Pressure Ratings for Stainless Steel Globe Valves
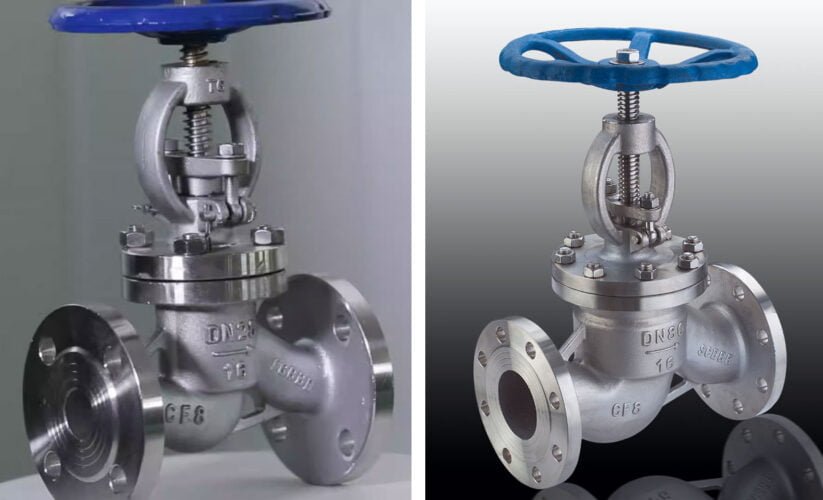
Table of Contents
ToggleThe Definitive Guide to Understanding Pressure Ratings for Stainless Steel Globe Valves
When it comes to understanding pressure ratings for stainless steel globe valves, it’s essential to grasp the significance of these ratings in ensuring the proper functioning and safety of industrial systems. Pressure ratings indicate the maximum pressure at which a valve can operate effectively and safely. In this comprehensive guide, we will delve into the intricacies of pressure ratings for stainless steel globe valves, covering the key factors, implications, and considerations that are crucial for engineers, technicians, and decision-makers in various industries. Understanding pressure ratings is fundamental to selecting the right globe valve for specific applications and maintaining system integrity.
Understanding the Role of Stainless Steel Globe Valves
Stainless steel globe valves play a crucial role in regulating the flow of fluids within a pipeline. Their robust construction and versatile design allow for effective control of water, gas, and oil. In this section, we will delve into the pivotal aspects of stainless steel globe valves, including their types, construction, operation, and advantages.
Types of Stainless Steel Globe Valves
Stainless steel globe valves come in two primary types:
- Wafer Globe Valves: These valves feature a ball supported by a seat and are typically employed in low-pressure applications.
- Trunnion-Mounted Globe Valves: Utilizing trunnions to support the ball, these valves are well-suited for high-pressure applications.
Stainless Steel Globe Valve Construction
Constructed primarily from austenitic stainless steel such as 304 or 316, stainless steel globe valves boast corrosion-resistant properties ideal for diverse applications. The essential components of a stainless steel globe valve include:
- Body: Serving as the primary housing, typically crafted from stainless steel.
- Ball: This valve element governs fluid flow and is usually made of stainless steel or a durable material like tungsten carbide.
- Seat: Providing a surface for the ball to seal against, typically composed of stainless steel or a hard-wearing material like tungsten carbide.
- Stem: Extending from the valve body and used for operation, typically made of stainless steel.
- Packing: A soft material such as PTFE or graphite used to form a seal between the stem and body.
Operation of Stainless Steel Globe Valves
The operation of a stainless steel globe valve involves the rotation of the stem. Clockwise rotation results in the ball blocking fluid flow, while counterclockwise rotation permits fluid passage.
Stainless Steel Globe Valve Advantages
Stainless steel globe valves offer numerous advantages, including:
- Reliable Sealing: The design allows for efficient sealing, minimizing the risk of leaks.
- Regulatory Control: Precise regulation of flow rate and pressure, ensuring optimal system performance.
- Durability: Robust construction enables longevity and resilience in various operating conditions.
- Versatility: Suitable for a wide range of applications, including water, gas, and oil systems.
- Corrosion Resistance: Austenitic stainless steel construction provides excellent resistance to corrosion and oxidation.
In the next section, we will explore the critical considerations for selecting stainless steel globe valves, empowering you to make informed decisions for your specific industrial requirements.
Basics of Stainless Steel Globe Valves
Stainless steel globe valves are essential components in fluid control systems, serving to regulate the flow of liquids and gases in various applications. Understanding the basics of these valves is crucial for professionals in the manufacturing, engineering, and construction industries.
What Are Stainless Steel Globe Valves?
Stainless steel globe valves are mechanisms designed to control the flow of fluid in a pipeline. They utilize a spherical-shaped component, known as the “globe,” to regulate the movement of liquids or gases. These valves are widely used in industrial settings due to their reliability and versatility.
