Selecting the Right Ball Valves for Gas Pipelines
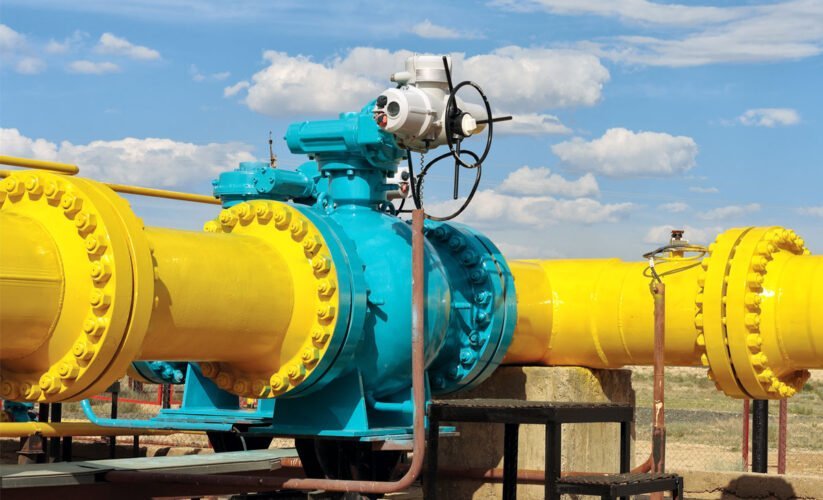
Table of Contents
ToggleThe Complete Guide to Selecting Ball Valves for Gas Pipelines
When selecting ball valves for gas pipelines, several factors need to be considered to ensure optimal performance and safety. The type of media being controlled dictates the valve material, with options such as PTFE and PFA for harsh or corrosive materials, and metal valves for pressurized gases. Proper valve sizing is crucial, considering temperature, pressure, and flow rate. Additionally, understanding the valve function, actuation method, and maintenance requirements is essential for making an informed decision. These considerations play a critical role in selecting the right ball valves for gas pipelines.
Understanding the Importance of Ball Valves for Gas Pipelines
Gas pipelines are crucial infrastructure for transporting natural gas from one point to another. To ensure the safety and efficiency of gas transportation, various components play a vital role, and ball valves are among the most important in this regard.
The Basic Function of Ball Valves for Gas Pipelines
Ball valves are quarter-turn valves that use a pivoting ball to control the flow of gas through a pipeline. When the valve’s handle is turned, the ball rotates to either allow gas to flow through or shut off the flow completely. This simple yet effective mechanism makes ball valves highly efficient in regulating gas flow, providing a quick and reliable method for controlling the pipeline’s operational status.
Why Ball Valves Are Essential for Gas Pipeline Safety
The use of ball valves in gas pipelines is essential for maintaining safety and preventing potential hazards. Their ability to provide a tight seal when closed ensures that gas flow can be promptly and securely halted in case of emergencies or routine maintenance. This feature is particularly critical for preventing gas leaks or pressure buildup, which could lead to catastrophic consequences if not swiftly addressed.
In addition, ball valves are also highly resistant to contamination and are capable of withstanding high pressures and temperatures commonly found in gas pipeline operations. Their robust construction and reliable performance make them an integral part of ensuring the overall safety and security of gas transportation systems.
By incorporating ball valves into gas pipelines, operators can have confidence in the ability to swiftly and effectively control gas flow, thereby enhancing the overall safety and reliability of the entire pipeline network.
Types of Ball Valves for Gas Pipelines
Floating Ball Valves
Floating ball valves are designed with a floating ball that moves as the fluid pressure changes. This type of ball valve is suitable for low to medium pressure applications and offers reliable performance in gas pipeline systems. The floating ball design allows for tight sealing, reducing the risk of leakage.
Trunnion Mounted Ball Valves
Trunnion mounted ball valves are ideal for high-pressure gas pipeline systems. The trunnion design provides additional support to the ball, ensuring stability and preventing excessive wear and tear. This type of ball valve is recommended for applications where tight shut-off and high cycling frequency are required.
Top Entry Ball Valves
Top entry ball valves are designed for easy accessibility and maintenance. With the ability to disassemble the valve from the top, maintenance and repairs can be conducted without removing the valve from the pipeline, minimizing downtime and operational disruptions. This feature makes top entry ball valves a practical choice for gas pipeline systems.
Full Port vs. Reduced Port Ball Valves
Full port ball valves allow for maximum flow capacity, making them suitable for applications where minimal flow restriction is desired. On the other hand, reduced port ball valves feature a smaller ball opening, which can lead to some flow restrictions. Understanding the specific flow requirements of the gas pipeline system is essential in determining whether a full port or reduced port ball valve is the most suitable option.
