Gate Valves: Components, Function, and Applications
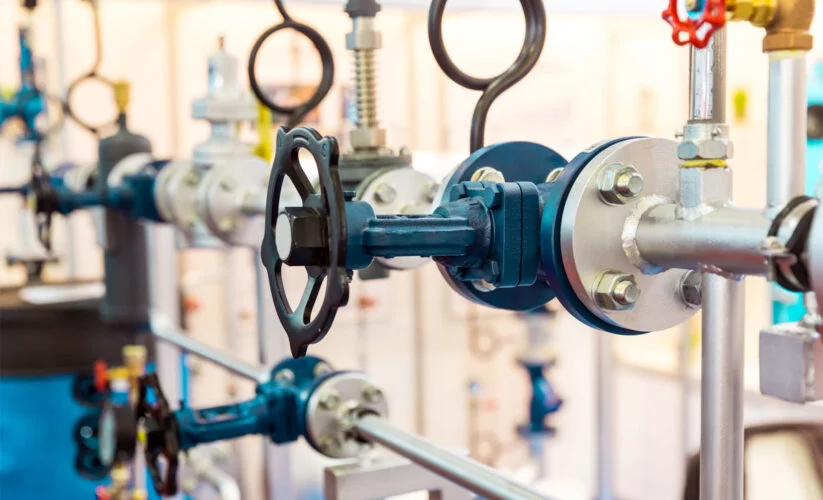
Table of Contents
ToggleComprehensive Guide to Understanding Gate Valves
A gate valve is a control valve that allows or stops fluid flow. It offers a straight-through unobstructed passageway, resulting in minimal pressure loss over the valve. This type of valve also allows for a pig’s passage in cleaning pipe procedures. However, gate valves are slower than quarter-turn valves and should only be used in the fully open or closed position, not to regulate flow. Automated gate valves exist with electric or pneumatic actuators, but a manual gate valve is cost-effective since gate valves are typically used infrequently. Gate valves are also commonly referred to as sluice gate valves.
What is a Gate Valve?
Gate valves are essential components in many industrial and commercial applications, providing a means to control the flow of various types of liquids. These valves operate by raising or lowering a gate within the valve to either block or permit the flow of fluids. Understanding the basic function and advantages of a gate valve is crucial for ensuring their effective use in diverse operational settings.
- What is a gate valve?
- A gate valve is a type of valve that uses a flat or wedge-shaped gate to control the flow of fluid through a pipeline.
- Design:
- It has a simple yet robust design consisting of a gate that slides up and down to either block or allow the flow of fluids.
- Functionality:
- When the valve is fully open, the gate is completely removed from the flow path, minimizing pressure drop and allowing unrestricted flow.
- When the valve is fully closed, the gate forms a tight seal against the valve seats, preventing the flow of fluids through the pipeline.
- Applications:
- Commonly used in applications where a straight-line flow of fluid with minimal restriction is desired, such as in water treatment plants, power plants, and oil and gas refineries.
- Advantages:
- Provides a tight seal, minimal pressure loss, and can be used in both high and low-pressure systems.
- Disadvantages:
- Not suitable for regulating flow, as it is typically either fully open or fully closed.
- Maintenance:
- Requires periodic maintenance to ensure smooth operation and prevent issues such as corrosion or gate jamming.
- Variants:
- Available in various designs including rising stem, non-rising stem, and outside screw and yoke (OS&Y) configurations to suit different installation requirements.
Definition and Basic Function of Gate Valves
A gate valve is a type of valve that employs a gate or wedge-shaped disc to control the flow of fluid. When the valve is fully open, the gate is completely removed from the flow path, allowing unobstructed passage for fluid. Conversely, when the valve is fully closed, the gate is pressed against the valve seat to halt the flow of fluid. This on/off functionality makes a gate valve ideal for applications requiring full flow or complete shut-off.
Key Advantages of Using Gate Valves
- Low Fluid Resistance: They offer minimal interference to fluid flow when fully open, resulting in low pressure drop and energy savings.
- Tight Seal: The gate mechanism allows for a tight seal, preventing leakage and ensuring efficient flow control.
