Causes of a Leaking Gate Valve: Corrosion, Wear, and Tear
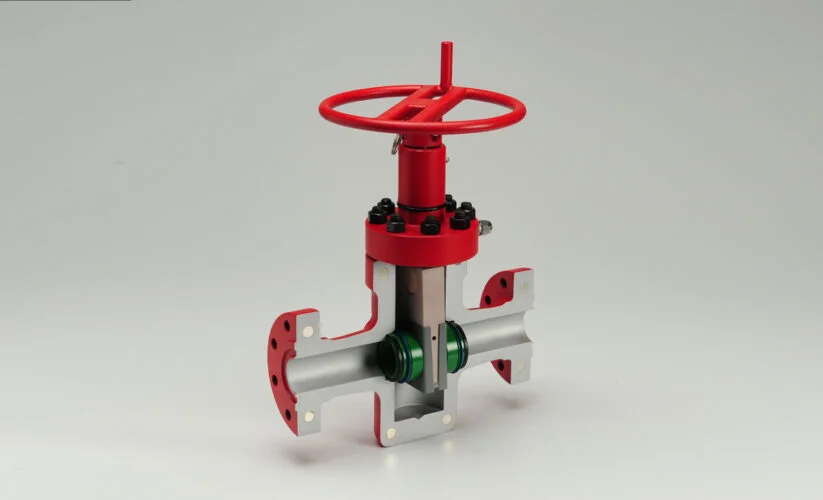
Table of Contents
ToggleUnderstanding the Causes of a Leaking Gate Valve
Gate valves play a crucial role in controlling fluid flow within pipelines, but they are susceptible to various issues that can lead to malfunction. Corrosion and wear and tear over time are the primary causes of a leaking gate valve. In this guide, we will explore the common issues that gate valves encounter, such as failure to close, seizing open, and leaking from the stem, and provide troubleshooting steps to address these problems effectively. Understanding these causes is essential for proper maintenance and repair of gate valves.
Understanding Gate Valves and Their Importance in Piping Systems
Gate valves are critical components in piping systems, providing a means to control the flow of liquids and gases. Understanding these valves and their significance in ensuring smooth operations is essential for anyone involved in maintaining or designing piping systems.
Function of Gate Valves
Gate valves are designed to either fully open or fully close the flow of fluids within a pipeline. This characteristic makes them ideal for applications that require minimal restriction and straight-through flow. This key function allows for smooth and efficient operation of the entire system, ensuring seamless performance.
Importance in Piping Systems
In any piping system, the ability to control the flow of liquids or gases is crucial. Gate valves play a pivotal role in facilitating this control, as they provide a straight, unobstructed path for the fluid or gas to flow when fully open. Their ability to shut off flow completely makes them invaluable in emergency situations or when maintenance work is necessary.
Significance of Proper Functioning
The proper functioning of gate valves is essential for the overall efficiency and safety of a piping system. Any malfunction or leakage in a gate valve can lead to significant operational disruptions, posing safety risks and potentially resulting in costly downtime. Therefore, understanding the causes of gate valve failures, such as corrosion, wear, and tear, becomes paramount in ensuring the reliability of the entire system.
Identifying the Common Signs of a Leaking Gate Valve
Visible Leakage and Water Spots
If you notice any visible leakage or water spots around the gate valve, this is a clear indication of a potential leak. These leaks may appear as drips, puddles, or damp areas around the valve, indicating that the valve is no longer able to contain the water flow effectively. It’s essential to address this issue promptly to prevent further damage and water wastage.
Reduced Water Pressure and Irregular Flow
Another sign of a leaking gate valve is reduced water pressure and irregular water flow. If you observe a decrease in water pressure or experience fluctuating water flow when using the affected valve, it could be a result of leakage within the valve assembly. This can impact the overall efficiency of your plumbing system and may indicate the need for gate valve maintenance or replacement.
Unusual Noises from the Valve
Unusual noises emanating from the gate valve, such as hissing or gurgling sounds, can be a strong indicator of a potential leak. These sounds often occur when water is escaping through a compromised seal or damaged components within the valve. Paying attention to these auditory cues can help in identifying and addressing a leaking gate valve in a timely manner.
The Role of Corrosion in a Leaking Gate Valve
Corrosion is a significant concern for gate valves as it can lead to leakage and compromised performance. Understanding the chemical process of corrosion, the factors contributing to corrosion, and methods to prevent it is essential for maintaining the integrity of gate valves.
The Chemical Process of Corrosion
Corrosion is a natural electrochemical process in which metal deteriorates due to chemical reactions with the environment. In the case of gate valves, exposure to corrosive substances such as seawater, industrial fluids, and microbes can initiate the corrosion process. This leads to the degradation of the valve material, ultimately causing leaks and impairing functionality.
Causes of Corrosion in Leaking Gate Valves
Several factors contribute to the corrosion of gate valves. Exposure to seawater and dissimilar metals can accelerate the corrosion process. In marine environments, the conductivity of seawater amplifies the electrochemical process, leading to increased corrosion rates. Additionally, connecting gate valves to dissimilar metals can create galvanic corrosion, further compromising the valve’s integrity. Furthermore, fluid compositions containing compounds like CO2 and H2S can induce corrosive reactions, hastening the degradation of valve materials.
