What Is a Globe Check Valve? Understanding the Basics
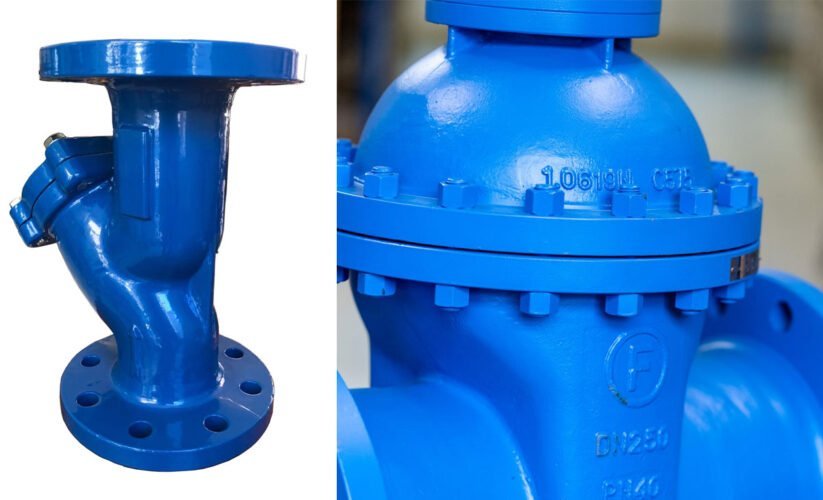
Table of Contents
ToggleGlobe Check Valves: A Comprehensive Overview
- A globe check valve is a type of valve used to control the flow of fluid in a pipeline.
- It consists of a movable disc or plug, a stationary ring seat, and a generally spherical body.
- The valve functions by allowing flow in one direction and preventing backflow.
- It is designed to regulate flow and provide tight shutoff when the flow is stopped.
Key Components
- The disc or plug controls the flow by either resting against or moving away from the seat to allow or stop the flow.
- The seat is the stationary ring against which the disc or plug seals to stop the flow.
- The body houses the internal components and provides the connection points for the pipeline.
Working Principle of a Globe Check Valve
- When fluid enters the valve, the pressure pushes the disc or plug away from the seat, allowing the fluid to pass through the valve.
- If there is backflow, the disc or plug is forced against the seat by the pressure, preventing the reverse flow.
Applications
- Globe check valves are commonly used in applications where backflow prevention and flow regulation are essential, such as in piping systems, refineries, power plants, and chemical processing facilities.
Advantages
- Provide a high level of control over flow.
- Offer reliable backflow prevention.
- Can be used in both horizontal and vertical pipe installations.
Considerations
- Proper installation and maintenance are crucial for optimal performance.
- Selecting the right material and size is important to ensure compatibility with the intended application and the fluid being handled.
What Is a Globe Check Valve?
Globe check valves are essential components in many piping systems, serving a crucial role in controlling the flow of fluids or gases in a one-way direction. Understanding the purpose, functionality, and key components of globe check valves is fundamental for anyone involved in the design, maintenance, or operation of industrial systems.
The Purpose of Globe Check Valves
Globe check valves are specifically designed to allow flow in one direction while preventing backflow, thus ensuring that fluids or gases move through the system in the intended manner. This prevents potential damage to equipment, maintains system efficiency, and enhances safety by preventing the reversal of flow that could lead to hazardous conditions.
How Does a Globe Check Valve Work?
The operation of a globe check valve is relatively straightforward. When there is forward flow, the pressure of the fluid or gas opens the valve, allowing it to pass through. However, when the flow attempts to reverse, the valve closes, preventing backflow. This is achieved through a disc or a flap mechanism that moves in response to the direction and pressure of the flow, effectively blocking any attempt at reverse flow.
Key Components of Globe Check Valves
Globe check valves consist of several key components that enable their functionality. These include the body, bonnet, disc, seat, stem, and actuator. The body provides the main structure, while the bonnet houses the moving parts and facilitates maintenance.
The disc, equipped with a hinge or pivot, is responsible for regulating the flow. The seat creates a seal when the valve is closed, preventing any leakage. The stem connects the actuator to the disc, transmitting the force necessary to open or close the valve.
The actuator, if present, provides the force to move the disc in response to changes in flow direction and pressure, ensuring the proper operation of the valve. Each of these components plays a critical role in the effective functioning of a globe check valve.
Types of Globe Check Valves
Globe check valves come in various types, each designed to suit different applications and operating conditions. Three common types include lift check valves, swing check valves, and disk check valves.
