Sluice/Gate Valves: Everything You Need to Know for Optimal Performance
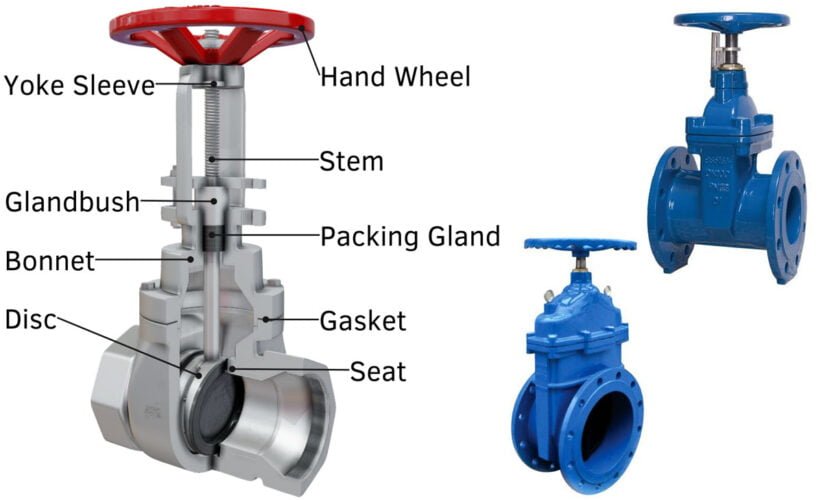
Table of Contents
ToggleComprehensive Guide to Sluice/Gate Valves: Types, Applications, and Future Trends
The sluice or gate valve is a critical component in various industrial and commercial systems, allowing for the regulation and control of fluid flow. Understanding the intricacies of sluice valves and their applications is essential for ensuring optimal performance and efficiency in fluid management systems.
In this comprehensive technical article, we will delve into the fundamental principles of sluice valves, exploring their design, functionality, and key considerations for selection and implementation. By providing in-depth insights, practical examples, and detailed data, this article aims to equip professionals and enthusiasts in the field with the knowledge and expertise necessary to make informed decisions regarding sluice valve integration and operation.
Understanding Sluice Valves
Sluice or gate valves are essential components in numerous industries, offering precise control over the flow of various fluids. Understanding these valves involves delving into their definition and functionality, exploring their historical evolution, and identifying the different types and their applications.
Definition and Functionality of Sluice/Gate Valves
Sluice valves, also known as gate valves, are designed to control the flow of liquids or gases through a pipe or duct. They operate by raising or lowering a gate, allowing or restricting the flow of the substance. When fully open, gate valves provide minimal obstruction to the flow, making them ideal for applications that require unobstructed flow when fully open and a tight seal when fully closed. The design of the sluice valve makes it suitable for applications that require a straight-line flow of fluids with minimum restriction.
Functions of Sluice/Gate Valves
- Regulating Flow: Sluice/Gate valves are used to control the flow of liquids or gases in a pipeline or system.
- On/Off Function: They serve as an on/off switch for the flow, allowing for complete closure or full opening of the passage.
- Pressure Regulation: These valves help in regulating and controlling the pressure within a system by managing the flow of fluid or gas.
- Direction Control: Sluice/Gate valves can be used to direct the flow of the medium in different directions, providing versatility in system design.
- Maintenance Access: They also provide easy access for maintenance and repairs within the pipeline or system.
- Isolation: These valves are capable of isolating a section of the pipeline or system for maintenance or safety purposes.
- Suitable for High Pressure: Sluice/Gate valves are suitable for high-pressure applications due to their robust design and ability to withstand pressure.
- Reliable Shut-Off: They offer reliable shut-off capabilities, ensuring that the flow of the medium can be completely stopped when needed.
- Durable Construction: Typically made from durable materials, these valves offer long-term reliability and performance in various industrial applications.
- Versatile Applications: These valves find applications in various industries, including water treatment, oil and gas, manufacturing, and more.
The History and Evolution of Sluice/Gate Valves
The history of gate valves dates back to ancient times when they were crafted from wood and used in basic irrigation systems. Over time, advancements in metallurgy and manufacturing processes led to the development of more robust and efficient gate valves. This evolution facilitated their widespread adoption across various industries, including oil and gas, water and wastewater, and chemical processing. Today, modern gate valves are engineered with precision to meet stringent performance requirements, ensuring optimal functionality and longevity.
Types of Sluice Gate Valves and Their Applications
Sluice gate valves come in various types to suit different applications. Some common types include wedge gate valves, parallel gate valves, and knife gate valves. Wedge gate valves are widely used in industries such as oil and gas, chemical, and power generation due to their ability to provide tight shut-off. Parallel gate valves, on the other hand, are suitable for low-pressure applications such as steam systems and water distribution. Knife gate valves are specially designed for applications involving the handling of viscous fluids, slurries, and powders, making them essential in industries like mining, pulp and paper, and wastewater treatment.