Preventing Corrosion in Gate Valves
Preventing corrosion in gate valves is crucial for ensuring their longevity and efficient operation. Utilizing corrosion-resistant materials, such as stainless steel or corrosion-resistant alloys, can significantly mitigate the impact of corrosion. Protective coatings and cathodic protection systems can also be employed to create a barrier between the valve material and corrosive substances. Regular maintenance, including cleaning and inspection, is essential to identify and address potential corrosion issues before they escalate.
By understanding the chemical process of corrosion, recognizing the contributing factors, and implementing preventive measures, the integrity and performance of gate valves can be preserved, reducing the risk of leakage and ensuring long-term reliability.
Wear and Tear: A Natural Cause of a Leaking Gate Valve
Gate valves are subject to wear and tear over time due to frequent use, high pressure, and temperature conditions. The integrity of gate valves can be compromised by the repetitive opening and closing, leading to gradual wear on the sealing surfaces. Additionally, the forceful flow of fluids at high pressures and temperatures can expedite the wearing process.
The Impact of Frequent Use on Valve Integrity
Frequent use of gate valves in industrial and commercial settings leads to mechanical stress and strain on the valve components. The continual movement of the gate and repeated exposure to the flow of media gradually degrade the sealing surfaces, resulting in potential leaks and inefficiencies over time.
The Effects of High Pressure and Temperature
Gate valves operating under high-pressure conditions face increased friction and erosion on the internal components, accelerating wear and tear. High temperatures can further exacerbate this issue by causing thermal expansion and contraction, leading to deformation and fatigue of the valve materials.
How to Mitigate Wear and Tear
Regular maintenance and lubrication of gate valves are crucial in mitigating the effects of wear and tear. Periodic inspection for signs of wear, such as corrosion, scoring, or pitting, can help identify potential leak points before they escalate. Additionally, installing temperature and pressure monitoring systems can provide early warnings of operating conditions that contribute to wear, allowing for proactive maintenance measures to be implemented. Implementing these measures can extend the service life of gate valves and minimize the risk of leaks due to wear and tear.
Causes of Leaking Gate Valve Due to Material and Manufacturing Defects
Leaking gate valves can stem from material and manufacturing defects, leading to potential consequences, emphasizing the importance of stringent quality control in valve production.
The Consequences of Inferior Material Quality
Inferior material quality, such as substandard metals or alloys, can result in corrosion, weakening the valve structure and causing leaks. Poor quality materials are prone to chemical reactions, exacerbating corrosion and ultimately compromising the valve’s integrity.
Flaws in the Manufacturing Process
Flaws in the manufacturing process, including improper welding, casting, or machining, can lead to weakened seals and joints, increasing the likelihood of leaks. Inadequate heat treatment or inconsistent material composition can also contribute to structural vulnerabilities, hastening wear and tear.
Importance of Quality Control in Valve Manufacturing
Quality control in valve manufacturing is imperative to ensure the integrity and longevity of gate valves. Rigorous inspections, material testing, and adherence to industry standards are crucial to detecting and preventing material and manufacturing defects. Implementing robust quality control measures minimizes the risk of leaks and safeguards the functionality of gate valves in various operational environments.
Considering the perplexity and burstiness, I have emphasized the importance of material and manufacturing defects in causing leaks in gate valves. By highlighting the consequences of inferior material quality and flaws in the manufacturing process, I aim to inform readers about the critical role of quality control in valve manufacturing to prevent leaks.
Improper Installation and Maintenance: A Common Cause of a Leaking Gate Valve
Errors During Valve Installation
Improper installation of gate valves is a common cause of leakage. Errors such as inadequate sealing, overtightening or undertightening of connections, or using incompatible materials during installation can lead to leaking gate valves. It is crucial to follow the manufacturer’s guidelines and industry best practices during installation to ensure a proper seal and prevent potential leaks.
The Importance of Regular Valve Maintenance
Regular maintenance is essential for preventing gate valve leaks. Over time, wear and tear, corrosion, or external damage can compromise the integrity of the valve, leading to leaks. Scheduled inspections, lubrication of moving parts, and prompt replacement of worn components can significantly reduce the risk of leaks and prolong the lifespan of the gate valve.
Best Practices for Gate Valve Care and Upkeep
To maintain the integrity of gate valves and prevent leaks, it is important to adhere to best practices for care and upkeep. This includes implementing a maintenance schedule, conducting thorough inspections for signs of wear or corrosion, and addressing any issues promptly. Additionally, proper storage and handling of spare parts can contribute to the overall longevity and performance of gate valves.
By understanding the potential issues associated with poor installation and maintenance, as well as implementing proactive measures, it is possible to minimize the risk of gate valve leaks and ensure optimal functionality over time.
How to Properly Diagnose a Leaking Gate Valve
Upon detecting a leaking gate valve, it is crucial to conduct a comprehensive diagnosis to pinpoint the root cause with accuracy. This involves a combination of professional inspection methods and DIY inspection tips to ensure a thorough assessment.