- Bi-Directional Service: They are suitable for use in both directions, providing versatility in fluid handling systems.
- High Durability: With their robust construction, gate valves exhibit longevity and reliability in demanding environments.
- Full Bore Design: The full bore design of them enables unrestricted flow, making them suitable for applications requiring high flow capacity.
Understanding these advantages underscores the value of gate valves in various industries, where precise and reliable fluid control is paramount.
Main Components of a Gate Valve
The Handwheel and its Role
The handwheel is a vital element of a gate valve, serving as the mechanism for opening and closing the valve. By turning the handwheel, the stem and gate mechanism are activated, allowing for precise control of the flow of fluids through the valve.
Stem and Gate Mechanism
The stem and gate mechanism work in unison to regulate the flow of fluids through the valve. As the handwheel is turned, the stem moves up or down, raising or lowering the gate. This action opens or closes the passageway, effectively controlling the flow of liquids or gases.
Sealing the Valve
A crucial function of the gate valve is its ability to create a tight seal when closed. The gate, when descended, fits snugly into the valve seat, preventing the passage of any fluid. This sealing capability ensures efficient shutoff and prevents leakage when the valve is not in operation.
Valve Body and Flanges
The valve body, typically constructed from durable materials such as stainless steel or brass, houses the gate and stem mechanism. The flanges, located at each end of the valve, provide a means for connecting the valve to the pipeline. Proper alignment and bolting of the flanges are essential for maintaining the integrity of the valve and preventing leaks.
This section provides a detailed look at the main components of a gate valve, from the handwheel and stem mechanism to the valve body and flanges. Understanding the role of each component is essential in comprehending the functionality of this type of valve.
How Gate Valves Work
A gate valve controls the flow of fluid by raising or lowering a gate within the valve. This process is simple yet crucial for regulating the flow of liquids or gases in various industrial applications. It is essential to understand the opening and closing process and the full bore flow characteristics of gate valves.
The Opening and Closing Process
The operation of a gate valve involves raising and lowering a gate to open and close the passageway for fluid flow. When the valve is in the open position, the gate is fully retracted into the bonnet, allowing unrestricted flow of the fluid. On the contrary, in the closed position, the gate is lowered to obstruct the flow, effectively shutting off the passage for the fluid. This simple yet effective mechanism makes a gate valve suitable for applications where on/off control is required.
Full Bore Flow Characteristics of Gate Valves
Gate valves are known for their full bore flow characteristics, meaning that the internal diameter of the valve matches the internal diameter of the connected pipeline. This design feature allows gate valves to provide minimal flow restriction, resulting in efficient and unimpeded flow of the fluid. As a result, gate valves are often preferred in applications where a straight, unrestricted flow path is essential to maintain the efficiency of the system.
Understanding the working principles of gate valves, including the opening and closing process and the full bore flow characteristics, is essential for selecting the right valve for a specific application and ensuring optimal performance in industrial settings.
Different Types of Gate Valves
Parallel vs. Wedge-Shaped Gates
Gate valves come in different variations, with the two main types being parallel and wedge-shaped gates. Parallel gate valves have parallel seats and require more precise alignment during operation to achieve proper sealing. In contrast, wedge-shaped gate valves have a single-piece gate with a slight angle on the bottom, allowing for a tight seal with less dependence on precise alignment.
Manual vs. Automated Operation
Gate valves can be operated manually or automated. A manual gate valve involves hand operation using a wheel or lever, providing simplicity and cost-effectiveness. On the other hand, an automated gate valve is powered by pneumatic, hydraulic, or electric actuators for remote or automatic control, offering convenience and adaptability to various industrial applications.
Applications of Gate Valves
Gate valves are crucial components in various industries due to their specific design and functionality. Understanding the different applications of gate valves helps in realizing their significance and effectiveness in diverse environments.
Industries That Rely on Gate Valves
- Oil and Gas Industry: Gate valves are extensively used in the oil and gas sector for regulating the flow of crude oil, natural gas, and other fluids in pipelines and storage facilities.
- Water and Wastewater Treatment: Municipal and industrial water treatment plants depend on gate valves for controlling the flow of water, sewage, and various chemicals.