Material Selection for Ball Valves for Gas Pipelines
Gas pipelines require durable and reliable ball valves to ensure safe and efficient operation. The material selection for ball valves plays a crucial role in their performance and longevity. When choosing ball valves for gas pipelines, it’s essential to consider factors such as corrosion resistance, pressure and temperature ratings, and overall durability. Here are the key material options to consider:
Stainless Steel Ball Valves
Stainless steel ball valves are highly favored for their exceptional corrosion resistance, making them ideal for gas pipelines where exposure to moisture and corrosive elements is a concern. The non-corrosive nature of stainless steel ensures long-term reliability, even in harsh environmental conditions. Additionally, stainless steel offers high strength and temperature resistance, making it suitable for a wide range of gas pipeline applications.
Carbon Steel Ball Valves
Carbon steel ball valves are known for their robustness and ability to withstand high pressure and temperature conditions. These valves are suitable for gas pipelines that experience significant mechanical stress and elevated operating temperatures. However, it’s important to consider the potential for corrosion in certain environments and implement appropriate protective measures to ensure the longevity of carbon steel ball valves.
Alloy Material Ball Valves
Alloy ball valves are designed to provide a balance of corrosion resistance, strength, and durability, making them versatile options for gas pipeline applications. Different alloy compositions offer varying levels of resistance to specific corrosive elements, allowing for customized selection based on the specific operating environment of the gas pipeline. Proper alloy selection can significantly enhance the performance and longevity of ball valves in gas pipeline systems.
Selecting the right material for ball valves in gas pipelines is a critical decision that directly impacts the reliability and safety of the entire system. By carefully evaluating the properties and performance characteristics of stainless steel, carbon steel, and alloy ball valves, pipeline operators can make informed decisions that ensure optimal performance and longevity.
Key Factors to Consider When Choosing a Ball Valve for Gas Pipeline
Pressure Rating and Temperature Range
When selecting a ball valve for a gas pipeline, it is crucial to consider the pressure rating and temperature range. The valve must be able to withstand the specific pressure and temperature conditions of the gas being transported. The material and construction of the valve should be carefully chosen to ensure it can handle the anticipated pressure and temperature variations without compromising performance or safety.
Valve Sizing and Flow Requirements
Proper valve sizing is essential to ensure optimal performance and efficiency in gas pipeline operations. The valve size must be matched to the flow requirements of the gas, taking into account factors such as pressure drop and flow rate. Incorrect valve sizing can lead to operational issues and inefficiencies, making it imperative to accurately determine the flow requirements before selecting a ball valve for the gas pipeline.
End Connection Types
The selection of end connection types for ball valves is a critical consideration in gas pipeline applications. The compatibility of end connections with the existing pipeline infrastructure, as well as the ease of installation and maintenance, should be thoroughly evaluated. Factors such as threading, flange connections, or weld ends must be carefully assessed to ensure seamless integration and reliable performance.
Operation Mechanism—Manual or Actuated
Choosing the appropriate operation mechanism for ball valves in gas pipelines is pivotal in ensuring efficient and reliable valve control. The decision between manual or actuated operation depends on the specific operational requirements, such as remote control capability, automation needs, and response time. Evaluating the advantages and limitations of manual and actuated mechanisms is essential in selecting the most suitable option for gas pipeline applications.
Safety and Compliance Standards
Gas pipelines are subject to stringent safety and compliance standards to ensure the protection of both people and the environment. Understanding and adhering to industry standards and relevant certifications is crucial for the selection of ball valves for gas pipelines.
Industry Standards for Gas Pipelines
The gas industry is governed by strict industry standards to guarantee the safe operation of gas pipelines. These standards cover various aspects such as design, construction, and maintenance to minimize the risk of accidents and ensure the reliability of pipeline systems. Adhering to these standards is vital for the selection of ball valves, as they play a critical role in the safe and efficient operation of gas pipelines.
Understanding API 6D and Other Relevant Certifications
API 6D is a widely recognized standard for pipeline valves, including ball valves, providing guidelines for their design, manufacturing, and testing. Compliance with API 6D ensures that ball valves meet the necessary performance and reliability requirements for use in gas pipelines. In addition to API 6D, other relevant certifications such as ISO 9001 for quality management and ISO 15848 for fugitive emissions further validate the reliability and compliance of ball valves with industry standards.
Adhering to these standards and certifications is a fundamental consideration when selecting ball valves for gas pipelines, as they directly impact the safety, efficiency, and compliance of the pipeline system.
Maintenance and Durability Considerations
In the context of gas pipelines, the selection of ball valves demands careful evaluation of maintenance requirements and expected lifespan. The ease of maintenance and repair, as well as the anticipated longevity of ball valves, are crucial factors when considering their suitability for gas pipeline applications.
Ease of Maintenance and Repair of Ball Valves for Gas Pipelines
Ball valves intended for gas pipeline usage should offer ease of maintenance and repair. Quick and straightforward maintenance procedures can minimize downtime and ensure the continuous and reliable operation of the pipeline system. Selecting ball valves with accessible components and efficient maintenance protocols can significantly contribute to the overall efficiency and cost-effectiveness of the gas transport infrastructure.
Expected Lifespan of Ball Valves for Gas Pipelines
The expected lifespan of ball valves in gas pipelines is a vital consideration for long-term operational reliability. Factors such as material durability, corrosion resistance, and the ability to withstand high-pressure environments directly impact the service life of the valves. Understanding the anticipated lifespan of the chosen ball valves is essential for planning maintenance schedules, replacement cycles, and overall operational strategies within the gas pipeline network.