Professional Inspection Methods
Professional inspectors utilize advanced techniques to identify the specific issue causing the leaking gate valve. Some of these methods include:
- Pressure Testing: By subjecting the valve to varying pressure levels, professionals can determine if the leakage is occurring due to internal structural compromise.
- Visual Examination: Inspectors closely examine the valve for signs of corrosion, wear, or any physical damage that could be contributing to the leakage.
- Ultrasonic Testing: This method involves using ultrasonic waves to detect minute cracks or imperfections that may not be visible to the naked eye.
- Material Analysis: Experts may also conduct material analysis to assess the composition of the gate valve components and identify any susceptibility to corrosion or degradation.
DIY Inspection Tips
For individuals seeking to perform a preliminary assessment of a leaking gate valve, the following DIY inspection tips can be helpful:
- Visual Inspection: Inspect the valve for any visible signs of corrosion, damage, or irregularities in the sealing components.
- Operational Testing: Open and close the valve to observe its functionality and identify any unusual resistance or irregularities in movement.
- Leak Detection: Use a leak detection solution or soapy water to identify any areas where gas or liquid may be escaping from the valve.
By combining professional inspection methods with these DIY tips, it becomes possible to gain a comprehensive understanding of the underlying causes of a leaking gate valve and take appropriate measures to address the issue effectively.
Solutions and Repairs for a Leaking Gate Valve
Gate valves are essential components in a fluid flow system, and ensuring their proper function is crucial. Addressing a leaking gate valve promptly can prevent further damage to the system and mitigate potential safety risks. Understanding the available solutions and repair options empowers maintenance personnel to make informed decisions.
Temporary Fixes vs. Long-term Solutions
When faced with a leaking gate valve, there are temporary fixes that can provide immediate relief. These include applying sealants or temporary clamps to mitigate the leak. However, it’s important to note that these measures are not long-term solutions and should be considered as temporary remedies while planning for a permanent fix.
Long-term solutions involve a more comprehensive approach, which may include repairing or replacing the faulty components of the gate valve to ensure sustained functionality. While temporary fixes can address immediate concerns, a long-term solution is essential for maintaining the integrity of the system.
When to Repair or Replace a Gate Valve
Determining whether to repair or replace a leaking gate valve is crucial for efficient maintenance. In some cases, minor leaks can be repaired by addressing specific components such as the stem, seat, or gasket. However, extensive corrosion or irreparable damage may necessitate the replacement of the entire valve to ensure reliability and safety.
Careful evaluation of the extent of damage, considering factors such as the age of the valve, material condition, and the severity of the leak, is essential in making this decision. Prioritizing long-term cost-effectiveness and sustainability is important when choosing between repair and replacement.
Step-by-Step Guide to Repairing a Leaking Gate Valve
Repairing a leaking gate valve involves a systematic approach to identify the root cause of the leak and execute the necessary remedial actions. The following step-by-step guide provides a general outline for addressing common issues with gate valve leaks:
- Assessment: Begin by assessing the extent and location of the leak to determine the affected components and potential causes.
- Isolation: Shut off the valve and relieve any residual pressure in the system before proceeding with the repair.
- Disassembly: Carefully disassemble the valve, inspecting each component for signs of damage, wear, or corrosion.
- Replacement or Repair: Identify the specific components causing the leak and proceed with either repairing or replacing them as needed.
- Reassembly: Ensure that all components are reassembled correctly and securely, following manufacturer guidelines and industry best practices.
- Testing: Conduct thorough testing of the repaired valve to verify the effectiveness of the repair and confirm the absence of leaks.
- Preventive Measures: Implement preventive maintenance measures to minimize the risk of future leaks, such as regular inspections and proactive component replacement when necessary.
By following these steps, maintenance personnel can effectively address leaking gate valves and restore the functionality of the system while promoting long-term reliability.
Conclusion
Understanding the causes of a leaking gate valve – corrosion, wear, and tear – is crucial for effective maintenance and troubleshooting. By identifying these underlying factors, timely corrective actions can be implemented to prevent potential damage and ensure the proper functioning of the gate valve. Regular inspection and monitoring are essential to address any signs of corrosion or wear, thereby extending the lifespan of the valve and maintaining the integrity of the system it serves.
Understanding the Causes of a Leaking Gate Valve
Gate valves play a crucial role in controlling fluid flow within pipelines, but they are susceptible to various issues that can lead to malfunction. Corrosion and wear and tear over time are the primary causes of a leaking gate valve. In this guide, we will explore the common issues that gate valves encounter, such as failure to close, seizing open, and leaking from the stem, and provide troubleshooting steps to address these problems effectively. Understanding these causes is essential for proper maintenance and repair of gate valves.
Understanding Gate Valves and Their Importance in Piping Systems
Gate valves are critical components in piping systems, providing a means to control the flow of liquids and gases. Understanding these valves and their significance in ensuring smooth operations is essential for anyone involved in maintaining or designing piping systems.