Key Components of a Globe Valve
The construction of a stainless steel globe valve involves several key components that enable its functionality:
- Body: The main housing of the valve, typically constructed from durable stainless steel.
- Disk (Ball): The spherical element responsible for managing the fluid flow, often made of robust materials like stainless steel or tungsten carbide.
- Seat: The sealing surface where the ball rests to close off the valve, commonly crafted from stainless steel or tungsten carbide.
- Stem: A shaft extending from the valve body, used to control the valve’s operation and typically made of stainless steel.
- Packing: Utilized to create a seal between the stem and the valve body, often composed of soft materials such as PTFE or graphite.
Understanding these key components provides insight into the inner workings of stainless steel globe valves and their fundamental role in industrial applications.
The Significance of Pressure Ratings
Defining Pressure Rating and Its Importance
Understanding pressure ratings is crucial in ensuring the optimal performance and safety of stainless steel globe valves. The pressure rating of a valve defines the maximum pressure at which the valve can operate safely and efficiently. It is a vital factor in determining the suitability of a valve for specific applications, as it indicates the valve’s capability to withstand pressure without experiencing failure or leakage.
How Pressure Ratings Ensure Safety and Efficiency
Pressure ratings play a fundamental role in maintaining safety and efficiency within a fluid handling system. By adhering to specified pressure ratings, the risk of overpressure-related accidents and system failures is mitigated. Ensuring that the pressure rating of a stainless steel globe valve aligns with the system’s operating pressure safeguards against potential hazards, such as leaks or ruptures.
Additionally, adhering to pressure ratings promotes operational efficiency by enabling the selection of valves that can effectively manage the pressure requirements of the application, ultimately contributing to the overall performance and longevity of the system.
Pressure Rating Standards for Globe Valves
American National Standards Institute (ANSI) Class Ratings
The American National Standards Institute (ANSI) has established a classification system for pressure-temperature ratings. This system categorizes globe valves based on their pressure-temperature capabilities, allowing for easy identification of suitable applications. The ANSI class ratings range from 150 to 4500, with each class indicating a specific pressure-temperature capability.
International Standards Organization (ISO) Ratings
The International Standards Organization (ISO) has also devised a pressure-temperature rating system for globe valves. This system provides a globally recognized standard for categorizing globe valves based on their pressure-temperature capabilities. The ISO ratings, represented by the PN (Pressure Nominal) values, facilitate international trade and application compatibility.
Comparing Different Standard Systems
When comparing different standard systems such as ANSI and ISO, it’s crucial to understand their respective rating methodologies and the implications for valve selection. While ANSI class ratings are widely used in the United States, the ISO ratings are prevalent in many international markets. Therefore, a comprehensive understanding of both systems is essential for businesses operating in diverse global environments. By comparing and contrasting these standard systems, businesses can make informed decisions when selecting globe valves for specific projects.
Factors Influencing Pressure Ratings of Stainless Steel Globe Valves
Material Grade and Its Impact on Pressure Tolerance
The material grade of stainless steel globe valves plays a crucial role in determining their pressure ratings. Higher grades of stainless steel, such as 316 or 316L, offer superior corrosion resistance and strength compared to lower grades, thereby enhancing the valve’s ability to withstand higher pressures. Manufacturers often provide pressure-temperature charts specific to the material grade, aiding in the selection of the most suitable valve for a given application.
Valve Size and Pressure Rating Correlation
Valve size directly influences the pressure rating of stainless steel globe valves. Larger valves generally have a higher pressure rating due to their capacity to accommodate a greater volume of fluid flow without compromising the structural integrity. Conversely, smaller valves may have lower pressure ratings. It is essential to consider the flow requirements and system pressure when selecting the appropriate valve size to ensure optimal performance and safety.
Temperature as a Critical Factor
Temperature fluctuations pose a significant impact on the pressure ratings of stainless steel globe valves. Elevated temperatures can affect the material properties of the valve, reducing its pressure tolerance. It is imperative to consider the maximum and minimum operating temperatures within the system to select a valve that can withstand the anticipated temperature range. Additionally, the valve’s sealing components and packing materials should be assessed for their temperature resistance to ensure long-term reliability under varying thermal conditions.
Reading and Interpreting Pressure Rating Information
Understanding Valve Markings and Tags
Stainless steel globe valves come equipped with pressure rating information that is crucial for determining their operational limits. The markings on the valve body typically include the maximum pressure it can handle, indicated in pounds per square inch (PSI) or bar. These markings serve as a guide to ensure that the valve is not exposed to pressures beyond its capacity, which is essential for maintaining safety and preventing equipment damage. Moreover, valve tags often provide additional details about the valve’s pressure rating, materials, and relevant standards, further aiding in the comprehensive understanding of its capabilities.