Cost-Efficiency and Lifecycle Costs
When selecting ball valves for gas pipelines, the cost-efficiency and long-term lifecycle costs are crucial factors to consider. It’s essential to weigh the initial investment against the potential long-term savings, along with evaluating the total cost of ownership for ball valves in gas pipelines.
Initial Investment vs. Long-Term Savings
The initial investment in ball valves for gas pipelines can vary based on factors such as materials, size, and pressure ratings. While it may be tempting to opt for the lowest upfront cost, it’s important to consider the potential long-term savings that high-quality, durable ball valves can offer. Investing in superior quality ball valves may result in fewer maintenance and replacement costs over time, ultimately leading to significant long-term savings.
Total Cost of Ownership for Ball Valves for Gas Pipelines
Assessing the total cost of ownership involves considering not only the initial purchase price but also ongoing maintenance, repair, and replacement expenses. High-quality ball valves designed for the specific demands of gas pipelines can contribute to lower total cost of ownership due to their extended lifespan, reduced downtime, and lower maintenance requirements. Factoring in the cost of downtime and the potential impact on operations is essential when evaluating the total cost of ownership.
Understanding the balance between initial investment and long-term savings, and conducting a comprehensive assessment of the total cost of ownership will guide the selection of ball valves that offer the optimal cost-efficiency and lifecycle costs for gas pipelines.
Vendor and Manufacturer Selection
Before selecting ball valves for gas pipelines, it is crucial to thoroughly assess the vendors and manufacturers. The reputation and experience of the vendor, along with the post-sale support and warranty offered, play significant roles in ensuring the reliability and performance of the selected ball valves.
Importance of Vendor Reputation and Experience
When choosing a vendor for gas pipeline ball valves, it is imperative to consider their reputation and experience in the industry. A vendor with a solid reputation is more likely to provide high-quality products and reliable service. Their experience signifies a deep understanding of the market’s demands and the ability to deliver solutions tailored to specific needs. By selecting a reputable and experienced vendor, the risk of receiving subpar products or inadequate support can be significantly mitigated.
Post-Sale Support and Warranty-Ball Valves for Gas Pipelines
The availability of post-sale support and a comprehensive warranty is a critical factor in the selection of ball valve vendors. A trustworthy vendor should offer reliable customer support, technical assistance, and guidance after the sale. Additionally, a robust warranty demonstrates the manufacturer’s confidence in the quality and durability of their ball valves. A comprehensive warranty provides assurance to the buyer, offering protection against potential malfunctions or defects in the product.
In summary, evaluating the reputation, experience, post-sale support, and warranty of vendors and manufacturers is vital in selecting the most suitable ball valves for gas pipelines. These considerations can significantly impact the performance, reliability, and longevity of the chosen valves, ensuring the integrity of the gas pipeline system.
Installation and Operational Best Practices
When it comes to ball valves for gas pipelines, proper installation and operational best practices are crucial for ensuring safety and efficiency. Here’s a look at the key considerations for installation techniques and routine inspection and testing procedures.
Proper Installation Techniques of Ball Valves for Gas Pipelines
The installation of ball valves in gas pipelines requires precision and adherence to industry standards. It begins with thorough planning, including the selection of the appropriate valve size, material, and type based on the specific requirements of the gas pipeline system. Proper alignment and support are essential to prevent stress on the valve and ensure optimal performance.
During installation, it’s imperative to follow the manufacturer’s guidelines to the letter, including torque specifications for bolt tightening, proper sealing techniques, and the use of compatible fittings and accessories. Additionally, ensuring the integrity of the valve’s seals and connections is critical to prevent gas leakage and maintain operational safety.
Routine Inspection and Testing Procedures
Routine inspection and testing are integral parts of maintaining the reliability and safety of ball valves in gas pipelines. Regular visual inspections should be conducted to check for signs of corrosion, damage, or wear that could compromise the valve’s functionality. Furthermore, non-destructive testing methods, such as ultrasonic examination or magnetic particle inspection, can be employed to assess the structural integrity of the valves.
Functional testing, including leak testing and operational performance checks, should be carried out at specified intervals to identify any anomalies and ensure proper valve functionality under varying operating conditions. Any deviations or issues discovered during inspections and testing must be promptly addressed to prevent potential safety hazards and operational disruptions.
In summary, adhering to proper installation techniques and conducting rigorous routine inspections and testing procedures are essential for maintaining the efficiency and safety of ball valves in gas pipelines. By prioritizing these best practices, gas pipeline operators can mitigate risks and uphold operational integrity.
Conclusionon Ball Valves for Gas Pipelines
Selecting the right ball valve for gas pipelines is crucial for ensuring efficient and safe operation. Considering factors such as the type of media being controlled, application conditions, valve function, actuation method, and maintenance requirements is essential in making an informed decision. By carefully evaluating these factors and understanding the specific needs of the application, you can choose the most suitable ball valve to optimize performance and longevity in gas pipeline systems.