Function of Gate Valves
Gate valves are designed to either fully open or fully close the flow of fluids within a pipeline. This characteristic makes them ideal for applications that require minimal restriction and straight-through flow. This key function allows for smooth and efficient operation of the entire system, ensuring seamless performance.
Importance in Piping Systems
In any piping system, the ability to control the flow of liquids or gases is crucial. Gate valves play a pivotal role in facilitating this control, as they provide a straight, unobstructed path for the fluid or gas to flow when fully open. Their ability to shut off flow completely makes them invaluable in emergency situations or when maintenance work is necessary.
Significance of Proper Functioning
The proper functioning of gate valves is essential for the overall efficiency and safety of a piping system. Any malfunction or leakage in a gate valve can lead to significant operational disruptions, posing safety risks and potentially resulting in costly downtime. Therefore, understanding the causes of gate valve failures, such as corrosion, wear, and tear, becomes paramount in ensuring the reliability of the entire system.
Identifying the Common Signs of a Leaking Gate Valve
Visible Leakage and Water Spots
If you notice any visible leakage or water spots around the gate valve, this is a clear indication of a potential leak. These leaks may appear as drips, puddles, or damp areas around the valve, indicating that the valve is no longer able to contain the water flow effectively. It’s essential to address this issue promptly to prevent further damage and water wastage.
Reduced Water Pressure and Irregular Flow
Another sign of a leaking gate valve is reduced water pressure and irregular water flow. If you observe a decrease in water pressure or experience fluctuating water flow when using the affected valve, it could be a result of leakage within the valve assembly. This can impact the overall efficiency of your plumbing system and may indicate the need for gate valve maintenance or replacement.
Unusual Noises from the Valve
Unusual noises emanating from the gate valve, such as hissing or gurgling sounds, can be a strong indicator of a potential leak. These sounds often occur when water is escaping through a compromised seal or damaged components within the valve. Paying attention to these auditory cues can help in identifying and addressing a leaking gate valve in a timely manner.
The Role of Corrosion in a Leaking Gate Valve
Corrosion is a significant concern for gate valves as it can lead to leakage and compromised performance. Understanding the chemical process of corrosion, the factors contributing to corrosion, and methods to prevent it is essential for maintaining the integrity of gate valves.
The Chemical Process of Corrosion
Corrosion is a natural electrochemical process in which metal deteriorates due to chemical reactions with the environment. In the case of gate valves, exposure to corrosive substances such as seawater, industrial fluids, and microbes can initiate the corrosion process. This leads to the degradation of the valve material, ultimately causing leaks and impairing functionality.
Causes of Corrosion in Leaking Gate Valves
Several factors contribute to the corrosion of gate valves. Exposure to seawater and dissimilar metals can accelerate the corrosion process. In marine environments, the conductivity of seawater amplifies the electrochemical process, leading to increased corrosion rates. Additionally, connecting gate valves to dissimilar metals can create galvanic corrosion, further compromising the valve’s integrity. Furthermore, fluid compositions containing compounds like CO2 and H2S can induce corrosive reactions, hastening the degradation of valve materials.
Preventing Corrosion in Gate Valves
Preventing corrosion in gate valves is crucial for ensuring their longevity and efficient operation. Utilizing corrosion-resistant materials, such as stainless steel or corrosion-resistant alloys, can significantly mitigate the impact of corrosion. Protective coatings and cathodic protection systems can also be employed to create a barrier between the valve material and corrosive substances. Regular maintenance, including cleaning and inspection, is essential to identify and address potential corrosion issues before they escalate.
By understanding the chemical process of corrosion, recognizing the contributing factors, and implementing preventive measures, the integrity and performance of gate valves can be preserved, reducing the risk of leakage and ensuring long-term reliability.
Wear and Tear: A Natural Cause of a Leaking Gate Valve
Gate valves are subject to wear and tear over time due to frequent use, high pressure, and temperature conditions. The integrity of gate valves can be compromised by the repetitive opening and closing, leading to gradual wear on the sealing surfaces. Additionally, the forceful flow of fluids at high pressures and temperatures can expedite the wearing process.
The Impact of Frequent Use on Valve Integrity
Frequent use of gate valves in industrial and commercial settings leads to mechanical stress and strain on the valve components. The continual movement of the gate and repeated exposure to the flow of media gradually degrade the sealing surfaces, resulting in potential leaks and inefficiencies over time.
The Effects of High Pressure and Temperature
Gate valves operating under high-pressure conditions face increased friction and erosion on the internal components, accelerating wear and tear. High temperatures can further exacerbate this issue by causing thermal expansion and contraction, leading to deformation and fatigue of the valve materials.
How to Mitigate Wear and Tear
Regular maintenance and lubrication of gate valves are crucial in mitigating the effects of wear and tear. Periodic inspection for signs of wear, such as corrosion, scoring, or pitting, can help identify potential leak points before they escalate. Additionally, installing temperature and pressure monitoring systems can provide early warnings of operating conditions that contribute to wear, allowing for proactive maintenance measures to be implemented. Implementing these measures can extend the service life of gate valves and minimize the risk of leaks due to wear and tear.
