Control Valve vs Gate Valve: A Comprehensive Analysis
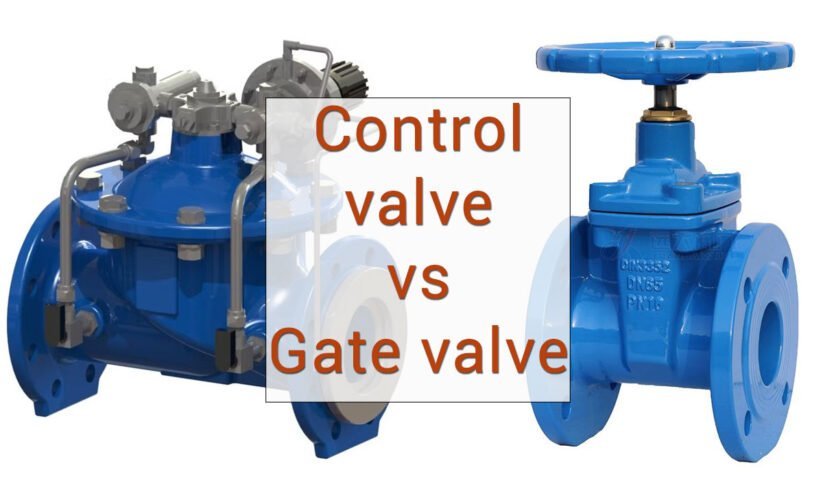
Table of Contents
ToggleDetailed Comparison of Control Valves and Gate Valves: A Comprehensive Analysis of Technical Data
When it comes to choosing between control valves and gate valves, it’s essential to understand the critical differences between these two types of valves. Control valves are designed to regulate fluid flow by adjusting the size of the valve opening, allowing for precise control in various applications, such as industrial and domestic settings. On the other hand, gate valves are used to control the flow of liquids and gases and are commonly found in industrial and commercial applications. They feature different operating mechanisms, such as rising and non-rising stems, and can be manually, automated, or remotely operated. Understanding the workings and unique features of these valves is crucial in determining their suitability for specific industrial applications.
Technical Comparison of Control Valve vs Gate Valve
In the realm of fluid control systems, the choice between a control valve and a gate valve can significantly impact the operation and efficiency of an industrial process. Understanding the technical differences between these two types of valves is crucial for discerning engineering decisions. In this article, we will delve into a comprehensive comparison of control valves and gate valves, examining their key technical specifications and functionality.
Operating Principle
- Control Valve: Control valves regulate flow by varying the size of the flow passage as directed by a signal from a controller.
- Gate Valve: Gate valves control flow by raising or lowering an internal gate to open or close the flow path completely.
Flow Regulation
- Control Valve: Offers precise and continuous flow regulation, making it suitable for applications requiring fine-tuning of flow rates.
- Gate Valve: Provides on/off flow control with minimal throttling capability, often used in applications where full flow closure is necessary.
Pressure Drop
- Control Valve: Generates a relatively higher pressure drop due to its design for flow regulation.
- Gate Valve: Causes a lower pressure drop as compared to control valves, particularly when fully open.
Velocity Control
- Control Valve: Effectively controls fluid velocity, allowing for precise adjustment to meet process requirements.
- Gate Valve: Does not provide velocity control, mainly focused on isolating the flow when fully closed.
Suitable Applications
- Control Valve: Ideal for processes requiring accurate flow control, such as chemical manufacturing, oil and gas refining, and power generation.
- Gate Valve: Commonly used in applications where a tight shutoff is essential, such as in pipelines for water distribution and sewage systems.
Materials and Construction
- Control Valve: Typically constructed with materials suitable for precise control and modulation of flow, such as stainless steel, brass, and exotic alloys.
- Gate Valve: Often made from materials capable of withstanding high-pressure environments and providing tight sealing, including cast iron, ductile iron, and carbon steel.
Actuation
- Control Valve: Can be pneumatically, electrically, or hydraulically actuated for automated control based on process conditions.
- Gate Valve: Primarily operated manually, but can also be equipped with actuators for remote operation in specific applications.
Maintenance and Serviceability
- Control Valve: Typically more complex and may require frequent maintenance due to its intricate design and components.
- Gate Valve: Relatively simpler in construction, often requiring less frequent maintenance and offering ease of serviceability.
In conclusion, the choice between a control valve and a gate valve should be based on the specific requirements of the fluid control application. While control valves excel in precision flow control, gate valves offer robust shutoff capabilities. By understanding the detailed technical differences outlined in this comparison, engineers and industry professionals can make informed decisions to optimize their fluid control systems.
