3 Types of Piston Check Valves and Their Applications in Different Industries
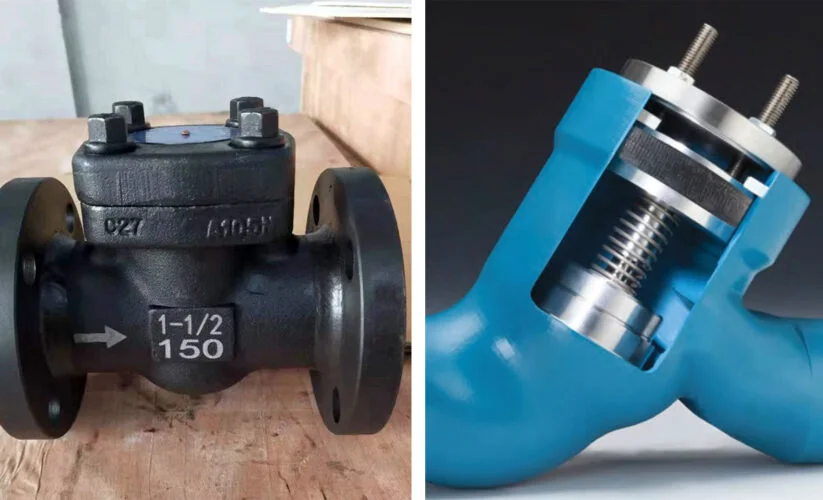
Table of Contents
ToggleUnderstanding the Function of Piston Check Valves
Piston check valves are a vital component in various industries, functioning to prevent backflow within a piping system. These valves operate similarly to ball check valves, allowing flow when pressure remains steady and providing gravitational closure when pressure decreases. They are commonly used in applications such as feed water control in the nuclear industry, dump lines, make-up water, and monitoring and sampling systems. Piston check valves may also include spring assistance depending on flow conditions. Their versatility and reliability make them a crucial asset in numerous industrial processes.
What is a piston check valve?
Definition and Basic Function
A piston check valve is a type of valve that permits the flow of fluid in one direction while preventing reverse flow. It consists of a body-guided piston or disk that moves within the valve body in response to the pressure of the fluid. The piston check valve is designed to allow the fluid to flow freely when the pressure is in the correct direction, while sealing off the flow if the pressure reverses.
What is a piston valve used for?
Piston check valves are commonly used in applications where preventing backflow is essential. They are suitable for use in industries such as oil and gas, petrochemical, pharmaceutical, and food processing, where the prevention of reverse flow of fluids or gases is crucial.
The Role of Gravity and Pressure in Operation
The operation of a piston check valve is influenced by both gravity and fluid pressure. When the fluid pressure exceeds the force of gravity, the piston or disk is lifted, allowing fluid to pass through. In the event of reverse flow, the force of gravity, combined with the pressure of the fluid, causes the piston or disk to close, effectively blocking the reverse flow.
What is the difference between piston check and lift check?
The main difference between a piston check valve and a lift check valve lies in their design and operation. While a piston check valve uses a guided piston or disk to regulate flow, a lift check valve uses a ball or disk that is free to move in response to fluid pressure. Both valves serve the purpose of preventing backflow, but their mechanisms of operation differ, leading to variations in performance and suitability for specific applications.
How does a piston check valve work?
A piston check valve operates to ensure unidirectional flow in a piping system, preventing the reversal of fluid. The valve’s design includes essential components that enable its functionality.
Design and Components of Piston Check Valves
The piston check valve is essentially a lift check valve, featuring a dash-pot comprising a piston and cylinder to provide cushioning during operation. When fluid pressure exceeds the weight of the check mechanism, the valve opens, allowing fluid to flow through the system. Conversely, any reversal of flow causes the valve to close. This closure can be accomplished by the check mechanism’s weight, back pressure, a spring, or a combination of these methods.
Construction
Similar to lift check valves, the construction of the seat and disk of a piston check valve follows the same principles. The valve is installed such that flow enters from under the seat, ensuring optimal performance.
Application
Piston check valves are commonly used in conjunction with globe and angle valves in piping systems experiencing frequent changes in flow direction. They find applications in water, steam, and air systems, where maintaining unidirectional flow is critical.
The design and components of piston check valves play a crucial role in their functionality within various industrial applications, ensuring efficient and reliable unidirectional fluid flow.
Variations of Piston Check Valves
Piston check valves are designed with different mechanisms to suit various industrial requirements. The variations include spring-loaded piston check valves, lift piston check valves, and angle piston check valves.