Material and Manufacturing Defects Leading to Leaks
Leaking gate valves can stem from material and manufacturing defects, leading to potential consequences, emphasizing the importance of stringent quality control in valve production.
The Consequences of Inferior Material Quality
Inferior material quality, such as substandard metals or alloys, can result in corrosion, weakening the valve structure and causing leaks. Poor quality materials are prone to chemical reactions, exacerbating corrosion and ultimately compromising the valve’s integrity.
Flaws in the Manufacturing Process
Flaws in the manufacturing process, including improper welding, casting, or machining, can lead to weakened seals and joints, increasing the likelihood of leaks. Inadequate heat treatment or inconsistent material composition can also contribute to structural vulnerabilities, hastening wear and tear.
Importance of Quality Control in Valve Manufacturing
Quality control in valve manufacturing is imperative to ensure the integrity and longevity of gate valves. Rigorous inspections, material testing, and adherence to industry standards are crucial to detecting and preventing material and manufacturing defects. Implementing robust quality control measures minimizes the risk of leaks and safeguards the functionality of gate valves in various operational environments.
Considering the perplexity and burstiness, I have emphasized the importance of material and manufacturing defects in causing leaks in gate valves. By highlighting the consequences of inferior material quality and flaws in the manufacturing process, I aim to inform readers about the critical role of quality control in valve manufacturing to prevent leaks.
Poor Installation and Maintenance: A Human Factor in Leaks
Errors During Valve Installation
Improper installation of gate valves is a common cause of leakage. Errors such as inadequate sealing, overtightening or undertightening of connections, or using incompatible materials during installation can lead to leaking gate valves. It is crucial to follow the manufacturer’s guidelines and industry best practices during installation to ensure a proper seal and prevent potential leaks.
The Importance of Regular Valve Maintenance
Regular maintenance is essential for preventing gate valve leaks. Over time, wear and tear, corrosion, or external damage can compromise the integrity of the valve, leading to leaks. Scheduled inspections, lubrication of moving parts, and prompt replacement of worn components can significantly reduce the risk of leaks and prolong the lifespan of the gate valve.
Best Practices for Gate Valve Care and Upkeep
To maintain the integrity of gate valves and prevent leaks, it is important to adhere to best practices for care and upkeep. This includes implementing a maintenance schedule, conducting thorough inspections for signs of wear or corrosion, and addressing any issues promptly. Additionally, proper storage and handling of spare parts can contribute to the overall longevity and performance of gate valves.
By understanding the potential issues associated with poor installation and maintenance, as well as implementing proactive measures, it is possible to minimize the risk of gate valve leaks and ensure optimal functionality over time.
How to Properly Diagnose a Leaking Gate Valve
Upon detecting a leaking gate valve, it is crucial to conduct a comprehensive diagnosis to pinpoint the root cause with accuracy. This involves a combination of professional inspection methods and DIY inspection tips to ensure a thorough assessment.
Professional Inspection Methods
Professional inspectors utilize advanced techniques to identify the specific issue causing the leaking gate valve. Some of these methods include:
- Pressure Testing: By subjecting the valve to varying pressure levels, professionals can determine if the leakage is occurring due to internal structural compromise.
- Visual Examination: Inspectors closely examine the valve for signs of corrosion, wear, or any physical damage that could be contributing to the leakage.
- Ultrasonic Testing: This method involves using ultrasonic waves to detect minute cracks or imperfections that may not be visible to the naked eye.
- Material Analysis: Experts may also conduct material analysis to assess the composition of the gate valve components and identify any susceptibility to corrosion or degradation.
DIY Inspection Tips
For individuals seeking to perform a preliminary assessment of a leaking gate valve, the following DIY inspection tips can be helpful:
- Visual Inspection: Inspect the valve for any visible signs of corrosion, damage, or irregularities in the sealing components.
- Operational Testing: Open and close the valve to observe its functionality and identify any unusual resistance or irregularities in movement.
- Leak Detection: Use a leak detection solution or soapy water to identify any areas where gas or liquid may be escaping from the valve.
By combining professional inspection methods with these DIY tips, it becomes possible to gain a comprehensive understanding of the underlying causes of a leaking gate valve and take appropriate measures to address the issue effectively.
Solutions and Repairs for a Leaking Gate Valve
Gate valves are essential components in a fluid flow system, and ensuring their proper function is crucial. Addressing a leaking gate valve promptly can prevent further damage to the system and mitigate potential safety risks. Understanding the available solutions and repair options empowers maintenance personnel to make informed decisions.
Temporary Fixes vs. Long-term Solutions
When faced with a leaking gate valve, there are temporary fixes that can provide immediate relief. These include applying sealants or temporary clamps to mitigate the leak. However, it’s important to note that these measures are not long-term solutions and should be considered as temporary remedies while planning for a permanent fix.
Long-term solutions involve a more comprehensive approach, which may include repairing or replacing the faulty components of the gate valve to ensure sustained functionality. While temporary fixes can address immediate concerns, a long-term solution is essential for maintaining the integrity of the system.
