Different Types of Gate Valves: An Overview
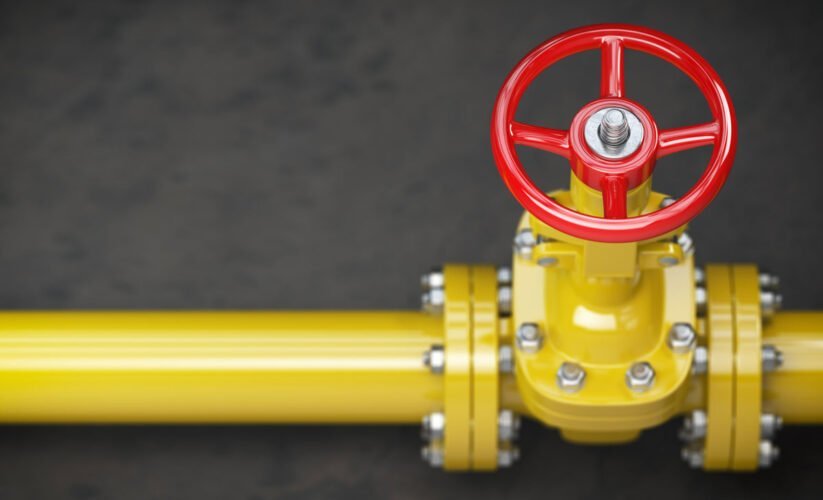
Table of Contents
ToggleIntroduction
A gate valve is a vital component in various process industries, providing efficient control over the flow of fluids and gases. It is a linear motion valve used to start or stop fluid flow, with the valve position being either fully open or fully closed gate. When fully open, the disk is completely removed from the flow, resulting in minimal pressure drops. However, it should not be used for regulating or throttling flow due to the potential for erosion, vibration, and noise. In this article, we’ll provide an overview of the different types of gate valves, including their construction, applications, and advantages they offer.
Understanding Gate Valves in Industry
Gate valves play a critical role in the regulation and control of fluid flow within various industrial applications. These valves are designed to either allow or stop the flow of liquids by implementing a straight-line motion, making them essential components in pipeline systems. Understanding the function and significance of gate valves is fundamental for ensuring efficient and reliable fluid management processes.
Definition and Function of Gate Valves
Gate valves are multi-turn or linear valves that utilize a closure element known as a disc or gate to control the flow of fluids. The disc is raised or lowered by a stem, either obstructing the flow path to stop the fluid flow or retracting fully to allow unrestricted flow. This distinctive operating mechanism distinguishes gate valves from other valve types, such as ball, plug, and butterfly valves.
Importance of Gate Valves in Controlling Flow
The crucial role of gate valves lies in their ability to provide unobstructed flow when fully open and complete shutoff when fully closed. Their capability to minimize resistance to flow when open makes them highly suitable for on/off applications, where unrestricted flow is essential. Additionally, these valves are preferred for blocking or isolating flow, as they can effectively prevent the passage of fluids when closed. However, it’s important to note that gate valves are not suitable for regulating flow or operating in partially open positions, as doing so can lead to damage and turbulence within the system.
By understanding the definition and function of gate valves, along with their significance in controlling flow within industrial settings, it becomes evident that these valves are integral to ensuring effective fluid management and operational safety.
Types of Gate Valves
- Rising Stem Gate Valve: In this type, the stem rises as the valve is opened, providing a clear visual indication of the valve’s position.
- Non-Rising Stem Gate Valve: The stem of this valve does not rise as the valve is opened, making it suitable for limited space installations.
- Solid Wedge Gate Valve: This design features a single, solid wedge for a tight seal when closed, but it can be more prone to sticking in some applications.
- Flexible Wedge Gate Valve: With a wedge made up of multiple pieces to allow for movement and flexibility, this type is suitable for systems with temperature variations.
- Split Wedge Gate Valve: A two-piece wedge that can accommodate thermal expansion and contraction within the valve, reducing the likelihood of binding.
- Parallel Slide Gate Valve: In this valve, the gate moves up and down in a parallel fashion to the direction of fluid flow, reducing wear and tear for high-velocity applications.
- Knife Gate Valve: Designed for handling slurries, powders, and other difficult media, this valve features a sharp-edged gate to cut through and seal against the material.
- Conduit Gate Valve: Also known as a slab gate valve, this type is specifically designed for the oil and gas industry, providing a full bore and bidirectional sealing.
Main Components of a Gate Valve
A gate valve comprises critical components, each playing a specific role in its operation. Understanding these components is essential for comprehending how gate valves function and identifying common issues that may arise.