Spring-Loaded Piston Check Valves
Spring-loaded piston check valves are equipped with a spring mechanism that assists in the closure of the valve. When the flow of fluid reverses, the spring helps push the piston into the closed position rapidly, hence preventing backflow. These valves are commonly used in applications where a rapid response to flow reversal is crucial.
Lift Piston Check Valves
Lift piston check valves utilize a body-guided disk that moves inside the body in an up and down motion. When the flow of fluid is in the right direction, the pressure and flow rate force the disk to allow liquid to pass through the valve. In case of a sudden flow reversal, the disk is forced into the closed position, thus preventing the return of fluid. These valves are suitable for applications requiring the prevention of backflow.
Angle Piston Check Valves
Angle piston check valves are designed at an angle to the pipeline, allowing for efficient flow regulation. The angular orientation of these valves enables them to be used in tight spaces or where the pipeline layout requires a change in flow direction. These valves are suitable for applications such as water treatment plants and industrial processing where space constraints are a consideration.
Piston check valves play a crucial role in ensuring the smooth and uninterrupted flow of fluids in various industries. The different variations cater to specific needs, making them essential components in industrial fluid control systems.
Applications in Various Industries
The applications of piston check valves are diverse, with their functionality proving valuable in various industries. Let’s explore how these valves are utilized in different sectors.
Nuclear Industry Uses
In the nuclear industry, the reliability of check valves is critical for safety and efficiency. Piston check valves are employed in nuclear power plants to control the flow of coolant within the reactor system. By preventing backflow, these valves ensure the integrity of the coolant loop, contributing to the safe operation of nuclear reactors.
Water Treatment and Processing
Piston check valves play a vital role in water treatment and processing facilities. These valves are utilized to maintain the directional flow of water, preventing the reverse flow of contaminated or untreated water. In water treatment plants, piston check valves help regulate the movement of water during filtration, purification, and distribution processes, ensuring the delivery of clean and safe water to consumers.
Industrial Process Systems
In industrial process systems, piston check valves are integral components in ensuring fluid control and system efficiency. These valves are employed in pipelines, chemical processing plants, and manufacturing facilities to prevent the reversal of fluids, safeguarding equipment and optimizing operational processes. Their ability to withstand high pressures and temperatures makes them suitable for a wide range of industrial applications.
Gas Systems and Monitoring
Piston check valves are also utilized in gas systems and monitoring equipment. These valves help maintain the flow of gases in a single direction, preventing leaks and ensuring precise control over gas distribution. In gas monitoring devices, piston check valves contribute to accurate measurements by regulating gas flow and preventing unwanted backflow, thus enhancing the reliability and functionality of the monitoring systems.
The versatility of piston check valves makes them indispensable in a variety of industries, demonstrating their significance in enhancing operational reliability and safety across different sectors.
Comparing Piston, Ball, and Stop Check Valves
Piston, ball, and stop check valves are all widely used in various industries, each with its unique features and applications. Understanding the differences between these valve types is crucial for selecting the right one for specific operational requirements.
Ball Check Valves and Their Unique Features
Ball check valves are designed with a spherical ball inside the valve body, which moves in response to the flow of fluid. When the pressure in the line exceeds the weight of the ball, it lifts, allowing the fluid to pass through. These valves are known for their simple design, which minimizes maintenance requirements and ensures reliable operation. The ball check valve is ideal for applications where backflow prevention is essential, such as sewage systems, industrial processing, and wastewater treatment plants.
Stop Check Valves
Stop check valves combine the functions of a globe valve and a check valve. They feature a disc that moves in a linear motion to control the flow of fluid, providing both check valve functionality to prevent backflow and the ability to stop the flow entirely. This dual functionality makes stop check valves suitable for applications where flow regulation and backflow prevention are critical, such as in steam systems and boiler feedwater control.
Selecting Between Valve Types for Specific Applications
When selecting between piston, ball, and stop check valves for specific applications, several factors must be considered. The type of fluid, pressure, temperature, and flow characteristics all play a vital role in determining the most suitable valve for a given application. Additionally, factors such as maintenance requirements, installation restrictions, and cost considerations must be evaluated to ensure the selected valve aligns with the operational needs effectively.
In essence, understanding the unique features and application considerations for piston, ball, and stop check valves is essential for making informed decisions in various industrial settings. By carefully evaluating the specific requirements of each application, operators can select the most appropriate valve type to optimize operation and ensure reliable performance.
Installation and Maintenance Considerations
Best Practices for Valve Installation
When installing piston check valves, it is essential to follow certain best practices to ensure optimal performance. Firstly, it is crucial to carefully align the valve with the pipeline to prevent any potential damage. Proper alignment will also help in reducing stress on the valve body, thereby extending its lifespan. Additionally, using the correct torque when tightening the valve’s fasteners is crucial for maintaining a leak-free seal. Lastly, verifying the compatibility of the valve material with the surrounding environment is vital to prevent corrosion and other forms of deterioration.