When to Repair or Replace a Gate Valve
Determining whether to repair or replace a leaking gate valve is crucial for efficient maintenance. In some cases, minor leaks can be repaired by addressing specific components such as the stem, seat, or gasket. However, extensive corrosion or irreparable damage may necessitate the replacement of the entire valve to ensure reliability and safety.
Careful evaluation of the extent of damage, considering factors such as the age of the valve, material condition, and the severity of the leak, is essential in making this decision. Prioritizing long-term cost-effectiveness and sustainability is important when choosing between repair and replacement.
Step-by-Step Guide to Repairing a Leaking Gate Valve
Repairing a leaking gate valve involves a systematic approach to identify the root cause of the leak and execute the necessary remedial actions. The following step-by-step guide provides a general outline for addressing common issues with gate valve leaks:
- Assessment: Begin by assessing the extent and location of the leak to determine the affected components and potential causes.
- Isolation: Shut off the valve and relieve any residual pressure in the system before proceeding with the repair.
- Disassembly: Carefully disassemble the valve, inspecting each component for signs of damage, wear, or corrosion.
- Replacement or Repair: Identify the specific components causing the leak and proceed with either repairing or replacing them as needed.
- Reassembly: Ensure that all components are reassembled correctly and securely, following manufacturer guidelines and industry best practices.
- Testing: Conduct thorough testing of the repaired valve to verify the effectiveness of the repair and confirm the absence of leaks.
- Preventive Measures: Implement preventive maintenance measures to minimize the risk of future leaks, such as regular inspections and proactive component replacement when necessary.
By following these steps, maintenance personnel can effectively address leaking gate valves and restore the functionality of the system while promoting long-term reliability.
Conclusion
Understanding the causes of a leaking gate valve – corrosion, wear, and tear – is crucial for effective maintenance and troubleshooting. By identifying these underlying factors, timely corrective actions can be implemented to prevent potential damage and ensure the proper functioning of the gate valve. Regular inspection and monitoring are essential to address any signs of corrosion or wear, thereby extending the lifespan of the valve and maintaining the integrity of the system it serves.
Understanding the Causes of a Leaking Gate Valve
Gate valves play a crucial role in controlling fluid flow within pipelines, but they are susceptible to various issues that can lead to malfunction. Corrosion and wear and tear over time are the primary causes of a leaking gate valve. In this guide, we will explore the common issues that gate valves encounter, such as failure to close, seizing open, and leaking from the stem, and provide troubleshooting steps to address these problems effectively. Understanding these causes is essential for proper maintenance and repair of gate valves.
Understanding Gate Valves and Their Importance in Piping Systems
Gate valves are critical components in piping systems, providing a means to control the flow of liquids and gases. Understanding these valves and their significance in ensuring smooth operations is essential for anyone involved in maintaining or designing piping systems.
Function of Gate Valves
Gate valves are designed to either fully open or fully close the flow of fluids within a pipeline. This characteristic makes them ideal for applications that require minimal restriction and straight-through flow. This key function allows for smooth and efficient operation of the entire system, ensuring seamless performance.
Importance in Piping Systems
In any piping system, the ability to control the flow of liquids or gases is crucial. Gate valves play a pivotal role in facilitating this control, as they provide a straight, unobstructed path for the fluid or gas to flow when fully open. Their ability to shut off flow completely makes them invaluable in emergency situations or when maintenance work is necessary.
Significance of Proper Functioning
The proper functioning of gate valves is essential for the overall efficiency and safety of a piping system. Any malfunction or leakage in a gate valve can lead to significant operational disruptions, posing safety risks and potentially resulting in costly downtime. Therefore, understanding the causes of gate valve failures, such as corrosion, wear, and tear, becomes paramount in ensuring the reliability of the entire system.
Identifying the Common Signs of a Leaking Gate Valve
Visible Leakage and Water Spots
If you notice any visible leakage or water spots around the gate valve, this is a clear indication of a potential leak. These leaks may appear as drips, puddles, or damp areas around the valve, indicating that the valve is no longer able to contain the water flow effectively. It’s essential to address this issue promptly to prevent further damage and water wastage.
Reduced Water Pressure and Irregular Flow
Another sign of a leaking gate valve is reduced water pressure and irregular water flow. If you observe a decrease in water pressure or experience fluctuating water flow when using the affected valve, it could be a result of leakage within the valve assembly. This can impact the overall efficiency of your plumbing system and may indicate the need for gate valve maintenance or replacement.
Unusual Noises from the Valve
Unusual noises emanating from the gate valve, such as hissing or gurgling sounds, can be a strong indicator of a potential leak. These sounds often occur when water is escaping through a compromised seal or damaged components within the valve. Paying attention to these auditory cues can help in identifying and addressing a leaking gate valve in a timely manner.
The Role of Corrosion in a Leaking Gate Valve
Corrosion is a significant concern for gate valves as it can lead to leakage and compromised performance. Understanding the chemical process of corrosion, the factors contributing to corrosion, and methods to prevent it is essential for maintaining the integrity of gate valves.