Understanding the diverse types of gate valves enables industries to select the most suitable valve for their specific applications, ensuring efficient and reliable fluid control.
The Anatomy of a Sluice/Gate Valve
In hydraulic engineering, the sluice gate valve is a critical component of hydraulic structures, offering the capability to seal the orifice of the building when necessary, or to fully or partially open the orifice to regulate upstream and downstream water levels and flow. Its applications are widespread, including flood control, irrigation, water supply, power generation, and navigation. Moreover, sluice gates can effectively remove floating materials, sediment, ice, etc., or facilitate the essential maintenance of related structures and equipment.
Key Components of a Sluice Valve and Material Selection
The steel sluice gate valve comprises the gate (movable part), fixing components, and gate opening and closing machinery. These core components consist of various smaller parts, each serving a distinct function to ensure the smooth operation of the valve. The gate structure includes components such as a gate, beam lattice, longitudinal and transverse linkage system, walking bearing, support arm, support hinge, water stop equipment, and lifting lug, all working in tandem to facilitate the opening and closing of the orifice water retaining structure. Additionally, buried components like the support line, reinforcing angle, water stop seat, and water stop rubber further contribute to the functionality of the valve.
Gate Valve vs. Sluice Valve
Gate valves and sluice valves both play pivotal roles in controlling the flow of fluids within a system. A gate valve utilizes a gate or wedge-shaped disc that moves perpendicular to the direction of fluid flow, whereas a sluice valve functions by sliding a gate to regulate the flow. While gate valves offer minimal resistance to flow when fully open, sluice valves are not designed for throttling due to the risk of disc and seat erosion as well as the potential for vibration and noise at high flow rates. Therefore, the choice between these valves largely depends on the specific operational requirements and flow control needs of the system.
Advantages of Using Sluice/Gate Valves in Systems
The utilization of sluice and gate valves provides several advantages in hydraulic and fluid control systems. These valves are well-suited for applications such as drains, sump tanks, and distribution boxes, where they can effectively hold back water with minimal leakage. Additionally, sluice/gate valves offer reliable and flexible opening and closing mechanisms, ensuring the safety and efficient operation of hydraulic structures. Their robust construction, coupled with the ability to manage upstream and downstream water levels and flow, makes them indispensable in various industries, including flood control, irrigation, power generation, and navigation.
How Sluice/Gate Valves Work
The sluice valve, also known as the gate valve, is an essential component in managing fluid flow in pipelines. This section delves into the mechanics of opening and closing sluice/gate valves, the flow characteristics and pressure management, as well as maintenance and troubleshooting of common issues.
The Mechanics of Opening and Closing
Sluice valves operate using a gate or wedge-shaped disk that moves perpendicular to the flow of fluid in the pipeline. When fully opened, the disk is completely separated from the flow, resulting in minimal flow resistance and pressure reduction. These valves are designed to be either fully opened or fully closed, making them unsuitable for precise flow regulation. The two main types of spindle used to raise the gate in a sluice valve are the Raising Spindle type valve and the Non-Raising spindle type valve. These types differ in how the spindle is connected to the gate and how the gate is raised during operation.
Flow Characteristics and Pressure Management
In the completely open position, sluice valves allow for an unobstructed flow path, leading to minimal flow resistance. However, the size of the open flow path varies nonlinearly when the gate is moved, impacting the flow rate unevenly. Partially opened gates can cause vibration due to the fluid flow, particularly in larger pipe diameters. It’s important to note that sluice valves are not suitable for flow regulation and may lead to erosion, vibration, and noise when used in partially open positions.
Sluice Valves Maintenance and Troubleshooting
Proper maintenance of sluice gate valves is crucial to ensure optimal performance and longevity. Regular inspection and lubrication of the valve components are essential to prevent issues such as leakage, corrosion, and operational inefficiencies. Common problems with sluice valves include seat surface erosion, leakage, and operational malfunctions. Troubleshooting these issues often involves inspecting the valve components, addressing any wear or damage, and ensuring proper alignment and operation of the spindle and gate.
In conclusion, understanding the mechanics of sluice/gate valves, their impact on flow characteristics and pressure management, as well as the importance of maintenance and troubleshooting, is key to their effective utilization in fluid control systems.
Usage Areas of Sluice/Gate Valves
- Hydroelectric power plants: Sluice/gate valves are crucial components in managing the flow of water to turbines, allowing for efficient power generation.
- Water treatment plants: These valves are used to control the flow of water through different stages of the treatment process, ensuring optimal purification.