Lift Check Valves
Lift check valves are designed with a guided disc that moves along the vertical line of the valve seat. When the fluid moves in the forward direction, the disc lifts to allow flow. However, when the fluid reverses, the disc closes to prevent backflow. These valves are suitable for applications where minimal pressure drop is crucial.
Swing Check Valves
Swing check valves, also known as tilting disc check valves, have a hinged disc that swings open as the fluid flows in the forward direction and swings back to close when the flow reverses. These valves are ideal for applications with high flow rates and can handle semi-solids or slurries due to their unobstructed flow path.
Disk Check Valves
Disk check valves operate using a disk or wafer that opens and closes in response to the flow of the fluid. When the flow is in the forward direction, the disk opens to allow passage, and when the flow reverses, the disk closes to block backflow. These valves are suitable for applications with high flow velocities and can handle a wide range of fluids.
Each type of globe check valve offers distinct advantages and is engineered to meet specific operational requirements, providing versatile solutions for various industries and applications.
Applications of Globe Check Valves
Globe check valves find applications in various industries due to their functionality and design. These valves are vital components in ensuring efficient and safe operation in different systems. They are commonly used in the following areas:
Water Systems
In water systems, globe check valves play a crucial role in maintaining the directional flow of water. They are instrumental in preventing backflow, which could lead to contamination of clean water sources. Water treatment plants, municipal water supply systems, and irrigation networks extensively employ globe check valves to regulate the flow of water and prevent any potential damage to the infrastructure.
Fuel Delivery Systems
Globe check valves are also widely used in fuel delivery systems to control the flow of various types of fuels, including gasoline, diesel, and aviation fuel. These valves help maintain the proper direction of fuel flow, ensuring that it moves efficiently through pipelines and storage tanks without the risk of backflow or leaks. They are essential for the safe and reliable operation of fuel distribution networks and storage facilities.
Chemical Processing
In the chemical processing industry, globe check valves are utilized to regulate the flow of various types of chemicals and industrial fluids. These valves play a critical role in ensuring the safety and efficiency of chemical processes by controlling the movement of fluids within intricate piping systems. Globe check valves are designed to withstand the corrosive and abrasive nature of many chemicals, making them indispensable in chemical manufacturing plants and processing facilities.
Globe check valves offer a versatile and reliable solution for controlling fluid flow in diverse applications, making them indispensable components in numerous industrial processes and systems.
Advantages of Using Globe Check Valves
Globe check valves offer several advantages that make them a popular choice in various industrial applications. From preventing backflow to enhancing system safety and offering durability and reliability, these valves provide essential functions that contribute to efficient and safe operations.
Preventing Backflow
Globe check valves are designed to prevent backflow by allowing flow in only one direction. This crucial function ensures that fluids or gases move in the intended direction, preventing any reverse flow that could lead to contamination or damage to the system. By effectively blocking backflow, globe check valves help maintain the integrity of the entire system, providing a fundamental layer of protection.
Enhancing System Safety
The use of globe check valves contributes to system safety by minimizing the risk of potential hazards. By maintaining proper flow direction and preventing backflow, these valves help prevent accidents and system failures. Their reliable performance and ability to uphold system integrity make them vital components for ensuring a safe and secure operational environment.
Durability and Reliability
Globe check valves are renowned for their durability and reliability, making them suitable for demanding industrial conditions. Constructed from robust materials and engineered to withstand high pressures and temperatures, these valves offer long-term performance and require minimal maintenance. Their resilience and ability to consistently function under challenging circumstances make them a dependable choice for critical applications.
In summary, the advantages of using globe check valves, including their ability to prevent backflow, enhance system safety, and provide durability and reliability, position them as essential components in various industrial systems. Their unique capabilities contribute to the efficient and secure operation of machinery and processes, making them indispensable in ensuring the smooth functioning of diverse industrial operations.
Installation Considerations for Globe Check Valves
Proper Sizing and Fit
When installing a globe check valve, it is crucial to ensure that the valve is properly sized and fits the application requirements. The size and fit of the valve should be in line with the size of the piping system it is being installed in. An improperly sized or fitted valve can lead to inefficiencies and functional issues within the system. Consideration should also be given to factors such as pressure, temperature, and flow rate to ensure proper sizing and fit of the globe check valve.