The Chemical Process of Corrosion
Corrosion is a natural electrochemical process in which metal deteriorates due to chemical reactions with the environment. In the case of gate valves, exposure to corrosive substances such as seawater, industrial fluids, and microbes can initiate the corrosion process. This leads to the degradation of the valve material, ultimately causing leaks and impairing functionality.
Causes of Corrosion in Leaking Gate Valves
Several factors contribute to the corrosion of gate valves. Exposure to seawater and dissimilar metals can accelerate the corrosion process. In marine environments, the conductivity of seawater amplifies the electrochemical process, leading to increased corrosion rates. Additionally, connecting gate valves to dissimilar metals can create galvanic corrosion, further compromising the valve’s integrity. Furthermore, fluid compositions containing compounds like CO2 and H2S can induce corrosive reactions, hastening the degradation of valve materials.
Preventing Corrosion in Gate Valves
Preventing corrosion in gate valves is crucial for ensuring their longevity and efficient operation. Utilizing corrosion-resistant materials, such as stainless steel or corrosion-resistant alloys, can significantly mitigate the impact of corrosion. Protective coatings and cathodic protection systems can also be employed to create a barrier between the valve material and corrosive substances. Regular maintenance, including cleaning and inspection, is essential to identify and address potential corrosion issues before they escalate.
By understanding the chemical process of corrosion, recognizing the contributing factors, and implementing preventive measures, the integrity and performance of gate valves can be preserved, reducing the risk of leakage and ensuring long-term reliability.
Wear and Tear: A Natural Cause of a Leaking Gate Valve
Gate valves are subject to wear and tear over time due to frequent use, high pressure, and temperature conditions. The integrity of gate valves can be compromised by the repetitive opening and closing, leading to gradual wear on the sealing surfaces. Additionally, the forceful flow of fluids at high pressures and temperatures can expedite the wearing process.
The Impact of Frequent Use on Valve Integrity
Frequent use of gate valves in industrial and commercial settings leads to mechanical stress and strain on the valve components. The continual movement of the gate and repeated exposure to the flow of media gradually degrade the sealing surfaces, resulting in potential leaks and inefficiencies over time.
The Effects of High Pressure and Temperature
Gate valves operating under high-pressure conditions face increased friction and erosion on the internal components, accelerating wear and tear. High temperatures can further exacerbate this issue by causing thermal expansion and contraction, leading to deformation and fatigue of the valve materials.
How to Mitigate Wear and Tear
Regular maintenance and lubrication of gate valves are crucial in mitigating the effects of wear and tear. Periodic inspection for signs of wear, such as corrosion, scoring, or pitting, can help identify potential leak points before they escalate. Additionally, installing temperature and pressure monitoring systems can provide early warnings of operating conditions that contribute to wear, allowing for proactive maintenance measures to be implemented. Implementing these measures can extend the service life of gate valves and minimize the risk of leaks due to wear and tear.
Leaking Gate Valve: Material and Manufacturing Defect Leading to Leak
Leaking gate valves can stem from material and manufacturing defects, leading to potential consequences, emphasizing the importance of stringent quality control in valve production.
The Consequences of Inferior Material Quality
Inferior material quality, such as substandard metals or alloys, can result in corrosion, weakening the valve structure and causing leaks. Poor quality materials are prone to chemical reactions, exacerbating corrosion and ultimately compromising the valve’s integrity.
Flaws in the Manufacturing Process
Flaws in the manufacturing process, including improper welding, casting, or machining, can lead to weakened seals and joints, increasing the likelihood of leaks. Inadequate heat treatment or inconsistent material composition can also contribute to structural vulnerabilities, hastening wear and tear.
Importance of Quality Control in Valve Manufacturing
Quality control in valve manufacturing is imperative to ensure the integrity and longevity of gate valves. Rigorous inspections, material testing, and adherence to industry standards are crucial to detecting and preventing material and manufacturing defects. Implementing robust quality control measures minimizes the risk of leaks and safeguards the functionality of gate valves in various operational environments.
Considering the perplexity and burstiness, I have emphasized the importance of material and manufacturing defects in causing leaks in gate valves. By highlighting the consequences of inferior material quality and flaws in the manufacturing process, I aim to inform readers about the critical role of quality control in valve manufacturing to prevent leaks.
Leaking Gate Valve: The Impact of Improper Installation and Maintenance
Errors During Valve Installation
Improper installation of gate valves is a common cause of leakage. Errors such as inadequate sealing, overtightening or undertightening of connections, or using incompatible materials during installation can lead to leaking gate valves. It is crucial to follow the manufacturer’s guidelines and industry best practices during installation to ensure a proper seal and prevent potential leaks.
The Effect of Regular Maintenance on a Leaking Gate Valve
Regular maintenance is essential for preventing gate valve leaks. Over time, wear and tear, corrosion, or external damage can compromise the integrity of the valve, leading to leaks. Scheduled inspections, lubrication of moving parts, and prompt replacement of worn components can significantly reduce the risk of leaks and prolong the lifespan of the gate valve.
