How Does a Gate Valve Work? Understanding the Basics
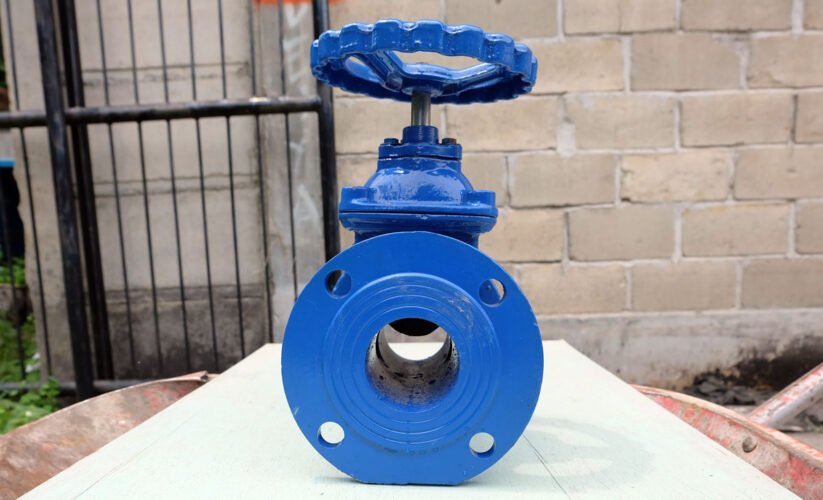
Table of Contents
ToggleThe Inner Workings of a Gate Valve: A Step-by-Step Analysis
The inner workings of a gate valve are crucial to many industrial processes. Understanding its step-by-step analysis is essential for anyone involved in the operation and maintenance of industrial systems. In this blog post, we will delve into the intricate details of how a gate valve functions, providing a comprehensive overview of its components and operations. This knowledge will be valuable for engineers, maintenance personnel, and anyone seeking a deeper understanding of this fundamental industrial valve.
Understanding the Basic Function of a Gate Valve
Gate valves play a crucial role in regulating fluid flow in industrial settings. By comprehending how these valves function, one gains valuable insight into their significance and utility. Let’s delve into the fundamental aspects and operation of these valves.
Fluid Flow Regulation
Gate valves are designed to control the flow of liquids or gases within a pipeline. This is achieved through the movement of a gate or wedge, typically crafted from metal, into or out of the path of the fluid flow. By raising the gate, the valve allows unrestricted fluid flow, while lowering the gate blocks the flow entirely, ensuring a secure seal and preventing leakage. This “on/off” functionality makes these valves well-suited for applications where precise flow control and minimal resistance are essential.
Internal Mechanism
The design and operation of gate valves can vary, with the rising stem and non-rising stem valves being the two primary types. In the rising stem gate valve, the stem moves vertically, providing visual confirmation of the gate’s position. On the other hand, the non-rising stem gate valve features a stationary stem, making it preferable for applications with limited space constraints.
Types of Gates
Gate valves are further categorized based on the type of gate they employ. These include the solid wedge, flexible wedge, and split wedge, each offering distinct advantages based on the application’s requirements. The solid wedge, for instance, is suitable for general use, while the flexible wedge accommodates slight pipeline alignment adjustments. The split wedge is effective in mitigating binding resulting from thermal expansion.
By understanding the basic function of a gate valve, one can appreciate its role in maintaining the efficiency and safety of fluid flow in diverse industrial processes. From oil and gas to water treatment and power generation, the versatility and precision of these valves make them indispensable components in various sectors.
How Does a Gate Valve Work?
- Closure Mechanism: A gate valve operates by raising and lowering a gate or wedge to control the flow of fluid. When the gate is raised, the flow is allowed, and when it’s lowered, the flow is shut off.
- Flow Control: The valve regulates the flow of fluid by the positioning of its gate. When fully open, the gate allows unobstructed flow, and when closed, it forms a seal to stop the flow completely.
- Upward and Downward Movement: The gate of the valve moves in a linear motion, either upwards to open the passage or downwards to close it.
- Minimal Obstruction: When fully open, the gate retracts into the bonnet of the valve, causing minimal obstruction to the flow path.
- Parallel or Wedge Gates: These valves have parallel gates for parallel seating types and wedge gates for wedge seating types, each functioning differently to control the flow.
