Flanged Gate Valves: Understanding the Basics!
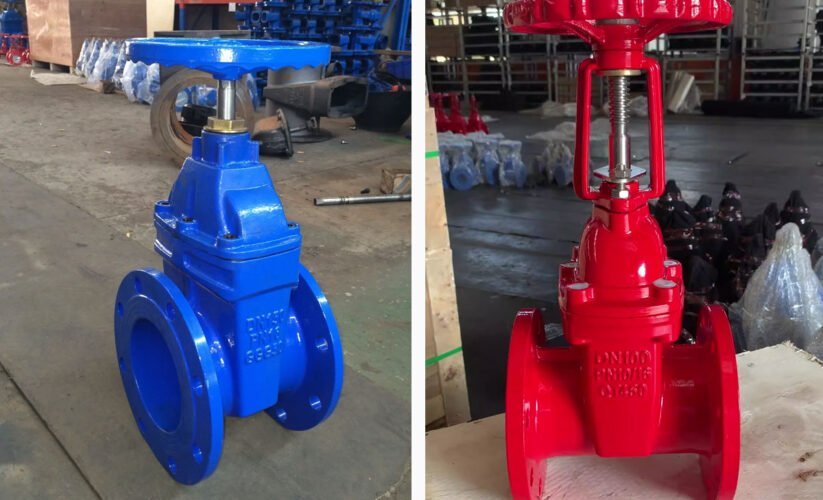
Table of Contents
ToggleComprehensive Guide to Flanged Gate Valves: Usage, Components, Advantages, and Considerations
Flanged gate valves find extensive usage in various industries due to their crucial role in controlling the flow within pipelines. These valves are designed to connect to the pipeline using a flange, allowing for efficient opening, closing, or obstructing of different pathways. The bolted flange connection with a gasket ensures minimal leakage, making them a popular choice for their ease of assembly and maintenance.
With features such as corrosion resistance and full port design, flange valves offer significant benefits in terms of durability and minimal resistance to flow. Additionally, the different types of flange valve connections, including flat face (FF) and raised face (RF) flanges, cater to specific application needs, further enhancing their versatility and utility.
Abstract: What is a Flanged Gate Valve?
- Flanged Gate Valves are linear motion valves that are designed to start or stop the flow of fluids in a pipeline.
- They are commonly used in systems where a straight-line flow of fluid and minimum flow restriction is desired.
- The flanged connections of these valves allow for easy installation and maintenance.
- These valves are equipped with a gate or wedge that can be lifted or lowered into the path of the flow of the fluid to control the flow.
- Flanged gate valves are suitable for a wide range of applications, including oil and gas, water, wastewater, and other industrial processes.
- They are available in various materials such as cast iron, carbon steel, stainless steel, and other alloys to suit different operating conditions.
- The sizes of flanged gate valves can vary widely to accommodate different pipeline requirements.
- Advantages of flanged gate valves include minimal pressure drop and bi-directional flow capabilities.
- Maintenance of these valves typically involves periodic inspection, cleaning, and replacement of components if necessary to ensure proper functioning.
- Proper installation and adherence to recommended operating parameters are crucial for the optimal performance and longevity of flanged gate valves.
Understanding Flanged Gate Valves
Definition of Flanged Gate Valves
Flanged gate valves are essential components in industrial flow management systems, designed to control the flow of liquids or gases. They consist of a flat gate or wedge that slides into the path of the fluid, restricting or allowing the flow as needed. These valves are equipped with flanged ends that allow them to be bolted to the piping system, ensuring secure and leak-free connections.
Role in Industrial Flow Management
The role of flanged gate valves in industrial settings is crucial for regulating the movement of fluids within pipelines. They offer reliable shut-off capabilities, making them suitable for applications where stopping the flow completely is necessary. These valves are commonly used in industries such as oil and gas, water treatment, chemical processing, and power generation. Their ability to handle high pressures and temperatures makes them versatile solutions for various flow control needs.