Understanding Control Valves
Control valves are pivotal components in the operation of various systems and processes, regulating the flow of liquids, gases, and steam. Understanding the definition, function, types, main components, and operating principles of control valves is fundamental to comprehending their significance and application.
Usage and Importance of Control Valves
- Control valves are crucial components in various industrial processes, including oil and gas, chemical, and power generation.
- They are used to regulate the flow, pressure, temperature, and level of fluids within a system, ensuring operational efficiency and safety.
- Control valves play a vital role in maintaining precise control over process variables, allowing for optimal performance and product quality.
- Through their ability to modulate flow, control valves enable accurate adjustment of process conditions, contributing to overall system stability and reliability.
- The proper selection and utilization of control valves directly impact process control, energy efficiency, and overall operational costs.
Definition and Function of Control Valves
Control valves are designed to manipulate the flow rate, pressure, and the level of a fluid within a system. They work by modulating the flow of the fluid through the valve in response to signals received from a controller, enabling precise control over the process variables. Essentially, control valves help to maintain desired conditions within a system by continuously adjusting the flow rates.
Types of Control Valves
There are various types of control valves, each catering to specific applications and operational requirements. Some common types include globe valves, butterfly valves, ball valves, diaphragm valves, and rotary valves. Each type offers distinct characteristics and performance capabilities, making them suitable for diverse environments and processes.
Main Components of a Control Valve
The primary components of a control valve include the valve body, actuator, bonnet, trim, and valve positioner. The valve body serves as the primary structure and conduit for fluid flow, while the actuator controls the valve position. The bonnet encloses and supports the moving parts of the valve, and the trim, consisting of the plug, seat, and other related parts, modulates the flow. Additionally, the valve positioner ensures accurate positioning of the valve in response to the control signal.
Operating Principles of Control Valves
Control valves operate based on various principles, such as linear motion, rotary motion, and axial flow. Linear motion valves move in a straight line to control the flow, while rotary motion valves rotate to modulate the fluid passage. Axial flow valves, on the other hand, regulate flow by adjusting the flow area through the valve. These operating principles enable control valves to effectively and precisely manage the flow of fluids in a wide range of industrial processes.
Exploring Gate Valves
Gate valves, also known as sluice valves, are essential mechanical devices used to control the flow of fluids or gases in a pipeline. Their primary purpose is to regulate the pathway for fluid or gas flow, enabling efficient control and management.
Gate valves operate by utilizing a sliding or rotating gate that either fully opens or closes the valve’s passageway. This mechanism allows for seamless flow when the valve is open, as the gate slides into a recess in the valve body. Conversely, when closed, the gate blocks off any fluid or gas from passing through, providing precise control over the flow.
These valves play a critical role in various industries such as oil and gas, water treatment, and chemical processing. In the oil and gas sector, gate valves are used to control the flow of crude oil, natural gas, and other petroleum products in pipelines. In water treatment plants, they regulate the flow of clean water for consumption or industrial use, while in chemical processing plants, gate valves manage the flow of chemicals and other fluids.
Gate valves come in different types, including rising stem gate valves and non-rising stem gate valves, each with unique designs and functionalities suited for specific applications.
Gate Valve Basics
Gate valves, also known as sluice valves, are mechanical devices used to control the flow of fluids or gases in a pipeline. The primary purpose of gate valves is to open and close the pathway for fluid or gas flow, allowing for efficient regulation and control.
Usage and Importance of Gate Valves
- Gate valves are commonly employed in applications where an unrestricted flow of fluid and minimal pressure drop are essential, such as in the water and wastewater industries.
- They are used to fully open or close the flow of fluids, providing a tight seal and minimal leakage when closed.
- Gate valves are critical for isolating sections of pipelines or controlling the on/off flow of liquids or gases in various systems.
- These valves are designed to withstand high pressures and are often utilized in demanding environments where reliability and durability are paramount.
- The proper selection and maintenance of gate valves are crucial for ensuring efficient and safe operation within a range of industrial settings.
Rising vs. Non-Rising Stem Gate Valves
- Rising Stem Gate Valves: These valves have a stem attached to the gate, which rises or lowers as the valve opens or closes. The design allows for easy visual indication of the valve’s position, making it ideal for applications where accurate and visible monitoring is necessary.
- Non-Rising Stem Gate Valves: These valves have a gate that rises and lowers within the valve body, eliminating the need for an external stem. This compact design makes them perfect for installations with limited space, as there is no need to account for the length of a rising stem.
Material and Design Variations
Gate valves are available in various materials and design variations, including cast iron, ductile iron, carbon steel, stainless steel, and bronze. These material options cater to different environmental and operational requirements, ensuring the suitability of gate valves for diverse applications.
