Deciphering Globe Valves: Grasping the Working Principles
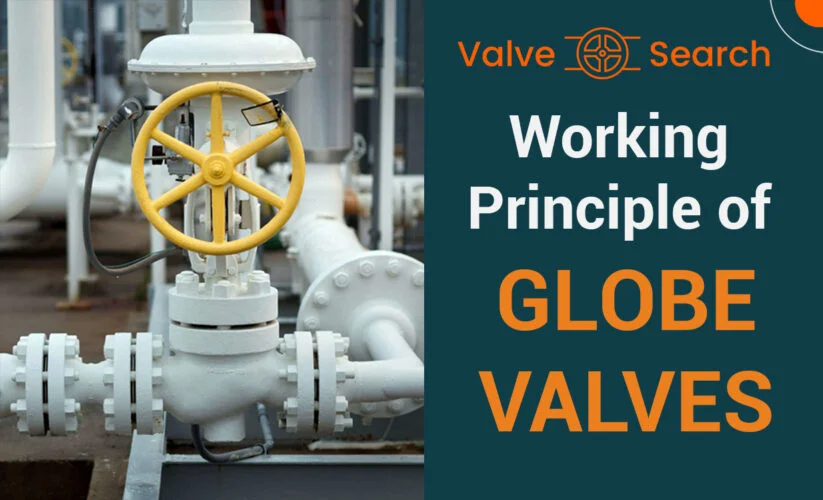
Table of Contents
ToggleMastering the Working Principles of Globe Valves: A Technical Guide for Engineers
The working principle of a globe valve is fundamental to understanding its functionality in various technical applications. Essentially, a globe valve operates by the movement of a disc that serves as the closure member. This movement, whether inwards or outwards, controls the flow of fluid or gas through the valve.
This valve is designed to start, stop, and regulate the flow, making it an essential component in fluid control systems. Comprising a movable disk and a stationary ring seat, the globe valve’s operation involves the positioning of the disk to modulate the flow according to system requirements.
Understanding the intricacies of how a globe valve functions is crucial for technical individuals involved in fluid control and pipeline systems. By delving into its working principle, one can gain valuable insights into the operational dynamics that underpin this vital component of engineering systems.
Understanding Globe Valve Working Principle
These valves are essential in regulating and controlling the flow of fluids in various industrial processes. Understanding the working principle of a globe valve is crucial for technical individuals to comprehend its operational dynamics and optimize its performance. This section will delve into the core concepts of the valve operation, mechanism of flow regulation, key components and their functions, types of valve actuators, and factors affecting the valve performance.
Basic Concept of Globe Valve Operation
The operation of a globe valve involves the movement of a disc or plug to modulate the flow of fluid through the valve. This movement is facilitated by the up-and-down motion of the valve stem, which raises or lowers the disc in relation to the stationary seat. When the disc is in the fully closed position, it obstructs the flow path, effectively stopping the fluid flow. As the stem is raised, the annular space around the disc increases, allowing for gradual flow regulation. The precise control over fluid flow makes the valves suitable for various applications, including throttling and isolation.
Mechanism of Flow Regulation
Globe valves regulate flow by using the linear motion of the disc to vary the flow passage’s size. By adjusting the position of the disc, the flow is either allowed to pass through the annular space or restricted by the disc’s contact with the seat. The versatility of this mechanism enables precise control over flow rates, making the valves well-suited for applications requiring accurate regulation of fluid flow.
Key Components and Their Functions
1. Body and Bonnet:
- The body houses the internal components of the globe valve, providing a passage for fluid flow. It is designed to withstand pressure and temperature variations, ensuring reliable performance in diverse operating conditions. The bonnet encloses the moving parts of the valve and facilitates access for maintenance and repairs.
2. Disc and Seat:
- The disc, also known as the plug, acts as the primary modulating element in the globe valve. It is designed to form a seal with the stationary seat to control the flow passage’s opening. The seat provides a stable sealing surface for the disc, ensuring tight shut-off and flow regulation.
Types of Globe Valve Actuators
Globe valve actuators are mechanisms responsible for initiating the movement of the valve disc or plug. Depending on the operational requirements and environmental conditions, different types of actuators are employed, including manual handwheels, pneumatic actuators, electric actuators, and hydraulic actuators. Each actuator type offers distinct advantages in terms of control, speed, and automation, catering to diverse industrial applications.
Factors Affecting Globe Valve Performance
1. Fluid Properties:
- The nature of the fluid being handled influences the choice of materials for the valve components to ensure compatibility and resistance to corrosion, erosion, and other detrimental effects.
2. Pressure and Temperature:
- Operating conditions such as pressure differentials and temperature variations impact the valve’s structural integrity and sealing capabilities, necessitating suitable design considerations for reliable performance.