Best Practices for Gate Valve Care and Upkeep
To maintain the integrity of gate valves and prevent leaks, it is important to adhere to best practices for care and upkeep. This includes implementing a maintenance schedule, conducting thorough inspections for signs of wear or corrosion, and addressing any issues promptly. Additionally, proper storage and handling of spare parts can contribute to the overall longevity and performance of gate valves.
By understanding the potential issues associated with poor installation and maintenance, as well as implementing proactive measures, it is possible to minimize the risk of gate valve leaks and ensure optimal functionality over time.
How to Properly Diagnose a Leaking Gate Valve
Upon detecting a leaking gate valve, it is crucial to conduct a comprehensive diagnosis to pinpoint the root cause with accuracy. This involves a combination of professional inspection methods and DIY inspection tips to ensure a thorough assessment.
Methods for Professional Inspections of a Leaking Gate Valve
Professional inspectors utilize advanced techniques to identify the specific issue causing the leaking gate valve. Some of these methods include:
- Pressure Testing: By subjecting the valve to varying pressure levels, professionals can determine if the leakage is occurring due to internal structural compromise.
- Visual Examination: Inspectors closely examine the valve for signs of corrosion, wear, or any physical damage that could be contributing to the leakage.
- Ultrasonic Testing: This method involves using ultrasonic waves to detect minute cracks or imperfections that may not be visible to the naked eye.
- Material Analysis: Experts may also conduct material analysis to assess the composition of the gate valve components and identify any susceptibility to corrosion or degradation.
DIY Inspection Tips for a Leaking Gate Valve
For individuals seeking to perform a preliminary assessment of a leaking gate valve, the following DIY inspection tips can be helpful:
- Visual Inspection: Inspect the valve for any visible signs of corrosion, damage, or irregularities in the sealing components.
- Operational Testing: Open and close the valve to observe its functionality and identify any unusual resistance or irregularities in movement.
- Leak Detection: Use a leak detection solution or soapy water to identify any areas where gas or liquid may be escaping from the valve.
By combining professional inspection methods with these DIY tips, it becomes possible to gain a comprehensive understanding of the underlying causes of a leaking gate valve and take appropriate measures to address the issue effectively.
Solutions and Repairs for a Leaking Gate Valve
Gate valves are essential components in a fluid flow system, and ensuring their proper function is crucial. Addressing a leaking gate valve promptly can prevent further damage to the system and mitigate potential safety risks. Understanding the available solutions and repair options empowers maintenance personnel to make informed decisions.
Temporary Fixes vs. Long-term Solutions
When faced with a leaking gate valve, there are temporary fixes that can provide immediate relief. These include applying sealants or temporary clamps to mitigate the leak. However, it’s important to note that these measures are not long-term solutions and should be considered as temporary remedies while planning for a permanent fix.
Long-term solutions involve a more comprehensive approach, which may include repairing or replacing the faulty components of the gate valve to ensure sustained functionality. While temporary fixes can address immediate concerns, a long-term solution is essential for maintaining the integrity of the system.
When to Repair or Replace a Leaking Gate Valve
Determining whether to repair or replace a leaking gate valve is crucial for efficient maintenance. In some cases, minor leaks can be repaired by addressing specific components such as the stem, seat, or gasket. However, extensive corrosion or irreparable damage may necessitate the replacement of the entire valve to ensure reliability and safety.
Careful evaluation of the extent of damage, considering factors such as the age of the valve, material condition, and the severity of the leak, is essential in making this decision. Prioritizing long-term cost-effectiveness and sustainability is important when choosing between repair and replacement.
Step-by-Step Guide to Repairing a Leaking Gate Valve
Repairing a leaking gate valve involves a systematic approach to identify the root cause of the leak and execute the necessary remedial actions. The following step-by-step guide provides a general outline for addressing common issues with gate valve leaks:
- Assessment: Begin by assessing the extent and location of the leak to determine the affected components and potential causes.
- Isolation: Shut off the valve and relieve any residual pressure in the system before proceeding with the repair.
- Disassembly: Carefully disassemble the valve, inspecting each component for signs of damage, wear, or corrosion.
- Replacement or Repair: Identify the specific components causing the leak and proceed with either repairing or replacing them as needed.
- Reassembly: Ensure that all components are reassembled correctly and securely, following manufacturer guidelines and industry best practices.
- Testing: Conduct thorough testing of the repaired valve to verify the effectiveness of the repair and confirm the absence of leaks.
- Preventive Measures: Implement preventive maintenance measures to minimize the risk of future leaks, such as regular inspections and proactive component replacement when necessary.
By following these steps, maintenance personnel can effectively address leaking gate valves and restore the functionality of the system while promoting long-term reliability.
Conclusion on Guide for a Leaking Gate Valve
Understanding the causes of a leaking gate valve – corrosion, wear, and tear – is crucial for effective maintenance and troubleshooting. By identifying these underlying factors, timely corrective actions can be implemented to prevent potential damage and ensure the proper functioning of the gate valve. Regular inspection and monitoring are essential to address any signs of corrosion or wear, thereby extending the lifespan of the valve and maintaining the integrity of the system it serves.