Mechanisms of Operation for Gate Valves
The operation of gate valves involves the movement of a gate to control flow. The mechanism allows for precise regulation of fluid or gas flow, making gate valves indispensable in industries where accurate control and management of flow is critical.
Comparing Control Valve vs Gate Valve
Valves play a crucial role in controlling the flow of fluids or gases within a system, catering to diverse applications across industries. Understanding the variances between gate valves and control valves is essential for selecting the most suitable valve for specific applications. Gate valves and control valves possess distinct features, flow control capabilities, and advantages, making them suited for different purposes.
Purpose and Applications
Gate valves are commonly used for on-off flow control. Their design, which involves the use of a gate that ascends or descends to obstruct or open the flow path, aligns well with applications requiring simple start-stop control. On the other hand, control valves are engineered for precise and continuous flow control, making them ideal for applications demanding regulation of flow rate, pressure, and other critical parameters.
Flow Control Capabilities
Gate valves control fluid flow by raising or lowering a gate within the valve body to modulate the flow path. In contrast, control valves regulate flow by varying the size of the flow passage to precisely manipulate the flow rate. This ability to minutely adjust flow positions control valves as the preferred option for applications needing accurate flow regulation.
Structural Differences
Gate valves are generally composed of a body, bonnet, stem, packing, and seat. The gate, typically made of metal, moves within the valve body to facilitate the opening and closing of the valve. Conversely, control valves consist of a control element, such as a ball, butterfly, or plug, along with an actuator that modulates the valve based on the control signal received.
Advantages and Disadvantages
Advantages of gate valves include their lower cost, ease of maintenance, and suitability for high-temperature and high-pressure applications. However, they are limited in terms of flow control precision and responsiveness. Control valves offer precise regulation, quick response times, and versatility across various applications, but they tend to be more complex and costly to maintain. Understanding these differences is crucial in selecting the appropriate valve to optimize system performance and efficiency.
Technical Specifications and Performance Data
Pressure Ratings for Control and Gate Valves
Control valves are typically designed to handle a wide range of pressure differentials, with some models capable of withstanding pressures ranging from 150 to 6000 psi. The pressure ratings for gate valves, on the other hand, are usually higher, often reaching up to 15000 psi. These specifications are important considerations when selecting the appropriate valve for a particular application, as they directly impact the valve’s ability to effectively control or shut off the flow of fluids in high-pressure systems.
Temperature Ranges and Capabilities
Control valves are engineered to operate within specific temperature ranges in order to maintain optimal performance. Most control valves are designed to handle temperatures ranging from -196°C to 566°C, making them suitable for a wide variety of industrial processes. In contrast, gate valves are known for their robust construction, enabling them to withstand extreme temperatures, often ranging from -29°C to 649°C. These temperature capabilities make gate valves a preferred choice for applications involving high-temperature fluids or environments.
Valve Sizing and Dimensional Standards
Control valves are available in various sizes and dimensional standards to accommodate diverse flow requirements. Common sizing standards include ANSI, ISA, and IEC, with valve sizes ranging from 1/2 inch to 24 inches or more. Gate valves are also offered in a range of sizes following industry-standard dimensions, often adhering to standards set by organizations such as API and ASME. The proper sizing and dimensional compatibility of valves are crucial for seamless integration into piping systems, ensuring optimal flow control and system efficiency.
Leakage Rates and Performance Benchmarks
Control valves are designed to minimize leakage to ensure precise flow regulation and system integrity. Performance benchmarks for control valves, such as the Valve Leak Rate Class (e.g., ANSI/FCI 70-2), provide a standardized method for evaluating and categorizing the allowable leakage rates based on the valve’s intended application. In contrast, gate valves are recognized for their tight shut-off capabilities, with leakage rates specified according to industry standards such as API 598. Understanding the leakage rates and performance benchmarks of both control and gate valves is vital in selecting the most suitable valve for specific operational requirements.
FAQ: Comparison of Control Valve vs Gate Valve
Control valves offer precise flow control and responsiveness but are complex, expensive, and require maintenance. On the other hand, gate valves are a cost-effective option without precise flow control capabilities, making them better suited for non-precision applications.
While both on-off valves and control valves serve similar functions, control valves provide a higher degree of precision and control over the flow of fluids. Traditional on-off valves, as the name suggests, are limited to turning on or off.
Control valves are designed for precise flow control by modulating the flow of fluid, while gate valves are designed for simple on-off operation without fine flow control capabilities.
Control valves are ideal for processes that require precise control over fluid flow, such as in chemical, petrochemical, and power plants, where accuracy and responsiveness are critical for efficient operation.
Gate valves are better suited for applications where precision flow control is not essential, such as in residential plumbing, sewage systems, and irrigation systems, where a cost-effective on-off solution is sufficient.
