The Complete Breakdown of Gate Valve Parts: An In-Depth Guide
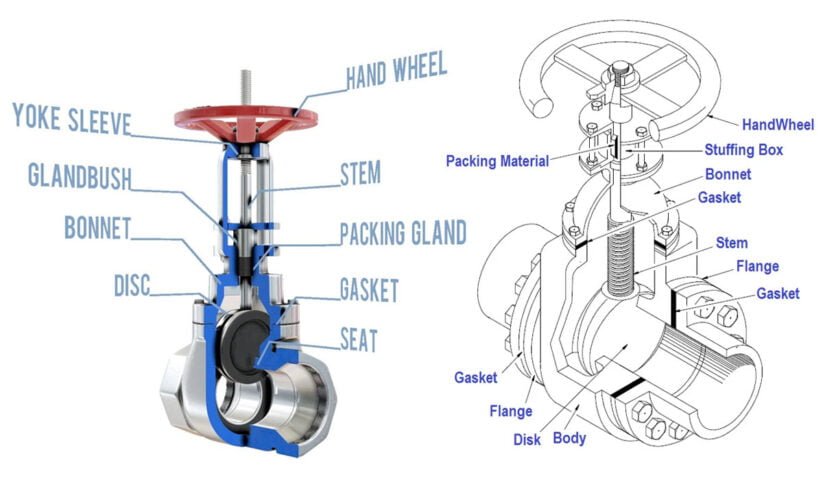
Table of Contents
ToggleThe Ultimate Guide to Gate Valve Parts: Everything You Need to Know
A gate valve is an essential component in industrial settings, often used to fully restrict or permit flow. This article provides a comprehensive overview of the key components that make up a gate valve, including the body, bonnet, gate, stem, and seat. Understanding these components is crucial for gaining insight into the functioning and maintenance of gate valves.
Understanding Gate Valves
Definition and Importance
A gate valve is a type of control valve that is designed to either allow media to flow through unobstructed or to stop the fluid flow completely. This valve is known for its straight-through unobstructed passageway, which results in minimal pressure loss over the valve. The unobstructed bore of a gate valve also makes it possible for a pig’s passage in cleaning pipe procedures. It is important to note that gate valves should only be used in the fully open or closed position, as they are not designed to regulate the flow.
Basic Function of Gate Valves
The basic function of a gate valve involves the operation of a handwheel to move the gate up or down on the stem. This action opens or closes the inlet to the outlet, allowing an unobstructed passageway for the media to flow or blocking the media flow, respectively. It’s worth noting that a gate valve typically requires more than one 360° turn to open or close the valve fully, making it slower than quarter-turn valves. Automated gate valves with electric or pneumatic actuators exist, though manual gate valves are often favored for their cost-effectiveness, especially when they are used infrequently.
The Body of a Gate Valve
A gate valve’s body serves as the primary pressure-retaining component, housing essential operational parts such as the gate and seat. It facilitates the flow through the valve and is connected to the piping at both ends. The choice of connection type, including threaded, flange, butt weld, compression fitting, or tube fitting, depends on client specifications, valve size, and operating pressure.
1. The Body Structure
The body of a gate valve typically consists of a bonnet, which encases the valve stem and provides a seal for the valve. It also includes inlet and outlet ports for the fluid to pass through.
2. Materials Used
Gate valve bodies are commonly made from materials such as cast iron, carbon steel, stainless steel, and bronze, chosen based on factors like pressure ratings, temperature limitations, and corrosion resistance.
3. Bonnet Design
The bonnet of a gate valve is designed to provide a leak-proof seal and to house the stem and the gate. It is essential for maintaining pressure containment and preventing fluid leaks.
4. Connection Types
Gate valve bodies can feature various connection types, including flanged ends, socket weld ends, threaded ends, and butt weld ends, each suited for different installation and operational requirements.
5. Pressure Classifications
Gate valve bodies are manufactured to different pressure classifications, such as Class 150, Class 300, Class 600, and Class 1500, to accommodate varying pressure requirements in different applications.
6. Operational Considerations
Understanding the body of a gate valve is crucial for proper installation, operation, and maintenance, as it directly impacts the valve’s performance and reliability in controlling fluid flow.
7. Design Variations
Gate valve bodies come in various designs to suit different applications. The most common design variations include:
- Rising Stem: This design features a stem that rises as the valve is opened, providing a visual indication of the valve’s position and facilitating the operation in applications where the flow needs to be controlled precisely.