Flow Direction and Orientation
Proper installation of a globe check valve also involves paying close attention to the flow direction and orientation of the valve. Globe check valves are designed to allow flow in one direction while preventing backflow in the opposite direction. It is essential to install the valve in the correct orientation to ensure its proper functionality. Improper orientation can lead to malfunctions and system inefficiencies. This could be compared to trying to swim against a strong current; the flow must be in the right direction for the valve to function effectively.
Maintenance Access
Consideration should be given to maintenance access when installing a globe check valve. Easy access to the valve for maintenance and repair purposes is essential for ensuring the longevity and optimal performance of the valve and the overall system. This can include factors such as accessibility for inspection, repair, and replacement of components. Proper maintenance access can greatly contribute to the reliability and efficiency of the system, preventing potential disruptions or downtime.
Common Issues and Troubleshooting Globe Check Valves
Globe check valves are susceptible to various issues that can affect their performance. Understanding these common problems and their troubleshooting methods is essential for maintaining the efficiency of these valves.
Leakage Problems
Leakage is a common issue with globe check valves and can occur due to various reasons such as damage to the sealing surfaces, improper installation, or corrosion. To troubleshoot leakage problems, it is important to inspect the sealing surfaces for any signs of wear or damage. Tightening the valve connection and applying sealant can help address minor leakage issues. In cases of severe damage, replacing the sealing components may be necessary to prevent further leaks.
Valve Wear and Tear
Over time, globe check valves can experience wear and tear, leading to reduced effectiveness and potential failure. It is crucial to regularly inspect the valve components for signs of wear, such as erosion, corrosion, or fatigue. Abrupt and frequent closure of the valve can contribute to accelerated wear. Implementing a routine maintenance schedule, including lubrication of moving parts and inspection of the valve seat, can help mitigate wear and tear issues and prolong the lifespan of the valve.
Noise and Vibration
Excessive noise and vibration during valve operation can indicate underlying issues such as cavitation, inadequate support, or flow turbulence. Addressing these issues requires a thorough analysis of the valve’s installation, including the piping system and support structures. Installing additional support mechanisms, such as dampeners or shock absorbers, can help reduce vibration and noise levels.
Additionally, modifying the flow conditions or selecting a valve with special trim designs can minimize cavitation, thereby reducing noise during operation.
By understanding these common issues associated with globe check valves and implementing appropriate troubleshooting measures, operators can ensure the reliable and efficient performance of these critical components in various industrial applications.
Choosing the Right Globe Check Valve
When it comes to choosing the right globe check valve, several critical factors should be considered to ensure optimal performance and reliability. Material selection, pressure and temperature ratings, manufacturer reputation, and quality are essential aspects to take into account.
Material Selection
The material of the globe check valve plays a significant role in its performance and longevity. Common materials include stainless steel, carbon steel, brass, and bronze. Stainless steel offers excellent corrosion resistance, making it suitable for harsh and corrosive environments. Carbon steel is known for its strength and durability, ideal for high-pressure applications. Brass and bronze are often chosen for their corrosion resistance and ease of machining. Selecting the appropriate material based on the specific requirements of the application is crucial for the overall effectiveness of the globe check valve.
Pressure and Temperature Ratings
Understanding the pressure and temperature ratings of a globe check valve is imperative to ensure its compatibility with the operating conditions. Different applications may demand varying levels of pressure and temperature, and it is essential to select a valve that can withstand these conditions without compromising performance. High-pressure or high-temperature environments require globe check valves with robust construction and resistance to thermal and mechanical stress.
Manufacturer Reputation and Quality
The reputation of the manufacturer and the quality of the globe check valve are indicators of reliability and performance. Choosing a trusted and reputable manufacturer ensures that the valve meets industry standards and undergoes rigorous testing for quality assurance. High-quality globe check valves are precision-engineered to deliver consistent and long-lasting performance, offering peace of mind to users regarding their operational reliability and efficiency.
When evaluating globe check valves, considering the manufacturer’s track record, certifications, and adherence to industry standards is vital in making an informed decision.
Conclusion
Understanding the basics of a globe check valve is crucial for those in the process industries. By exploring resources like the Control Valve Handbook and educational videos from reputable sources like the Fisher Valves & Instruments YouTube channel, individuals can gain valuable insights into the components and operation of globe valves.
Building a strong foundation of knowledge about these essential control elements will contribute to the safe, reliable, and efficient operation of production processes. Continuously seeking educational opportunities and connecting with industry experts will further enhance one’s understanding of globe check valves and their role in industrial operations.