Different Types of Gate Valves: The Complete Guide
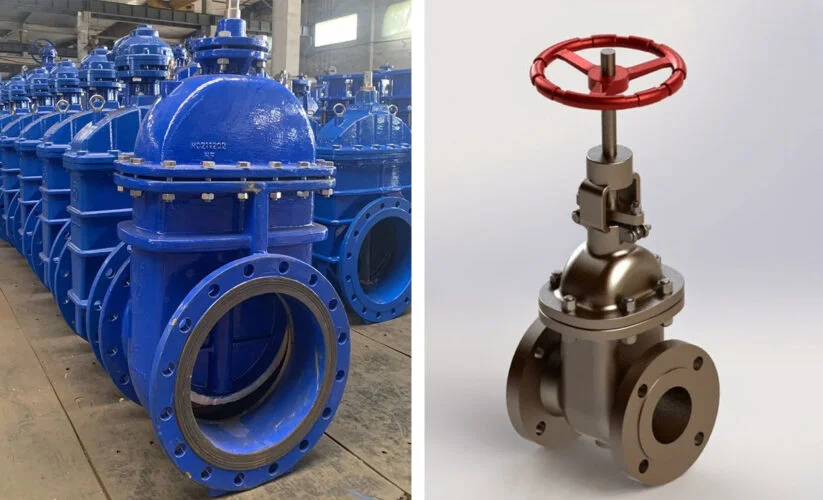
Table of Contents
ToggleAn Overview of Gate Valves: Understanding Their Functionality
Gate valves are crucial components in many industries, providing effective control over the flow of fluids and gases. Understanding the different types of gate valves is essential for selecting the most suitable option for specific applications. In this article, we will delve into the construction, applications, and advantages of various types of gate valves, offering valuable insights for professionals in the field.
The Basics of Gate Valves
What is a Gate Valve?
Gate valves are an essential component within the industrial sector. They are specifically designed to control the flow of liquids and gases by the use of a straight-line motion. This mechanism allows for a full and unobstructed flow bore, minimizing resistance and friction.
How Does a Gate Valve Work?
The gate valve operates through the movement of a disk, known as the gate, which travels up and down along the base of a stem or spindle. This action, accomplished with multiple turns of the spindle, enables the regulation of the flow. Gate valves are distinctive in their straight-line motion, setting them apart from other valve designs. Their ability to open fully and provide minimal obstruction to the flow makes them highly suitable for on/off applications, often referred to as block valves.
Types of gate valves are available in various sizes, materials, and pressure classes, catering to diverse industrial requirements. They are known for their cost-effectiveness and ease of maintenance, making them a popular choice in the industry. However, it is important to note that gate valves are not suitable for flow regulation and should only be operated in fully open or closed positions to prevent damage to the valve components.
Types of gate valve encompass a range of internal design possibilities, with the most common components being the body, bonnet, closure element (disc or gate), stem, and packing material. The stem/disc design can either be rising or non-rising, each catering to different industrial applications.
By understanding the basics of gate valves and their operational mechanisms, industries can effectively utilize these valves for diverse requirements, ensuring optimal performance and efficiency.
Gate Valve Diagram
A gate valve diagram illustrates the internal components and operation of a gate valve. The diagram typically shows the valve body, bonnet, gate, seat, stem, and handwheel. As the handwheel is turned, the stem moves up or down, causing the gate to open or close. The gate valve is used to control the flow of fluids in a pipeline and is often chosen for its ability to provide a tight seal when fully closed. This type of valve is commonly used in industrial applications where a straight-line flow of fluid and minimum restriction is desired.
Common Uses of Gate Valves in Industry
Types of gate valves are commonly utilized in various industrial applications due to their ability to provide a tight seal and regulate the flow of fluids. Here’s a breakdown of their common uses:
Water Supply Systems
In water supply systems, types of gate valves are essential for isolating specific sections of the network during maintenance, repairs, and new installations. They also serve the purpose of redirecting water flow within the pipeline, making them crucial components in ensuring the smooth operation of water supply infrastructure.
Oil and Gas Industry
Gate valves play a vital role in the oil and gas industry, where they are employed to control the flow of crude oil, natural gas, and other hydrocarbons. Their robust construction and ability to withstand high-pressure environments make them indispensable in this sector.
Manufacturing and Processing Plants
In manufacturing and processing plants, gate valves are widely used to regulate the flow of various liquids and gases. From controlling the movement of chemical solutions to managing the distribution of industrial gases, these valves are integral to the operational efficiency of such facilities.
Wastewater Treatment
Gate valves are integral in wastewater treatment processes, where they are deployed to manage the flow of sewage, sludge, and other waste materials. Their reliable performance under demanding conditions makes them well-suited for handling the challenges associated with wastewater management.
HVAC Systems
Heating, ventilation, and air conditioning (HVAC) systems rely on gate valves to control the flow of water, steam, and refrigerants. These valves ensure precise regulation of fluid movement within HVAC infrastructure, contributing to the effective operation of heating and cooling systems.