Common Usage Fields of Flanged Gate Valves
Water and Wastewater Treatment
Flanged gate valves are widely utilized in water and wastewater treatment facilities for controlling the flow of water and various fluids. These valves play a crucial role in regulating the movement of water, sewage, and other liquids within treatment plants, ensuring efficient and reliable operations.
Oil and Gas Industries
In the oil and gas sectors, flanged gate valves are essential components in controlling the flow of crude oil, natural gas, and refined petroleum products. These valves provide the necessary shut-off and flow control functions in pipelines, refineries, and offshore drilling operations, contributing to the smooth and safe transportation of oil and gas products.
Power Generation
In power plants, flanged gate valves are integral to the operation of steam and water systems. These valves help to manage the flow and pressure of steam, condensate, and cooling water within power generation facilities, contributing to the efficient and reliable generation of electricity.
Mining Operations
Flanged gate valves are extensively used in mining operations to regulate the flow of various materials, including slurries, acids, and other mining by-products. These valves are critical for maintaining the proper flow and pressure conditions in mining processes, supporting the extraction and processing of valuable minerals.
Parts and Components of a Flanged Gate Valve
A flanged gate valve is a crucial component often used in industrial applications to control the flow of fluids. Understanding the various parts and components of a flanged gate valve is essential for its proper functioning and maintenance.
Body and Bonnet
The body of a flanged gate valve is the primary pressure-containing structure that houses the internal components such as the gate and seat. It is designed to provide a passage for fluid flow and is connected to the piping system on both ends. The bonnet, on the other hand, serves as an additional pressure-containing part that encloses and protects the valve’s stem and gate. The type of connection, be it threaded, flanged, butt weld, compression fitting, or tube fitting, plays a crucial role in determining the suitability of the body and bonnet for specific applications.
Stem and Disc
The stem of a flanged gate valve is responsible for transmitting the motion of the operator to the disc, allowing it to move up and down to regulate the flow of fluids. The disc, also known as the gate or obturator, plays a pivotal role in either allowing or obstructing the flow through the valve. The design and material of the stem and disc are significant factors in determining the valve’s efficiency and longevity.
Sealing Elements
Sealing elements in a flanged gate valve are critical for maintaining a tight seal when the valve is closed, preventing any leakage of fluid. Proper sealing is essential for the overall performance and safety of the valve. Different types of sealing elements, such as gaskets and packing materials, are used to ensure effective sealing based on the specific operational requirements and environmental conditions.
Actuators
Actuators are devices used to control the motion of the gate or disc in a flanged gate valve. They can be manual, electric, pneumatic, or hydraulic, providing flexibility in operating the valve based on the application’s needs. The selection of the appropriate actuator depends on factors such as the operational environment, flow control requirements, and the level of automation desired.
Understanding the intricate details of the parts and components of a flanged gate valve is essential for ensuring its efficient operation and longevity. Proper maintenance and periodic inspection of these components are crucial for preventing potential issues and ensuring safety in industrial fluid control systems.