- Operational Handles: The valve’s operation can be manual, with a handwheel or lever for small valves, or automated with actuators for larger valves, allowing remote or automatic operation.
- Sealing Surfaces: The gate and the seating surfaces are designed to ensure a tight seal when closed, preventing any leakage through the valve.
Key Components of a Gate Valve
A gate valve consists of several key components, each playing a crucial role in the valve’s function and performance. Understanding these components is essential for comprehending the inner workings of this valve and its applications in various industrial settings.
Body
The body of a gate valve serves as the primary pressure-retaining part, housing essential operational components such as the gate and seat. It provides the passage for fluid flow and connects to the piping on both ends. The choice of connection type, including threaded, flange, butt weld, compression fitting, or tube fitting, depends on factors such as valve size, operating pressure, and client specifications.
Bonnet
The bonnet acts as another pressure-retaining component, enclosing and safeguarding the valve’s stem and wedge. It allows access for repair or maintenance of internal elements and comes in various designs, including screwed, union, bolted, welded, and pressure seal bonnets, each suited for specific applications and pressure ranges.
Gate
The gate, also known as a disc or obturator, is responsible for regulating the flow of fluid through the valve. Depending on the application’s requirements, gate valves employ different gate designs and technologies, such as the wedge gate, ideal for high-flow or turbulent applications, and various other designs tailored to specific operational demands.
Stem
The stem of the valve facilitates the movement of the gate, allowing it to open or close the flow passage. It plays a crucial role in ensuring the proper functioning and control of the valve’s operation.
Seals and Gaskets
Seals and gaskets are vital components of a gate valve, serving to maintain a tight and secure seal to prevent leakage. They are designed to withstand the pressures and temperatures experienced during the valve’s operation, ensuring the integrity of the valve assembly.
Actuators
Gate valves can be equipped with actuators to automate the opening and closing of the gate, enabling remote or automated control of fluid flow. Actuators enhance the functionality and versatility of these valves, making them suitable for a wide range of industrial applications requiring precise flow control.
Understanding the roles and interactions of these key components provides valuable insights into the functionality and versatility of these valves in industrial processes, emphasizing their significance in fluid flow regulation and control.
Step-by-Step Analysis of How a Gate Valve Works
The Closed Position
In the closed position, a valve effectively shuts off the flow of fluid by employing a gate-like obstruction to block the pathway. When the handwheel is turned to close the valve, the gate is lowered into position to obstruct the passage, preventing the flow of fluid. The perpendicular movement of the gate is crucial for achieving a complete seal, thereby stopping the fluid from passing through.
The Open Position
Conversely, when the handwheel is turned to open the valve, the gate is lifted to allow unobstructed flow of the fluid. As the gate is raised, it clears the pathway for the fluid to pass through, enabling the valve to fully open and facilitate the flow of the medium. The gate’s perpendicular movement is once again fundamental as it dictates the smooth and unimpeded passage of the fluid.
Intermediate States
In its operation, a gate valve may also assume intermediate states, where the gate is positioned partially between open and closed. In such instances, the valve can be adjusted to regulate the flow of fluid, allowing for varying degrees of fluid passage. These intermediate states offer flexible control over the flow rate, making these valves suitable for diverse applications where precise flow adjustments are essential.
Types of Gate Valves and Their Applications
Gate valves are essential components in various process industries, providing efficient control over the flow of fluids and gases. Understanding the different types of valves and their applications is crucial for optimizing their use in industrial processes. Here’s a detailed analysis of the various types of gate valves and their specific applications.
Parallel vs. Wedge-Shaped Gate Valves
Among the different types, two common variations are parallel and wedge-shaped gate valves.
Parallel Gate Valves: These valves feature two parallel seats with a flat gate between them. They are ideal for applications where a tight seal is required, such as in low-pressure environments and for viscous fluids.
Wedge-Shaped Gate Valves: With a wedge-shaped gate, these valves allow for a tighter seal as the gate is wedged into the flow stream. They are suitable for high-pressure applications and are more effective in preventing leakage compared to parallel gate valves.
Rising Stem vs. Non-Rising Stem Gate Valves
Gate valves are also categorized based on their stem movement. Understanding the differences between rising stem and non-rising stem valves is crucial for selecting the right valve for specific applications.