Fire Protection Systems
Gate valves are utilized in fire protection systems to control the flow of water in fire suppression applications. Their ability to provide a secure shutoff ensures the reliable functioning of fire protection infrastructure in safeguarding properties and lives.
Marine and Shipbuilding
In marine and shipbuilding applications, types of gate valves are employed for managing fluid flow on ships, offshore platforms, and maritime installations. Their durability and resistance to harsh marine environments make them essential components in maritime engineering.
Gate valves are versatile components that find extensive use across diverse industries, contributing to the seamless regulation of fluid flow and ensuring the efficient operation of critical systems.
Components of Gate Valves
A gate valve comprises various integral components, each playing a crucial role in its overall functionality. Understanding these components is essential for maintaining and troubleshooting gate valves.
Body and Bonnet
The body serves as the primary pressure-retaining structure of the gate valve, housing the essential operational parts such as the gate and seat. It enables the passage of flow and features connections like threaded, flange, butt weld, compression fitting, or tube fitting, chosen based on specific requirements such as valve size and operating pressure. The bonnet, on the other hand, functions as an additional pressure-retaining component, enclosing and safeguarding the valve’s stem and wedge. The choice of body-bonnet connection, whether screwed, union, bolted, welded, or pressure seal bonnet, depends on factors like valve size, pressure, and maintenance needs.
The Gate
The gate, also known as the disc or obturator, is responsible for controlling the flow through the valve by obstructing or allowing it. This critical component comes in various designs, each tailored to specific application requirements. For instance, the wedge gate, featuring a wedge-shaped disc that rises or lowers from inclined seats to regulate flow, is suitable for high-flow or turbulent applications such as steam service.
Valve Stems
Valve stems are integral to the proper functioning of gate valves, as they facilitate the movement of the gate to regulate flow. The design and material of the valve stem are chosen based on factors like environmental conditions, operating pressures, and required cycle life.
Seals and Seats
Seals and seats are essential for ensuring a tight closure and preventing leakage in types of gate valves. These components are designed to withstand the flow media, while also minimizing friction and wear to ensure longevity and reliability.
Understanding the intricacies of these key components is vital for comprehending the operation and maintenance of gate valves, enabling efficient and effective utilization in various industrial applications.
Types of Gate Valves Based on Gate Design
Gate valves are categorized based on their gate design, which plays a crucial role in their functionality and applications. Let’s delve into the different types of gate valves based on gate design.
Solid Wedge Gate Valve
The solid wedge gate valve is a traditional design with a solid, one-piece gate. It is suitable for applications where a tight seal is required. The simplicity of its design allows for easy maintenance and a reliable shut-off mechanism. However, solid wedge gate valves are more susceptible to thermal binding in high-temperature environments.
Flexible Wedge Gate Valve
In contrast to the solid wedge design, the flexible wedge gate valve features a two-piece gate that flexes to accommodate any potential deflection of the seating surfaces. Flexible wedge types of gate valves are ideal for handling changing operating conditions, such as fluctuations in temperature and pressure. They provide improved sealing performance and is less prone to the effects of thermal binding.
Split Wedge or Parallel Disk Gate Valve
The split wedge or parallel disk gate valve consists of two pieces that are attached to the stem independently. This design helps to enhance the seating and sealing capabilities of the valve, making it suitable for high-pressure and high-temperature applications. The parallel disk configuration allows for improved alignment and seating, reducing the likelihood of leakage.
Understanding the distinctions between these types of gate valve designs is essential for selecting the most suitable option based on the specific requirements of a given system or process. Each design offers unique advantages and considerations that can significantly impact performance and reliability.
Types of Gate Valves Based on Body and Bonnet Connection
Types of gate valves come in various designs based on their body and bonnet connection. Understanding these variations can help in choosing the right valve for specific applications.
Screwed Bonnet Gate Valves
Screwed bonnet gate valves are designed with a threaded connection for the bonnet, which makes maintenance and repair easier. These types of gate valves are suitable for low-pressure applications and come with a compact design, making them ideal for use in limited space installations.
Bolted Bonnet Gate Valves
Bolted bonnet gate valves feature a union or bolted connection between the bonnet and the body, providing a robust seal for high-pressure and high-temperature applications. These types of gate valves are commonly used in industrial settings where reliable performance under extreme conditions is essential.
Welded Bonnet Gate Valves
Welded bonnet gate valves are constructed with a welded connection between the body and the bonnet, ensuring a secure and leak-free seal. These types of gate valves are preferred for applications requiring resistance to corrosion and pressure, such as in the petrochemical and chemical industries.
Pressure Seal Bonnet Gate Valves
Pressure seal bonnet gate valves are designed to offer exceptional sealing performance in high-pressure systems. The bonnet is connected to the body through a pressure seal gasket, providing a tight seal even under intense pressure conditions. These types of gate valves are commonly used in power generation and oil and gas operations where sealing integrity is critical.
Understanding the different types of gate valves based on body and bonnet connection is crucial for selecting the right valve to ensure optimal performance and safety in various industrial applications.
Types of Gate Valves Based on Stem Movement
Types of gate valves are classified based on the movement of their stem. This section will discuss the two main types: rising stem gate valves and non-rising stem gate valves.