Utilizing Manufacturer’s Data Sheets
Manufacturer’s data sheets offer comprehensive insights into the pressure ratings of stainless steel globe valves. These documents provide detailed tables or charts presenting the maximum pressure limits corresponding to different temperatures and valve sizes. By referring to the data sheets, engineers and operators can make informed decisions regarding the suitability of a specific valve for their application, considering factors such as operating conditions and system requirements. Additionally, the data sheets may include installation guidelines and maintenance recommendations, contributing to the effective utilization of the valve while adhering to its pressure limitations.
Selection Tips for Stainless Steel Globe Valves Based on Pressure Ratings
Assessing Application Requirements
When selecting stainless steel globe valves, it is crucial to assess the specific requirements of the application. Consider factors such as the type of fluid or gas that will flow through the valve, the temperature and pressure conditions, and any potential corrosive properties of the medium. Understanding these application requirements will help in determining the appropriate pressure rating needed for the globe valve to ensure optimal performance and longevity.
Importance of Matching Valve Rating to Piping System
Matching the pressure rating of the stainless steel globe valve to the piping system is essential for ensuring system integrity and safety. Failure to match the valve rating to the system’s pressure requirements can lead to catastrophic consequences, including leakage, valve malfunctions, or even system failures. It is imperative to select a globe valve with a pressure rating that aligns with or exceeds the maximum pressure that the piping system will encounter during operation.
By carefully assessing application requirements and ensuring the proper matching of the valve rating to the piping system, operators can mitigate risks and optimize the performance of stainless steel globe valves in various industrial applications.
Maintenance and Testing to Preserve Pressure Integrity
Routine Maintenance Practices
Regular maintenance of stainless steel globe valves is essential to ensure their durability and pressure integrity. This includes inspection of the valve body, bonnet, stem, disc, and seats for signs of corrosion, erosion, or wear. Proper lubrication of moving parts, such as the stem and disc, is crucial to prevent friction and ensure smooth operation. Checking the packing gland for leaks and adjusting it if necessary can help maintain the sealing integrity of the valve. Additionally, ensuring that the valve is installed in a clean environment and protected from external contaminants can prolong its service life and preserve pressure integrity.
Testing Procedures for Pressure Verification
Pressure testing is a critical aspect of ensuring the integrity of stainless steel globe valves. This involves subjecting the valves to a specified pressure to verify their ability to withstand the intended operating conditions. Hydrostatic testing, using water or another suitable liquid, is commonly performed to assess the valves’ pressure resistance. During this process, the valves are pressurized and inspected for any signs of leakage or structural deformation. Regular pressure verification testing helps identify potential weaknesses in the valves and ensures that they can maintain their pressure ratings under actual operating conditions.
Troubleshooting Common Pressure-Related Issues with Globe Valves
Pressure-related issues can significantly impact the performance of stainless steel globe valves. Recognizing the signs of pressure rating problems and understanding the steps to address them is crucial for maintaining the integrity of the valve system.
Identifying Symptoms of Pressure Rating Problems
- Leakage: If there are visible leaks around the valve, it could indicate that the pressure is exceeding the valve’s rating, causing it to compromise its sealing capabilities.
- Reduced Flow: A decrease in flow rate through the valve could signal that the pressure is too low, preventing the valve from operating efficiently.
- Vibration and Noise: Unusual vibrations and noise during valve operation may be indicative of pressure fluctuations, potentially stemming from a mismatch between the system’s pressure and the valve’s rating.
- Inconsistent Performance: Fluctuations in the valve’s performance, such as erratic opening and closing or irregular flow control, could be linked to pressure-related issues.
Steps for Addressing Pressure Deficiencies
- Review System Pressure: Conduct a thorough assessment of the system’s pressure to ensure it aligns with the valve’s specified rating. This may involve using pressure gauges or consulting with a qualified technician.
- Adjust Operating Conditions: If low pressure is the culprit, consider modifying the operating conditions to optimize the flow and pressure levels within the system.
- Upgrade Valve Components: In cases of persistent pressure-related issues, upgrading certain valve components, such as the trim or actuator, may be necessary to accommodate the required pressure rating.
- Reevaluate Valve Sizing: An incorrect valve size in relation to the system’s pressure demands could lead to inefficiencies. Reevaluate the valve sizing to ensure it aligns with the specific pressure requirements.
By promptly identifying symptoms and taking appropriate corrective actions, potential pressure-related issues with stainless steel globe valves can be effectively mitigated, ensuring optimal performance and longevity.
Conclusion
Understanding the pressure ratings for stainless steel globe valves is essential for ensuring their optimal performance and safety in various industrial applications. By considering factors such as temperature, material, and design specifications, you can select the appropriate pressure rating to meet the specific requirements of your system. With this comprehensive guide, you are now equipped with the knowledge to make informed decisions when choosing stainless steel globe valves based on their pressure ratings.