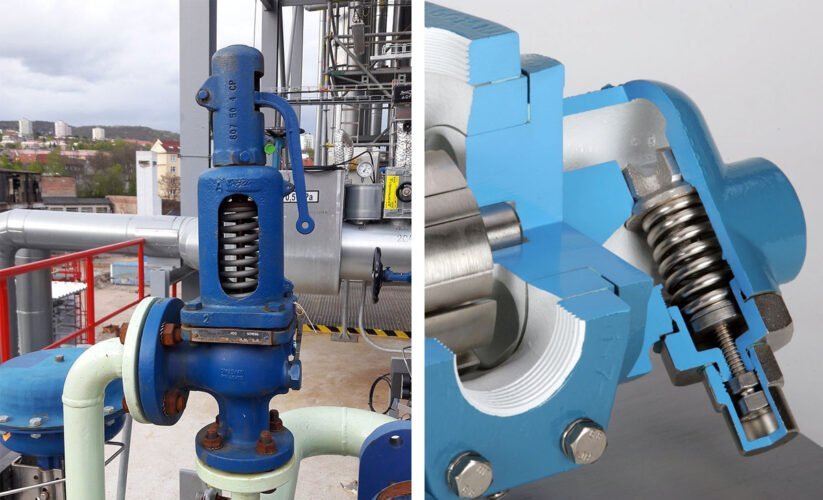
Table of Contents
TogglePressure Relief Valve and High-Temperature Applications
When it comes to high-temperature applications, selecting the right pressure relief valve (PRV) is crucial for ensuring the safety and efficiency of a pressurized system. A PRV serves as a safeguard against overpressure events, preventing potential damage or hazards. Understanding the different types of PRVs, such as spring-loaded, pilot-operated, buckling pins, and rupture disks, is essential in making an informed choice. Factors like backpressure, service, discharge capacity, and inlet pressure losses play a significant role in determining the most suitable PRV for a specific application. Additionally, considerations for set pressure and CDTP (Coefficient of Discharge, Temperature, and Pressure) calculations are vital in the selection process to ensure optimal performance.
Understanding Pressure Relief Valves
Definition and Importance in High-Temperature Applications
Pressure relief valves, also known as safety relief valves, play a critical role in high-temperature applications to safeguard equipment from overpressure and potential damage. These valves are designed to open at a predetermined pressure to release excess fluid until the pressure returns to safe levels. In high-temperature settings, the risk of overpressure and system failure is particularly significant, making the selection of the right pressure relief valve a crucial consideration for ensuring operational safety and efficiency.
How Pressure Relief Valves Work
Pressure relief valves function through a simple yet effective mechanism. Comprising three main elements, including the valve, sensing component, and reference force element, these valves remain closed under normal operating conditions. However, when the pressure within the system surpasses the predetermined set point, the valve opens to release the excess fluid. As the upstream pressure falls back slightly below the set pressure, the valve closes once again, ensuring that the system remains within safe operating parameters.
In high-temperature applications, the proper functioning of pressure relief valves is essential to prevent the build-up of excessive pressure that could lead to catastrophic consequences. The design and operation of these valves are tailored to withstand the challenges posed by elevated temperatures and ensure the reliable protection of equipment and personnel in such demanding environments.
Types of Pressure Relief Valves for High-Temperature Use
Safety Valves
Safety valves are essential in high-temperature applications for efficiently releasing excess pressure to prevent catastrophic system failures. These valves are designed to open gradually, allowing fluid to escape as the system pressure rises. Operating like a pressure watchdog, safety valves guarantee that pressure levels do not surpass the specified limit, ensuring the safety and longevity of the equipment.
Pilot-Operated Relief Valves
Pilot-operated relief valves are ideal for high-temperature environments as they offer precise pressure control and stability. By utilizing a control pilot to sense the system pressure, these valves provide accurate and reliable relief, safeguarding the equipment from potential damage. In high-temperature applications, these valves play a critical role in maintaining optimal pressure levels within the system.
Rupture Discs
Rupture discs are a crucial component in high-temperature systems, serving as a proactive solution for pressure relief. These discs act as a barrier that ruptures at a predefined pressure, facilitating the immediate release of excess pressure. Their rapid response is particularly beneficial in high-temperature applications, where swift pressure relief is essential to prevent equipment damage.
