Choosing the Right Material for Globe Valves
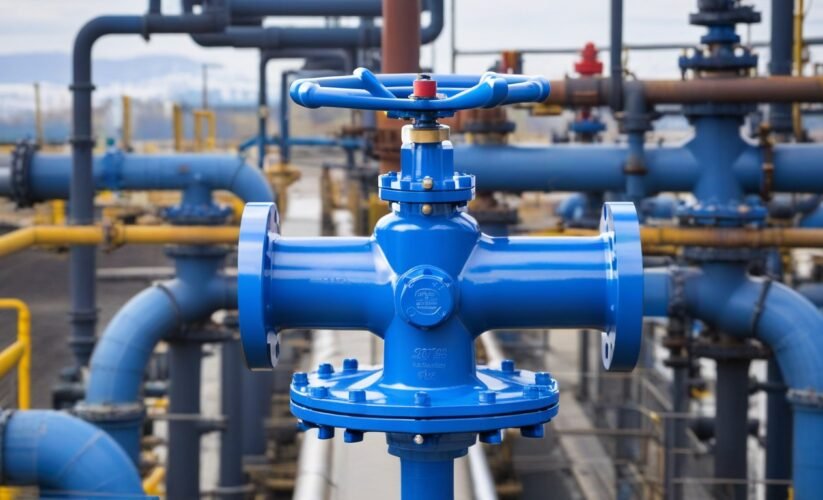
Table of Contents
ToggleIntroduction
In the world of fluid control systems, the importance of choosing the right valve cannot be overstated. Globe valves are a common and versatile type of valve used in various industries, and selecting the right one can significantly impact the efficiency and safety of your operations. To make an informed decision, it’s essential to consider several factors and work with reputable Globe Valve Manufacturers and Suppliers. In this blog, we will explore key selection tips and considerations to help you choose the right globe valve for your specific application.
What is a Globe Valve?
Before diving into the selection process, let’s have a basic understanding of what globe valves are and how they work. Globe valves are linear motion valves that control the flow of fluids by moving a disc (or plug) along a seat, which regulates the flow rate. These valves are used to start, stop, and regulate the flow of liquids, gases, or steam in various applications, including industrial, commercial, and residential systems.
Factors Affecting Globe Valve Material Selection
Globe valves are crucial components in various industries, and choosing the right material is paramount for their optimal performance and longevity. Selecting the appropriate material involves considering several factors to ensure compatibility with the fluid, endurance under specific conditions, and resistance to corrosive elements. Understanding the impact of fluid characteristics, temperature and pressure demands, as well as the corrosiveness of the environment, is essential for effective globe valve material selection.
Fluid Characteristics and Compatibility of Globe Valves
The nature of the fluid flowing through the valve significantly influences the choice of material. Factors such as acidity, viscosity, and erosiveness play a critical role in determining material compatibility. For instance, corrosive fluids require materials with high resistance to chemical reactions, while high-temperature fluids necessitate materials with excellent thermal stability. Selecting the wrong material can lead to accelerated corrosion, erosion, or even catastrophic failure, underscoring the importance of aligning material properties with the fluid’s characteristics.
Temperature and Pressure Demands from Globe Valves
The operating temperature and pressure range exert significant influence on the material selection for globe valves. Materials must withstand the prevailing temperature conditions without compromising their mechanical properties or structural integrity. High-pressure environments demand materials with exceptional tensile strength and resistance to deformation, ensuring reliable operation under varying pressure levels. The interplay between temperature and pressure necessitates a comprehensive evaluation of materials to mitigate the risk of material failure due to thermal expansion, contraction, or mechanical stress.
Corrosiveness and Material Endurance
The corrosiveness of the operating environment directly impacts the longevity and performance of globe valve materials. Exposure to corrosive elements can degrade materials over time, leading to diminished structural integrity and functionality. Selecting materials with superior corrosion resistance is imperative for ensuring the long-term reliability of globe valves in aggressive industrial applications. Additionally, evaluating the material’s endurance under specific environmental conditions, such as exposure to chemical agents or abrasive particles, is crucial for mitigating the detrimental effects of corrosion and preserving the valve’s operational efficiency.
Globe Valve Size and Pressure Rating for Your System
Selecting the right globe valve for your industrial system is crucial for ensuring optimal performance and longevity. When assessing valve size and pressure ratings, understanding the importance of valve sizing and the significance of pressure ratings is paramount.
Importance of Sizing for Globe Valves
Valve sizing is a critical factor in ensuring that a globe valve meets the required flow rate of your system. The size of the valve directly impacts its maximum flow capacity, and selecting the appropriate size is essential for achieving the desired flow rate within the system.
Manufacturers often provide a flow coefficient (Cv) for their valves, which indicates the relationship between pressure drop across the valve and the corresponding flow rate. Understanding the Cv and the geometry of the valve’s flow path or orifice is essential for proper sizing, as different types of valves offer varying flow resistance and capacity based on their design. It’s important to consider the functional differences between valve types and their intended application to make an informed sizing decision.
Understanding Pressure Ratings
Pressure ratings play a crucial role in ensuring the safety and efficiency of your industrial fluid system. The pressure rating of a globe valve determines its capacity to withstand pressure within the system without compromising its integrity. It is imperative to select a valve with a pressure rating that aligns with the operating pressure of your system to prevent potential leaks or failures. Evaluating the temperature and pressure requirements of your application is essential when considering pressure ratings, as these factors directly impact the performance and lifespan of the valve.