Body and Bonnet
The body serves as the primary pressure-retaining part of the valve. It contains operational parts such as the gate and seat and provides passage for flow. The bonnet acts as an additional pressure-retaining component, enclosing and safeguarding the valve’s stem and wedge. It also allows access for maintenance and repairs.
- Screwed Bonnet: Simple and suitable for small valves and low-pressure applications.
- Union Bonnet: Offers robust connection and prevents seal deterioration over time.
- Bolted Bonnet: Necessary for larger valve sizes and higher working pressures, requiring a gasket for sealing.
- Welded Bonnet: Ideal for designs not requiring frequent disassembly, offering a lightweight assembly compared to bolted bonnets.
- Pressure Seal Bonnet: Specifically designed for high-pressure applications, utilizing the internal pressure to enhance the body-bonnet joint seal.
Gate Mechanism
The gate, also known as a disc or obturator, is responsible for obstructing or allowing flow through the valve. Different gate designs and technologies are available to cater to specific application requirements.
- Wedge Gate: Utilizes a wedge-shaped disc to obstruct or allow flow, making it suitable for high-flow or turbulent applications such as steam service.
Valve Seats
Valve seats play a crucial role in providing a sealing surface for the gate, ensuring leak-tight closure and preventing flow when the valve is in the closed position. Proper seat design is essential for efficient valve operation and longevity.
Valve Stem Operation
The valve stem facilitates the movement of the gate within the valve body. It is crucial for controlling the flow of the medium passing through the valve and ensuring smooth operation.
Understanding the main components of gate valves, including the body and bonnet, gate mechanism, valve seats, and valve stem operation, provides valuable insights into the functionality of these essential industrial components.
Types of Gate Valves Based on Gate Design
Gate valves are essential in various industries for controlling fluid and gas flow. When selecting a valve, it’s crucial to consider the gate design as it directly affects the valve’s performance. Here, we’ll explore three common types of gate valves based on gate design.
Solid Wedge Gate Valve
Solid wedge gate valves feature a single, solid gate that moves up and down to control flow. This design provides a tight seal when the valve is fully closed, effectively preventing leakage. However, these valves may be susceptible to thermal binding due to temperature variations.
Flexible Wedge Gate Valve
Flexible wedge gate valves are equipped with a gate that can flex slightly to improve the sealing ability against the valve seats. This design is suitable for addressing potential issues related to thermal binding, offering enhanced performance in varying temperature conditions.
Split Wedge or Parallel Disk Gate Valve
The split wedge or parallel disk gate valve comprises two independent gate segments that come together to halt the fluid flow. This design can compensate for potential deformation or misalignment, ensuring a secure seal even in less-than-ideal operating conditions.
Selecting the appropriate gate design is crucial for ensuring optimal performance and efficiency in fluid and gas control systems. Understanding the unique characteristics of each gate design enables industries to make informed decisions when choosing the right valves for specific applications.
Gate Valves Classified by Body and Bonnet Connection
Gate valves are classified based on their body and bonnet connection, which influences their performance and applications. The following types are commonly used:
Screwed Bonnet Gate Valves
Screwed bonnet gate valves are designed with a threaded connection between the body and the bonnet. This type is suitable for low-pressure applications where frequent maintenance or inspection is required. The threaded bonnet allows for easy disassembly and reassembly, making it convenient for maintenance purposes.
Bolted Bonnet Gate Valves
Bolted bonnet gate valves feature a bolted connection between the body and the bonnet, providing a more secure and durable seal compared to screwed bonnet valves. They are suitable for a wide range of pressure and temperature conditions, making them versatile for various industrial applications. The bolted construction ensures a tight seal, making these gate valves suitable for high-pressure services.
Welded Bonnet Gate Valves
Welded bonnet gate valves are constructed with a welded connection between the body and the bonnet, providing a permanent and leak-proof seal. This design is ideal for high-pressure and high-temperature applications where reliable performance is essential. The welded construction enhances the valve’s integrity, making it suitable for critical service conditions.
Pressure Seal Bonnet Gate Valves
Pressure seal bonnet gate valves feature a pressure seal design between the body and the bonnet, allowing for superior sealing capability in high-pressure applications. The pressure seal construction ensures a tight and reliable seal under extreme pressure conditions, making these valves suitable for severe service environments where safety and performance are paramount.
Distinguishing Gate Valves by Stem Movement
Gate valves can be distinguished by the movement of their stems, which impacts their operation and performance. This section will delve into the characteristics of rising stem and non-rising stem gate valves to provide a comprehensive understanding of the differences between the two types.