In the realm of high-temperature applications, selecting the appropriate pressure relief valve type is paramount to ensuring operational safety and efficiency. The distinct characteristics of safety valves, pilot-operated relief valves, and rupture discs offer tailored solutions to address the unique demands of high-temperature environments.
Material Considerations for High-Temperature Applications
Selecting the right materials is crucial for high-temperature pressure relief valve applications to ensure optimal performance and longevity. In such demanding environments, the choice of materials can significantly impact the valve’s ability to withstand extreme heat and pressure. Here, we’ll explore the key material considerations for high-temperature applications, including stainless steel valves, alloy valves, and ceramic valves.
Stainless Steel Valves
Stainless steel is a popular choice for high-temperature applications due to its exceptional resistance to corrosion and oxidation at elevated temperatures. These valves are known for their durability and strength, making them suitable for withstanding harsh operating conditions. The austenitic structure of stainless steel provides stability and reliability, making it a preferred material for high-temperature pressure relief valves in various industries, including oil and gas, chemical processing, and power generation.
Alloy Valves
Alloy valves are engineered to offer superior performance in high-temperature environments where standard materials may fail. These valves are crafted from a combination of metals and other elements to enhance their heat resistance, mechanical properties, and corrosion resistance. Common alloy materials used for high-temperature applications include Inconel, Hastelloy, and Monel, each tailored to withstand specific temperature ranges and chemical exposures. Alloy valves provide reliable protection against extreme conditions, making them essential for critical industrial processes.
Ceramic Valves
Ceramic valves are well-suited for high-temperature applications that demand exceptional wear and corrosion resistance. These valves are engineered from advanced ceramic materials such as silicon nitride, alumina, and zirconia, offering excellent thermal stability and mechanical strength. Ceramic valves exhibit low thermal expansion and high hardness, making them ideal for withstanding intense heat and thermal cycling. Their ability to maintain dimensional stability under extreme temperatures makes ceramic valves a valuable choice for high-temperature pressure relief applications in industrial settings.
In the next sections, we will delve into additional factors and considerations to guide the selection of the right pressure relief valve for high-temperature applications.
Key Factors in Selecting the Right Valve
Temperature Ratings and Limits
Selecting the right pressure relief valve for high-temperature applications necessitates a thorough examination of the temperature ratings and limits associated with the valve. High temperatures can significantly impact the performance and longevity of the valve, making it imperative to choose a valve with a temperature rating that aligns with the specific demands of the application. It is crucial to consider the material composition of the valve and ensure that it can withstand the high temperatures without compromising its functionality.
Pressure Settings and Overpressure Allowance
Another critical factor in the selection process is the pressure settings and overpressure allowance of the valve. Understanding the operating pressure conditions and the maximum pressure that the valve may be subjected to is essential for ensuring optimal performance and safety. It is vital to choose a valve with precise pressure settings that align with the application’s requirements, along with an adequate overpressure allowance to accommodate any potential pressure spikes.
Flow Requirements and Capacity
When selecting a pressure relief valve for high-temperature applications, evaluating the flow requirements and capacity is paramount. Ensuring that the valve can effectively manage the flow of hot fluids or gases is crucial for maintaining operational efficiency and safety. By understanding the specific flow requirements and capacity demands of the application, it becomes possible to select a valve that can accommodate the anticipated flow rates without experiencing performance limitations.
Valve Sizing for Optimum Performance
Valve sizing plays a pivotal role in determining the optimum performance of the pressure relief valve in high-temperature applications. Properly sizing the valve involves considering factors such as the inlet and outlet connections, discharge piping, and the overall system design. The goal is to select a valve size that facilitates efficient pressure relief while minimizing backpressure and ensuring compatibility with the surrounding system components. Careful consideration of valve sizing is essential for maximizing the effectiveness and reliability of the pressure relief system.
Installation and Maintenance
Prior to installation, it’s pivotal to ascertain that the pressure relief valve (PRV) is compatible with high-temperature applications and meets the required codes and standards. Here are crucial aspects to consider when installing and maintaining a PRV for high-temperature applications:
Proper Installation Practices
- Positioning: Ensure the PRV is positioned in a way that allows for proper heat dissipation and ease of access for maintenance.