3. Flow Characteristics:
- The flow profile and velocity within the pipeline affect the valve’s ability to regulate flow effectively, requiring proper sizing and selection to mitigate issues such as cavitation and excessive pressure drop.
The intricacies of globe valve operation and the interplay of its components contribute to its fundamental role in fluid flow control systems. By comprehending the working principles and functional attributes of them, technical professionals can make informed decisions regarding their utilization in diverse industrial processes.
Closing Mechanism of Globe Valve
Globe valves are known for their effective closing mechanism, ensuring tight shut-off to control the flow of fluids in a pipeline. The closing mechanism of the valve relies on several key elements, including pressure-dependent sealing, the role of the valve stem pressure, and the dynamics of the sealing surface.
Pressure-Dependent Sealing
The sealing properties of a globe valve are pressure-dependent, meaning that the valve’s ability to seal off the flow is directly influenced by the pressure acting on the valve components. When the valve is in the closed position, the pressure of the flowing fluid against the sealing surfaces creates a tight seal, preventing any leakage. This pressure-dependent sealing mechanism enables the valve to effectively control the flow of fluids, making it a reliable choice in various industrial applications where precise flow regulation is crucial.
Role of Valve Stem Pressure
The valve stem plays a critical role in the closing mechanism of a globe valve. As the handwheel or actuator is operated to close the valve, the force exerted on the valve stem transfers to the sealing disc, pressing it firmly against the valve seat. The valve stem pressure ensures that the sealing surfaces make full contact, creating a secure barrier that prevents any undesired fluid flow. This mechanism allows for precise control over the flow rate, making the globe valve a preferred choice in systems that demand accurate flow management.
Sealing Surface Dynamics
The dynamics of the sealing surfaces within a globe valve contribute to its efficient closing mechanism. The interaction between the valve disc and the valve seat is designed to minimize friction and wear, ensuring a durable and effective seal. The smooth movement of the disc as it engages with the seat enables the globe valve to withstand high-pressure environments while maintaining its sealing integrity. This dynamic interplay between the sealing surfaces enables the globe valve to consistently deliver reliable shut-off performance, making it an essential component in fluid control systems.
By understanding the intricacies of the closing mechanism of a globe valve, engineers and technicians can leverage this knowledge to optimize the performance of fluid handling systems, ensuring precision, reliability, and safety in various industrial operations.
What are the main engineering principles behind the functionality of globe valves?
The main engineering principles behind the functionality of globe valves lie in their design, which consists of a movable disk or plug that regulates the flow of fluid through the valve. This disk is connected to a stem, which is operated by a handwheel or actuator to move the disk up and down, thereby controlling the flow.
The valve body has a globular shape, hence the name “globe” valve, with an inlet and outlet on opposite sides, allowing for efficient directional changes in the flow. When the handwheel or actuator is turned to open the valve, the disk is raised, allowing the fluid to pass through the annular space between the disk and the stationary seat.
Conversely, when the valve is closed, the disk is lowered to shut off the flow. This design allows for precise flow control and throttling, making globe valves suitable for applications where accurate regulation of flow is required.
The key engineering principles at play in globe valves include the use of a linear motion to control the flow, the shape of the valve body to facilitate directional changes, and the precise alignment of the disk and seat to achieve tight shut-off when closed.
These principles underpin the reliable and efficient functionality of globe valves in various industrial and commercial settings.
Why is perpendicular motion important in globe valve operation?
Perpendicular motion is crucial in globe valve operation because it allows for precise control of the fluid flow. When the valve stem moves perpendicular to the direction of the fluid flow, it creates a direct and effective means of regulating flow rates and pressures. This motion enables the valve to be finely tuned, providing the ability to modulate the flow and shut off the fluid completely when necessary.
By moving perpendicular to the flow, the valve stem can accurately position the valve plug in relation to the seat, effectively controlling the flow area to achieve the desired flow rate. This level of control is essential in many industrial applications where precise regulation of fluids is critical for the operation and safety of the system.
Whether it is in process industries, power generation, or HVAC systems, the ability to precisely control fluid flow through perpendicular motion in globe valve operation is indispensable for optimal performance and efficiency.
How does the structure of a globe valve contribute to its operating principles?
The structure of a globe valve contributes to its operating principles in several key ways. First and foremost, the design of the valve includes a movable disk or plug that can be adjusted to regulate the flow of the fluid through the valve. This allows for precise control over the rate and volume of the flow, making the globe valve well-suited for applications where flow regulation is crucial. Additionally, the vertical orientation of the valve allows for an efficient and streamlined flow path, minimizing pressure drop and turbulence.