- Non-Rising Stem: In this design, the stem does not rise as the valve is opened. It is suitable for applications with space constraints as it occupies less vertical space.
- Bolted Bonnet: Gate valves with bolted bonnets are widely used in applications with higher working pressure. The bolted bonnet design allows for easy maintenance and repair by providing access to the internals of the valve.
- Pressure Seal Bonnet: Suitable for high-pressure applications, the pressure seal bonnet design ensures a tight seal as the internal pressure increases. It is commonly used in applications exceeding 1500 psi.
The choice of design variation depends on the specific requirements of the application, such as pressure, temperature, and maintenance considerations.
The body of a gate valve plays a critical role in its overall function and reliability. By understanding its components, materials, and design considerations, industry professionals can make informed decisions regarding the selection, installation, and maintenance of gate valves in diverse industrial applications.
Remember, body of the valve is not just a physical structure but a key element in ensuring the efficient and safe operation of fluid control systems.
The Gate: Heart of the Valve
The gate is the central component of a gate valve and is crucial for regulating the flow of fluids. There are different types of gate designs that cater to varying operational requirements. The most common types include wedge gates, slab gates, and parallel slide gates. Each design offers distinct advantages and is chosen based on factors such as pressure, temperature, and flow control precision.
1. Wedge Gates
Wedge gates are one of the most commonly used designs in gate valves. They feature a wedge-shaped gate that provides a tight seal, making them ideal for applications where a high degree of shutoff is required. The angle of the wedge can vary, with options including flexible and solid wedges, each offering unique advantages in different operating conditions.
2. Slab Gates
Slab gates are characterized by a flat, single gate design that provides an unobstructed flow path when fully open. This design is particularly effective for handling slurries and viscous fluids due to its ability to minimize flow resistance. Slab gates are often preferred in applications where the prevention of fluid buildup is crucial.
3. Parallel Slide Gates
Parallel slide gates utilize two parallel gates that move in opposite directions to control the flow. This design offers precise flow control and is well-suited for high-pressure and high-temperature applications. Parallel slide gates are known for their ability to minimize wear and erosion, making them durable and reliable in demanding environments.
Understanding the unique characteristics and operational advantages of each gate design is essential for making informed decisions when selecting gate valves for specific industrial, commercial, or residential applications.
4. Material Choices for Gates
The choice of gate material is vital to ensure the valve’s performance and durability. Some common materials used for gates include:
- Stainless Steel: Resistant to corrosion and erosion, making it suitable for a wide range of applications.
- Carbon Steel: Known for its strength and reliability in high-pressure systems.
- Brass: Ideal for low-pressure applications, offering corrosion resistance and easy machinability.
- Bronze: Provides durability and resistance to corrosion, making it suitable for seawater and other corrosive environments.
The material selection is influenced by factors such as fluid properties, temperature, and pressure, ensuring compatibility and longevity of the gate in the valve system.
In conclusion, the gate serves as the heart of the valve in gate valve systems, and selecting the appropriate gate design is vital for ensuring optimal performance and efficiency in fluid flow control applications. With considerations such as pressure, temperature, and flow control precision, choosing the right gate design is crucial for meeting operational requirements and achieving reliable fluid regulation.
The Stem: The Mover of the Gate
Rising vs. Non-Rising Stem
In the realm of gate valves, the stem plays a crucial role in controlling the movement of the gate. When it comes to stems, there are two main types: rising and non-rising. A rising stem gate valve has a stem that moves upwards when the valve is opened, providing a visual indicator of the valve’s position. On the other hand, a non-rising stem gate valve has a stem that does not move upwards as the valve is opened or closed. The choice between rising and non-rising stems is often determined by the space available and the specific requirements of the application.
Stem Material and Durability
Stem material is a significant consideration in the design and functionality of gate valves. Generally, stems are made from stainless steel, brass, bronze, or other robust materials to withstand the demanding conditions they are subjected to. The choice of stem material depends on factors such as the type of fluid being handled and the operating environment. Durability is a key concern, as the stem must endure repetitive movement and potential exposure to corrosive elements. A well-chosen stem material ensures the longevity and reliability of the valve, contributing to efficient operation and minimal maintenance requirements.
Gate Valve Sealing: Ensuring Tight Closure
The sealing element, also known as the seat, comes in different types, each with its unique features and applications. Understanding the various sealing elements of gate valves is fundamental for selecting the most suitable option for specific operational requirements.