- Power Generation: Gate valves play a vital role in power plants by managing the flow of steam, cooling water, and other fluids in different stages of the energy generation process.
- Marine Industry: Shipbuilding and marine operations utilize gate valves for controlling the flow of water, fuel, and other fluids within the vessel systems.
- Chemical Processing: The chemical industry relies on gate valves to handle the flow of corrosive and hazardous fluids in manufacturing processes.
Situations Best Suited for Gate Valves
- On/Off Service: Gate valves are ideal for applications that require full flow or complete shutoff, making them suitable for isolation and regulation purposes.
- High-Pressure Systems: Their robust construction enables gate valves to withstand high-pressure environments, making them well-suited for systems operating at elevated pressures.
- Non-Throttling Applications: In situations where throttling or controlling flow rate is not necessary, gate valves offer a simple and effective solution for fluid regulation.
- Bi-Directional Flow Control: Gate valves are capable of handling bidirectional flow, allowing for versatile usage in systems requiring flow reversal capabilities.
Selection and Installation Considerations
Sizing and Connection Types
When selecting a gate valve, one of the primary considerations is the sizing and connection types. It’s crucial to choose the right size to ensure optimal flow control. Gate valves are available in various sizes, so it’s essential to select one that aligns with the intended application. Additionally, understanding the connection types is important for seamless integration with the existing piping system. Gate valves come with different end connections such as flanged, threaded, and welded, each serving specific purposes. Therefore, carefully analyzing the sizing and connection types is imperative for successful installation and functionality.
Material and Pressure Rating Choices
Another vital aspect to consider when choosing a gate valve is the material and pressure rating. The material of the valve should be compatible with the fluid it will be controlling to avoid corrosion or contamination. Common materials for a gate valve include stainless steel, carbon steel, and brass, each offering unique properties. Additionally, evaluating the pressure rating is crucial to ensure that the valve can withstand the operating pressure of the system. This consideration directly impacts the safety and performance of the gate valve, making it essential to make well-informed decisions based on the specific requirements of the application.
Maintenance and Troubleshooting
Maintenance troubleshooting is essential in ensuring the smooth operation of gate valves. It involves identifying and addressing issues with the valves to prevent unexpected breakdowns. By effectively troubleshooting and maintaining a gate valve, you can optimize it’s performance and extend their lifespan. Here, we will explore common issues and their solutions, as well as tips for ensuring the durability and longevity of gate valves.
Common Issues and Solutions
When it comes to gate valves, there are several common issues that may arise, such as leaks, corrosion, and valve sticking. Leaks can occur due to worn-out seals or gaskets, while corrosion may result from exposure to harsh chemicals or environmental factors. Valve sticking can be caused by debris or sediment buildup within the valve.
To address leaks, it is crucial to inspect and replace damaged seals or gaskets promptly. Corrosion can be mitigated through regular cleaning and protective coatings. Valve sticking can be resolved by performing regular maintenance to remove any debris and ensure smooth operation.
Lifespan and Durability Tips
The lifespan of a gate valve can be significantly extended through proper maintenance and care. Regular inspections, lubrication, and cleaning are key to ensuring the longevity of a gate valve. Implementing a proactive maintenance schedule and adhering to manufacturer guidelines for service intervals can help prevent potential issues and prolong the durability of a gate valve.
Additionally, considering the operating conditions and environment in which the gate valves are installed is crucial. Utilizing corrosion-resistant materials and protective coatings, where applicable, can further enhance the durability of gate valves, especially in harsh industrial settings.
By being proactive in addressing common issues and adhering to preventive maintenance practices, maintenance professionals can effectively optimize the performance and lifespan of a gate valve, ultimately minimizing downtime and optimizing operational efficiency.
Conclusion
In conclusion, a gate valve is a pivotal control valve that allows or stops the flow of media. It offers a straight-through unobstructed passageway, minimizing pressure loss. While gate valves are slower than quarter-turn valves and should only be fully open or closed, their unobstructed bore allows for pig’s passage in cleaning pipe procedures. This makes them a cost-effective option for infrequent use. Gate valves are commonly referred to as sluice gate valves and are crucial in various industrial applications.