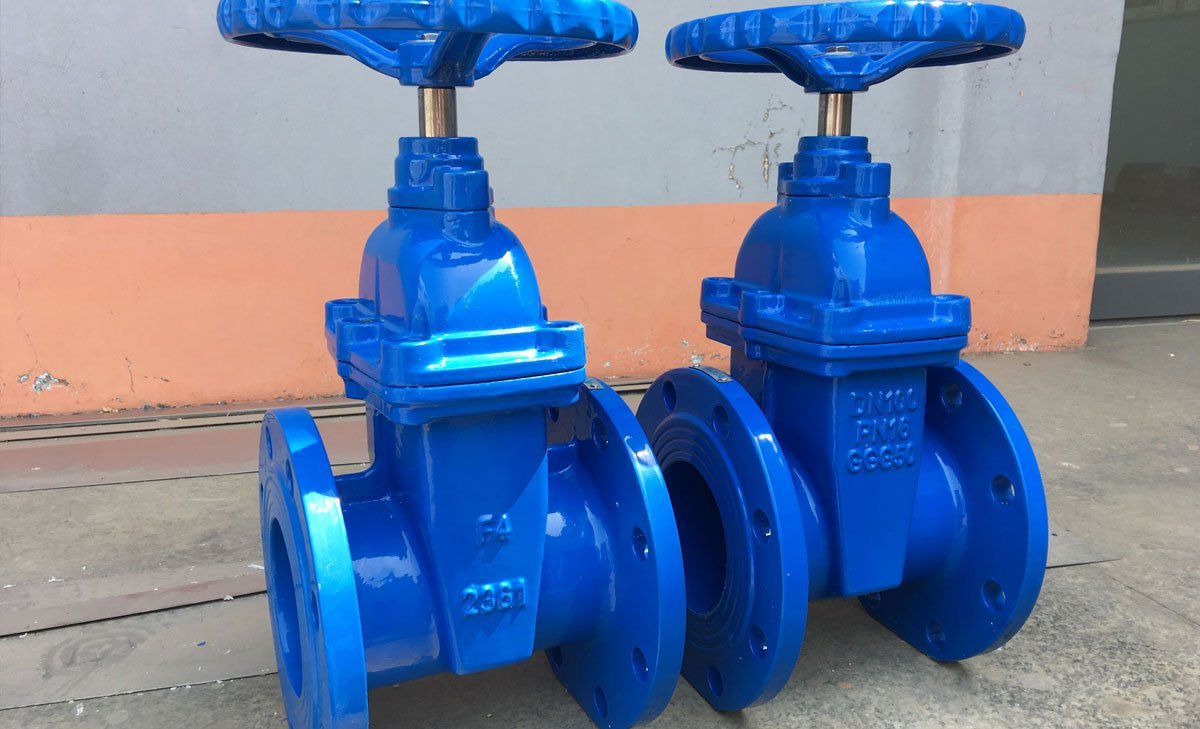
Advantages of Using Flanged Gate Valves
Leak Prevention with Flange Connections
Flanged gate valves provide superior leak prevention due to their robust flange connections. The bolted flange joint ensures a secure and tight seal, minimizing the risk of leakage in high-pressure applications. This feature enhances operational safety and reliability, making flanged gate valves an ideal choice for critical systems where leakage could result in environmental or safety hazards.
Durability and Corrosion Resistance
With their sturdy construction and high-quality materials, flanged gate valves exhibit exceptional durability and corrosion resistance. The flanged connections add an extra layer of strength to the valve assembly, enabling it to withstand demanding industrial environments and harsh operating conditions. This resilience extends the service life of the valves, reducing the frequency of maintenance and replacement cycles, thus lowering overall lifecycle costs.
Full Port Design Benefits
The full port design of flanged gate valves allows for unobstructed flow, minimizing pressure drop and turbulence within the system. This design feature ensures efficient fluid handling and contributes to energy savings by reducing pumping requirements. Moreover, the full port design facilitates easier pigging and cleaning processes, making maintenance and operational procedures more streamlined and cost-effective.
Pressure and Temperature Considerations
When it comes to selecting a flanged gate valve for specific applications, considering pressure and temperature is paramount. These factors directly impact the material selection, design standards, and performance capabilities of the valve. Let’s delve into the crucial aspects to consider when evaluating pressure and temperature requirements for flanged gate valves.
Material Selection for Extreme Conditions
In extreme temperature and pressure conditions, the choice of valve material is critical. Stainless steel, alloy steel, and other high-performance alloys are often preferred for their ability to withstand harsh environments without compromising integrity. These materials exhibit exceptional resistance to corrosion, erosion, and thermal expansion, making them suitable for handling extreme pressure and temperature variations.
Design Standards for Safety
Adhering to design standards is imperative for ensuring the safety and reliability of flanged gate valves in diverse operating conditions. Industry standards such as API, ASME, and ASTM provide guidelines for the design, manufacturing, and testing of valves to withstand high-pressure and high-temperature applications. Compliance with these standards guarantees robust construction, leak-tight performance, and long-term durability, instilling confidence in the valve’s ability to operate safely under challenging conditions.