Common Challenges in Valve Maintenance
Valve maintenance often poses challenges that can impact operational efficiency. One common challenge is the build-up of deposits within the valve, which can restrict the flow and affect the overall functionality. Additionally, wear and tear on sealing components can lead to leakage, reducing the valve’s effectiveness. To mitigate these challenges, it is important to conduct regular inspections and cleaning to prevent any build-up and replace worn components promptly.
Tips for Ensuring Long-Term Valve Performance
To ensure long-term performance of piston check valves, implementing proactive measures is essential. Regularly scheduled maintenance, including cleaning and lubrication, can significantly extend the valve’s lifespan and prevent unexpected failures. It is also advisable to monitor the valve’s operating conditions and address any deviations promptly. Furthermore, utilizing compatible materials and coatings can protect the valve from corrosion and erosion, contributing to its long-term performance and reliability.
Advantages and Disadvantages of Piston Check Valves
Piston check valves offer several advantages in industrial applications, but they also come with certain limitations and potential issues.
Benefits in Industrial Applications
Flow Control: Piston check valves provide precise flow control, allowing for efficient regulation of fluid movement in industrial systems. This feature makes them invaluable in processes where accurate flow management is crucial.
Tightness: The tight contact between the metal piston and non-metal seal packs ensures excellent sealing, preventing fluid leakage and maintaining system integrity. This feature is particularly important in applications where maintaining a secure seal is essential.
Versatility: Piston check valves can effectively handle a wide range of fluids, including those containing solid particles and gaseous substances. Their ability to seal packs during opening and closing enables them to perform reliably across diverse industrial environments.
Durability: The use of non-metal gaskets for the movement of pistons results in reduced wear and tear, contributing to the valves’ longevity and sustained performance. This durability is a significant advantage in industrial settings with rigorous operating conditions.
Limitations and Potential Issues
High Pressure Losses: The structural design of piston check valves can lead to significant pressure losses within fluid systems. This drawback necessitates careful consideration of the overall system pressure and flow dynamics when integrating these valves.
Dead Volume: Piston check valves may have dead volume, creating the potential for residue accumulation within the valve body. This can compromise fluid purity and operational efficiency, particularly in systems where cleanliness is paramount.
Operational Challenges: In larger nominal dimensions, piston check valves experience substantial forces during opening and closing, posing operational challenges. This can affect the ease and efficiency of valve closure, requiring additional considerations for seamless functionality.
When incorporating piston check valves into industrial setups, it’s essential to weigh these benefits against the associated limitations and potential issues to make informed decisions for optimal system performance.
Choosing the Right Piston Check Valve
Factors Impacting Valve Selection
When considering the right piston check valve for a specific application, several factors come into play. It’s crucial to assess the pressure, temperature, flow rate, and the type of fluid the valve will be handling. The operating environment, including the presence of corrosive or abrasive substances, also plays a significant role in determining the appropriate valve for the job. Additionally, the installation space, maintenance requirements, and regulatory compliance should be carefully evaluated to ensure the selected valve meets all necessary criteria.
Material Considerations for Durability
The material of the piston check valve is a crucial consideration in ensuring its longevity and effectiveness. For applications dealing with corrosive fluids, stainless steel or other corrosion-resistant alloys are often preferred to prevent degradation over time. In contrast, for applications with high temperatures, materials with excellent heat resistance, such as titanium or specially formulated polymers, should be chosen to withstand the harsh operating conditions. Material selection is imperative to guarantee the durability and reliability of the piston check valve in various industrial settings.
Assessing Flow Requirements and Conditions
Understanding the specific flow requirements and operating conditions is fundamental in selecting the right piston check valve. Factors such as flow rate, pressure drop, and the presence of backflow need to be thoroughly evaluated to ensure that the chosen valve can effectively regulate the flow in a given system. Additionally, considering the nature of the fluid and potential flow disturbances within the system is essential for choosing a piston check valve that can maintain optimal performance under varying flow conditions. By carefully assessing the flow requirements and conditions, an appropriate piston check valve can be selected to seamlessly integrate into diverse industrial applications.
Conclusion
In conclusion, piston check valves are crucial components in various industries such as the nuclear industry, process systems, and monitoring and sampling systems. Their ability to prevent backflow and maintain steady flow pressure makes them indispensable in applications where flow control and protection against reverse flow are essential. With their diverse applications and functionality, piston check valves play a vital role in ensuring the efficiency and safety of piping systems across different sectors.