Rising Stem Gate Valves: In these valves, the stem rises above the handwheel when the valve is opened. This design provides a visual indication of the valve’s status and allows for easy lubrication and maintenance.
Non-Rising Stem Gate Valves: These valves have the threads of the stem contained within the valve body, resulting in no upward stem movement during operation. They are suitable for applications with limited vertical space and are less prone to contamination.
Specialized Valves for Unique Applications
In addition to the standard parallel and wedge-shaped gate valves, there are specialized valves designed for unique applications.
Knife Gate Valves: These valves are specifically designed for applications involving viscous fluids, slurry, or solids, where the gate cuts through the media to provide shut-off.
Through-Conduit Gate Valves: Suitable for transporting abrasive media, through-conduit gate valves offer a full-bore design with minimal pressure drop, making them ideal for pipeline applications.
Understanding the specific characteristics and applications of these specialized gate valves is essential for selecting the right valve to meet the unique requirements of different industrial processes.
Maintenance and Troubleshooting Common Gate Valve Issues
Gate valves are essential components in various industries such as plumbing, oil and gas, and manufacturing. To ensure their optimal functionality, routine maintenance is crucial. Regular inspections and lubrication can significantly contribute to the longevity of these valves.
Routine Maintenance for Longevity
Routine maintenance involves inspecting the valve seat and gate for signs of damage or corrosion. It’s essential to identify any potential issues early on to prevent future problems. Additionally, applying anti-corrosion coatings and selecting materials resistant to corrosion can help mitigate this issue.
Identifying and Fixing Leakage
Leaking gate valves can lead to significant problems if left unaddressed. The primary cause of leakage is usually a damaged or worn-out valve seat or a damaged gate. It is recommended to inspect the valve seat and gate for signs of damage or corrosion. Regular maintenance and lubrication can also help prevent leaks.
Dealing with Gate Valve Sticking or Jamming
Gate valves can become stuck in the open or closed position due to rust, debris, or lack of lubrication. Resolving this issue may involve gently tapping the valve body with a rubber mallet to dislodge any debris or rust. If the valve remains stuck, it may require disassembly for a more thorough inspection and potential replacement of damaged parts.
Advancements in Gate Valve Technology
In recent years, advancements in valve technology have revolutionized the valve industry, leading to improved performance and efficiency across various sectors. These advancements have been driven by innovations in materials, design, and automation, aiming to enhance the functionality and reliability of gate valves.
Improved Materials for Enhanced Performance
The use of advanced materials such as corrosion-resistant alloys, ceramics, and composite materials has significantly improved the durability and performance of the valves. These materials offer superior resistance to harsh operating conditions, extending the service life of valves and reducing maintenance requirements. By leveraging these materials, industries can achieve higher levels of operational efficiency and reliability.
Innovations in Gate Valve Design
Innovative design approaches have transformed traditional gate valves into more streamlined and versatile configurations. The incorporation of streamlined flow paths and optimized sealing mechanisms has minimized fluid turbulence and pressure drops, resulting in improved flow control and reduced energy consumption. Additionally, the integration of smart design features has enhanced the adaptability of the valves to diverse application scenarios, catering to the evolving needs of modern industries.
Automation in Gate Valve Operations
The integration of automation technologies, such as actuators and positioners, has revolutionized the operation and control of gate valves. Automated systems enable precise valve positioning, remote operation, and real-time monitoring, facilitating enhanced process control and safety. The implementation of smart automation solutions has not only increased operational efficiency but also reduced the reliance on manual intervention, mitigating the risk of human error and optimizing overall system performance.
The continuous evolution of gate valve technology through improved materials, innovative design concepts, and automation solutions reflects a progressive paradigm shift towards enhanced functionality, reliability, and efficiency in industrial valve applications. These advancements signify a pivotal stride towards the future of valve technology, where performance, sustainability, and operational excellence converge to drive the next phase of industrial innovation.
Conclusion
Understanding the inner workings of a gate valve is crucial for anyone working with fluid control systems. The step-by-step analysis of its components sheds light on the importance of each part in regulating fluid flow. From the main body to the stem, each component plays a vital role in ensuring the functionality and efficiency of the gate valve. By comprehending the intricacies of a gate valve, one can make informed decisions in selecting, operating, and maintaining this essential industrial valve.