- Temperature Consideration: Prioritize the installation location, considering the ambient temperature and the potential for temperature fluctuations to ensure optimal PRV performance.
- Piping and Discharge: Properly size the piping and discharge line to handle the high-temperature fluid and prevent any obstructions that could hinder valve operation.
Regular Maintenance and Testing
- Scheduled Inspections: Establish a routine inspection schedule to assess the PRV’s condition and functionality.
- Testing Protocols: Conduct regular testing to verify the PRV’s response to overpressure conditions, ensuring its reliability during high-temperature operations.
- Record-Keeping: Maintain detailed records of maintenance activities, including test results, replacements, and any adjustments made to the valve.
Recognizing Signs of Valve Failure
- Leakage: Any indication of leakage from the PRV, especially in high-temperature environments, warrants immediate attention and potential replacement.
- Abnormal Sounds: Unusual sounds during valve operation could signal potential malfunctions, necessitating thorough inspection and maintenance.
- Pressure Fluctuations: Regular monitoring of pressure fluctuations and irregularities can help identify potential valve failure and the need for remedial action.
Regular maintenance and timely recognition of potential issues are essential for ensuring the reliability and effectiveness of pressure relief valves in high-temperature applications.
Compliance with Industry Standards
ASME Codes and Requirements
When selecting a pressure relief valve for high-temperature applications, it is crucial to ensure compliance with industry standards. The American Society of Mechanical Engineers (ASME) has established codes and requirements that govern the design, testing, and installation of pressure relief valves. These codes, particularly Section VIII of the ASME Boiler and Pressure Vessel Code, provide specific guidelines for the selection and use of pressure relief valves in high-temperature applications. Adhering to ASME standards not only ensures safety and reliability but also legal compliance with industry regulations.
ISO and Other International Standards
Apart from ASME codes, it is imperative to consider international standards such as those set by the International Organization for Standardization (ISO). ISO standards offer global directives for the design, manufacture, and testing of pressure relief valves, ensuring consistency and quality across international markets. Additionally, other regional and national standards may apply depending on the specific operating environment. By adhering to ISO and other international standards, businesses can demonstrate a commitment to quality and safety on a global scale, enhancing credibility and market competitiveness.
Case Studies
Success Stories
In a recent case study, a manufacturing plant faced a high-temperature application challenge. After consulting with experts, they selected a pressure relief valve with advanced thermal capabilities, ensuring optimal performance even in extreme conditions. This led to a significant decrease in downtime, resulting in substantial cost savings and enhanced operational efficiency.
Another success story involves a petrochemical facility that experienced valve failures due to high temperatures. By implementing a specially designed pressure relief valve, they were able to mitigate potential safety hazards and prevent costly equipment damage. This proactive approach not only safeguarded the plant but also boosted confidence in their high-temperature operations.
Lessons Learned from Valve Failures
Valve failures in high-temperature applications can have severe consequences, ranging from production delays to safety risks. In one case, inadequate understanding of temperature thresholds led to valve malfunctions, causing unplanned shutdowns and financial setbacks. This emphasizes the criticality of selecting the right pressure relief valve designed for specific temperature ranges.
Furthermore, improper maintenance and neglecting temperature-related factors resulted in valve failures at a power generation facility. The repercussions included regulatory non-compliance and reputational damage. These instances underscore the significance of conducting thorough assessments and adhering to recommended maintenance schedules to avert potential valve failures in high-temperature environments.
Conclusion
Selecting the right pressure relief valve for high-temperature applications is crucial for ensuring the safety and efficiency of pressurized systems. Considerations such as backpressure, service requirements, discharge capacity, and inlet pressure losses play a significant role in determining the most suitable type of relief valve for a specific application. Understanding the distinctions between conventional, bellows-type, and pilot-operated relief valves, as well as their respective limitations, is essential for making an informed decision. Additionally, recognizing the set pressure and CDTP calculations is fundamental to identifying the most appropriate pressure relief valve for high-temperature applications. By carefully evaluating these factors, engineers and operators can effectively mitigate the risks of overpressure events in industrial processes.