Rising Stem Gate Valve
Rising stem gate valves are primarily utilized to start or stop flow without the need for regulation. When in the open position, the valve disc is completely removed from the flow path, minimizing pressure drop. This design makes them an optimal choice for isolation applications, particularly in large-diameter and high-pressure lines. The rise and fall of the stem in response to the rotation of the handwheel facilitate easy identification of the valve’s position. However, it is important to note that the installation height required for this valve design is relatively larger compared to non-rising stem valves. Additionally, the exposed threading allows for ease of lubrication, enhancing maintenance efficiency.
Non-Rising Stem Gate Valve
In contrast to rising stem valves, non-rising stem gate valves do not exhibit vertical movement of the stem during operation. Instead, the stem’s position remains unchanged, regardless of the valve’s open or closed state. This design eliminates the need for additional clearance above the valve, making it a preferred choice in constrained spaces. Furthermore, the compact structure of non-rising stem gate valves enables them to be deployed in applications where vertical space is limited. Additionally, the absence of exposed threading contributes to a more streamlined appearance and reduces the risk of damage to the stem.
Understanding the distinctive features of rising stem and non-rising stem gate valves is crucial for selecting the most suitable valve type based on specific operational requirements and spatial constraints.
Specialized Gate Valves and Their Applications
Gate valves come in various specialized forms to cater to specific industrial and commercial requirements. The following are two specialized types of gate valves and their applications:
Knife Gate Valves
Knife gate valves are designed for heavy-duty applications such as slurries and viscous fluids that may clog other valve types. Their unique thin gate design allows them to cut through thick media while offering a tight seal. These valves are commonly used in industries such as mining, pulp and paper, wastewater treatment, and power plants. Their ability to handle tough applications makes them an essential component in processes involving abrasive and viscous fluids.
Through-Conduit Gate Valves
Through-conduit gate valves are specially designed with a slab gate that allows uninterrupted flow of fluids. These valves are ideal for applications that require minimal pressure drop and bi-directional shutoff capability. Their design makes them suitable for the transportation of large volumes of fluid in industries such as oil and gas, petrochemical, and water treatment plants. Through-conduit valves provide efficient and reliable flow control, making them a preferred choice for critical pipeline applications.
By understanding the specific features and applications of each specialized valve, industries can optimize their fluid handling processes while ensuring efficient and reliable operations.
Applications of Gate Valves
Gate valves are utilized in a broad range of applications, both above and below ground, due to their design that allows for a free bore and minimal pressure loss. They are particularly well-suited for scenarios where a fully open valve with no obstruction in the flow path is needed, enabling the use of pipe cleaning devices such as pipe cleaning pigs. Gate valves find extensive use with various fluids, including water, gas, wastewater, and neutral liquids within specific temperature limits. For gas applications, these valves can handle a maximum flow velocity and operate within certain temperature ranges.
Where Gate Valves Are Commonly Used
Gate valves are commonly employed in industries such as oil and gas, water and wastewater treatment, mining, and chemical processing. They are used in systems requiring full flow and minimal pressure drop, making them suitable for applications involving slurries, viscous fluids, and non-condensing gases.
Advantages of Using Gate Valves
One of the primary advantages of gate valves is the minimal pressure loss they offer due to the unobstructed flow path when fully open. These valves also feature a multi-turn operation, allowing for gradual opening and closing to prevent water hammer effects. Their bidirectional nature, with the ability to sit on either side of the gate, ensures a tight seal and prevents solids from obstructing the valve, contributing to reliable performance.
Limitations and Considerations in Gate Valve Usage
While gate valves offer several advantages, it is essential to consider their limitations. These valves are not suitable for regulating flow since they are designed for full open or full close operations. Additionally, these valves may be susceptible to damage when exposed to high-velocity flows, and special care must be taken during installation to avoid issues related to solid particles in the fluid stream.
The applications, advantages, and considerations of gate valves make them a versatile option for various industrial and commercial purposes, providing efficient fluid control and reliable performance.
Conclusion
In conclusion, gate valves play a crucial role in controlling the flow of fluids and gases in various industrial processes. With different types of gate valves available, including solid wedge, flexible wedge, and split wedge, as well as variations based on body and bonnet connection, there are options to suit different applications and operational requirements. Understanding the advantages and disadvantages of gate valves, and their specific uses and applications, is essential in selecting the right type of valve for a particular system. By considering these factors, industries can ensure efficient and reliable fluid and gas control in their operations.