Control valves require regular maintenance due to their complex design and precision components, while gate valves generally have simpler maintenance needs, often requiring periodic lubrication and inspection of the sealing surfaces.
Control valves allow for precise regulation of fluid flow by modulating the flow area, while gate valves provide full flow when fully open and complete closure when fully closed, without the ability to regulate flow in between.
While control valves may have higher upfront costs and maintenance requirements, their ability to provide precise flow control can lead to improved efficiency and reduced operating costs in precision-critical applications, while gate valves are more cost-effective for non-precision applications.
Installation and Maintenance Considerations
Installation Procedures for Control and Gate Valves
When installing control valves, it’s essential to ensure that the valve is placed in the correct position in the pipeline to effectively regulate the flow of the fluid. It’s crucial to follow the manufacturer’s guidelines for installation to avoid any issues. Gate valves, on the other hand, require a different installation approach. They can be installed in a fully open or fully closed position and should be handled with care as they are sensitive to debris and particles that can obstruct the seal.
Maintenance Requirements and Lifespan
Control valves demand regular maintenance to ensure optimal performance. This involves inspecting and replacing worn-out parts, checking for leaks, and calibrating the valve to maintain precision. The lifespan of a control valve can vary depending on the frequency of use and the operating conditions. However, with proper maintenance, they can last for many years. Gate valves also require routine maintenance to prevent corrosion and ensure the sealing surfaces remain intact. Their lifespan can be prolonged with regular greasing and inspection to prevent any potential failures.
Troubleshooting Common Issues
Common issues with control valves include internal leakage, improper response to control signals, and excessive noise during operation. Troubleshooting these issues involves checking for wear and tear, ensuring proper calibration, and inspecting the control system for any malfunctions. Gate valves may face issues such as leakage, obstruction due to debris, and difficulty in opening or closing. Troubleshooting involves checking for blockages, inspecting the sealing surfaces, and ensuring the operating mechanism is functioning smoothly.
Replacement and Repair Tips
When it comes to replacement, control valves may need to be upgraded or replaced with a newer model to meet changing system requirements. Repairing control valves involves replacing faulty components, re-calibrating the valve, and conducting thorough testing to ensure proper functionality. For gate valves, repairing minor leaks and replacing damaged parts can extend their lifespan. In the case of irreparable damage, replacement with a new gate valve may be necessary.
Industry Applications and Case Studies
The versatile nature of control and gate valves allows them to be widely utilized across various industries. From water treatment to oil and gas operations, these valves play pivotal roles in ensuring efficient processes and operations.
Control and Gate Valves in Water Treatment
In the field of water treatment, control valves are employed to regulate the flow, pressure, and temperature of water in treatment plants. These valves enable precise control of the water treatment processes, ensuring that the water meets required quality standards before being distributed for consumption. On the other hand, gate valves find application in water distribution systems, where they serve as on/off valves to control the flow of water within pipelines and reservoirs.
The Role of Valves in Oil and Gas Industry
In the oil and gas industry, control valves are instrumental in managing the flow of crude oil, natural gas, and other fluids within pipelines and processing facilities. These valves enable precise control over the fluid flow, pressure, and composition, contributing to the efficient extraction, transportation, and refining of petroleum products. Gate valves are also utilized in the industry for their ability to provide a tight seal, making them suitable for isolation applications in pipelines and refining equipment.
Case Study
A notable case study illustrating the significance of control valves in the oil and gas sector is the implementation of control valve technology in offshore drilling operations. By integrating advanced control valves with real-time monitoring and automation capabilities, a leading oil company achieved enhanced operational efficiency, reduced downtime, and improved safety in their offshore drilling processes.
Innovation in Valve Technology and Future Trends
Advancements in valve technology continue to drive innovation in the industry, with a focus on enhancing precision, durability, and automation capabilities. The integration of smart technologies, such as IoT-enabled sensors and predictive maintenance algorithms, is revolutionizing the way control and gate valves are monitored and managed in industrial settings. Looking ahead, the future of valve technology is poised to encompass further digitization, increased sustainability, and seamless integration with advanced control systems.
Conclusion
In conclusion, after thorough research and analysis from various reputable sources, it’s evident that both control valves and gate valves offer distinct advantages and are suitable for specific applications. Control valves are ideal for precise fluid flow regulation in industries such as food processing and chemical manufacturing. On the other hand, gate valves are commonly used to control the flow of liquids and gases in industrial and commercial settings.
The decision between the two valves ultimately depends on the specific requirements of the application, including fluid type, pressure, and flow control precision. Understanding the fundamental differences and applications of these valves is crucial for making an informed decision and ensuring optimal performance in various operational environments.