Metal Seated Gate Valves
Metal seated gate valves are designed with sealing surfaces made of metal, such as stainless steel or alloy materials. These valves are ideal for high-temperature and high-pressure applications, offering excellent resistance to wear and corrosion. The metal seated gate valves are commonly used in industries such as oil and gas, refining, and petrochemical plants.
Resilient Seated Gate Valves
Resilient seated gate valves feature a soft elastomeric seat, such as EPDM or NBR, providing a bubble-tight seal. These valves are suitable for water and wastewater applications, offering low torque operation and reliable sealing performance. Resilient seated gate valves are commonly used in municipal water systems, irrigation, and sewage treatment plants.
Knife Gate Valves
Knife gate valves utilize a sharp-edged blade to cut through and seal against soft materials, such as slurries and powders. These valves are widely used in industries such as mining, pulp and paper, and chemical processing for handling abrasive and viscous media. Knife gate valves offer bi-directional sealing and are available in various materials to suit different process conditions.
Throttling Gate Valves
Throttling gate valves are designed for flow control applications, featuring a tapered or wedge-shaped disc to regulate the flow of fluids. These valves offer precise throttling capabilities and are commonly used in pipelines, steam systems, and power plants. The sealing elements of throttling gate valves are engineered to provide accurate flow modulation without compromising tight shut-off capabilities.
Expanding Gate Valves
Expanding gate valves utilize a mechanism to expand the gate during operation, pressing it against the seats to achieve a tight seal. These valves are well-suited for high-temperature and high-pressure services in the oil and gas industry, offering bidirectional sealing and reliable performance in challenging operating conditions. The expanding gate design ensures a secure seal even in fluctuating temperatures and pressures.
The selection of the appropriate sealing element (seat type) for gate valves is critical to ensuring reliable and efficient operation in various industrial applications. Understanding the characteristics and applications of different types of sealing elements enables engineers and operators to make informed decisions when choosing the valves for specific process requirements. By considering factors such as temperature, pressure, media, and operational conditions, the optimal sealing element can be selected to enhance the performance and longevity of gate valves in diverse industrial settings.
Actuators: Power Behind the Movement
Actuators are essential components of gate valves, providing the power behind the movement critical for their operation. Understanding the different types of actuators and their functions is crucial for anyone involved in the selection, installation, or maintenance of the valves.
Manual Actuators Explained
Manual actuators offer a simple yet effective means of controlling gate valves. They are operated by hand, making them ideal for applications where power sources may be limited or impractical. Manual actuators are commonly used in smaller-scale operations or as backup mechanisms in case of power failure.
Automated Actuators and Their Uses
Automated actuators, on the other hand, are designed to provide automated and often remote control of the valves. These actuators are powered by electricity, hydraulics, or pneumatics, allowing for precise and efficient operation of gate valves in a wide range of industrial settings. Automated actuators are essential in scenarios where frequent or precise valve adjustments are required, and they offer the benefits of improved efficiency and reduced reliance on manual intervention.
The selection of the appropriate actuator type, whether manual or automated, depends on the specific requirements of the application, including factors such as operational frequency, environmental conditions, and available power sources. Understanding the distinctions between manual and automated actuators is crucial for ensuring the optimal performance and longevity of gate valves in diverse industrial settings.
Bonnets: The Valve’s Protector
Bonnet Functions
The bonnet serves as a protective cover for the valve’s internal components, safeguarding them from environmental factors such as corrosion, erosion, and high pressure. It also provides a leak-proof closure to contain the fluid within the valve.
Different Bonnet Types
- Bolted Bonnet: This type of bonnet is connected to the valve body using bolts, allowing for easy maintenance and repair.
- Pressure Seal Bonnet: Suitable for high-pressure applications, this bonnet design ensures a tight seal by using pressure to enhance the closure.
- Welded Bonnet: Welded directly to the valve body, this bonnet type provides a permanent seal, making it ideal for critical applications.
Gaskets and Packing: Preventing Leaks
Gasket Materials and Placement
Gaskets are crucial components that prevent leaks by providing a tight seal between the gate valve components. They are commonly made from materials such as rubber, graphite, Teflon, or metal, depending on the specific application and the pressure and temperature conditions the gate valve will be exposed to. The placement of gaskets is strategically designed to seal the space between the body and bonnet, as well as between the body and the valve cover, ensuring that no fluid can escape through these connections.