- Flood control systems: Sluice/gate valves are utilized to regulate water levels in reservoirs, dams, and rivers, helping to mitigate the risk of flooding in surrounding areas.
- Irrigation systems: These valves play a key role in controlling the distribution of water to agricultural fields, promoting efficient and targeted irrigation.
- Marine and shipbuilding: Sluice/gate valves are employed in ship systems for managing water intake, ballast control, and other essential functions.
- Wastewater treatment facilities: These valves aid in directing the flow of wastewater through various treatment stages, facilitating effective processing.
- Mining operations: Sluice/gate valves are utilized in mine dewatering processes, helping to regulate water levels and maintain operational efficiency.
- Municipal water supply networks: These valves are used to regulate the flow of water within urban water distribution systems, ensuring consistent supply and pressure.
- Industrial processes: Sluice/gate valves play a critical role in controlling the flow of various liquids and gases in diverse industrial settings, supporting production operations.
- Oil and gas industry: These valves are essential for regulating the flow of fluids in pipelines, refineries, and offshore platforms, contributing to safe and efficient operations.
Sluice/Gate Valve Installation and Usage
Valves play a crucial role in regulating the flow of liquid in various industries, and one such valve widely used is the sluice gate valve. It is essential to understand the installation and usage of sluice valves to ensure optimal performance and longevity.
Pre-Installation Checklist
Before installing a sluice valve, certain key steps need to be followed to ensure a seamless installation process:
- Valve Inspection: Prior to installation, thoroughly inspect the valve body, stem, and gate to check for any damages that may have occurred during transit.
- Debris and Dirt Removal: Ensure that the valve is free of any debris, corrosion, wrapping material, and dirt to prevent any hindrance to its operational efficiency.
- Positioning: When installing large-size sluice valves, it is recommended to position them upright to facilitate ease of operation.
Sluice/Gate Valve Step-by-Step Installation Guide
The installation of a sluice valve involves the following steps:
- Pipeline Preparation: Prepare the pipeline by ensuring that the flanges are parallel and mate with the valve flange without leaving any gaps, ensuring a proper seal.
- Alignment and Fastening: Align the sluice valve with the pipeline and securely fasten it in place using appropriate fasteners, following the manufacturer’s guidelines.
- Testing: After installation, conduct thorough testing to ensure that the valve operates smoothly and effectively without any leaks or malfunctions.
Best Practices for Operators and Maintenance Personnel
Operators and maintenance personnel should adhere to the following best practices:
- Regular Inspection: Routinely inspect the sluice/gate valve for any signs of wear and tear, corrosion, or operational issues to address any potential issues promptly.
- Proper Lubrication: Ensure proper lubrication of moving parts to minimize friction and maintain smooth operational functionality.
- Scheduled Maintenance: Implement a scheduled maintenance program to carry out necessary checks, repairs, and replacements, thereby optimizing the valve’s lifespan and performance.
By following these pre-installation, installation, and maintenance best practices, sluice valve operators and maintenance personnel can ensure the efficient and reliable functioning of these essential components within industrial systems.
Sluice/Gate Valve Performance and Specification
Sluice/gate valves are crucial components in various industrial and commercial applications. Understanding their performance and specifications is essential for ensuring optimal functionality and safety.
Standard Measurements and Sizing Criteria
When it comes to sluice/gate valves, standard measurements and sizing criteria play a vital role in determining their compatibility with different systems. These valves come in a range of sizes, typically ranging from 2 inches to 48 inches in diameter. The sizing criteria are based on the flow requirements, pressure ratings, and the pipe systems they will be integrated into. It’s important to select the appropriate valve size to ensure efficient flow control and system integrity.
Performance Metrics and Testing Methods
The performance of sluice/gate valves is evaluated based on several key metrics, including leak tightness, operational torque, and pressure drop. Leak tightness is crucial to prevent any unwanted fluid leakage, while operational torque determines the force required to actuate the valve. Pressure drop measurement assesses the resistance to flow through the valve. These performance metrics are typically tested using industry-standard methods such as hydrostatic testing, pneumatic testing, and torque testing to ensure reliability and functionality.
Certifications and Industry Standards Compliance
To guarantee the quality and safety of sluice/gate valves, certification and compliance with industry standards are essential. These valves should adhere to standards set by organizations such as the American Society of Mechanical Engineers (ASME), American Petroleum Institute (API), and International Organization for Standardization (ISO). Additionally, certifications from regulatory bodies such as the American Bureau of Shipping (ABS) and the European Conformity (CE) mark signify adherence to stringent quality and safety standards, providing assurance of reliability and performance in diverse operating conditions.
By understanding the standard measurements, performance metrics, and certifications related to sluice/gate valves, stakeholders can make informed decisions and ensure the seamless integration of these critical components into their systems.