Rising Stem Gate Valves (OS & Y Type)
Rising stem gate valves, also known as OS & Y (outside stem and yoke) gate valves, feature a stem that rises above the valve to indicate the position of the gate. As the valve is operated, the stem moves up and down, providing a visual indication of the valve’s status. This design allows for easy detection of whether the valve is open or closed, making it suitable for applications where visual confirmation is necessary.
Non-rising Stem Gate Valves
Non-rising stem gate valves, also referred to as insider screw gate valves, have a stem that does not protrude from the valve. Instead, the stem’s threads are located inside the bonnet, and the gate is attached to the end of the stem. As the handwheel is turned, the stem and gate move up or down within the valve body, controlling the flow of fluid. This design is ideal for applications with space constraints, as the valve’s operation does not require additional clearance above the valve.
Understanding the movement of the stem in gate valves is crucial for selecting the appropriate type based on the specific requirements of a system or application. Both rising and non-rising stem gate valves offer distinct advantages and are chosen based on factors such as visibility, space limitations, and operational preferences.
Specialized Types of Gate Valves
Efficient handling of slurry and viscous media is crucial in various industrial settings. Knife gate valves are specially designed to meet the demands of these challenging applications. These valves feature a sharp-edged blade to cut through the media, offering a reliable shut-off solution. The resilient seat ensures tight shut-off, making them ideal for controlling the flow of slurries.
Knife Gate Valves for Slurry and Viscous Media
Knife gate valves designed for handling slurries and thick, viscous media are constructed to prevent clogging and maintain consistent flow. Their custom-manufactured square or rectangular ports accommodate the specific requirements of each application. With options for resilient seats and bonneted or bonnetless configurations, these valves provide tailored solutions for challenging media conditions.
In addition, the custom-fabricated gate valves offer versatility in design, size, and material selection to address unique application needs. The solid wedge design of the wedge gate valves ensures tight shut-off, with options for specialized and custom configurations, including narrow or custom face-to-face dimensions. Moreover, the specialized bonneted slide gate valves are adept at handling low-pressure systems with a lightweight construction, displacement pockets, and a tapered body for efficient material handling service.
Through-Conduit Gate Valves for Streamlined Flow
Through-conduit gate valves are engineered to provide streamlined flow with minimal resistance, ensuring optimum performance in various applications. These valves promote efficient fluid movement and are suitable for industries where uninterrupted flow is critical.
With the ability to withstand high pressure and temperature, the fabricated high-pressure/temperature knife gate valves are tailored for severe services, making them suitable for applications with temperatures up to 2000°F and pressures up to ASME Class 900. These specialized gate valves are designed to meet specific application requirements, offering reliable performance in demanding conditions.
Selecting the Right Gate Valve
When it comes to selecting the right gate valve for a specific application, it’s crucial to consider various factors to ensure optimal performance and longevity. Types of gate valves offer several advantages, but they also come with limitations. Understanding these aspects and the key considerations in the selection process is essential.
Advantages of Using Gate Valves
- Unrestricted Flow: Gate valves provide minimal obstruction to the flow of liquids due to their straight-through, unobstructed passage when fully open.
- Tight Seal: These valves offer a reliable seal when fully closed, reducing the risk of leakage.
- Suitable for High Pressure and Temperature: Types of gate valves are often preferred for applications involving high pressure and temperature due to their robust design.
- Minimal Pressure Drop: Their design allows for minimal pressure drop when fully open, making them ideal for applications where flow efficiency is crucial.
Disadvantages and Limitations of Gate Valves
- Slow Operation: Gate valves are not ideal for applications that require frequent opening and closing as they have a slower operation compared to other types of valves.
- Prone to Leakage: If not maintained properly, gate valves can be susceptible to leakage, especially when used for throttling applications.
- Susceptible to Clogging: The design of gate valves can make them prone to clogging when used with fluids that contain solid particles.
- Limited Control: Gate valves are not well-suited for applications that require flow rate control, as they are designed for full flow or shut-off operations.
Factors to Consider When Choosing a Gate Valve
- Application Requirements: Understand the specific demands of the application, including pressure, temperature, flow rate, and fluid characteristics.
- Valve Size and Type: Select a gate valve size and type that aligns with the piping system and the intended function, whether it’s for isolation, regulation, or other purposes.
- Material Compatibility: Consider the compatibility of the valve materials with the fluid conveyed to prevent corrosion and ensure longevity.
- Operation and Maintenance: Evaluate the frequency of operation and maintenance requirements to ensure the selected gate valve can meet the demands of the application while offering durability and reliability.
By carefully weighing these advantages, disadvantages, and key factors, one can make an informed decision when selecting the right gate valve for a specific industrial or commercial application.
Conclusion
Understanding the different types of gate valves is essential for anyone working with process industries. The knowledge of solid wedge, flexible wedge, split wedge, knife, and through-conduit gate valves, as well as the various body and bonnet connections and valve stem functions, can help in making informed decisions about valve selection and application. With this understanding, professionals can ensure the efficient control of fluid and gas flow in their operations, maximizing safety and productivity.