Packing Material Types and Functions
Packing materials play a vital role in preventing leaks in gate valves. They are typically made from materials such as flax, synthetic fibers, graphite, or Teflon, and are used to create a seal around the valve stem as it moves through the packing gland. This seal prevents fluid from escaping past the stem and ensures smooth operation of the valve. The choice of packing material depends on factors such as the type of fluid, pressure, and temperature, and it is essential for maintaining the integrity of the valve and preventing leakage.
By selecting the appropriate gasket and packing materials and ensuring their correct placement, gate valves can effectively prevent leaks and maintain their functionality, making them reliable components in various industrial applications.
Other Key Components of a Gate Valve
Yokes and Yoke Nuts
The yoke serves as a support for the stem, providing stability and strength to withstand the forces exerted during valve operation. It is crucial in ensuring proper alignment of the gate and stem to maintain efficient performance. Yoke nuts, on the other hand, are responsible for securing the yoke in place, preventing any misalignment or potential damage during operation.
When looking at yokes and yoke nuts, it’s essential to consider the material and construction. Opting for durable materials such as stainless steel or bronze can significantly enhance the longevity and resilience of these components, ensuring smooth valve functionality.
Bushings and Bearings
Bushings and bearings play a vital role in minimizing friction and wear within the gate valve. These components are strategically placed to reduce the resistance encountered during the movement of the stem, maximizing operational efficiency and longevity.
By incorporating self-lubricating materials or coatings, such as Teflon or graphite, the friction between moving parts can be significantly reduced, promoting smoother movement and minimizing the need for frequent maintenance. Proper selection and maintenance of these components can contribute to the overall performance and lifespan of the valve.
Incorporating high-quality bushings and bearings can elevate the operational reliability of gate valves, ensuring consistent performance and minimal downtime.
Specialty Gate Valve Parts for Specific Needs
Cryogenic Extensions for Cold Temperatures
Cryogenic extensions for gate valves are engineered to withstand extremely low temperatures, making them ideal for applications in industries such as aerospace, pharmaceuticals, and energy, among others. These extensions are designed to ensure that the valve components remain operational and maintain their integrity in environments with temperatures as low as -196°C (-321°F). The cryogenic extensions prevent materials from becoming brittle or failing due to thermal stress, allowing the gate valve to function effectively even in the harshest cold conditions.
Bypass Valves for Pressure Balancing
Bypass valves are essential for pressure balancing in the valve systems. They enable the regulation of pressure by diverting a portion of the flow to another part of the system, ensuring that excessive pressure is managed effectively. This feature is particularly valuable in scenarios where pressure surges or fluctuations could potentially damage the valve or the overall system. Bypass valves contribute to the smooth and safe operation of gate valves, providing an additional layer of control and stability in various industrial applications.
Maintenance and Replacementof Gate Valve Parts
Common Wear and Tear Issues
Over time, valves can experience wear and tear due to regular use and exposure to various elements. Common issues include corrosion, erosion, and damage to the sealing surfaces. Corrosion can occur when the valve is exposed to corrosive fluids, leading to deterioration of the valve body and internal components. Erosion is often caused by the flow of high-velocity fluids, gradually wearing away the valve surfaces. Damage to the sealing surfaces can occur from repeated opening and closing of the valve, as well as exposure to abrasive materials. Identifying these wear and tear issues is crucial for maintaining the integrity and functionality of the valves.
When to Replace Gate Valve Parts
Knowing when to replace gate valve parts is essential for preventing potential malfunctions and ensuring optimal performance. Signs that parts may need replacement include leakage, reduced flow control, difficulty in operation, and visible damage to gate valve components. Leakage around the valve seat or stem, as well as a decrease in the ability to control fluid flow, indicates potential issues with the internal parts.
Additionally, if the valve operation becomes stiff or shows signs of visible damage such as cracks or deformities, it is advisable to consider replacing the affected parts. Regular inspection and proactive replacement of worn or damaged components can extend the lifespan of the valves and minimize the risk of costly downtime.
Conclusion for Gate Valve Parts
Understanding the key components of a gate valve is essential for anyone working with industrial valves. The body, bonnet, gate, stem, and seat each play a crucial role in the valve’s function and performance. With this comprehensive overview of gate valve parts, you now have the knowledge needed to identify, maintain, and troubleshoot these essential components. Whether it’s selecting the right connection type or choosing the appropriate gate design for your application, this guide equips you with the essential information to navigate the world of gate valves with confidence.