The linear motion of the disk or plug also provides a reliable shut-off mechanism, ensuring that the valve can effectively stop the flow when fully closed. Furthermore, the internal structure of the valve includes a seat that forms a tight seal with the disk or plug, preventing leakage and providing a high degree of shutoff integrity. Overall, the combination of these structural elements enables the globe valve to operate with precision, reliability, and effectiveness in controlling fluid flow in various industrial and commercial settings.
Applications and Considerations
Globe valves are extensively used in various industrial applications due to their efficient flow control capabilities and reliable performance. Understanding their operating conditions and maintenance requirements is crucial for ensuring optimal functionality.
Industrial Applications
Globe valves find widespread use in industries such as petrochemical, power generation, oil and gas, and water treatment. Their ability to control and regulate the flow of liquids, gases, and steam makes them an integral part of complex industrial processes. In the petrochemical industry, these valves are employed in systems requiring precise flow regulation, while in power generation plants, they are utilized for fluid and steam control. Additionally, their suitability for high-pressure and high-temperature applications makes them indispensable in the oil and gas sector. Furthermore, they play a vital role in water treatment facilities, where accurate flow management is essential for maintaining water quality and system efficiency.
Operating Conditions and Maintenance
Operating conditions significantly influence the performance and longevity of globe valves. Regular maintenance is essential to ensure their proper functioning and prevent potential issues. Proper lubrication of the valve stem and ensuring the integrity of the sealing surfaces are imperative for optimal performance. Additionally, monitoring operating conditions such as pressure differentials, temperature fluctuations, and fluid characteristics is essential for identifying potential issues and ensuring the longevity of the valves.
In industrial applications, globe valves are subjected to varying conditions, including high temperatures, corrosive environments, and high-pressure flows. As a result, selecting the appropriate materials for construction is crucial to ensure compatibility with the operating environment and to prevent premature wear or failure. Regular inspection and testing of these valves are vital for detecting wear, corrosion, and other potential issues that may affect their performance. Implementing a proactive maintenance schedule and adhering to recommended operating parameters are essential for maximizing the lifespan and efficiency of globe valves in industrial settings.
Enhancing Globe Valve Performance
As crucial components in industrial systems, globe valves play a vital role in regulating fluid flow. To optimize their performance, it is essential to focus on two key aspects: optimizing flow control and implementing preventative maintenance strategies.
Optimizing Flow Control
When it comes to enhancing the performance of globe valves, optimization of flow control is of utmost importance. By fine-tuning the flow control mechanisms, engineers and technicians can ensure the efficient operation of globe valves within a system.
To achieve optimal flow control, it is imperative to consider factors such as pressure differentials, fluid viscosity, and the specific application requirements. Implementing advanced flow control technologies and precision engineering can significantly improve the responsiveness and accuracy of the valves, enabling seamless regulation of flow within industrial processes.
Utilizing sophisticated flow measurement and control systems, including intelligent actuation mechanisms, can further enhance the precision and reliability of the valve operations. By integrating state-of-the-art control algorithms and feedback mechanisms, engineers can achieve superior fluid regulation, resulting in enhanced system performance and operational efficiency.
Preventative Maintenance Strategies
In addition to optimizing flow control, implementing effective preventative maintenance strategies is essential for maximizing the longevity and reliability of globe valves. Proactive maintenance measures can mitigate the risk of unexpected downtime and ensure continuous operational readiness.
Adopting a comprehensive maintenance schedule that includes regular inspections, lubrication, and performance monitoring is crucial for identifying potential issues before they escalate. This proactive approach allows maintenance teams to address minor wear and tear, mitigate corrosion, and preemptively replace critical components, thereby extending the service life of the valves.
Furthermore, integrating condition-based monitoring and predictive maintenance technologies can revolutionize the way globe valves are managed. By leveraging real-time diagnostics and predictive analytics, maintenance teams can anticipate potential failures, optimize maintenance intervals, and proactively address performance degradation, ultimately minimizing operational disruptions.
By focusing on preventative maintenance, organizations can uphold the performance and reliability of their valves, safeguarding the overall functionality of industrial systems and reducing the total cost of ownership.
In summary, optimizing flow control and implementing preventative maintenance strategies are instrumental in enhancing the performance of globe valves within industrial applications. By prioritizing precision flow control and proactive maintenance, engineers and operators can elevate the operational efficiency and longevity of their valves, contributing to the seamless function of critical industrial processes.
Conclusion
In conclusion, the working principle of a globe valve involves the movement of a disc as the closure member to regulate the flow in the pipeline. This valve is designed to stop, start, and regulate the flow of liquid or gas through pipes. The sealing surfaces of the valve disc and the valve seat play a crucial role in the closing principle of the globe valve, ensuring efficient and reliable operation. The small working stroke of the globe valve contributes to its good sealing, long life, and minimal friction between the sealing surfaces, making it a vital component in fluid control systems.