Pressure Ratings and Temperature Ranges
Understanding the pressure ratings and temperature ranges of flanged gate valves is essential for determining their suitability for specific industrial environments. Valves are typically rated for maximum allowable working pressure and temperature, indicating the upper limits at which they can effectively function without compromising performance or safety. It’s imperative to align these ratings with the operational demands of the application to prevent potential failures and ensure optimal performance over the valve’s service life.
In conclusion, evaluating pressure and temperature considerations for flanged gate valves involves meticulous attention to material selection, adherence to design standards, and comprehension of pressure ratings and temperature ranges. By taking these factors into account, industries can confidently deploy flanged gate valves in demanding environments, knowing that they are equipped to withstand the rigors of high-pressure and high-temperature applications.
Assembly of Flanged Gate Valves
Step-by-step Installation Guide
When assembling a flanged gate valve, it’s crucial to follow a systematic approach to ensure proper functionality. Begin by inspecting the valve components for any damage or defects. Clean the mating flanges thoroughly to remove any dirt or residue that could impede a secure fit. Carefully align the valve between the flanges and insert the bolts.
Gasket Placement for Optimal Sealing
Proper gasket placement is essential for achieving an effective seal in flanged gate valve assembly. Select a gasket material that is compatible with the fluid and temperature requirements. Ensure that the gasket is positioned evenly and aligns with the bolt holes. Tighten the bolts uniformly, alternating across the flange to maintain consistent pressure and prevent leaks.
Bolting Techniques for a Secure Fit
Employing the correct bolting techniques is critical to securing a flanged gate valve in place. Utilize the appropriate torque wrench to tighten the bolts in a staggered pattern, gradually increasing the torque to the specified level. This approach ensures a uniform and secure fit, preventing uneven stress distribution and potential leakage.
Frequently Asked Questions About Flanged Gate Valves
Maintenance and Troubleshooting Tips
When it comes to maintaining flanged gate valves, regular inspections are crucial. Look out for signs of corrosion or leakage, as these could indicate the need for replacement or repairs. Lubricate the valve components as recommended by the manufacturer to ensure smooth operation and prevent wear and tear. In terms of troubleshooting, if you encounter issues such as difficulty in opening or closing the valve, it may be due to obstructions in the flow path or damage to the sealing surfaces. In such cases, a thorough inspection and potential replacement of components may be necessary to restore functionality.
Choosing the Right Valve for Your Application
Selecting the appropriate flanged gate valve for your specific application requires careful consideration of factors such as the type of fluid or gas being controlled, the pressure and temperature conditions, and the flow rate. Different materials and designs are suited for different environments, so it’s essential to consult with experts or refer to industry guidelines to ensure the valve chosen is compatible with your system requirements. Additionally, evaluating the size and configuration of the pipeline, as well as the operational conditions, will help in determining the most suitable valve for optimal performance and longevity.
Differences Between Flanged and Other Valve Types
In comparing flanged gate valves to other valve types such as ball valves or globe valves, it’s important to recognize the distinct characteristics that set them apart. While ball valves offer quick shutoff and globe valves provide precise flow control, flanged gate valves excel in applications where a tight shutoff is essential. Their ability to minimize pressure drop and accommodate high temperatures makes them favorable for certain industrial settings. Understanding the unique features and capabilities of each valve type enables informed decision-making when selecting the most appropriate valve for a specific use case.
Conclusion
Flanged gate valves are essential components in various industries, providing crucial control over the flow within pipelines. Their ease of assembly and disassembly make maintenance a breeze, ensuring smooth operations. These valves come with corrosion-resistant properties, offering durability and resilience in the face of harsh substances. The full port feature ensures minimal resistance to flow, enhancing efficiency in fluid dynamics. With different types of flange valve connections available, each with its own set of advantages, these valves cater to a wide range of pressure and temperature considerations, making them an indispensable asset in various applications.